Интересная конструкция пресса для изготовления топливных брикетов

Наш мир не стоит на одном месте, поэтому самые ультрасовременные технологии проявляют себя в таких отраслях, в которых как может показаться придумать что-то новое совершенно не возможно! Самым ярким тому доказательством, которое смело можно привести здесь в виде примера, являются топливные брикеты. Или как их многие называют — евродрова. Это все та же древесина которой отапливались наши предки, но за счет того, что в процессе брикетирования она получила некоторые новые свойства, за счет которых она может сгорать с большей эффективностью.
Для создания топливных брикетов не нужны какие-нибудь запрещенные технологии, космические наработки и т.д. В основе простейшего станка для брикетирования лежит обычный пресс. Поэтому наладить производство таких дров, с некоторыми улучшенными свойствами по отношению к обычным дровам, дело вполне реальное. Топливный брикет — это измельченная древесина, разнообразные стружки, опилки, угольные отходы и даже шелуха от семечек, которые спрессованы в определенную форму, удобную для хранения и транспортировки. Так же имеются и другие достоинства данного вида топлива.
Увеличенная температура горения и соответственно более высокая теплоотдача. Так как брикеты спрессовываются под большим давлением, то, соответственно имеют большую плотность, что позволяет им дольше гореть по сравнению с топливом такого же объёма. Брикеты уменьшают количество образования сажи и золы. И многое другое.
Вот о таком станке, который своими руками изготовил автор Ютуб-канала МихалычTV или своими руками и пойдет речь в данной статье.
Для работы необходимы:
сварочный станок
болгарка
дрель со сверлами разного диаметра
Шаг 1.
Автор приступает к изготовлению загрузочных бункеров. Для этого используется профильная труба квадратного сечения. Отпиливаются 4 заготовки необходимого размера, в которых сначала накерниваются места для отверстий, а потом высверливаются сами отверстия во всех всех заготовках со всех 4 сторон. После данной процедуры поверхности подвергаются шлифовке как изнутри, так и снаружи. Далее все детали сваривают, предварительно поставив между ними проволоку диаметром 6 мм. Это нужно для того, чтобы во время прессовки топливной массы из нее свободно выходила влага. Для того чтобы масса при загрузке не забивала межъемкостные промежутки, там будут приварены заглушки из той же проволоки.

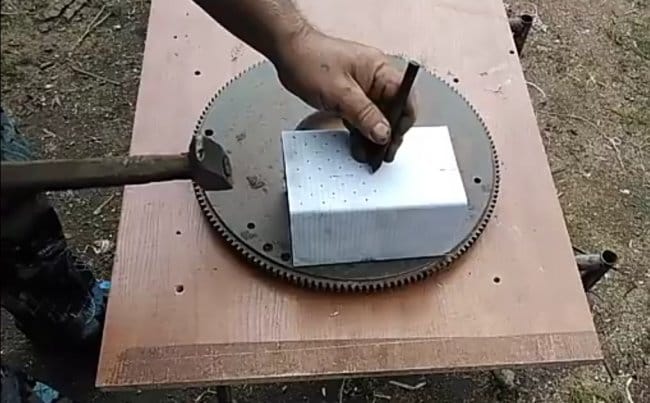

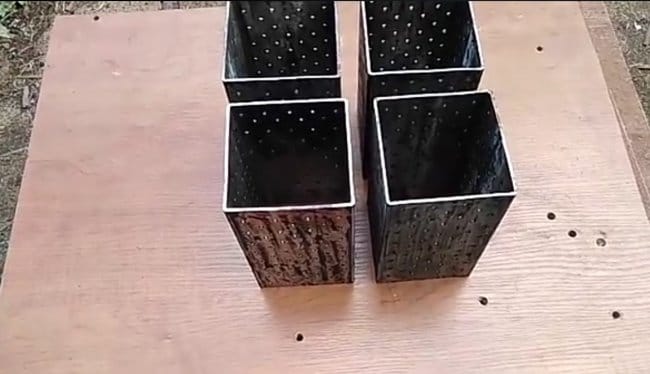
Шаг 2.
Нарезаются 4 металлические полосы, которые будут играть роль юбки на загрузочных емкостях. Служат они ограничителями, чтобы во время загрузки топливная смесь не выпадала за пределы емкостей. После автор изготавливает дно для емкостей. Оно должно быть открывающимся, чтобы полученные брикеты можно было легко и удобно извлечь из станка. Отрезается пластина, которая усиливается по бокам ребрами жесткости из профильной трубы или уголков. Это важный момент так как на эту часть станка будет приходиться вся нагрузка при работе пресса. В дне тоже делаются отверстия. Изготавливается шарнирное соединение для открывания дна.
