Преимущества пеллет (топливных гранул)
Пеллеты (топливные гранулы) — экологически чистый вид биотоплива. Пеллеты производят из предварительно измельченного и высушенного растительного сырья без химических закрепителей, которое прессуют под высоким давлением.
Сырьем для производства пеллет служат древесные отходы, которым необходимо переработка.
Вид и размеры пеллет
По внешнему показателю пеллеты представляют собой прессованные, цилиндрической формы материал, диаметром до 25 мм. Широкое применение получили пеллеты диаметром 6-10 мм.
Данная форма благоприятствует фактору сыпучесть и позволяет использовать все известные способы автоматизации в подающих устройствах котельных. Учитывая именно этот фактор, следует сказать, что пеллеты стали основным прессованным топливом в Европе.
Соломенные пеллеты используют еще в качестве подстилки для скота, а пеллеты из травы или сена считаются ценным кормом. По технологии производства пеллет за счет обработки паром, количество усваиваемых белков увеличивается.
Плотность пеллет, образованная под действием высокого давления, достигает 1, 25 т/м3. Влажность пеллет – 10…12%. Для сравнения: у сырой древесины уровень влажности составляет половину веса. Таким образом, пеллеты – это концентрированный источник энергии. По определению теплотворная способность пеллет в 5-7 раз превышает теплотворную способность сырья такого же объёма, и равна теплотворности каменного угля.
Область применения пеллет
Пеллеты используют в котельных и ТЭЦ широкого диапазона мощности — от каминов и котлов в частных домах до ТЭЦ мощностью более 500 МВт, которые расходуют 450 тыс. тонн пеллет в год.
Преимущества эксплуатации древесных гранул.
- Высокая теплотворная способность — 4,8 кВт/час/кг (средняя), сопоставимая с теплотворностью каменного угля.
- Транспортировка и простой способ хранения топливных гранул.
- Высокая насыпная плотность, 650 кг/м3 и сыпучесть.
- Дает возможность производить эффективную транспортировку на большие расстояния с помощью любого вида транспорта.
- По статистике объём, занимаемый пеллетами при сопоставимой теплотворности, в 5 раз ниже, чем у щепы, и равен объему угля.
- В процессе производства выполняется сушка, во время которой пеллеты биологически неактивны. Они не гниют в течение длительного времени и не утрачивают своих полезных свойств.
Автоматизация сжигания пеллет
Стандартный размер и устойчивость свойств пеллет дают возможность автоматически совершать перемещение и дозирование в сжигающих установках.
Небольшие относительные энергозатраты при производстве пеллет
Для производства пеллет необходимо 5% электроэнергии от энергоемкости пеллет и до 15-20% тепловой энергии, используя сырое сырье. Тепловая энергия получается из сырья для пеллет и учитывается в сырьевом балансе.
Безопасность
Влажность — 10-12%
Пыль <1%
Пеллеты производят из высушенного сырья, используя метод прессования. Пеллеты не расположены к самовоспламенению и не взрывоопасны.
Следующие важные параметры пеллет:
- Зольность
- Плотность
- Истираемость
Следует обратить внимание на то, что при сжигании пеллет в промышленных установках с автоматическим золоудалением, их зольность не имеет большого значения.
Экологичность
Использование полезных качеств пеллет благоприятствует снижению загрязнения атмосферы. Применение топливных гранул признано и поддерживается на государственном и межгосударственном уровнях (Киотский протокол), а также международными экологическими фондами (NEFCO, SIDA и др.) и общественными организациями. Использование биотоплива возведено в ранг национальных приоритетов многими странами.
Древесные пеллеты украинского производства | AW-Therm.com.ua
Топливные гранулы из древесины в Украине в настоящее выпускают десятки крупных и сотни мелких производителей, обеспечивая при этом потребности внутреннего рынка, а также экспортируя продукцию в развитые страны
Применение пеллет из древесины получило широкое распространение в мире ввиду чрезвычайного удобства их использования. В развитых странах они относятся к возобновляемым, экологически чистым природным ресурсам. Однако это во многом справедливо лишь в том случае, если для их производства используются специально высаженные быстрорастущие деревья. К таким породам относятся, например, тополь, ива. Отдельно можно отметить перспективность производства пеллет из отходов деревообработки.
По данным Украинского пеллетного союза, на сегодня в нашей стране зарегистрировано 347 предприятий по производству или продаже твердого биотоплива. За 2014 г. ними было произведено 380 тыс. т древесных пеллет и 178 тыс. т брикетов из древесины. Средняя мощность предприятий составляет 380 т в месяц. Хотя есть и заводы мощностью 5 или даже 10 тыс. т в год.
Пеллеты производства «Биоэнергосбыт»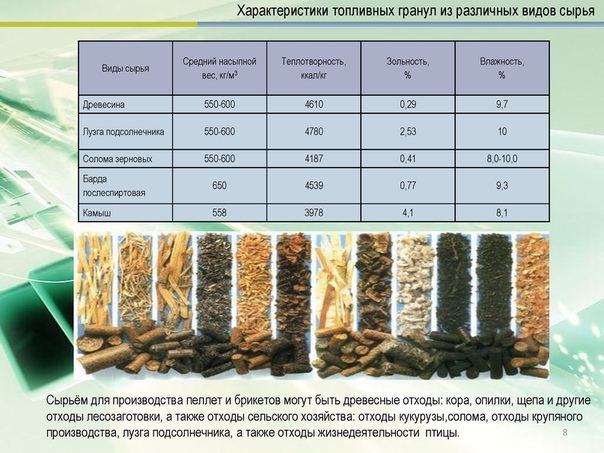
ООО «Киев Пеллетс» предлагает древесные гранулы диаметром 6 и 8 мм, соответствующие европейским стандартам.
В частности, пеллеты стандарта ENplus-A1 диаметром 6 мм производятся из древесины хвойных пород, выросших в Черниговской области. Они характеризуются минимальной теплоотдачей 18,4 МДж/кг. Остаточная зола составляет 0,31%. Пеллеты древесные размера 6 и 8 мм DIN plus – также из древесины хвойных пород. Происхождение товара – Киевская область. Теплоотдача топлива – свыше 18,5 МДж/кг, остаточная зола – 0,35% от веса.
Древесные топливные гранулы DIN производятся диаметром 6 и 8 мм из древесины хвойных и твердых пород в Житомирской области.
Производители указанных типов пеллет сертифицированы Украинской биоэнергетической ассоциацией, а также качество подтверждено заключениями независимых лабораторий SGS, Incolab Services. Согласно исследованиям, содержание серы в топливе составляет 0,012%, насыпная плотность – 650 кг/м3, теплота сгорания – 5030 ккал/кг.
Пеллеты ENplus-A1 и DIN plus поставляются в полиэтиленовых пакетах весом нетто по 15 кг, DIN – в мешках по 40 кг. Кроме того, для пеллет DIN plus предусмотрен вариант поставки в четырехстропных «биг-бэгах» весом нетто 900–1200 кг, а также насыпом в специализированном автотранспорте. При этом выгрузка древесных пеллет производится автоматически через гнущийся рукав длиной до 30 м. Отгруженный тоннаж фиксируется на дисплее пульта управления в автомобиле.
Компания также предлагает древесные брикеты типа Pini Kay, RUF и круглые брикеты различного качества из древесины хвойных и твердолиственных пород.
Компания предлагает светлые пеллеты из твердых пород дерева: граб (более 50% состава), дуб, береза, клен, ясень. Диаметр – 8 мм, длина – 10 мм. Зольность топливных гранул – 1,21 %. Влажность: 3,1 %. Теплота сгорания – 20,33 МДж/кг. Поставки производятся в мешках по 25 кг или «биг-бэгах» по 1 т.
СПД «Пеллет 2014» – отечественный производитель пеллет из древесных отходов. В качестве сырья применяются опилки, кора и т. д. Готовые гранулы пакуют в упаковку – от небольших пакетов 15 кг до «биг-бэгов» весом 1 т. Диаметр пеллет – 4 – 10 мм, длина – 10 мм. Зольность – 1,5 %, влажность – 8 %. Теплота сгорания: 5,079 МДж/кг. Продукция сертифицирована согласно DIN 51 731.
Пеллеты производства «Пеллет-Энерго»«Пеллет-Энерго Украина», входящая в группу компаний KM Core, выпускает древесные пеллеты, состоящие на 80% из сосны и на 20% из смеси таких лиственных пород древесины как дуб, береза и осина.
Компания предлагает пеллеты древесные светлые диаметром 6 мм, изготовленные из хвойных пород деревьев (ель, сосна). Влажность гранул – 8,1%; зольность – 0,26%. Нижняя теплота сгорания: 17,93 МДж/кг. Высшая теплота сгорания: 21,13 МДж/кг. Плотность: 1,21 г/см
Производственно-коммерческое объединение «Центрум» специализируется на производстве и реализации древесных топливных гранул диаметром 8 мм и длиной 10 мм. Их основные характеристики: зольность – 1%; влажность – 7%; теплота сгорания – 19 МДж/кг. Поставки осуществляются партиями по 2–66 т. Кроме того, предприятие выпускает пеллеты из соломы.
Производимые предприятием древесные пеллеты имеют диаметр 8 мм и насыпную плотность около 700 кг/м3. Зольность, в соответствие с лабораторными исследованиями, составляет 0,48%, содержание влаги 7,8%, серы – 0,012%. Теплота сгорания – 19,28 МДж/кг. Базовым сырьем для производства древесной гранулы является сосна, которая, после рубки и размельчения, подвергается процессу сушки при температуре от 200 до 350 ˚С (в зависимости от исходной влажности сырья). Пеллета имеет светло-коричневой цвет. Готовая продукция транспортируется автомобильным транспортом в джутовых мешках типа «биг-бэг» или в полиэтиленовых мешках на 15 кг.
Пеллеты производства «Экогран»ООО «Экогран» производит индустриальные древесные гранулы, которые используются в качестве топлива для промышленных котельных и тепловых электростанций. Пеллеты выпускаются диаметром 6 или 8 мм. Согласно результатам лабораторных исследований, гранулы содержат 5,9% влаги, 0,8% золы, 0,01% серы. Выход летучих веществ в рабочем состоянии составляет 79%. Теплота сгорания – 4315 – 4935 кал/кг. Компания сотрудничает как с внутренними потребителями, так и осуществляет поставки своей продукции на экспорт. Основной вид используемого транспорта – железнодорожный.
Компания «Экопеллет» занимается производством и продажей пеллет, изготовленных из древесины, в Черниговской области (завод находится в зоне действия 4-х лесхозов). Гранулы спрессованы под высокой температурой и давлением из сухих чистых древесных опилок. Состав пеллет – 100 % опилок из бревна сосны. Основные характеристики выпускаемой продукции: зола – 0,41%, влажность – 6,73%, сера – 0,01%, хлор <0,02%, азот <0,30%. Теплота сгорания – 5039 – 5061 ккал/кг. Размеры пеллет: диаметр – 6 и 8 мм, длина <30 мм. Теплотворная способность 21 МДж/кг (5,0 кВт·ч/кг). Плотность – 1,12 кг/дм³.
Пеллеты для промышленных потребителей фасуются в мягкие полипропиленовые контейнеры типа «биг-бэг» по 1–1,2 т, либо отгружаются насыпом в самосвалы – от 27 т. Для частных потребителей и небольших котельных используются полипропиленовые мешки по 20–40 кг.
Предприятие также производит топливную древесную щепу.
Пеллеты производства «Эко Прайм»Предприятие производит древесные гранулы диаметром 6 мм из химически необработанной стволовой древесины хвойных пород (сосна, ель). Перед дроблением с каждого бревна специальным станком снимается кора. По своим физическим характеристикам пеллеты соответствуют европейским стандартам, в том числе DIN EN 14961-2 (А1). Длина пеллет – от 7 до 30 мм; влажность – 4,5%; зольность – 0,64; содержание серы – 0,01%. Насыпная плотность – 720 кг/м3. Теплота сгорания – 17,87–20,19 МДж/кг. Выход летучих веществ в рабочем состоянии – свыше 80,5%. Продукция, по желанию заказчика, может быть упакована в «биг-бэги» по 1,1 т или полиэтиленовые мешки по 15–25 кг.
Предприятие, входящее в состав международной группы Barlinek, специализирующейся на изготовлении паркетной доски. Остатки древесины основного производства используются для выпуска топливных гранул и брикетов. При этом сырьевой материал подвергают тщательному отбору и обработке. Пеллеты Barlinek – первые топливные гранулы в Украине, которые имеют два сертификата качества DIN Plus и EN Plus A1.
Стандартный состав для пеллет диаметром 8 мм: 70% опилок хвойных пород древесины и 30% – лиственных. Длина пеллет до 40 мм. Теплотворная способность топлива – не менее 18000 кДж/кг (около 5,3 кВт·ч/кг). Содержание золы – до 0,7%, влаги – до 10%. Насыпная плотность ≥600 кг/м3. Гранулы упакованы в мешки по 25 кг и сложены по 1000 кг на поддоне.
В группе компаний BKM Wood, производят топливные пеллеты ТМ BioPellets. Используется сырье из древесины, произрастающей на территории Буковины (Черновицкая обл.): бук, ель, сосна. При этом соотношение сырья в готовой продукции – 70% бука и 30% хвойных пород. Плотность – 650 кг/м3, высшая теплота сгорания – 4814 ккал/кг. Удельная теплота сгорания ≥ 18 MДж/кг. Диаметр пеллет – 6 мм.
Процесс формирования пеллет происходит под давлением около 300 атм. при температуре 120–170°С. Связующий материал – лигнин. Пеллеты выпускаются двух типов: для применения в домашних и промышленных котлах.