Далее автор изготавливает так называемые поршни, которые будут входить внутрь загрузочных емкостей и прессовать смесь. Для этого к пластине приваривается 4 куска профильной трубы, на концах которых приварены площадки, размером как и диаметр загрузочных емкостей. Эти площадки будут давить на смесь и прессовать ее. Верх поршневой группы усиливается уголками. На нем будет установлен гидравлический домкрат.
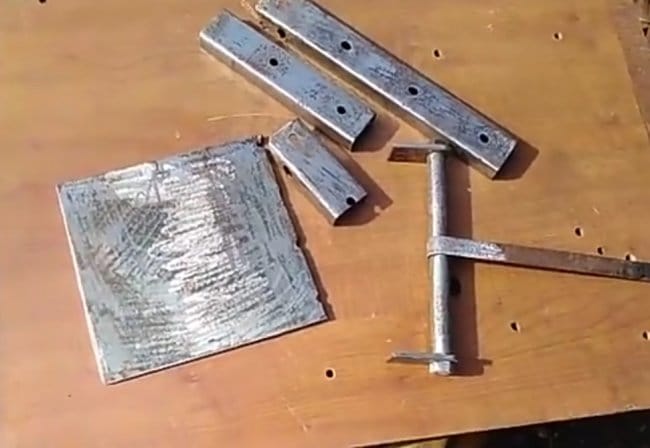

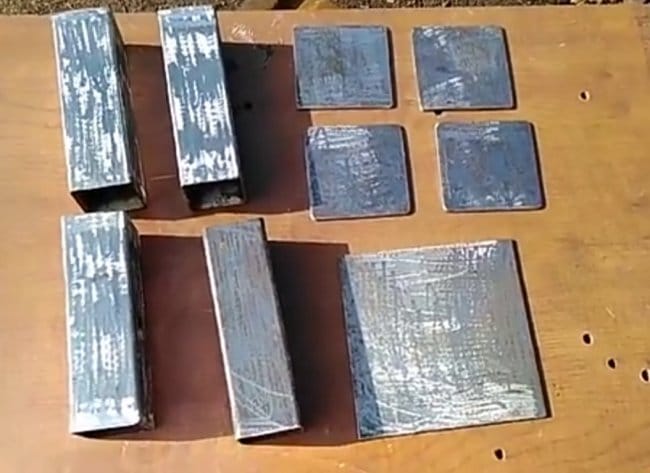
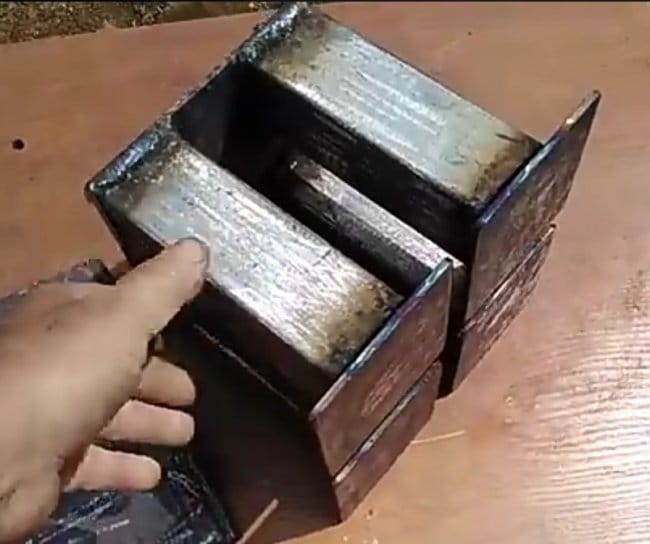
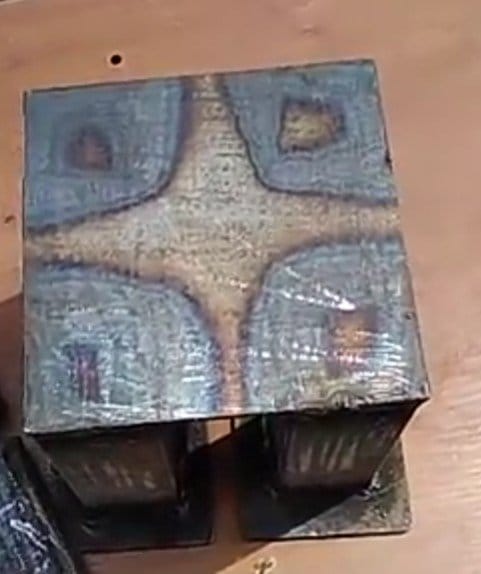
Шаг 3.