Топливная пеллета диаметром 6 мм для бытового применения отличается более светлым цветом, что обусловлено минимальным содержанием древесной коры. Соответственно, данный тип пеллет имеет малую зольность – до 0,7% и влажность – до 7%. Длина пеллеты – 25–35 мм.
Промышленная пеллета – более темная, с примесями коры. Ее характеристики: зольность – 0,9%; влажность – 7,05%; длина – 15–30 мм.
Поставки осуществляются в полиэтиленовых мешках по 15 кг, либо в упаковке «биг-бэг» – 1 т. Мешки укладываются на деревянный поддон и обтягиваются пленкой.
Параметры механической прочности пеллет ТМ BioPellets позволяет перевозить их на дальние расстояния без потери качества и в рамках стандарта образования пыли – не более 2%.
Пеллеты производства Ditek PelletsКомпания является производителем и экспортером древесных топливных гранул в страны Евросоюза, а также занимается мелкооптовой и розничной реализацией пеллет на территории Украины. Производимая продукция соответствует маркам ENPlus A2 и DIN Plus, производимым по международным стандартам. Продукция фасуется в «биг-бэги» или мешки по 15 кг. В частности, компания предлагает пеллеты древесные из сосны диаметром от 4 до 10 мм, длиной 10 мм. Зольность – 0,8–1,2%, влажность – 7%. Теплота сгорания: 18,06 МДж/кг.
Пеллеты производства EcoPelletКомпания работает в направлениях поставок биотоплива (пеллеты, дрова, брикеты), а также продаж систем отопления и котельного оборудования для их сжигания. Зольность пеллет – до 0,6%. Влажность – до 4,3 % Теплота сгорания – выше 18 МДж/кг. Упаковка – мешки по 15 и 40 кг, Big bag по 1000 кг.
Пеллеты стандарта DINplus из массива сосны без примесей коры для бытовых котлов характеризуются зольностью 0,32% и влажностью 5,37%. Диаметр – 6 мм. Теплотворная способность: 19 МДж/кг.
Древесные пеллеты DINplus диаметром 6 мм из твердых лиственных пород имеют зольность 0,37 %, влажность 4,37 % и теплотворную способность 18 МДж/кг.
Пеллеты древесные для бытовых и промышленных котлов стандарта ENplus-A1 диаметром 6 мм характеризуются зольностью 0,65 %, влажностью 4,37 %. Теплотворная способность: 19 МДж/кг.
Компания также предлагает светлые пеллеты из сосны диаметром 8 мм с зольностью 0,34 % и содержанием влаги 4,96 %. Теплотворная способность – 19 МДж/кг.
Пеллеты производства VNT-GroupVNT-Group занимается производством и продажей древесных топливных пеллет из мягких хвойных пород дерева: сосна. Исходный материал (деревянная колода) доставляется в дробилку, где дробится до состояния щепы. Она поступает в «мельницу», сушку и пресс-гранулятор, где измельчается в древесную муку, просушивается, а затем прессуется в гранулу. После этого гранула поступает в охладитель, предназначенный для отвода лишней температуры и влажности от вновь сформированной гранулы. В конце, уже готовая гранула проходит процесс отсеивания негранулированной биомассы и мелкой крошки, и упаковывается.
Базовый вариант производства – топливная гранула для бытового и промышленного использования диаметром 8 мм, длиной 25–35 мм, упакованная в полиэтиленовый мешок весом 15 или 25 кг, или мешок типа Big-bag.
По результатам теста, согласно EN/TS 14774-2, пеллеты имеют следующий состав: зольность – 0,34%, влага – 4,96%, сера – 0,01 %, летучие вещества – 80,63%. Низшая/высшая теплота сгорания – 4650/4972 ккал/кг.
Читайте статьи и новости в Telegram-канале AW-Therm. Подписывайтесь на YouTube-канал.
Вам также может понравиться
Заказ был отправлен, с Вами свяжется наш менеджер.
Цены и новости на рынке леса и пиломатериалов
Новости и события
; www.fzlomov.ru работает с 1858 г. В 2019 г. выпуск фанеры 25 тыс. м3, экспорт, с 2017 г. — пеллет Компания «Орион» (Удмуртская Р., г. Ува) http…
из осины, пеллет и шпона. NEW В 2019 г. — сертификат на выпуск шпона — весь на экспорт ФК «Вологодская фанера» (г. Вологда) fanera35.ru…
— 762, 9 тыс. куб. м.; Пеллеты — 57, 6 тыс. т.
ООО
«Патриот» Вологодская
область. ..
лесосеки, 6309 тыс. м3 Пиломатериалы — 563 тыс.куб.м, Пеллеты — 220 тыс. тонн; целлюлоза — 375 тыс…
тыс. м3 ПМ, 16 тыс. м3 шпон, 4 тыс. тонн пеллеты. 2026 г. – окончание проекта «Создание нового завода по производству шпона с собственным циклом лесозаготовки». В дек. 2018…
. 2021 г. ГК «Свеза» сообщила о намерении компании инвестировать в создание нового лесопильного завода в Вологодской области мощностью 255 тыс. м3 сухих пиломатериалов и 35 тыс. тонн пеллет…
Информация
Предприятия по выпуску фанеры – ПФО, средние
Предприятия по выпуску фанеры – СЗФО, средние
Пиломатериалы, пеллеты, дома — проекты «ПИП» — СЗФО
Предприятия по выпуску фанеры – ПФО, средние
Предприятия по выпуску фанеры – СЗФО, средние
Пиломатериалы, пеллеты, дома — проекты «ПИП» — СЗФО
Каталог организаций и предприятий
«Компания ТД «Щебеночный завод» реализует щебень (гранит, доломит, известняк) фр. 3(5)-10, 5-15, 5-20, 10-20, 10-40, 20-40, 25-60, 40-70, камень бутовый 70-150, 150-300, отсев 0-0-5, 0-10. ЖД-доставка…
Мы являемся производителями оборудования для производства кормов и пеллет. Наши продукты: Гранулятор, Экструдер, Оборудование для производства комбикорма, Оборудование для производства пеллет, Линия п…
Производство и продажа оборудования для производства пеллет: пресс-грануляторы, грануляторы, грануляторы с плоской матрицей, мини-грануляторы, сушилки опилок, дробилки древесных отходов, молотковые дробилки, рубительные машины, охладители и просеиватели…
Оптовая продажа пеллет. Древесные топливные гранулы в наличии. Пеллеты 6мм. Пеллеты 8мм…
Продажа зерновых, изделий из стали, ферросплавов, упаковки, топливных пеллет…
Поставки топлива в организации, собственное производство топливных древесных брикетов, пеллет. Доставка в регионы.
Предложения на покупку и продажу продукции
ООО «ПФ «Стандарт» предлагает Вам ознакомиться с ассортиментом back-покрытий (компенсационные покрытия, баланс-бумага) для мебельных производств, от российского производителя. Материалы специально раз…
ООО «ПФ «Стандарт» предлагает фенольные пленки для ламинирования фанеры: Плотность 120, 135, 150, 220 гр/м2. Ширина роликов 1270 и 1560 мм. Цвета: коричневый, черный и другие. Бумага основа «Nordic P…
Скидки до 50% на оборудование GRAN для производства пеллет из опила и др. отходов производства. На нашем оборудовании Вы можете зарабатывать на ваших отходах. В наличии! Пеллетайзер GRAN – новое слово…
Компания КАИС реализует Пеллеты EnPlusA1 светлые Диаметр:6 мм Зольность: 0, 33% Влажность: до 7, 1% Теплота сгорания: 18, 32 МДж/кг Пеллеты — топливные гранулы, получаемые прессованием отход…
Компания реализует Пеллеты светлые Диаметр: 6 мм Зольность: 0, 33% Влажность: 7, 1% Теплота сгорания: 18, 32 МДж/кг Пеллеты — топливные гранулы, получаемые прессованием отходов деревообработки при н…
ГОСТы, ТУ, стандарты
Стандарт не распространяется на никелевый порошок, получаемый восстановлением никелевых соединений. Ключевые слова — порошок никелевый;марки;химический состав;насыпная плотность;безопасность;методы контроля;транспортирование;хранение.
Заглавие на русском языке — Порошки металлические. Определение насыпной плотности.
Заглавие на русском языке — Порошки металлические. Определение насыпной плотности. Часть 1. Метод с использованием воронки.
сорта: ПВХ-Е-7050-М, сорт высший ГОСТ 14039-78 То же, для переработки через пасты, с величиной К от 66 до 69, с ненормируемой насыпной плотностью, с остатком на сите с сеткой № 0063 — 5 %, для переработки через средневязкие пасты, первого сорта…
Таблица 3 Насыпная плотность, г/см3 0 Без данных 1 0, 30 — 0, 40 2 0, 35 — 0, 45 3 0, 40 — 0, 50 4 0, 40 — 0…
Плотность определяют по ГОСТ 15139 методом гидростатического взвешивания. Продолжительность пребывания образца в воде должна быть не более 1 мин. Допускается определять плотность методом обмера и взвешивания образца.
Пеллеты для отопления и не только
Топливные пеллеты получили широкое распространение в России и применяются в твердотопливных и пеллетных котлах. Это древесные гранулы цилиндрической формы спрессованные особым методом. Сырьем для пеллет может послужить различное растительное топливо не только опилки. Для создания пеллет берут за основу отходы мебельных производств, солому, кукурузные стебли, лузгу подсолнечника и гречихи.
В зависимости от исходного сырья показатели теплоотдачи топливных пеллет немного меняются, но все равно остаются более высокими чем у обычных дров. Обусловлено это тем, что при прессовании плотность пеллет во многом превышает плотность древесины. Соответственно при меньшем расходе топлива удается получить большую теплоотдачу.
Качество пеллет их хранение и перевозка
На производительность отопительного оборудования оказывает больше влияние качество топлива. Пеллетные котлы на данном этапе все еще нуждаются в регулярных чистках, так как топливо имеет небольшую зольность. Данный показатель очень важен и в первую очередь учитывает покупателями. Обычно в спросе чистые древесные пеллеты с минимальной зольностью, они практически белого цвета.
При изготовлении пеллет от производителя зависит очень многое: прочность гранул, качество соединяющего компонента. Пеллеты высоко ценят за то, что они являются экологически чистым топливом, не загрязняют атмосферу и являются продуктом переработки отходов.
Транспортировка прессованного топлива осуществляется с минимальными требованиями к безопасности. При перевозке пеллет самовозгорание не возможно в отличие от жидкого топлива.
Одним из недостатков пеллет является их относительная хрупкость. То есть при сильном давлении прессованные гранулы разрушаются. Топить таким материалом неудобно и нецелесообразно, теплоотдача падает.
Для того чтобы сохранить гранулы целыми, производитель упаковывает их в водонепроницаемые мешки малого и среднего объема. Хранить пеллеты кипами также нецелесообразно, так как нижние упаковки начнут разрушаться под весом верхних.
Выгодно и практично покупать пеллеты тоннами россыпью, либо в прозрачных полиэтиленовых пакетах. Таким образом можно видеть качество материала, его сухость и плотность.
Древесные пеллеты — виды и области применения
Существует несколько разновидностей гранулированного топлива. Классификация формируется по материалу производства.
- Белые пеллеты премиум класса считаются лучшими по всем показателям. Их делают из натуральной древесины измельченной и высушенной специальными методами. Применяют данный вид топлива для обогрева помещений, для растопки каминов и мангалов.
- Темные или серые пеллеты производят из древесины вместе с корой. За счет этого увеличивается зольность материала и сразу падает стоимость. Несмотря на это топливо отлично подходит для индустриальных колов и растопки дачных печей. Кроме того, именно данный вид пеллет хорошо подходит для наполнителя кошачьих туалетов и для подстилки грызунам.
- Пеллеты из лузги считаются самыми зольными, но за счет масла, оставшегося в кожуре дают повышенную теплоотдачу, поэтому их широко используют на дачных участках и промышленных котлах специально созданных под данный вид топлива. По стоимости они являются наиболее дешевыми.
Производители пеллет есть в каждом регионе России. Высокая популярность пеллетных котлов и наличие множества мебельных производств и лесопилок, а также обширные аграрные участки, позволяют предпринимателям производить топливо высокого качества по оптимальной цене.
Информацию предоставила компания Прогесс В — производитель топливных пеллет в Москве. Позвоните нам если хотите приобрести пеллеты по оптовой цене.
Пеллеты для отопления, состав, расход по площади дома.
Как так получилось что в статье – «что такое пеллетный котел» я совершенно не уделил внимание тому, что из себя представляют сами пеллеты для отопления, из чего их изготавливают, их достоинства как топлива для обогрева частных домов, коттеджей, дач.
Что такое пеллеты для отопления.
Попробую исправить эту оплошность – пеллеты для отопления это гранулы или древесные капсулы, достойная замена таким видам топлива как дрова и уголь. Их история появления проста, шелуха подсолнечника, обработка древесины, все это подразумевает отходы, которые раньше попросту выбрасывали. Пробовали топить ими котлы, даже выпускали и сейчас выпускаются котлы для работы на отходах древесного производства, прижилась только шелуха семечки, неплохо горела, котлы легко автоматизировались.
Вот один умный человек и решил, а почему не выпускать из них брикеты, наподобие коксового угля, а другой, глядя на растительные гранулы, комбикорм – корм для скота решил совместить эти два похожих продукта, так пеллеты и приобрели форму гранул. Хочется добавить, что оборудование для производства пеллет тоже, что и для производства комбикорма.
Размер древесных пеллет для отопления и сейчас разный. Всё зависит от сырья, из которого их изготавливают и машин на производстве. Пеллеты имеют высокую плотность, хотя они и сделаны из дерева, не тонут в воде. Высокая плотность пеллет, одинаковый размер гранул, позволили автоматизировать котлы, работающие на них, и сделала этот вид топлива эффективным средством отопления, теплота, выделяющаяся при сгорании древесных гранул сопоставима с углём. При схожих показателях теплотворной способности угля и пеллет у последних гораздо меньшая цена.
Конечно, если сравнивать отопление пеллетами и газом, стоимость отопления пеллетами будет выше. Но добавьте сюда высокую стоимость прокладки газопроводов к дому, стоимость газового котла, топка пеллетами получается дешевле. Разница в окупаемости между отоплением дома газом и пеллетами по окупаемости ниже не менее 12 раз. Это значит, что окупив затраты на проведение газа к участку через 12 лет, вам необходимо будет думать о новом газовом оборудовании (оно морально устареет, вам предпишут его заменить), а котел на пеллетах будет продолжать работать, ему предписания не страшны, лишь бы не появилась течь из котла. У хороших производителей срок эксплуатации котлов работающих на пелеттах достигает 30 лет.
Котел, работающий на пеллетах – разрез.
При производстве пеллет не используются химические добавки, а значит это чистый вид топлива с точки зрений экологии и при этом, если вспомнить что пеллеты это отходы древесины, возобновляемый, дрова, которые в процессе изготовления превратили в удобные гранулы.
Расход пеллет на отопление дома.
По теплотворной способности 1000 м3 бытового газа равны 2 тоннам пеллет. Проанализировав отзывы владельцев, эксплуатирующие котлы на пеллетах, можно сделать главный и естественный вывод, чем толще стены дома и теплее зима, тем меньше расход пеллет. Ниже привожу данные по расходу пеллет на 1 квадратный метр площади дома в зависимости от его характеристики и температуры на улице.
Идеальный теплый дом для вашей местности расход пеллет на отопление дома составит:
- при температуре -9С = 3,2 кг на 1 кв. м. в месяц
- при температуре -13С = 3,5 на 1 кв. м. в месяц
- при температуре -25С = 5,5 на 1 кв. м. в месяц
Удельный расход пеллет на отопление дома за год 3,5 кг на 1 кв. метр в месяц.
Дом из бруса 15 см, утеплен эковатой 15 см.
Удельный расход пеллет на отопление дома за год 4,5 кг на 1 кв. метр в месяц.
Каркасный дом, утепление каркаса 150 мм базальтовой ваты, потолка 250 мм ваты, пол 200 мм ваты, удельный расход пеллет на отопление дома составил:
- 3,7 кг на кв. м. в октябре
- 5,5 кг на кв. м. в ноябре
- 9 кг на кв. м. в декабре
В среднем по стране удельный расход пеллет на отопление и производство горячей воды составляет от 3,6 до 5,6 кг на 1 кв.м. дома в месяц. Отсюда можете сами посчитать, сколько пеллет необходимо заготовить на зиму и во что это вам обойдется.
Пеллеты цена
Самые дешевые пеллеты из лузги подсолнечника, купить их можно от 2000р за тонну. Плохие они или хорошие, если дешевые это уж как повезет, теплота сгорания обычная для пеллет, зольность низкая теоретически и смол в них быть не должно, а значит и отложений на стенках котла и дымохода. Могут сильнее крошиться в шнеке, чем пеллеты их хвойных пород, но в тех смолы уж точно больше.
Дальше ценообразование самое разное, у кого из производителей какая совесть, в малых мешках цена до 8000р за тонну, в больших от 3000р, навалом прямо с производства как договоритесь.
Если считать стоимость отопления применительно к площади дома в 200 м2 это 1 тонна в месяц или 7500р в переводе на стоимость хороших пелетт, для сравнения — у меня за отопление такого же дома газом в морозный месяц уходит до 6500 тысяч.
Пример хранения пеллет.
Отопительные пеллеты удобно транспортировать и хранить, для их производства подходить абсолютно любая древесина, отсюда и разный цвет пеллет, поэтому не стоит судить о качестве пеллет по цвету, например, коричневые гранулы, скорее всего, просто передержали в печи, они могли подгореть.
А вот ход маркетологов, уверяющих, что при сгорании пеллет выделяет лишь то количество углекислого газ, сколько дерево успело впитать в себя во время роста, не верен. Древесные гранулы действительно помогают сохранить лес от вырубки, ведь они производиться из древесных отходов, но у них, как и у любого другого топлива при неправильном, неполном сгорании выделяется угарный газ. Воздуха на горение не хватает, идет недожог, поэтому будьте внимательны, ограничивая подачу воздуха для экономии пеллет, чтобы не угореть.
Те, кто использует котлы, работающие на пеллетах большой мощности, на производстве, это хорошо знают, их не раз «прессовали» экологи. Если Вы относитесь к этой категории, и вам необходима режимная наладка отопительных котлов работающих на пеллетах или шелухе семечек, звоните – режимная наладка котлов малой, средней и большой мощности это наш основной вид деятельности с 1985 года.
Пеллеты – современный экологически чистый вид биотоплива
ПЕЛЛЕТЫ – СОВРЕМЕННЫЙ ЭКОЛОГИЧЕСКИ ЧИСТЫЙ ВИД БИОТОПЛИВА
Полищук А. И., Рубинская А. В. (Лф СибГТУ, г. Лесосибирск, РФ)
In work questions of processing of the wood waste formed at timber cutting are considered. A perspective direction of processing of wood waste is manufacture of fuel granules which on thermal feedback do not concede to such fuel as coal and black oil. This property allows to use fuel granules in boiler-houses for heating premises.
Древесные гранулы (пеллеты) — современный экологически чистый вид топлива, который изготавливают из древесного сырья методом прессования. Котлы и камины на пеллетах используют для отопления дачных домов и коттеджей в любое время года. Их отличает простота установки, несложное подключение к системе отопления и наличие автоматических систем управления режимами работы.
Пеллеты как вид топлива появились сравнительно недавно. Но благодаря натуральности и высоким теплотворным способностям они получили большое распространение в Европе, странах Северной Америки, Японии. Рост их потребления обусловлен возможностью использования гранул на промышленных теплоэлектростанциях и в установках, предназначенных для частного применения. Производят данное топливо из отходов деревообрабатывающей и лесозаготовительной промышленности на специальных линиях без применения каких либо проклеивающих веществ. Таким образом, удается решить сразу две проблемы: переработать потенциально пожароопасные отходы и произвести высококалорийное топливо. В готовом виде пеллеты представляют собой цилиндры диаметром 6–10 мм длиной до 50 мм. По причине высокой собственной плотности они прекрасно сохраняют форму во время перевозки и хранения, а поверхностная пленка, образующаяся в процессе производства, препятствует проникновению атмосферной влаги. Хранение даже больших запасов такого теплоносителя не требует особых мер предосторожности и контроля. В отличие от древесной щепы и опилок, зачастую являющихся причиной пожаров, пеллеты не подвержены самовозгоранию, их можно держать в непосредственной близости от жилого помещения. По теплотворной способности древесные гранулы аналогичны углю или 2 кг пеллет заменяют 1 кг дизельного топлива. Учитывая дороговизну традиционных теплоносителей в Европе, можно представить ту выгоду, которую получают частные потребители от использования пеллет.
Сырьем для производства пеллет в нашей стране служат хвойные породы, однако лучшие пеллеты получаются из сырья лиственных пород (однако это требует оборудования более высокого класса).
Влажность пеллет составляет 7-10%, что позволяет их с успехом использовать в пиролизных котлах (правда, после небольшой доработки последних). Плотность пеллет 1,5, поэтому, пеллеты тонут в воде. Процесс формирования пелет происходит под давлением около 300 атм., без каких-либо добавок и клею, что делает их экологически безопасными, и безвредными, даже для здоровья детей. Теплотворная способность 1 кг пеллет = 5 кВт час ( правда, тут не стоит забывать о КПД того устройства где Вы их сжигаете, и в действительности эта цифра меньше), что примерно в 1,5 раза больше чем у дров. Достаточно приблизительно, но весьма образно можно сказать, что содержание энергии в одном килограмме пеллет равняется энергии, содержащейся в половине литра жидкого топлива. И этот килограмм не разольется по Вашему дому, загрязняя и оставляя после себя неприятный запах, и не взорвется от случайной искры.
Пеллеты производятся без применения каких-либо химических добавок, что и обеспечивает экологическую чистоту топлива. Иными словами, это те же самые дрова, сформированные в удобную для транспортировки, хранения и применения форму. В качестве склеивающей составляющей используется природный компонент древесины – лигнин, который при достижения определенной температуры склеивает частицы.
Сырьём для производства пеллет могут быть как деловая древесина, так и древесные отходы: кора, опилки, щепа и другие отходы лесозаготовки и лесопереработки. В зависимости от используемого сырья, пеллеты отличаются по цвету. Например, отходы от лесозаготовки (пиловка и т.д.) содержат кору, которая в свою очередь содержит песок, который в конечном итоге снижает качество продукта. Цвет таких пеллет можно определить как «капучино». Однако, цвет пеллет также зависит от температуры гранулирования, и в этом случае цвет говорит о слишком высокой температуре гранулирования, пеллеты просто подгорают. Таким образом, судить о качестве пеллет по их цвету можно только предварительно.
Сырье от вторичной переработке древесины (изготовление мебели, окон и т.д.) чище, и пеллеты имеют бело-желтый цвет, однако тут возникает вопрос наличия примесей от ДСП или других искусственных материалов, применяемых в производстве мебели, и в этом случае, об экологической составляющей говорить уже не приходится. Косвенным признаком хим. примесей может являться наличие красной окалины на колосниках котла после сгорания таких пеллет.
Сырьё (опилки, кора и т. д.) поступает в дробилку, где измельчается до состояния муки. Полученная масса поступает в сушилку, из нее — в пресс-гранулятор, где древесную муку сжимают в пеллеты. На производство одной тонны пеллет уходит около 5 кубометров древесных отходов. Поэтому, если Вам придет в голову заняться этим «прибыльным» бизнесом, прежде всего, прикиньте, где Вы будете брать такой обьем сырья, т.е. для производства 10 тонн пеллет в смену Вам необходимо 50 кубов опилок, причем, желательно собранных не с земли, т.е. без примесей. Кроме того, учитывая что затраты на сушку сырья достаточно высоки, в целях снижения себестоимости лучше искать сухую стружку, т.е. что бы Ваша цена была конкурентоспособной. В конечном итоге, Вам для производства 1 тонны необходимо 50 кубов сухих опилок. Некоторые специалисты утверждают, что пеллетное производство экономически эффективно при обьемах не менее 300-500 тонн в месяц, однако на наш взгляд данная оценка завышена. Готовые пеллеты охлаждают, пакуют в пластиковые мешки или доставляют потребителю россыпью.
Пеллеты являются частью натурального круговорота СО2 в окружающей среде. Пеллеты являются экологически чистым топливом, так как при их сгорании выделяют ровно столько СО2, сколько было впитано деревом при его росте (закрытый углеродный обмен), в отличие от угля и т.д. Т.е. при сжигании пеллет количество выделяемого углекислого газа в атмосферу не превышает объем выбросов, который образовался бы путем естественного разложения древесины. Используя пеллеты, Вы сберегаете от рубки живой лес и от загрязнения отходами деревообрабатывающего производства окружающую среду. Кроме того, пеллеты относятся к возобновляемым источникам топлива, в отличие от угля, нефти и газа.
Известно, что от котельной, работающей на дизельном топливе или на угле, зачастую исходит неприятный запах. Пеллеты при горении не выделяют запах, и, как правило, за счет высокого КПД котельного оборудования дым от пеллет практически бесцветен. За счет низкого содержания серы в пеллетах уменьшаются выбросы в атмосферу двуокиси серы, а это, в свою очередь, ведет к уменьшению количества кислотных дождей. Пеллеты также выигрывают по всем позициям у каменного угля и жидкого топлива в области выброса других вредных веществ. И если в промышленности это пока мало кого беспокоит, то иметь вокруг своего частного дома таблицу Менделеева — малое удовольствие. И даже эстетически — котельная, работающая на пеллетах, выглядит более привлекательно, чем работающая на угле или солярке.
По сравнению с другими видами топлива пеллеты не оставляют следов на поверхностях и легко убираются с помощью веника и совка. В отличии, например от жидкого топлива, утечка которого пожароопасна, рассыпанные пеллеты могут применять в качестве абсорбента пеллеты впитывают в несколько раз больше собственного веса. За счет высокой температуры при изготовлении пеллет пеллеты биологически не активны и за это их очень любят использовать в качестве наполнителя для туалетов домашних животных.
Таким образом, пеллеты как вид альтернативного топлива применяют в современных системах отопления и водоснабжения наравне с традиционными теплоносителями. А если учесть его экологические особенности и развитие производства древесных гранул в России, то в скором будущем такие аппараты будут на равных конкурировать с газовыми, мазутными, дизельными и твердотопливными котлами.
При сжигании пелет достигается КПД до 94%. По своим тепловым свойствами пелеты превосходят даже каменный уголь. Гранулы производят без использования химических укрепителей. Экологические показатели вне конкуренции: в выбросах практически отсутствует сера, эмиссия углекислого газа ниже в 10 — 50 раз, чем у любого другого вида топлива. Не содержат пыль и споры, которые вызывают аллергию у людей. Не имеют запаха, в отличие от стандартных видов топлива. При хранении топливные гранулы не самовоспламеняются от повышения температуры. Не взрывоопасны, в отличие от газа. Могут сохраняться в непосредственной близости от жилищных помещений. Не набирают влаги из воздуха, потому их высокая теплотворность не снижается со временем. Гранулы удобно транспортировать и хранить — необходимая площадь в 2 раза меньше, чем при транспортировке и хранении дров, торфобрикетов. Легко поддаются автоматизации за счет хорошей сыпучести, которая делает их удобными в использовании. Пепел, который остается при сгорании деревянных и торфяных гранул с успехом применяется как удобрение на приусадебных газонах или грядках. Является самым дешевым видом топлива на данном этапе.