Автор начинает собирать изготовленные части в единое целое. Приваривается к основе ограничивающая юбка и опоры станка. Ставится дно.




Шаг 4.
К основанию станка привариваются упоры для гидравлического домкрата. Сам домкрат установлен на крышку поршневой группы и на поперечную перекладину, к которой он закреплен с помощью уголков на подвижное болтовое соединение. Имеющаяся сбоку длиная рукоять помогает в поднятии домкрата и поршневой группы для закладки топливной смеси. Конечно это очень неудобно и в плане загрузки, и в плане эксплуатации станка. Но тем не менее идея достаточно интересная и работоспособная.

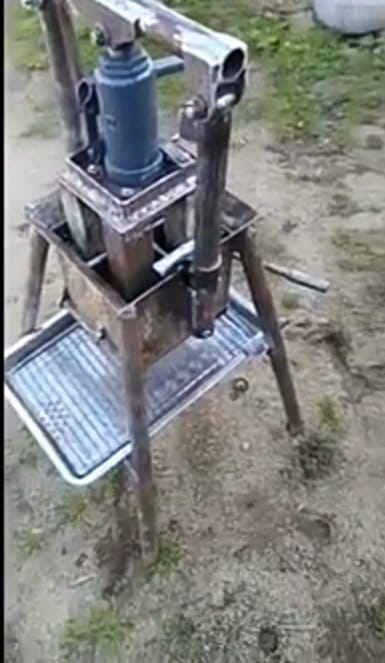
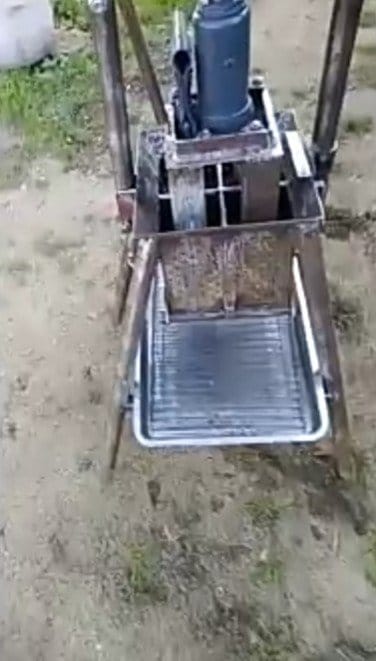
Вот, по словам автора, результат работы данного станка. Загружая большее или меньшее количество смеси, на выходе получаем брикеты нужного вам размера.


Источник
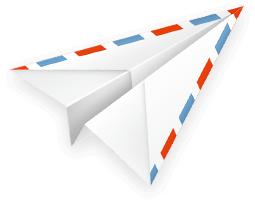
Получайте на почту подборку новых самоделок. Никакого спама, только полезные идеи!
*Заполняя форму вы соглашаетесь на обработку персональных данных
Становитесь автором сайта, публикуйте собственные статьи, описания самоделок с оплатой за текст. Подробнее здесь.Варианты станков для изготовления топливных брикетов
Современные технологии проявляют себя там, где, казалось бы, ничего нового не придумаешь. Примером тому являются топливные брикеты или, как их еще называют, евродрова. Это та же древесина, но за счет спецобработки получившая новые свойства, позволяющие ей сгорать с большей эффективностью.
Для их создания не требуются космические технологии – простейший станок для изготовления топливных брикетов представляет собой пресс. Поэтому наладить получение современного топлива с некоторыми свойствами, улучшенными по сравнению с обычными дровами, можно и своими руками.


Содержание статьи
Чем хороши брикеты
Топливный брикет – измельченная древесина и древесные отходы, спрессованные в форму, удобную для транспортировки и хранения.
В результате обработки на станках прессованием под высоким давлением готовые брикеты приобретают новые качества. Их применение вместо обычных дров в печах, каминах и дровяных котлах дает следующие преимущества:
- повышенная температура горения и, соответственно, лучшая теплоотдача;
- большая плотность брикетов приводит к более длительному горению одинакового объема;
- уменьшенное образование сажи и зольных остатков;
- брикеты выпускаются различной формы – короткие цилиндры, прямоугольные кирпичи. Но в любом случае они удобны для хранения и переноски.
Если сравнивать с обычными дровами, то ни по одному параметру евродрова не будут хуже. К недостаткам можно отнести то, что по внешнему виду брикета не всегда можно определить конкретную древесину, из которой он изготовлен. И если, например, требуется именно березовый брикет, то приходится положиться на добросовестность производителя.
Изготовление промышленным способом
Первым этапом при получении топливных брикетов в промышленных условиях является измельчение материала на специальных станках. Зачастую сырьем для изготовления брикетов служат отходы деревообработки – стружки, опилки, щепки. Крупные куски дерева измельчаются до состояния опилок размером не более 4 мм.
Затем происходит тщательная сушка древесины. Удельная влажность материала доводится до 10% и даже меньше. Чем суше древесина для последующего брикетирования, тем лучше качество готового топлива.
Завершающий этап – получение самих топливных брикетов. Для этого подготовленное сырье подвергают мощному давлению. Происходит повышение температуры, а из древесной массы выделяется клейкий компонент – лигнин. При большом давлении и в присутствии связующего лигнина древесная масса формируется в единый твердый брикет.
Плотность такого продукта превышает плотность природной древесины в 1,5-2 раза, что обеспечивает брикетному топливу повышенную теплоотдачу и увеличивает длительность горения. При промышленном производстве евродров различают два способа сдавливания.
Метод прессования
В случае прессования исходное сырье подвергается давлению в подготовленных формах с помощью гидравлического пресса. Типовая величина давления в станке для прессовочного производства топливных брикетов составляет 300-600 атмосфер. На выходе получаются брикеты в виде прямоугольных кирпичей или коротких цилиндров, в зависимости от формы, в которой они прессуются.
Метод экструзии
При этом методе происходит постоянное выдавливание древесной массы из выходного отверстия рабочего канала. Сырье загружается в бункер, оттуда подается в рабочий канал, где дополнительно разогревается. Канал выполнен в виде конуса, сужающегося к выходу. Подача сырья из бункера и его сдавливание в рабочем канале производится на станке шнековым винтом. Подобный пресс на основе шнека обеспечивает давление на сырьевую массу до 1000 атмосфер. Выходящая из экструзионной установки спрессованная «колбаска» охлаждается и нарезается на стержни нужного размера.
Брикетирование своими руками – за и против
Самостоятельно сделать пресс и наладить производство топливных брикетов возможно. Но это требует материальных затрат, физических усилий и времени. Надо учитывать и то, что достичь качества евродров, выпускаемых в заводских условиях, вряд ли получится. Конечно, можно приобрести станок, мало уступающий производственному, но затраты на приобретение будут колоссальными.
Необходимо хорошо представлять, для чего требуется собственное производство, какие есть для этого условия и какие предстоят затраты. Может быть, и не стоит отказываться от обычных дров или лучше закупать для отопления уже готовые брикеты.
Плюсы
Положительные стороны домашнего изготовления состоят в следующем. Собственные топливные брикеты не дадут качества горения, как у покупных, но будут эффективнее дров.
Если есть возможность получения большого количества древесных отходов – опилок, мелких обрезков, стружки, коры, – то из них выгоднее сделать спрессованные дрова. Опилки и стружка в чистом виде малопригодны для горения, а после обработки на станке для прессовки опилок из них выходит хорошее топливо.
Можно пустить в дело не только дровяные, но и любые другие горючие отходы – солому, сухие листья, бумагу, картон. По отдельности из них горючий материал – никакой, а в брикетах будет толк. Брикетированное топливо удобно для складирования и для загрузки в топку.
Минусы
Но есть и недостатки, о которых следует помнить. Попытки улучшить качество самодельных евродров могут привести к тому, что будет покупаться дорогостоящее оборудование или постоянно дополняться существующее. В итоге окажется, что выпуск собственных брикетов не оправдает затраты.
Самодельным топливным брикетам требуется место для качественной сушки. Просушивание на солнце не всегда оправданно. Требуется просторное сухое помещение. Хранить самодельные брикеты тоже надо так, чтобы они не впитывали влагу.
Домашние связующие материалы
На самодельных станках добиться давления, при котором из древесной массы выделяется лигнин, практически невозможно. Поэтому в сырье для самостоятельного брикетирования обязательно надо добавлять материалы, которые помогут связать, склеить сырье в монолитный брикет. Чаще всего для этих целей используют:
- глину. Объемная пропорция 1 к 10 древесного сырья;
- клей. Годится любой, но, естественно, лучше брать самый дешевый;
- измельченную бумагу или картон. Помимо того что это тоже горючий материал, в бумаге содержится лигнин. А бумажный лигнин свои клейкие свойства проявляет при замачивании. Правда, потом понадобится дополнительное время на просушку брикетов, содержащих бумагу.
Чтобы связующие добавки в полной мере проявили свои свойства, их надо тщательно перемешивать с горючим сырьем, а потом эту смесь замачивать в воде.
Обратите внимание! При промышленном производстве сырье перед прессовкой тщательно высушивают, а при самодельном – тщательно замачивают.