Таблица 1 – Сравнительная характеристика пеллет
Вид топлива | Теплота сгорания, МДж/кг | Калорийность, кКал | % пепла | % серы | Цена, грн./т |
каменный уголь | 15-25 | 4500-5200 | 10-36 | 1-3 | 800-1000 |
бурый уголь | 14-22 | 4000-4300 | 10-35 | 1-3 | 700-900 |
Дрова | 10 | 2000 | 2 | 0 | 400-600 |
Торфяные гранулы | 18 | 4500-4800 | 6 | 0,7 | 600-700 |
Пеллеты | 19 | 4800-5000 | 1,5 | 0,1 | 960 |
Торфобрикеты | 15 | 3200 | 23 | 1-3 | 400-450 |
Природный газ | 35-38 | 0 | 0 | 0 | Нестабильная, постоянно растет |
При сжигании 1000 кг пеллет выделяется столько же тепловой энергии как при сжигании: 1600 кг древесины; 479 м3 газа; 500 л дизтоплива; 685 л мазута.
Анализ методик оценки физико-механических и тепловых характеристик древесных пеллет Текст научной статьи по специальности «Промышленные биотехнологии»
Деревопереработка. Химические технологии
DOI: 10.12737/3354 УДК 674.8
АНАЛИЗ МЕТОДИК ОЦЕНКИ ФИЗИКО-МЕХАНИЧЕСКИХ И ТЕПЛОВЫХ ХАРАКТЕРИСТИК ДРЕВЕСНЫХ ПЕЛЛЕТ
соискатель кафедры древесиноведения Е. В. Зотова доктор технических наук, профессор, декан лесопромышленного факультета, профессор кафедры древесиноведения А. О. Сафонов ФГБОУ ВПО «Воронежская государственная лесотехническая академия» [email protected], [email protected]
В связи с непрерывным повышением цен на ископаемые энергоносители и ограниченностью их мировых резервов большой интерес в последние годы проявляется к твердому топливу из возобновляемых источников. Большинство стран, включая те, которые обладают значительными запасами природных энергоносителей, разрабатываются государственные программы, принимаются нормативные документы, направленные на стимулирование производства биотоплива из растительного сырья. Для России, обладающей большими запасами древесной биомассы, которая скапливается в виде отходов на деревоперерабатывающих заводах, требующих скорейшей утилизации, задача производства полезной продукции из этого сырья, несомненно, является актуальной [1]. При этом напряженная экологическая обстановка стимулирует поиск альтернативных менее опасных видов топлива [2].
Применение пеллет из древесного сырья снижает выброс парниковых газов в атмосферу. При этом не нарушается баланс CO2 в атмосфере по причине возобновляемости этого сырья. Высвобождаемый газ CO2 в топливе на основе отходов растительного происхождения считается «нейтральным». Древесина высвобождает
такое количество CO2, которое поглотило в период роста, так называемый закрытый углеродный обмен. Во время сжигания невозобновляемых угля, нефти, природного газа, наоборот, высвобождается углекислый газ, собранный за миллионы лет. Это обстоятельство является причиной повышения содержания CO2 в атмосфере, создается парниковый эффект. Древесные отходы в отличие от ископаемых углеводородов практически не содержат серы и фосфора, что обеспечивает при их сжигании невысокую токсичность отходящих газов. Также технологический процесс изготовления древесного биотоплива, как правило, не требуется использования химических связующих или других составляющих. Однако сырье требует дополнительных затрат на подготовку, например, сушку, характеризующуюся значительными затратами энергии [3]. Одновременно применение древесного топлива позволяет увеличить полезный выход древесины, который сейчас находится на низком уровне и составляет 40…60 %. По различным данным ежегодно в России перерабатывается 170 млн м древесины и, соответственно, образуется около 70 млн м3 древесных отходов, требующих переработки или утилизации.
Лесотехнический журнал 1/2014
113
Деревопереработка. Химические технологии
Процесс гранулирования давно известен, он был изобретен более 75 лет назад и заключался в прессовании измельченного сырья. С тех пор гранулирование начало широко использоваться для уплотнения соломы, других отходов сельского хозяйства и плодоовощной промышленности, компоста, бумаги, целлюлозы, угольной пыли, химических веществ, материалов при производстве пива, отходов резины, синтетических моющих средств и так далее.
Пеллеты впервые были произведены более 25 лет назад немцем по происхождению Руди Гуннерманом, проживающим в США. В Европе промышленным производством пеллет впервые заинтересовались в Швеции. Там в середине восьмидесятых годов прошлого столетия начали производить топливо из отходов деревообработки. С начала девяностых годов прошлого столетия в Швеции промышленное производство древесных гранул получило широкое распространение. Затем этот вид биотоплива начал производится во многих странах Европы, странах Прибалтики, Канаде, США, Бразилии, Китае.
В настоящее время свойства технические характеристики твердого биотоплива, в том числе древесных пеллет регламентируются национальным стандартом [4]. Согласно этому документу для оценки качественных и транспортных свойств пеллет необходимо обязательно проводить измерения и расчеты следующих показателей:
1) Размеры (диаметр и длина).
2) Массовая доля влаги.
3) Зольность.
4) Механическая прочность.
5) Содержание мелкой фракции.
6) Содержание добавок.
7) Насыпная плотность.
8) Теплота сгорания.
9) Удельная энергоемкость.
10) Содержание серы.
11) Содержание азота.
12) Содержание хлора.
13) Плавкость золы (информативно).
При этом в документе [3] даны ссылки на стандарты, регламентирующие определение части вышеуказанных характеристик. Другая часть таких характеристик, как механическая прочность, теплота сгорания, удельная энергоемкость, плавкость золы определяют либо по общим стандартам, независимо от происхождения топлива, либо как в случае с механической прочностью по не стандартным методикам.
Рассмотрим определение этих характеристик с возможностью применения в реальных промышленных производствах пеллет из отходов древесного происхождения.
Размеры пеллет. Метод заключается в известной для многих дисперсных сред процедуре просеивания материала через горизонтальные колеблющиеся сита и рассортировке его частиц по классам крупности в убывающей последовательности. Для твердого биотоплива эти методики определяются национальными стандартами ГОСТ Р 54188-2010, ГОСТ Р 54188-2010, ГОСТ Р 54188-2010. В качестве оборудования при ручном просеивании применяются сита и сборный лоток, при механическом — грохот. Набор сит с ячейками круглой или прямоугольной формы с минимальной эффективной площадью просеивания 1200 см . Количество сит и размеры отверстий сит
114
Лесотехнический журнал 1/2014
Деревопереработка. Химические технологии
должны выбираться в зависимости от крупности испытуемого образца материала. Рама сита должна иметь высоту, позволяющую вместить образец и обеспечивающую свободное перемещение образца в процессе просеивания. Для материалов с номинальным предельным размером менее 10 мм допускается применение сит с эффективной площадью менее 1200 см . Рекомендуется использовать сита с отверстиями диаметром 3,15, 16, 45 и 63 мм. Для более точного распределения частиц по размерам и во избежание преобладания одной из фракций рекомендуется добавить в набор 8-мм сито. С целью дальнейшей сортировки по размерам частиц фракции, прошедшей последнее сито (менее 3,15 мм). Сборный лоток применяется для сбора материала, проходящего через сита.
Если используется механическое устройство для просеивания (грохот), его колебания должны быть направлены в горизонтальной плоскости (в одном или двух направлениях) с частотой колебаний, соответствующей типу испытуемого материала. Принципиальный чертеж механического грохота приведен на рис. 1.
2
ж» Ч
Рис. 1. Принцип операции просеивания:
1 — направление увеличения диаметра отверстий; 2 — загрузка испытуемого материала; 3 — направление движения материала
Также следует помнить, что слишком низкая частота колебаний может привести к неполному разделению частиц. Минимальная частота колебаний может быть определена предварительными испытаниями. Весы, должны измерять массу образца, подлежащего просеиванию, с точностью до 0,1 г.
Подготовка проб. Для определения гранулометрического состава минимальный объем испытуемого образца должен быть не менее 8 л и должен быть отобран в соответствии с ГОСТ Р 54217-2010. ГОСТ Р 54218-2010 и ГОСТ Р 54187-2010. Для биотоплива мелких классов, где 100 % частиц проходят через сито с отверстиями диаметром 45 мм, выборка уменьшается до объема не менее 4 л. Образец для проведения просеивания включает в себя собственно материал для определения его гранулометрического состава и массовую долю содержания влаги. В зависимости от размера сит испытуемый образец может быть разделен на несколько частей, которые просеивают последовательно, одна за другой. Размер образца должен быть таким, чтобы высота наполнения верхнего сита никогда не превышала 5 см.
Содержание влаги в пробе для просеивания должно быть менее 20 % в целях предотвращения слипания частиц или потери влаги в процессе просеивания. При необходимости образцы должны быть предварительно высушены. Сушка осуществляется в соответствии с ГОСТ Р 542122010. Предварительной сушкой влажность образца для испытаний приводят в равновесие с влажностью окружающей атмосферы. Содержание влаги в материале для
Лесотехнический журнал 1/2014
115
Деревопереработка. Химические технологии
просеивания определяют на отдельной подвыборке в соответствии с процедурами, описанными в ГОСТ Р 54186-2010 или ГОСТ Р 54192-2010. Содержание влаги должно определяться и записываться одновременно с определением распределения частиц по размерам.
Проведение испытаний. Ручное просеивание. Сито с наибольшим диаметром отверстий помещают на сборный лоток. Взвешивают образец с точностью до 0,1 г. Распределяют образец ровным слоем на сите и начинают просеивание. Просеивают до тех пор, пока наблюдается прохождение частиц через сито, затем процедуру прекращают. При использовании сит меньшей площади для удобства можно просеивать одновременно на двух или больше ситах. Частицы, прошедшие через сито, собирают в сборный лоток. Распределяют содержимое сборного лотка ровным слоем по ситу с меньшим диаметром отверстий и повторяют операцию. После просеивания материала через сито с наименьшим диаметром отверстий взвешивают содержимое каждого из сит и сборного лотка с точностью до 0,1 г и записывают полученные данные. В случае, когда частица застревает в отверстии сита, ее следует извлечь и добавить к фракции, которая остается на этом сите. Необходимо избегать потерю частиц с экранов сит. Это может быть достигнуто путем герметизации промежутков между лотками и использованием верхней крышки. В процессе определения гранулометрического состава методом просеивания некоторые из тонких частиц, которые по длине превышают диаметр отверстия, пройдут сито и смешаются с частицами
меньшей по размеру фракции. Большинство из этих частиц должны оставаться в этой фракции. При необходимости проведения определения фракционного состава частиц, которые прошли наименьшее по диаметру отверстий сито, испытание выполняют по ГОСТ Р 54189-2010.
Механическое просеивание. Взвешивают образец с точностью до 0,1 г. Распределяют образец (подвыборку) ровным слоем на верхнем сите и начинают операцию просеивания. Операция просеивания должна продолжаться в течение 15 мин. Следует учитывать, что более длительное время просеивания может привести к истиранию и искусственному увеличению доли мелких фракций. Взвешивают материал, оставшийся на каждом из сит и в сборном лотке, с точностью до 0,1 г и записывают полученные данные. Как и при ручном просеивании, если частица застревает в отверстии сита, ее следует извлечь и добавить к фракции, которая остается на этом сите (как если бы она не прошла в отверстие). Следует избегать потери частиц с экранов сит. Это может быть сделано путем герметизации промежутков между лотками и использованием верхней крышки.
В процессе классификации по размеру методом просеивания некоторые из тонких частиц, которые по длине превышают диаметр отверстия, пройдут сито и смешаются с частицами меньшей по размеру фракции. Большинство из этих частиц должны оставаться в этой фракции. При определении фракционного состава частиц, которые прошли наименьшее по диаметру отверстий сито, испытание проводят по ГОСТ Р 54189-2010.
116
Лесотехнический журнал 1/2014
Деревопереработка. Химические технологии
Обработка результатов. Определение отдельных классов крупности выражают в процентах от общей массы всех фракций. Если испытуемый образец просеивают отдельными подвыборками, массы соответствующих фракций, полученные в проведенных определениях, должны быть сложены перед расчетом общей доли каждого класса крупности и зафиксированы. Разница между общей массой пробы и общей массой всех фракций не должна превышать 2 %. Большие различия могут возникать из-за потери частиц образца или их застревания в ячейках сит, или в связи с изменением массовой доли влаги в процессе испытаний. В этом случае причины отклонений должны быть исследованы, а испытание должно быть проведено повторно.
Точность метода. Из-за различной природы твердых биотоплив, охватываемых ГОСТ Р 54188-2010, ГОСТ Р 541892010, ГОСТ Р 54190-2010, не представляется возможным на данном этапе установить предел погрешности (повторяемость и воспроизводимость) для данного метода испытаний.
Протокол испытаний должен включать следующую информацию: название лаборатории и дату проведения испытания, идентификацию товара или исследуемого образца, номер стандарта, по которому проводились испытания, сведения о том, какая операция просеивания (ручная или механическая) применялась, любое отступление в процессе испытаний от стандарта, условия и наблюдения, например, необычные наблюдения во время проведения испытаний, которые могут повлиять на результат, результаты испытаний в
виде таблицы.
Если расхождение между общей массой пробы и общей массой всех фракций в процентах от общей массы пробы, было превышено более чем на 2,0 %, это должно быть обязательно отмечено в протоколе испытаний.