В этом основное отличие домашнего изготовления. Сушат топливные брикеты уже после прессовки, чтобы они затвердели, держали форму и хорошо горели.
Самодельный станок
Встречаются сведения об изготовлении в домашних условиях самодельных шнековых экструзионных установок. Но даже создатели таких эффективных станков для производства топливных брикетов отмечают, что устройства требуют качественных материалов и использования электродвигателя. Гораздо легче сделать вместо сложного станка обычный пресс.
Ручной пресс
Прессы, использующие только ручные усилия, бывают двух видов – винтовые и рычажные. В винтовых вариантах шток, сдавливающий сырьевую массу, перемещается накручиванием винта. В рычажных прессах давление создается собственными мускульными усилиями, используя длину рычага. На винтовой установке достигается большее давление и качество топливных брикетов становится лучше. Но закручивание и откручивание винта требует времени, поэтому производительность невелика. Рычажные прессы работают быстрее. Нужно только продумать способ или механизм выталкивания готового брикета из прессовочной формы. В этой же форме должны быть отверстия для выхода воды при сдавливании, поскольку при ручном производстве сырье замачивается.
Измельчители
Важным этапом в производстве брикетов является измельчение древесного сырья. Конечно, можно делать это вручную, с применением простейших резаков. Но эффективнее будет механизировать этот процесс. Подойдет роторный станок, применяемый для измельчения растительной массы при производстве удобрений в домашних условиях. Умельцы применяют для этих целей и старые стиральные машины активаторного типа. На активаторе крепятся ножи, измельчающие загруженное сырье.
Станок с использованием готовых механизмов
Усовершенствовать ручной станок можно, снабдив его готовым гидравлическим домкратом или покупным гидравлическим прессом. Потребуются также материалы для крепления механизма и изготовления других элементов конструкции. Форма матрицы, в которой будет прессоваться сырье, может быть круглой или прямоугольной. Для круглых форм можно использовать стальные трубы нужного диаметра.
Основание станка для изготовления топливных брикетов сваривается из швеллеров. Для стоек подходят уголки размером 100 х 100.
Для формовочной матрицы берется толстостенная труба. Диаметр подбирается исходя из желаемых размеров готовых изделий. В трубе равномерно высверливаются несколько отверстий диаметром 4-5 мм для выхода воды при сжатии.
Матрица оборудуется съемным дном, необходимым для извлечения готовых брикетов. Но есть более перспективный вариант: дно приваривается к матрице намертво, а с внутренней стороны крепится пружина с диском чуть меньшего диаметра. При прессовке пружина сжимается, а после отведения штока – разжимается, выталкивая диском спрессованный продукт.
Для штока подойдет труба миллиметров 30 в диаметре. К ней приваривается пуансон, свободно входящий в матрицу. Другой конец штока крепится к гидравлическому механизму.
Перед загрузкой в матрицу древесную массу желательно хорошо перемешать. Барабан для перемешивания можно сделать из листовой стали или взять готовый от стиральной машины. Закрепляется барабан на стойках.
Подающий лоток, по которому сырье из барабана загружается в матрицу, тоже делается из стального листа.
На такой установке вряд ли удастся получить сверхплотные евродрова. Но с задачей сделать из рассыпающегося сырья твердый брикет она вполне справится. В итоге из отходов получится продукт, по плотности равный древесине, но спрессованный в удобную форму.
drevogid.com
Как изготовить брикеты из опилок своими руками?
Брикеты из опилок пользуются большой популярностью в Европе из-за их экологичности и доступности. У нас такой вид топлива тоже достаточно востребован. Ими можно топить камин, печку или разжигать мангал. Изготовить брикеты из опилок возможно и своими руками, правда понадобится специальное оборудование и знания о выборе подходящего сырья.
Что такое брикеты из опилок?
В неподготовленном виде топить опилками не выгодно из-за низкого КПД теплоотдачи. Для увеличения КПД их брикетируют путем уплотнения. Брикеты имеют влажность на уровне от 10 до 12% и теплоотдачу в 4500 ккал/кг. Такой КПД в 2-4 раза выше, чем у дров. Это является причиной популярности готового брикетированного продукта.
У производителей изготовление брикетов пользуется популярностью по причине выгоды и дешевизны изготовления. Деревообработчики получают возможность достигать безотходности производства.
Прессуют опилки без добавок. Процесс уплотнения способствует выделению лигнина, естественного клейкого вещества, благодаря которому достигается высокая прочность.