Определение массовой доли влаги в пеллетах. Сущность метода заключается в высушивании образца биотоплива в воздушной атмосфере при температуре 105 °С до постоянной массы и вычислении массовой доли влаги в процентах, исходя из потери массы образца и включает процедуру корректировки эффекта изменения массы холодного и горячего лотка. Используется сушильный шкаф с электрическим нагревом и терморегулятором, обеспечивающим устойчивую температуру нагрева (105±2) °С, снабженный устройством для подачи воздуха со скоростью от 3 до 5 рабочих объемов печи в час. Скорость воздуха должна быть такой, чтобы частицы пробы не улетали с лотка. Необходим лоток для взвешивания пробы, изготовленный из термо- и коррозионно-стойкого материала такого размера, чтобы вмещался весь образец и слой топлива не превышал 1 г/см2. Поверхность лотка должна быть чистой и гладкой, чтобы возможность адсорбции/абсорбции была сведена к минимуму. Весы лабораторные должны быть по ГОСТ Р 53228-2008 с точностью взвешивания до 0,1 г.
Отбор и подготовка проб для определения общей влаги проводят по ГОСТ Р 54217-2010, ГОСТ Р 54218-2010 и ГОСТ Р 54212-2010. Пробы доставляют в лабораторию в герметичной водо- и воздухонепроницаемой таре (контейнерах, банках, меш-
Лесотехнический журнал 1/2014
117
Деревопереработка. Химические технологии
ках). Меры предосторожности должны соблюдаться для того, чтобы не происходила потеря влаги до приготовления пробы. Пробу для определения содержания влаги взвешивают непосредственно после приготовления. Масса образца должна быть не менее 300 г, но желательно более 500 г.
Проба в ходе подготовки может быть предварительно высушена по ГОСТ Р 54212-2010 с определением внешней влаги W„* которую учитывают при расчете содержания массовой доли общей влаги Wt, по формуле (1)
Wt = Wex + Wh (10° ~ W), (1)
где Wex — массовая доля внешней влаги, определенная при предварительном высушивании образца при подготовке пробы, %;
Wh — массовая доля влаги воздушносухого топлива, определенная в предварительно высушенных образцах, %.
Проведение испытаний. Взвешивания проводят на лабораторных весах по ГОСТ Р 53228-2008 с точностью взвешивания до 0,1 г. На взвешенный пустой чистый лоток помещают пробу из тары и распределяют ее ровным слоем. Одновременно с этим проводят испытание с пустым идентичным лотком (сравнительный лоток). В случае если на поверхности мешка или тары осталась влага, это количество влаги должно быть учтено в расчете. Для этого упаковку образца (контейнер, мешок или др.) высушивают в сушильном шкафу и взвешивают до и после высушивания. Если материал упаковки не выдерживает температуру 105 °С, то сушат ее при комнатной температуре. В процедуру испытания включается сравнительный лоток, так как вес холодно-
го лотка больше, чем горячего, а во избежание абсорбции влаги из атмосферы лоток с высушенным образцом взвешивают, пока он еще горячий. Взвешивают лоток с образцом и сравнительный лоток, помещают их в сушильный шкаф, нагретый до (105±2) °С, и сушат до постоянной массы. Нельзя перегружать сушильный шкаф. Там должно быть достаточно свободного места над слоем образца, а также между лотками. Твердые биотоплива гигроскопичны, наполненный и сравнительный лотки после сушки взвешивают в течение 10.. .15 с, пока они еще горячие, для предотвращения абсорбции влаги. Для защиты весов от прямого контакта с горячим лотком используют теплоизоляционный материал. Постоянство массы означает, что ее изменения не превышают 0,2 % от общей потери массы при дальнейшей сушке при (105±2) °С в течение не менее 60 мин. Требуемое время высушивания зависит от размера частиц образца, скорости обмена воздуха в сушильном шкафу, толщины слоя образца и так далее. Во избежание потери летучих веществ время сушки обычно не должно превышать 24 ч. Требуемое время сушки может быть определено на основании предыдущих испытаний подобных типов топлива со сравнимым размером частиц.
Обработка результатов. Массовую долю общей влаги рассчитывают на рабочее состояние топлива по формуле (2). Пересчет результатов анализа с рабочего состояния топлива на сухое состояние проводят по формуле (3) и с сухого состояния на рабочее — по формуле (4). Результаты представляют на рабочее или сухое состояние топлива.
118
Лесотехнический журнал 1/2014
Деревопереработка. Химические технологии
WY = (m2 ~ Шз) ~ (m4 ~ m5) + m6 ,100 ‘ (m2 — т1) ’
где mi — масса пустого лотка, г;
т2 — масса лотка с образцом до высушивания, г;
т3 — масса лотка с образцом после высушивания, г;
m4 — масса сравнительного лотка до высушивания (взвешенного при комнатной температуре), г;
т5 — масса сравнительного лотка после высушивания (взвешенного горячим), г;
т6 — масса влаги, собранной с упаковки, г.
Результат вычисляют с точностью до 0,01 % и округляют до 0,1 %. Если проба перед определением влаги была предварительно высушена, то массовую долю общей влаги Wt рассчитывают, исходя из массовой доли внешней влаги WBX и массовой доли влаги воздушно-сухого топлива Wh.
Wtd =
WY
100 — wy
•100,
(3)
где Wtr — массовая доля общей влаги на рабочее состояние топлива, %;
Wtd — массовая доля общей влаги на
сухое состояние топлива, %.
wy =■
Wd
100 — Wd
•100,
(4)
Прецизионность. Из-за различного происхождения твердого биотоплива, достоверно установить показатели повторяемости и воспроизводимости не представляется возможным, что допускает действующий стандарт ГОСТ Р 54186-2010.
Протокол испытаний должен содержать: идентификационные данные лаборатории и дату проведения анализа, иденти-
фикацию продукции или испытуемого образца, ссылку на используемый стандарт, любое отклонение от методики определения, результаты испытаний с указанием состояния топлива, на которое рассчитана общая влага (в соответствии с договором с заказчиком).
Также регистрируются все особенности, происходящие во время процедуры испытания, которые могут повлиять на его результат.
Определение зольности. Контроль этого показателя проводится по ГОСТ Р 54185-2010. В качестве оборудования применяются тигли, муфельная печь, весы, эксикатор. Тигли для сжигания из инертного материала, такого как фарфор, кремний или платина, глубиной от 10 до 20 мм и такого размера, чтобы на 1 см2 поверхности дна тигля масса пробы топлива не превышала 0,1 г/см2. Муфельная печь обеспечивает равномерный нагрев, необходимую температуру и скорость нагрева в соответствии с требованиями действующего стандарта ГОСТ Р 54185-2010. Вентиляция должна быть такой, чтобы не было недостатка кислорода при горении и разогреве. Скорость обмена воздуха муфельной печи должна составлять от 5 до 10 рабочих объемов печи в минуту. Эксикатор применяется без осушителя.
В ГОСТ Р 54185-2010 указано оборудование, дословно: «5,3 Весы лабораторные по ГОСТ Р 53228-2008 с точностью взвешивания до 0,1 г». В этом же стандарте утверждается «Все взвешивания проводят на весах согласно 5,3 с точностью до 0,1 мг». Несомненно, в этом стандарте допущена опечатка. Это подтвер-
Лесотехнический журнал 1/2014
119
Деревопереработка. Химические технологии
ждается тем, что масса пробы должна составлять 1 г. Следовательно, точность взвешивания не должна превышать 0,1 мг.
Подготовка пробы. Для определения зольности используют пробу, измельченную до размера частиц 1 мм и менее, отобранную по ГОСТ Р 54187-2010 и подготовленную в соответствии с ГОСТ Р 542122010. Определение зольности выполняют одним из следующих способов: а) прямо на подготовленной аналитической пробе, включая одновременное определение содержания влаги в образце по ГОСТ Р 54211-2010; б) на образце аналитической пробы, которая была предварительно высушена и хранилась абсолютно сухой перед взвешиванием в закрытом контейнере в эксикаторе. Для некоторых видов биотоплива подготавливают образцы размером менее 1 мм (например, 0,25 мм) для того, чтобы сохранить заявленную точность.
Проведение испытания. Испытания проводят минимум на двух навесках. Все взвешивания проводят на весах согласно с точностью до 0,1 мг. Прокаливают пустой тигель в муфельной печи при (550±10) °С не менее 60 мин, дают остыть на жаростойких пластинах в течение 5.. .10 мин и помещают в эксикатор. Когда тигель остынет до температуры окружающей среды, его взвешивают с точностью до 0,1 мг и записывают массу. Несколько тиглей могут обрабатываться одновременно.
Перед началом определения аналитическую пробу тщательно перемешивают и затем взвешивают. Пробу массой 1 г помещают на дно тигля и разравнивают. Взвешивают тигель с пробой с точностью до 0,1 мг и записывают массу. Если анали-
тическая проба требует высушивания, то тигель с пробой высушивают в сушильном шкафу при температуре (105±10) °С, а затем взвешивают.
Помещают наполненный тигель в холодную печь. Затем нагревают печь с тиглем следующим образом:
— печь нагревают равномерно до температуры (250±10) °С в течение 50 минут (то есть увеличение температуры составляет +5 °С/мин). Поддерживают температуру на этом уровне в течение 60 мин, чтобы вышли летучие вещества до воспламенения;
— продолжают равномерно нагревать печь до температуры (550±10) °С в течение 60 мин (т.е. увеличение температуры составляет +5 °С/мин) и поддерживают температуру на этом уровне не менее 120 мин.
Вынимают тигель с его содержимым из печи. Помещают тигель для охлаждения на толстую металлическую пластину на 5.10 мин, затем переносят в эксикатор без осушителя для остывания до температуры окружающей среды. Как только температура окружающей среды будет достигнута, взвешивают тигель с его содержимым с точностью до 0,1 мг и записывают массу. Рассчитывают зольность на сухое состояние по формуле
Ad
(n3 — П1) 100 100
(n2 — n) 100 — Wa’
(5)
где ni — масса пустого тигля, г; п2 — масса тигля с пробой, г; п3 — масса тигля с зольным остатком, г; W — массовая доля влаги в аналитической пробе, %.
Результаты испытаний вычисляют до 0,01 % и округляют до 0,1 %. За оконча-
120
Лесотехнический журнал 1/2014
Деревопереработка. Химические технологии
тельный результат испытаний принимают среднеарифметическое значение результатов двух параллельных определений. Если возникает сомнение, что образец сгорел не полностью (например, при визуальном осмотре обнаружена сажа), то:
— либо тигель с его содержимым помещают в печь, нагретую до 550 °С, и прокаливают 30 мин, после чего взвешивают. Прокаливание повторяют до тех пор, пока изменение массы тигля с остатком не станет менее 0,2 мг;
— либо в тигель добавляют несколько капель воды или нитрата аммония, затем помещают его в холодную печь, нагревают до температуры (550±10) °С и прокаливают в течение 30 мин, после чего взвешивают. Прокаливание повторяют до тех пор, пока изменение массы тигля с остатком не станет менее 0,2 мг.
Прецизионность. Повторяемость (сходимость). Результаты двух параллельных определений (проведенных в течение краткого промежутка времени, но не одновременно), выполненных в одной и той же лаборатории одним исполнителем с использованием одной и той же аппаратуры на двух образцах, взятых из одной и той же пробы для испытаний, не должны отличаться друг от друга более чем на значения, указанные в таблице.
Воспроизводимость. Разность результатов двух параллельных определений, выполненных в двух различных лабораториях на представительных образцах, взятых из одной и той же пробы для испытаний, не должны отличаться друг от друга более чем на значения, указанные в таблице.
Протокол испытаний должен содержать наименование лаборатории и дату проведения анализа, наименование продукции или образца испытаний, ссылку на используемый стандарт, любое отклонение от стандарта, отмеченное во время определения, результаты испытаний на сухой основе, условия, замечания и отклонения в ходе процедуры испытания, которые могут повлиять на его результат.
Действующего национального стандарта на определение механической прочности пеллет в настоящее время нет. Стандарт ГОСТ Р 55110-2012 вступит в силу лишь 01 июля 2014 г. Сейчас многие производители этой продукции пользуются различными методиками и определяют различные показатели, характеризующие в той или иной степени физико-механические показатели. Это усложняет приведение различных методик к единым показателям. На основе анализа различных способов предлагается следующая методика.
Механическую прочность древесных
Таблица
Повторяемость и воспроизводимость метода
Зольность, % Максимально допустимые расхождения между результатами при доверительной вероятности р=0,95 (на сухое состояние)
Предел повторяемости Критические различия воспроизводимости
Менее 10 % 0,2 % (абсолютных) 0,3 % (абсолютных)
10 % и более 2,0 % от среднего значения 3,0 % от среднего значения
Лесотехнический журнал 1/2014
121
Деревопереработка. Химические технологии
пеллет предлагается определять методом сбрасывания. Для этого в ящик с открывающимся дном насыпают до 4 килограммов образцов гранул. Затем поднимают их на высоту 1,5 метра и, открывая днище ящика, сбрасывают гранулы на стальную плиту. Эту операцию повторяют 4 раза. После все целые и поломанные пеллеты собирают и просеивают на сите с ячейками меньше диаметра гранул на 20 %. Затем собирают мелкую фракцию под решеткой и взвешивают. Также взвешивают остаток на сите. После этого прочность определяется из выражения
S = V -100, (6)
V0
где: Vj — вес гранул, оставшихся на сите, кг; v0 — первоначальный вес гранул, кг;
S — прочность гранул, %. Истираемость гранул. Также важный показатель, влияющий на состояние гранул после их транспортировки потребителю. Определяют при испытании образцов гранул во вращающемся барабане. Для этого в барабан необходимо загрузить 10 кг гранул и произвести 100 оборотов барабана. Затем содержимое барабана просеивают на сите с диаметром ячейки на 20 % меньше диаметра гранул. Истираемость определяется из выражения
I = h_ -100, (7)
h0
где: I — истираемость гранул, %;
h2 — вес остатка гранул на сите, кг; h0 — начальный вес засыпанных в барабан гранул, кг.
При истираемости гранул I > 75 % стойкость гранул считается удовлетвори-
тельной.