Особенности изготовления промышленным способом
Промышленное производство брикетов из опилок включает два рабочих процесса – дробление сырья и прессование. Если пресс создает высокое давление – на выходе получаются уже готовые брикеты. При применении пресса более низкого давления, брикетам понадобится сушка. Используют как горячее, так и холодное прессование.
Самые мелкие опилки получаются при распиловке леса, их и используют для брикетов высшего качества. Из обычных древесных опилок тоже получается вполне достойное топливо.
На производстве процесс изготовления брикетов из опилок выглядит следующим образом:
- Опилки засыпают в контейнер дробилки для измельчения.
- Полученную фракцию прессуют. Пресс пропускает сырье через фильеры, позволяющие получить на выходе определенную форму брикетов.
- Фасуют брикеты в пленку.
Исходное сырье должно иметь влажность не более 10%. Процесс прессования создает давление, повышающее температуру опилок. Они досушиваются до влажности 4%. При такой влажности их можно упаковывать.
Виды форм топливных брикетов из опилок
Различают три формы, получаемые в процессе прессования:
- Кирпичи – форма RUF. Размеры- 150х100х60 мм. Влажность брикета до 10%, плотность порядка1,2 г/см3. Теплоотдачу дают в 4400 ккал/кг. Такие брикеты малозольные, хорошо горят. Упаковка весит 10 килограмм, в ней 12 брикетов. Производятся холодным прессованием и имеют большой срок хранения – 3 года.
- Карандаши – Pini Kay. Показатели влажности, теплоотдачи и плотности аналогичны RUF. Размеры -250х60 мм, с отверстием диаметром 18-20 мм. Горят прекрасно за счет наличия отверстия в середине брикета. Создается дополнительная тяга. Делаются шнековым прессованием при высоких температурах. Срок годности до пяти лет.
- Цилиндры – NESTRO. Влажность брикетов от 8 до 10%. Плотность -1,0 г/см3. Теплоотдача 3900 ккал/кг. Имеют длину от 200 до 380 мм. В диаметре такой цилиндр 90 мм. Делают брикеты прессованием при среднем давлении. Срок годности у них всего год и зольность выше, чем у двух других.

Лучше всего горят и долго хранятся Pini Kay и RUF. Хороши для отопления дома и растопки бани. Цилиндры лучше использовать для обогрева нежилых помещений из-за более высокой зольности.
Домашний способ прессования
Изготовление брикетов из опилок своими руками требует соблюдения определенной технологии и этапов производства.
Сырье и подготовка
Для изготовления брикетов из опилок своими руками нужно определенное сырье и оборудование. В качестве сырья можно использовать:
- опилки древесные, стружку и мелкую щепу;
- шелуху, полученную после обработки сельскохозяйственных культур – риса, гречихи, риса, подсолнечника;
- отходы угля и торфа – мелкая фракция;
- солому;
- макулатуру (картон и бумагу).
При выборе состава неоднородного сырья (из разных отходов), нужно помнить, что опилки должны занимать более 60%, чтобы обеспечить высокое качество горения.
Можно также использовать глину. В процессе домашнего прессования опилок лигнин не будет выделяться из-за низкой мощности пресса, поэтому понадобится связующее вещество, которым будет размоченный картон или глина. Картон вносят в подготовленное сырье в размоченном виде, он должен занимать не более трети объема. Глину вмешивают в опилочное сырье в пропорциях 1 к 10.
Некоторые умельцы вместо картона и глины вмешивают в сырье обойный клей. Он относительно натурален, но при наличии в нем химических добавок его использовать не рекомендуется. Брикеты при сгорании будут коптить.
Необходимое оборудование для производства брикетов из опилок:
- дробилка;
- пресс выбранной модификации.
- емкость для подготовки сырья.

Этапы изготовления брикетов из опилок своими руками
Процесс домашнего прессования опилок выглядит следующим образом:
- сушка сырья, если оно имеет высокую влажность;
- измельчение сырья в дробилке или ручным способом;
- перемешивание измельченного опилочного сырья с глиной или картоном;
- загрузка под пресс;
- прессование в формы;
- выгрузка и сушка на воздухе;
- упаковка в пленку.
Качество сушки можно проверить путем разлома брикета, он должен быть плотным и сухим на срезе.
Если нет подходящей дробилки – можно применить перфоратор.
Пленка обязательно должна быть термоусадочной, чтобы влага не проникала в готовый продукт и сохранялась его форма.
Прессы для изготовления брикетов из опилок
Для производства брикетов из опилок можно использовать три вида прессов.
Механизм с ручным приводом
Процесс изготовления: сделать раму из металлической трубы ( сварить ее). Раму прикрепить для устойчивости к стене любой постройки. В нижней части рамы неподвижно закрепить форму бля брикетирования. Сверху на шарнире надо закрепить длинный рычаг. К рычагу надо прикрепить пресс, который будет нажимать на сырье. Пресс должен быть меньше формы по размеру, чтобы вдавливать в нее массу. Таким прессом можно изготавливать брикеты небольшой формы.
Механический пресс может быть и винтовым. Он представляет собой емкость для сырья и металлическую станину, в которую вставляется пресс в виде винта с площадкой. Закручивание винта производит уплотнение сырья.
Плюсы такого механизма:
- простота изготовления своими руками;
- дешевизна материалов.
Минусы:
- большие усилия прессования;
- высокий износ рабочих элементов.

Механизм с гидравлическим домкратом
Изготовить его – процесс невыполнимый, но можно взять готовый автомобильный гидравлический домкрат. Минимальная его грузоподъемность 2 тонны. Усилие домкрата должно быть направлено вниз – к форме с сырьем.
Плюсы механизма:
- большое усилие прессования дает возможность получить качественные брикеты;
- можно получить брикеты разной формы.
Минусы:
- громоздкость сооружения;
- при покупке обойдется не дешево.
Шнековый пресс
Шнековый пресс напоминает мясорубку. Сделать его дома очень сложно, проще взять бывший в употреблении. Основная рабочая деталь в прессе – это шнек, он несет основную нагрузку и обеспечивает формирование брикета.
Шнековым прессом создаются брикеты в форме прямоугольника или восьмиугольника, в центре есть отверстие. Плотность таких брикетов очень высокая, они долго и равномерно горят.
Плюсы оборудования:
- высокое качество брикетов.
Минусы пресса:
- покупка обойдется не дешево.
Плюсы и минусы самодельных брикетов
Преимущества топливных самодельных брикетов из опилок:
- углекислого газа выделяется намного меньше, чем при топке дровами или углем;
- компактный продукт, требующий мало места для хранения;
- материал не гниет из-за высокой плотности;
- ровно и красиво горит;
- в доме не будет мусора и пыли;
- экономия средств, при условии доступности сырья и оборудования для изготовления;
- брикеты долго горят – до четырех часов;
- выделяется мало дыма;
- не выбрасываются в воздух вредные вещества;
- чистку дымохода можно будет производить в три раза реже;
- экологично и безопасно;
- мощность котла увеличивается на 50%;
- сжигание угля дает зольность 20%, а брикетов 1-1,5%;
- кубометр брикетов из опилок по уровню теплоотдачи равен 4-6 кубометрам дров.

Недостатки самодельных брикетов из опилок:
- при недостаточном усилии пресса, брикеты могут рассыпаться;
- в домашних условиях готовые брикеты трудно хорошо высушить. В летнее время их можно просушить на солнце, а в другое время года – только в помещении, что не дает сильного снижения влажности. Соответственно они будут хуже гореть.
- изготовление и сушка брикетов требуют много места;
- процесс изготовления крайне трудоемкий и требует больших физических усилий.
Брикеты нужно хранить в сухом помещении. Срок хранения брикетов из опилок, сделанных в домашних условиях, не превышает года. Зола, получаемая от сгорания продукта, является прекрасным удобрением.
Самодельные брикеты из опилок являются дешевым и безопасным топливом. Если есть возможность их сделать своими руками, то брикеты сделают процесс отопления дома выгодным и экологичным.
pechiexpert.ru
особенности брикетирования на производстве и дома, выгодна ли прессовка в домашних условиях
Одним из лучших типов твёрдого топлива для отопления дома являются брикеты из опилок. Они занимают мало места, а также имеют высокую теплоёмкость. Но есть у такого горючего минус — позволить себе дорогостоящий материал может не каждый. Поэтому многие домовладельцы изготавливают пресс для опилок самостоятельно.
Подходы к изготовлению
Прежде чем приступать к изготовлению топлива самостоятельно, нужно понимать, на чём основано его производство на заводе. Неважно, в каких условиях изготавливают сырье, в домашних или промышленных: подготовительный этап одинаковый. Он состоит из измельчения сырья и его сушки. В качестве материала используют крупные отходы деревообрабатывающей промышленности и опилки. Иногда применяют агропромышленные отходы, например, шелуху семечек или угольную пыль. Влажность сырья после просушки не должна превышать 8%.
Следующий этап изготовления — брикетирование опилок или прессовка. Существует 2 способа проведения этого процесса:
- Создание брикетов с помощью гидравлического пресса.
- Способ экструзии.