Содержание мелкой фракции. Определяют при нахождении размеров пеллет по методике, описанной выше в соответствии с ГОСТ Р 54188-2010, ГОСТ Р 541892010, ГОСТ Р 54190-2010.
Добавки. Методика определения содержания добавок в пеллетах в настоящее время не регламентирована действующим национальным стандартом. Связующие материалы вводятся в перерабатываемую массу, если не удается на грануляторе получить пеллеты достаточной механической прочности. Вид, количество связующих материалов в массе можно определить в лабораторных условиях. Для экспериментального определения содержания вредных газообразных выбросов в продуктах сгорания пеллет рекомендуется проводить исследования при разных режимах сжигания гранул в бытовых или промышленных печах для отопления помещений. Для отбора проб газов, образующихся при сжигании гранул, на дымовой трубе (на высоте около 1,5 м от корпуса печи) монтируется штуцер, к которому стыкуется газозаборное устройство газоанализатора. В качестве газоанализатора используется, например, многокомпонентный прибор АНГОР, реализуемый в России. Этот прибор позволяет автоматически фиксировать содержание в уходящих газах, нормируемых вредных выбросов. Опыты проводятся следующим образом. В печь загружается порция гранул, затем она поджигается. При наступлении устойчивого пламенного горения, которое характеризуется наибольшим количеством образующихся вредных продуктов сгорания, через каждые 5.. .10 мин проводятся измерения
122
Лесотехнический журнал 1/2014
Деревопереработка. Химические технологии
требуемых величин состава отходящих газов. Помимо режима пламенного горения проводятся также измерения состава отходящих газов на режиме окончания выгорания топлива, то есть режиме дожигания коксового остатка, так называемого тления.
После завершения выгорания топлива из печи отбирается зола для анализа на содержание в ней связанной серы и несгоревшего углерода. Для оценки опасности загрязнения окружающей среды выбросами проводятся расчеты рассеивания этих выбросов.
Определение насыпной плотности пеллет. Согласно ГОСТ 54191-2010 пробу помещают в стандартный контейнер заданного размера и формы и затем взвешивают. Насыпную плотность рассчитывают по весу нетто стандартного объема и с учетом одновременно определенного содержания влаги.
В качестве оборудования для определения этого важного показателя используют контейнеры. Они должны быть цилиндрической формы из ударопрочного материала с гладкой поверхностью, устойчивые к деформации для предотвращения изменений формы и объема, водонепроницаемые, с наружными захватами для облегчения работы и с соотношением высоты и диаметра в пределах 1,25…1,50. Большой контейнер объемом (50±1) л (допускаемое отклонение ±2 % от номинального объема) с внутренним диаметром 360 мм и внутренней высотой 491 мм (рис. 2).
Отклонение от этих параметров допустимо, если соотношение высоты и диаметра соответствует указанному выше диапазону.
Малый контейнер объемом (5±0,1) л (допускаемое отклонение ±2 % от номина-
б)
Рис. 2. Измерительный контейнер:
а) большой; б) малый
льного объема) с внутренним диаметром 167 мм и внутренней высотой 228 мм (рис. 2). Отклонение от этих параметров допустимо, если соотношение высоты и диаметра соответствует указанному выше диапазону.
Используются весы с различной точностью взвешивания: весы 1 с точностью взвешивания до 10 г при использовании больших контейнеров, весы 2 с точностью взвешивания до 1 г при использовании малых контейнеров. Используется также брусок из древесины твердых пород длиной около 600 мм с поперечным сечением 50х50 мм для удаления излишка материала с поверхности контейнера. Прочный брус из твердого дерева высотой 150 мм применяется для определения высоты, с которой сбрасывают контейнер.
Плоская деревянная отшлифованная доска толщиной около 15 мм и достаточных размеров, чтобы контейнер свободно поместился на ней при сбрасывании. Отбор и подготовку проб проводят по ГОСТ Р 54217-2010 и ГОСТ Р 54218 -2010. При необходимости проба может быть разделена по ГОСТ Р 54212-2010. Объем пробы должен превышать объем контейнера на 30 %. Необходимо следить, чтобы влага испытуемой пробы была равномерно рас-
Лесотехнический журнал 1/2014
123
Деревопереработка. Химические технологии
пределена внутри образца для предотвращения потери влаги.
Проведение испытания. Перед использованием контейнера определяют его массу и объем. Взвешивают пустой, чистый и сухой контейнер на весах. Затем полностью заполняют контейнер водой и добавляют несколько капель смачивающего вещества (например, жидкое мыло) и снова взвешивают его. Вода должна иметь температуру 10…20 °С. Затем рассчитывают объем контейнера (V) с учетом веса нетто воды и плотности воды 1000 кг/м3 и записывают результат с точностью до
0.00001 м3 для больших контейнеров и с точностью до 0.000001 м для малых контейнеров. Влиянием температуры на плотность воды пренебрегают. Объем контейнера должен регулярно контролироваться. Большие контейнеры используют для всех видов топлива. Для топлива с номинальным верхним размером кусков до 12 мм и диаметром частиц, не превышающим 12 мм, применяют малый контейнер.
Проведение измерения. Измерения проводят следующим образом:
а) в контейнер засыпают материал с высоты от 200 мм до 300 мм над верхним краем контейнера, пока не образуется конус максимально возможной высоты. Перед использованием контейнера необходимо убедиться, что он сухой и чистый;
б) заполненный контейнер встряхивают для равномерного распределения материала. Для этого его сбрасывают с высоты от 150 мм на деревянную доску, которую размещают на ровном жестком полу. Необходимо убедиться, что доска плотно прилегает к полу. При столкновении с доской кон-
тейнер должен находиться в вертикальном положении. Повторяют данную процедуру 2 раза. Затем заполняют пустое пространство в контейнере в соответствии с указанными выше условиями. Для правильного определения расстояния между доской и заполненным контейнером необходимо его поместить на высоту бруса в 150 мм;
в) удаляют излишек материала с помощью небольшого бруска вращающими движениями по поверхности контейнера. Если образец из грубого материала и его частицы не дают бруску свободно двигаться, то их удаляют вручную. При удалении большого количества материала вновь заполняют пространство контейнера и вновь проводят процедуру удаления;
г) взвешивают контейнер;
д) смешивают использованный и неиспользованный материал, повторяют измерение;
е) определяют массовую долю влаги в образце по ГОСТ Р 54186-2010 и ГОСТ Р 54192-2010 сразу после определения насыпной плотности.
Насыпную плотность образца (BD)7, выраженную в кг/м3 на рабочее состояние топлива, рассчитывают по формуле
Y mp2 — m,
(BD) = p2v p1 . (8)
Результат каждого отдельного определения вычисляют и округляют до первого десятичного знака после запятой, а среднюю насыпную плотность — как среднеарифметическое значение насыпной плотности и округляют до 10 кг/м.
Насыпную плотность образца (BD)d, выраженную в кг/м3 на сухое состояние топлива, рассчитывают по формуле
124
Лесотехнический журнал 1/2014
Деревопереработка. Химические технологии
(BD)d = (BD)y 100 W . (9)
100
Формула (9) не учитывает усадку или расширение материала в зависимости от влажности волокон. Древесному топливу свойственно содержание влаги ниже точки насыщения волокон, которая составляет около 25 % в зависимости от породы древесины. Поэтому корректное сравнение результатов измерений возможно только на образцах с аналогичным содержанием влаги. Если необходимо сравнить образцы с различным содержанием влаги и влажность хотя бы одного образца ниже точки насыщения волокна, то эффект набухания или усадки составляет порядка 0,7 % изменения объема, связанного с отличием влажности образца от влажности точки насыщения волокна. Для сравнения измерений на образцах с аналогичным содержанием влаги может быть использован этот поправочный коэффициент.
Протокол испытаний должен содержать: наименование лаборатории и дату проведения испытаний, наименование продукции или образца для испытаний, ссылку на используемый стандарт, описание размера используемого контейнера; описание любого отклонения от стандарта, условия, замечания и отклонения в ходе процедуры испытания, которые могут повлиять на его результат, результаты определения содержания влаги.
Повторяемость. Максимально допустимые расхождения между результатами измерений насыпной плотности при доверительной вероятности р=0,95 на сухое состояние топлива: для образцов с насыпной плотностью меньше 300 кг/м3 —
3,0 %; для образцов с насыпной плотностью, равной и большей 300 кг/м3 — 2,0 %.
Результаты двух параллельных определений (проведенных в течение краткого промежутка времени, но не одновременно), выполненных в одной и той же лаборатории одним исполнителем с использованием одной и той же аппаратуры на двух представительных образцах, взятых из одной и той же пробы для испытаний, не должны отличаться друг от друга более чем на значения, указанные выше.
Воспроизводимость. Разность результатов двух параллельных определений насыпной плотности на сухое состояние топлива при доверительной вероятности р=0,95, выполненных в двух различных лабораториях на представительных образцах, взятых из одной и той же пробы для испытаний, не должны отличаться друг от друга более чем на следующие значения: для образцов с насыпной плотностью меньше 300 кг/м3 — 6,0 %; для образцов с насыпной плотностью, равной и большей 300 кг/м3 — 4,0 %.
Действующий национальный стандарт на определение теплоты сгорания твердого биотоплива или древесных пел-лет отсутствует. Рекомендуется для определения этой характеристики использовать хорошо известный действующий стандарт для твердого минерального топлива ГОСТ 147-95.
Количество теплоты, выделяющейся при полном сгорании пеллет, отнесенное к единице массы этого топлива является удельной энергоёмкостью. Поэтому, определив теплоту сгорания пеллет можно перейти к определению удельной энергоемкости.
Лесотехнический журнал 1/2014
125
Деревопереработка. Химические технологии
Таким образом, национальным стандартом ГОСТ Р 54220-2010 определено большое разнообразие видов твердого биотоплива: брикеты, пеллеты, щепа,
дробленое топливо, кругляк, поленья (дрова), стружка, кора, солома, двукисточник, мискантус, энергетические культуры, семена плодов и другие виды биотоплива. При всем разнообразии этих видов, несомненно, требуется грамотная производственная адаптация как стандартных методик определения технических характеристик, регламентированных соответствующими документами, так и принятых для каждого случая индивидуально. Некоторые неточности, выявленные в стандартах на биотопливо твердое, объясняются объективными причинами их первичного введения, трудностями модифицирования европейских региональных стандартов под российские условия. При этом указанная часть характеристик не имеет общепринятых методик определения. Задачу принятия «унифицированных правил» или «методик» оценки некоторых свойств биотоплива требуется решать в ближайшее время, в противном случае ни производители, ни потребители этого вида продукции не смогут найти общих, понятных» всем измерительных инструментов». Такое обстоятельство усложняет продвижение на рынке этой востребованной для ряда субъектов хозяйственной деятельности продукции.
Сейчас требуется значительная, кропотливая работа по адаптации этих методик для конкретного вида биотоплива. Большое разнообразие характеристик, рег-
ламентированных стандартами в совокупности в большим разнообразием видов твердого биотоплива, предполагает создание и расширение сети сертифицированных лабораторий. Это объясняется сложностями процедуры проведения некоторых методик, обязательным наличием высококвалифицированного персонала и значительной дороговизной применяемого оборудования, что финансово обременительно, а иногда не под силу не только мелким, но и крупным производителям.
Библиографический список
1. Сафонов А. О. Пути рационального использования отходов древесины и сельскохозяйственных растений [Текст] / А. О. Сафонов, Чжоу Динггуо, Чжан Ян [и др.] // Вестник Таджикского технического университета. — 2012. — № 4 (16). — С 11-14.
2. Сафонов, А. О. Состояние и перспективы производства новых видов древесного биотоплива [Текст] / А. О. Сафонов, Е. В. Зотова // Актуальные направления научных исследований XXI века: теория и практика: сб. науч. тр. — Воронеж, 2013. — Вып 5. — С. 320-324.
3. Сафонов, А. О. Тепломассоперенос и динамика сушки дисперсных материалов в барабанных сушилках [Текст] / А. О. Сафонов. — Воронеж : ВГУ, 2002. — 240 с.
4. ГОСТ Р 54220-2010 (ЕН 149611:2010) Биотопливо твердое. Технические характеристики и классы топлива. Часть 1. Общие требования. — М., 2012. — 43 с.
126
Лесотехнический журнал 1/2014
Удельное энергопотребление и качество древесных гранул, полученных с использованием измельчения сосны с высоким содержанием влаги в грануляторе с плоской матрицей (Журнальная статья)
Тумулуру, Джая Шанкар. Удельное энергопотребление и качество древесных гранул, полученных с использованием измельчения высоковлажной древесной сосны на грануляторе с плоской матрицей . США: Н. П., 2016.
Интернет. DOI: 10.1016 / j.cherd.2016.04.007.
Тумулуру, Джая Шанкар. Удельное энергопотребление и качество древесных гранул, полученных с использованием измельчения высоковлажной древесной сосны на грануляторе с плоской матрицей . Соединенные Штаты. https://doi.org/10.1016/j.cherd.2016.04.007
Тумулуру, Джая Шанкар. Сидел .
«Удельное энергопотребление и качество древесных гранул, полученных с использованием измельчения высоковлажной древесной сосны в грануляторе с плоской матрицей».Соединенные Штаты. https://doi.org/10.1016/j.cherd.2016.04.007. https://www.osti.gov/servlets/purl/1357216.
@article {osti_1357216,
title = {Удельное энергопотребление и качество древесных гранул, полученных с использованием измельчения высоковлажной сосновой древесины в грануляторе с плоской матрицей},
author = {Тумулуру, Джая Шанкар},
abstractNote = {В настоящем исследовании план эксперимента Бокса – Бенкена использовался для понимания влияния содержания влаги в измельченной древесной сосне (33–39%, мас.б.), скорость фильеры (40–60 Гц) и температура предварительного нагрева (30–90 ° C) от качества окатышей и удельного энергопотребления. Полученные частично высушенные гранулы имели высокое содержание влаги в диапазоне 19–28% (мас.%) И были дополнительно высушены до содержания <9% (мас.%) В механической печи, установленной на 70 ° C, в течение 3 часов. Высушенные гранулы дополнительно оценивали на содержание влаги в гранулах, единицу, объем, плотность утряски и долговечность. Модели поверхности отклика, разработанные для свойств продукта, адекватно описывают процесс на основе значений коэффициента детерминации.Разработанные участки поверхности показали, что более высокая удельная, насыпная плотность и утряска (1050, 520, 560 кг / м3) достижима при содержании влаги 33–35% (мас. –60 ° С. Более высокое содержание влаги в 39% (мас.%) Снижает удельную, насыпную и насыпную плотность до <912, 396 и 452 кг / м3. Более высокие значения долговечности> 95% были получены при 33–35% (масс.) При более низких температурах предварительного нагрева 30–50 ° C и более высокой скорости фильеры> 50 Гц. При содержании влаги 33% (масс.%) В измельченной древесной сосне, температуре предварительного нагрева 90 ° C и скорости фильеры 60 Гц наблюдаемое удельное потребление энергии составило <116 кВт · ч / т.В результате исследования с помощью сканирующего электронного микроскопа показали, что сшивание лигнина является основной причиной связывания измельченной древесины сосны ложной при высоком содержании влаги.},
doi = {10.1016 / j.cherd.2016.04.007},
url = {https://www.osti.gov/biblio/1357216},
journal = {Химические исследования и разработки},
issn = {0263-8762},
число = C,
объем = 110,
place = {United States},
год = {2016},
месяц = {4}
}
(PDF) Определение плотности частиц окатышей и брикетов
были рассчитаны для 15 повторов в каждой лаборатории
и для всех участвующих лабораторий.Кроме того, пределы относительной и абсолютной повторяемости и воспроизводимости
были рассчитаны в соответствии с ISO 5725.2 [8]. Для
таблетокбыли рассчитаны повторяемость и воспроизводимость
для трех отдельных групп таблеток. Первая группа включала
из всех 15 типов пеллет, испытанных в проекте, вторая группа
состояла только из пеллет из сельскохозяйственных остатков, а третья группа
состояла только из древесных пеллет.
Количество повторов, необходимое для обеспечения
нескольких уровней точности 0.5%, 1; 2% или 5% было
, определенным в соответствии с обычной процедурой статистического расчета
в соответствии с Дагнели [10], учитываемые ошибки первого рода
,и второго рода равны, соответственно, a¼0: 05 и
b¼0: 5. Для сравнения средних значений плотности частиц
, полученных разными методами, был проведен дисперсионный анализ
(ANOVA) с уровнем значимости 5%.
Сравнение пределов повторяемости и воспроизводимости
было проведено с помощью F-теста (тест на равенство
дисперсий с a5%) [10].
В отношении парафинового покрытия были проведены различные расчеты
для оценки различных режимов коррекции
для добавленного объема покрытия. Зная массу нанесенного парафина
и плотность парафина, объем нанесенного парафина
на образец был определен расчетом
.
В первом подходе предполагалось, что общее количество парафина
остается за пределами образца. Следовательно, скорректированная плотность
(плотность Corr1) была рассчитана путем вычитания
расчетного объема парафина из измеренного объема
.Этот расчет был сделан для брикетов и окатышей.
Во втором подходе (только для гранул) использование пикнометра
позволяет определить среднее количество парафина
, которое проникает в образец во время подготовки (нанесения покрытия)
. Для измерений были выбраны три из 15 типов гранул
(древесные гранулы диаметром 6 мм, древесные гранулы диаметром
8 мм и гранулы из сельскохозяйственных отходов
). Три образца были измерены дважды с
ибез парафинового покрытия (10 повторов каждый).Сравнение
между обоими объемами и количеством нанесенного парафина
позволило определить долю проникновения парафина для каждого из
трех типов гранул.
Эти доли проникновения парафина были нанесены на все
испытанных окатышей (в зависимости от сырья и диаметра
) для расчета второй скорректированной плотности (плотность Corr2
) с учетом только объема парафина, который остается на
. поверхность гранулы.Скорректированные плотности
(Corr1 и Corr2) сравнивали с нескорректированной плотностью
(плотность Nc).
3. Результаты и обсуждение испытаний таблеток
3.1. Средние значения и стандартное отклонение
На рис. 5 показаны результаты и стандартные отклонения испытанных методов определения плотности частиц
для 15 гранул
(средние значения для всех лабораторий). Что касается вариабельности результатов
, наблюдается тенденция в зависимости от типа
одиночных гранул.Это было подтверждено дисперсионным анализом
(метод двухфакторного дисперсионного анализа и типы гранул, фиксированная модель
), который показывает, что тип одиночной гранулы имеет значительное влияние
, а метод имеет большое влияние на дисперсию
.
Фактически, на изменчивость влияет значение самой плотности частиц
. Отклонения наиболее высоки для окатышей
низкой плотности, а наименьшие — для окатышей высокой плотности. Это
было подтверждено анализом ANOVA (двухфакторный анализ: диаметр
и сырье) дисперсий с плотностью
в качестве сопеременной.
Для пеллет из сельскохозяйственных остатков и древесины с низкой плотностью
пеллет (плотность ≥1,2 г / см
3
), стереометрические определения
приводят к более высокой вариабельности (отклонение 0,062 (г / см
3
))
2
)
по сравнению с методами вытеснения жидкости, особенно
, когда используется метод плавучести с добавлением смачивающего агента
(отклонение 0,019 (г / см
3
)
2)
).
Что касается древесных гранул с более высокой плотностью частиц,
в качестве теста на равенство дисперсии показало, что методы с использованием смачивающего агента
дают эквивалентные отклонения (0,028 (г / см
3
)
2
)
, что значительно ниже, чем полученные с помощью трех других методов
.
Из-за парафинового покрытия плотности, полученные с помощью методов
с использованием парафинов (гидростатических и плавучести), на
ниже, чем при использовании других методов.
Сравнение гидростатических методов и методов плавучести
с парафином и смачивающим агентом было выполнено с помощью
ANOVA (двухфакторный дисперсионный анализ, методы и
партнеров, фиксированная модель). Этот анализ показал, что методы плавучести и гидростатики
— независимо от того, применяются ли парафиновые покрытия
или смачивающие агенты — похоже, дают аналогичные результаты и поэтому могут считаться совместимыми с
. Было также обнаружено, что влияние лаборатории
на результат очень существенно.Дополнительно
наблюдалось взаимодействие между лабораторией и методом
факторов, что означает, что для некоторых лабораторий
средние значения плотности частиц, полученные с помощью
обоих методов, могут быть разными.
ИЗДЕЛИЕ В ПРЕССЕ
0,9
1
1,1
1,2
1,3
1,4
Плотность частиц (г / см3)
HP
BP
StB
Пеллеты
Древесные гранулы
P1P2P6P13P12P5P9P8P7P4P3P11P10P14P15
Рис.5. Плотность частиц 15 типов гранул, оцененная 5 различными методами
(среднее значение и стандартное отклонение участвующих лабораторий). HP,
гидростатический с парафиновым покрытием, BP, плавучесть с парафиновым покрытием,
StB, стереометрические измерения, HWA, плавучесть с смачивающими веществами,
BWA, плавучесть с смачивающими веществами.
F. Rabier et al. / Биомасса и биоэнергетика 30 (2006) 954–963958
(a) Взаимосвязь между плотностью гранул и давлением уплотнения, (b)….
Прессование конденсации — ключевой процесс перед утилизацией сыпучей кукурузной соломы. В этом исследовании сначала изучалось влияние времени стабилизации на плотность релаксации и стабильность размеров кукурузной соломы, а затем время стабилизации было определено как 60 с путем всестороннего учета эффекта сжатия, потребления энергии, эффективности и значимости. Исходя из этого, влияние содержания воды (12%, 15%, 18%), отношения времени поддержания давления к времени стабилизации (0, 0.5, 1), максимальное напряжение сжатия (60,4, 120,8, 181,2 кПа) и масса подачи (2,5, 3, 3,5 кг) от плотности релаксации, коэффициента размерной стабильности и удельного энергопотребления соломенных блоков после сжатия были исследованы с помощью Дизайн Бокса – Бенкена. Было обнаружено, что содержание воды, отношение времени поддержания давления к времени стабилизации, максимальное напряжение сжатия и подаваемая масса — все это очень существенно влияет на плотность релаксации, коэффициент размерной стабильности и удельное потребление энергии.Взаимодействие между содержанием воды и максимальным напряжением сжатия существенно повлияло как на плотность релаксации, так и на удельное потребление энергии. Взаимодействие между отношением времени поддержания давления ко времени стабилизации и подаваемой массой существенно повлияло на коэффициент размерной стабильности. Коэффициенты и индексы регрессировали по квадратным уравнениям с коэффициентами детерминации выше 0,97 во всех уравнениях. Оптимизированные параметры процесса: содержание воды 13.63%, время поддержания давления 22,8 с, время поддержания деформации 37,2 с, максимальное напряжение сжатия 109,58 кПа и масса исходного материала 3,5 кг. В этих условиях плотность релаксации блоков соломы холодного прессования составляла 145,63 кг / м3, коэффициент размерной стабильности составлял 86,89%, а удельный расход энергии составлял 245,78 Дж / кг. Ошибки между результатами тестирования и прогнозируемыми результатами были менее 2%. Низкая теплотворная способность блоков из измельченной кукурузной соломы холодного отжима составила 12,8 МДж / кг.Благодаря методу ситуационного анализа, основанному на внутренней и внешней конкурентной среде и условиях конкуренции (метод SWOT-анализа), блоки измельченной кукурузной соломы холодного прессования потребляли наименьшее потребление энергии на формирование, чем другие методы формования, и, таким образом, их можно нагревать фермерами. . Наши результаты могут служить справочным материалом для группирования кукурузной соломы, процессов формования холодным прессованием и повторного прессования тюков соломы.
Гранулометрический состав и физико-химические свойства гранул из соломы, сена и их смесей
Гранулометрический состав
На основании теста Колмогорова – Смирнова (K – S) можно предположить, что биомасса и Физико-химические параметры гранул имеют нормальное распределение, поскольку значения p были выше 0.20 для всех параметров распределений (таблица 1). Тест Лиллиэфорса, скорректированный с помощью теста K – S (p = 0,01–0,05), и тест Шапиро – Уилка (p = 0,0011–0,0360) не дали положительных результатов. На основании теста K – S предполагалось, что значения физико-химических параметров имеют нормальное распределение.
Таблица 1 Значения нормального распределения измельченной биомассы и параметров гранул на основе тестов Колмогорова – Смирнова (KS, D) и скорректированных тестов Лиллиефорса (p-Lilliefors) и Шапиро – Уилка (WS, W)На основе тестов Хартли, Кохрана, Бартлетта и Левена параметры гранул показали однородность дисперсии, поскольку значения p для этих параметров находились в диапазоне от 0.01 до 0,77 (таблица 2). P-значения для этих тестов были ниже 0,01 для измельченной биомассы. Однако с некоторой осторожностью можно предположить однородность дисперсии, учитывая, что наиболее важные параметры гранул соответствуют этим предположениям.
Таблица 2 Значения дисперсионного анализа однородности на основе тестов Хартли, Кохрана, Бартлетта и Левена для параметров измельченной биомассы и гранулНебольшие значения асимметрии и эксцесса подтверждают соответствие исследуемых распределений параметров нормальному распределению.Соответственно параметры асимметрии и эксцесса находились в диапазонах (- 1,46, 2,09) и (- 1,27, 2,99) соответственно (таблица 3).
Таблица 3 Средние, минимальные и максимальные значения, стандартные отклонения (SD), коэффициент вариации (CV), асимметрия и эксцесс для различных типов биомасс и параметры распределения гранулРаспределение плотности частиц сена, соломы и их смеси было асимметричным (рис. 1) с асимметричным графиком справа GS i малых значений 0.15–0,36 (таблица 4). Положительные значения графического эксцесса, K г = 0,96–1,03 (таблица 4), подтверждают крутизну распределений. Аналогичные тенденции распределения частиц наблюдались для проса проса и ячменной соломы [1], гигантского мискантуса, Spartina pectinata , топинамбура [23], проса просо, пшеничной соломы и кукурузной соломы [29], соломы и сена [46].
Рис. 1Распределение частиц измельченной биомассы по размерам и частота накопленной массы с использованием модели Розина – Раммлера (сплошные линии для реальных значений, прерывистые линии для модели Розина – Раммлера)
Таблица 4 Средние значения характеристических показателей гранулометрического состава сена, соломы и их смесейПоскольку резка и измельчение биомассы проводились в одних и тех же условиях, с одинаковыми настройками параметров машины, исходя из характеристик гранулометрического состава, можно сделать вывод, что хрупкая солома была более мелкой, чем сено.В диапазоне размеров до 0,50 мм доля мелких частиц соломы была больше, чем у сена, что хорошо видно на кумулятивном графике гранулометрического состава. Доля мелких частиц определилась с более низким средним геометрическим значением размера частиц соломы, чем для сена, которые составили 0,63 мм и 0,65 мм соответственно (Таблица 3). Но более крупная доля соломы, чем сена, повлияла на увеличение безразмерных стандартных отклонений, которые составили 2,95 и 2,09 соответственно (Таблица 3). Смесь сена и соломы привела к уменьшению доли мелких частиц и увеличению доли средних и более длинных частиц, что привело к увеличению среднего геометрического размера частиц до 0.69 мм, т.е. больше, чем у соломы, но с меньшим размером частиц, так как безразмерное стандартное отклонение составило 2,37 (таблица 3). Параметры гранулометрического состава в зависимости от качества гранул описаны в дальнейшей части статьи.