Какая бы технология ни была выбрана, нужный результат достигается благодаря сильному давлению на сырье. В процессе прессовки из него начинает выделяться лигнин, природный компонент. Именно он не даёт рассыпаться материалу. При работе на гидравлическом прессе опилки хорошо формируются в виде кирпича. Этому способствует произвольное разогревание опилок.
Принцип метода экструзии напоминает работу соковыжималки или мясорубки. Сначала материал отправляют в специальный бункер. Он переносится в рабочий канал агрегата с помощью шнека. Именно там начинается сжатие и прессование под усилием в 1000 бар. В итоге машина выдаёт брикетированные дрова из опилок. Они имеют форму шестигранника. Брикеты проходят дополнительную термическую обработку.
Домашняя методика
Конечно, приобретение мощного профессионального оборудования для домашнего использования не имеет смысла. Стоимость такого агрегата окупится только в случае производства прессованных дров на продажу. К сожалению, придерживаться стандартной технологии, при которой выделяется лигнин, не получится.
Заменить отходы деревообрабатывающего производства можно ветками деревьев после зимней обрезки.
Перед прессованием их необходимо измельчить дробилкой. Также можно использовать материалы, которые хорошо горят, например, солома, бумага, шелуха семечек.
Домашние мастера придумали, как сформировать брикеты без природного связующего вещества. Взамен лигнина нередко используют:
- Глину.
- Клей для обоев.
- Бумагу и картон.
Умельцы смогли обойти отсутствие брикетировочного пресса для опилок. Сырье замачивают в воде, после чего перемешивают в глине. При этом важно придерживаться пропорции 1:10. Если нет глины, добавляют размокшую бумагу или клей. Подготовленный материал отправляют в самодельный брикетировочный агрегат и прессуют усилием рук. Получившиеся брикеты вынимают из пресса и отправляют сушиться на свежий воздух.
Оборудование своими руками
Самодельный пресс для брикетирования опилок может быть с винтовым приводом. Ёмкость для формирования дров наполняют сырьём и устанавливают под неподвижную часть машины. Необходимое давление достигается за счёт закручивания ручного винта. Такие винтовые агрегаты не пользуются популярностью из-за плохой производительности. Загрузка сырья, прессование и сушка изделия требуют больших временных затрат.
Хорошей альтернативой винтовому прессу для прессования опилок является самодельная машина с улучшенным механизмом выталкивания готовых брикетов и длинными рычагами управления. Для ускорения прессования к станине приваривают 2 ёмкости вместо одной. Домашние мастера не остановились на этом.
Они создали улучшенный механизм: установили вместо ручных рычагов гидравлический домкрат. Но даже самодельный пресс с гидравлическим домкратом не сможет создать давление в 300 бар, поэтому повторить традиционную технологию в домашних условиях не получится.
Несмотря на трудоёмкость изготовления деталей и создания машины, некоторым мастерам удалось получить прессованные дрова высокого качества. Они собрали шнековый агрегат. Люди, которые пользуются такими прессами, отмечают, что производство шнека и корпуса машины требует огромных затрат. Кроме того, агрегат потребляет не менее 7 кВт — и это по самым скромным подсчётам.
Рациональность домашнего производства
Отопление с помощью опилок очень привлекательно для хозяев домов, а когда есть собственное производство дров, можно покупать сырье по низким ценам. Поэтому мысль о прессовании опилок в домашних условиях посещает многих. Перед тем как решиться на создание специального агрегата для этого, нужно знать некоторые тонкости.
Не для любой отопительной системы подойдёт такое топливо. Опилки в печке или котле мгновенно сгорают, не успевая отдать тепло.
Кроме того, немалая их часть осыпается в зольник. Для опилок необходим специальный котёл — шахтный или верхнего горения. Создать такой тип отопления очень непросто.
Прессованные опилки в виде брикетов использовать намного удобнее. Однако и здесь есть трудности:
Создавать брикеты самостоятельно невыгодно. Покупка промышленного оборудования для сушки и прессования обойдётся в круглую сумму. Намного дешевле купить готовые брикетированные опилки.
- Кустарный способ изготовления евродров в самодельном прессе для прессовки опилок куда дешевле. Продукты, сделанные в нём, имеют ненадлежащее качество. Они не дадут достаточного количества тепла. Кроме того, на создание машины, обработку сырья, изготовление и сушку изделия потребуется много времени.
Изготавливать евродрова в домашних условиях реально. Для этого требуется много свободного времени и сил, а также место для сушки и хранения материала. Требуется найти сырье по низким ценам и договориться с доставкой, чтобы она не обошлась слишком дорого. В противном случае самостоятельное изготовление брикетов из опилок теряет смысл, так как покупные дрова обойдутся значительно дешевле.
vtothod.ru