Кривые кумулятивной массовой частоты для модели RR относительно точек измерения показаны на рис. 1, а характерные параметры гранулометрического состава сена, соломы и их смеси представлены в таблице 4.Параметры размера x R 0,78, 0,75 и 1,01 мм соответственно были больше медианного размера x 50 на 0,65, 0,56 и 0,80 мм соответственно. Средние геометрические параметры сена, соломы и их смешанных частиц были смещены вправо с увеличением на x R , что привело к сочетанию уменьшения количества мелких частиц и увеличения количества крупных частиц. Параметр распределения RR n (наклон), который для сена, соломы и их смеси составил 1.96, 1,26 и 1,61, соответственно, представляет собой однородность частиц, которая имеет сильную положительную корреляцию (0,993, Таблица 5) с эффективным размером x 10 (0,25, 0,12 и 0,25 мм соответственно) и очень сильной отрицательной корреляция (- 0,986) с относительной массой RS м (1,45, 2,39 и 1,81 соответственно), которые накапливались для 80% массы частиц. Относительный диапазон масс был больше 1,0, что указывает на широкое распределение частиц для каждого типа биомассы.Это согласуется с опубликованными тенденциями [29].
Таблица 5 Матрица коэффициентов корреляции Пирсона Параметры гранулометрического состава сена, соломы и их смесей (N = 15)Значение индекса однородности I u = 14,29% было наименьшим для гранулометрического состава сена, за которым следовали смесь и солома со значениями 9,41% и 4,79% соответственно. Этот параметр связан со значениями эксцесса и асимметрии.Если гранулометрический состав является плоским (наименьший эксцесс K г значение 0,96 было для сена) и симметричным (наименьший коэффициент асимметрии GS i значение 0,15 было для сена), смесь более однородна [46]. Таким образом, добавление сена к соломе повысило однородность смеси, и в то же время более длинные частицы соломы могут повысить прочность гранул для разрушения. Влияние неоднородности размера частиц на критическое значение числа фракций по размеру частиц было исследовано Wiącek и Stasiak [51] для насадок с различным соотношением диаметров наибольшего и наименьшего зерен.В смесях с большим соотношением размеров частиц мелкие частицы легко помещаются в поры между крупными частицами, тем самым увеличивая плотность упаковки. Kong et al. [27] предположили, что более длинные и широкие волокна могут служить «твердым мостиком» для обертывания мелких частиц. Смесь частиц разного размера даст оптимальное качество гранул, потому что смесь частиц будет обеспечивать межчастичное связывание практически без промежутков между частицами. Для сена и смеси, включая перекос изображения GS i был равен 0.15 и 0,25, соответственно, и это распределение частиц биомассы по размеру было «мелким перекосом» (+ 0,1 ≤ GS i ≤ + 0,3). Для соломы GS i = 0,36, а распределение частиц по размерам было «симметричным» (+ 0,3 ≤ GS i ≤ + 1,0). Для всех типов биомассы в отношении графического эксцесса K г (0,96–1,03) распределения можно назвать «мезокуртическим» распределением (0.90 ≤ K г ≤ 1.11) [52], которое представляет собой распределение с такой же степенью пика относительно среднего, что и у нормального распределения.
Значения коэффициента однородности сена и смеси C и 3,00 и 3,84, которые были <4,0, подтвердили однородность размеров частиц этих типов биомассы. Для соломы значение коэффициента однородности составило 5,83 и указывало на разнообразие гранулометрического состава.Коэффициент градации C г для гранулометрических составов составлял 1,13–1,30 и в диапазоне от 1 до 3 представляет хорошо дифференцированные распределения частиц по размерам всех типов биомассы [46].
Включая графические стандартные отклонения σ ig описательно классифицируют биомассу твердых частиц на основе логарифмической исходной классификации графических мер Фолка и Уорда [53] [52]. На основании определенных значений (Таблица 4) гранулометрический состав сена с включенными графическими стандартными отклонениями 0.37 был классифицирован как « хорошо отсортированный » (0,35 <σ ig <0,50 мм), а солома и смесь с σ ig 0,52 и 0,56, соответственно, как « умеренно хорошо отсортированный » (0,50 <σ ig <0,70 мм). Эти классификации будут меняться, когда одна и та же биомасса преобразуется при различных настройках перерабатывающего оборудования или рабочих параметрах, таких как зазор или скорость, а также размеры проема экрана классификации продукта [46].
Физико-химические свойства гранул
Параметры измельченной биомассы и гранул статистически значимо различались (при p ≤ 0.0001). На основе теста Дункана было обнаружено, что почти все значения создают отдельную гомогенную группу (Таблица 3).
После агломерации биомассы под давлением средняя влажность материала гранул снизилась на 0,50% мас. И достигла абсолютных значений для сена, соломы и их смеси, равных 5,56 ± 0,15, 5,56 ± 0,20 и 5,87 ± 0,26. % wb соответственно. Это может быть результатом случайного отбора проб, о чем свидетельствует тот факт, что влажность гранул из сена и соломы была выше, чем в отдельных компонентах биомассы.Незначительное уменьшение влажности гранул по сравнению с измельченным материалом могло быть связано с более низким давлением уплотнения, о чем свидетельствуют низкие значения коэффициентов прочности гранул (92,68–93,59%) (Таблица 3). В других исследованиях того же типа биомассы [16] снижение содержания влаги в гранулах составило 2,57%, в то время как добавление карбоната кальция привело к снижению на 6,44%. Карбонат кальция значительно снизил влажность материала в производимых гранулах.Различия в содержании влаги в материале и его подверженность изменениям под влиянием карбоната кальция могут повлиять на агломерацию биомассы и, следовательно, на механическую прочность и прочность гранул. Сравнение полученных результатов с ранее опубликованными данными показало, что значения влажности полученной измельченной биомассы и гранул были примерно в два раза ниже, чем значения, полученные в других лабораторных испытаниях [46]. Mani et al. [1] наблюдали, что влага в материале во время уплотнения увеличивает сцепление за счет сил Ван-дер-Уолла, тем самым увеличивая площадь контакта частиц.Сила сжатия, размер частиц и влажность 12–15% масс. Значительно повлияла плотность гранул из соломы ячменя, соломы кукурузы и проса. Однако различные размеры частиц пшеничной соломы не имели существенных различий по плотности гранул [54]. Низкое содержание влаги в материалах (5–10%) привело к получению более плотных, стабильных и долговечных продуктов по сравнению с продуктами, произведенными из биомассы с более высоким содержанием влаги (15%). В лабораторном прессе для гранул [55] содержание влаги в сырье было доминирующим фактором для плотности гранул и прочности на сжатие.Для тростниковой канареечной травы оптимальная плотность гранул достигается при содержании влаги 5,2% и 8,5% при давлении сжатия 300 МПа и 400 МПа. Для рисовой соломы оптимальный диапазон содержания влаги составляет от 13% до 20% при температуре формования 60 или 80 ° C. Оптимальный размер частиц составлял от 10 до 20 мм с учетом времени и энергии, необходимых для измельчения, хотя размер частиц не оказывал значительного влияния на коэффициент выхода и долговечность гранул рисовой соломы [30]. Оптимальное содержание влаги для производства плотных гранул из ячменной соломы было выше и оказалось в диапазоне 19–23% [56].
Хотя значения коэффициентов долговечности гранул находились в узком диапазоне, они статистически значимо различались для всех типов биомассы, таким образом давая наивысшее среднее значение 93,59% для соломенных материалов и наименьшее значение 92,68% для смешанных материалов. материалы. Принимая во внимание значения стандартного отклонения для сена и соломы, можно констатировать, что статистическая значимость различий незначительна. Учитывая небольшую разницу в содержании влаги в измельченной биомассе, можно сказать, что долговечность гранул была логически изменена.Можно предположить, что долговечность гранул аналогична, когда изменения небольшие. Смешивание сена и соломы не привело к ожидаемому синергическому эффекту, который привел бы к усилению связей между частицами различных типов биомассы. Размеры частиц для смесей биомассы были самыми большими (0,69 мм), тогда как соответствующие размеры для сена и соломы были несколько меньше, 0,65 мм и 0,63 мм соответственно. Таким образом, подтверждается, что доля более мелких частиц в соломе, но с переплетенными более длинными частицами (рис.1), т.е. наиболее разнообразное распределение размеров частиц относительно сена и смеси, характеризующееся безразмерным стандартным отклонением (2,95 против 2,10 и 2,37 соответственно), позволило немного улучшить связи между частицами и произвести гранулы с немного более высокой прочностью. (93,59%). По данным Kraszkiewicz et al. [57], долговечность гранул из соломы тритикале, сена и зерновых смесей с влажностью 11,5–14,8% мас. Составила 96,00%, 97,67% и 98,33% соответственно.Коэффициент стойкости гранул растительной биомассы находился в пределах 86,60–98,50% [60].
Удельная плотность и насыпная плотность гранул были самыми высокими для продуктов, изготовленных из смесей биомассы, и достигли значений 1102 кг сухого вещества м -3 и 514 кг сухого вещества м -3 , соответственно. Удельная плотность гранул из сена и соломы составляла 1034 кг DM м -3 и 974 кг DM м -3 , соответственно, а значения объемной плотности составляли 478 кг DM м -3 и 498 кг DM м м. −3 соответственно.Согласно стандарту PN-EN ISO 17225-6: 2014-08 [58], объемная плотность недревесных гранул требуется ≥ 600 кг м −3 . Шведский стандарт SS 18 71 20 [59] требует, чтобы насыпная плотность была выше 500 кг м −3 (для «промышленного» качества; 3-й класс окатышей). Таким образом, насыпная плотность гранул из сена и соломы была даже ниже, чем требуется шведским стандартом. Аналогичные результаты насыпной плотности пеллет в диапазоне 323–567 кг м −3 , полученные из растительной биомассы (пшеничная солома, рапсовая солома, кукурузная солома, луговое сено, пшеничные отруби, зерновые и рапсовые отходы), были получены Недзилкой и Шпрингиелем. [60].
По прочности и плотности гранул можно надежно оценить качество продукции. Свойства и параметры гранулятора, такие как механика давления прессующих валков, размеры матрицы, геометрия канала в матрице, способ подачи и увлажнения сырья перед уплотнением и дозировка сырья в матрицу были сопоставимы. . Кроме того, долговечность и плотность гранул зависят в основном от свойств обработанной биомассы.Значительно более высокие размеры частиц гранул смеси (0,69 мм) по сравнению с гранулами сена и соломы (0,65 мм и 0,63 мм соответственно), вероятно, привели к более низкой долговечности гранул из смеси, чем из отдельных видов биомассы. Однако следует подчеркнуть, что размеры частиц биомассы были намного меньше необходимого размера 3,2 мм [1]. Обычно предполагается, что мелкие частицы не должны составлять более 10–20% корма, поскольку они снижают качество гранул и вызывают трение о фильере для гранул [9].Гранулы, полученные из мелких частиц, обладают большей прочностью на сжатие и абразивом, а также долговечностью [14, 19, 27, 51, 57]. Mani et al. [54] обнаружили, что размер частиц значительно влияет на плотность гранул из ячменной соломы, кукурузной соломы и проса, но не в случае пшеничной соломы. Jannasch et al. [34] обнаружили, что твердость гранул проса проса умеренно повышалась при уменьшении размера сита с 3,2 до 2,8 мм. Основываясь на результатах текущих исследований, можно сказать, что усиленное измельчение улучшает восприимчивость биомассы к процессу агломерации под давлением [12], но повышенная фракция мелких частиц и пыли является нежелательным свойством [16].Сообщается, что для получения гранул необходимо сочетание мелкого и среднего измельчения, поскольку смесь будет обеспечивать межчастичное связывание практически без промежутков между частицами. Сообщалось, что частицы, имеющие длинную форму, обладают преимуществами, поскольку они могут прочно слипаться благодаря механизму блокировки [1, 13, 17]. Результаты, представленные Лисовским и Свентоховским [61] по значениям коэффициента долговечности, привели к выводу, что отделение крупных частиц от смеси мискантуса, предназначенной для производства гранул, не привело к статистически значимой разнице в долговечности продуктов.
В заключение, качество гранулированного топлива подтверждается двумя основными факторами; плотность и прочность [62]. Как уже упоминалось, высокая насыпная плотность гранул подразумевает более высокую удельную энергию топлива, в то время как механическая прочность представляет собой более высокое сопротивление гранул различным внешним нагрузкам, таким как истирание, сдвиг, изгиб и ударные силы, прикладываемые во время погрузочно-разгрузочных работ и транспортировки. Вариации удельной плотности гранул и насыпной плотности существенно влияют на количество и качество топлива или подаваемого топлива во время транспортировки и хранения или когда они помещаются на ленточный конвейер электростанций и в биореакторы для производства биотоплива и биоэнергетики.Следовательно, производство гранул должно осуществляться в таких условиях, чтобы уменьшить колебания плотности гранул [5].
Теплотворная способность гранул из смеси сена и соломы была близка к средним арифметическим значениям теплотворной способности гранул, сделанных только из сена или соломы. Соответствующая теплотворная способность составляла 16,64 МДж кг -1 , 16,07 МДж кг -1 и 17,00 МДж кг -1 , соответственно. Более того, Niedziółka и Szpryngiel [63] сообщили о средней теплотворной способности для пшеничной и ржаной соломы 17.05 МДж кг -1 и 16,35 МДж кг -1 , соответственно, и значения 16,1-17,5 МДж кг -1 для растительной биомассы.
На основании значений коэффициента корреляции Пирсона (таблица 6) можно сделать вывод, что теплотворная способность коррелирует с насыпной плотностью гранул (0,637), но не обеспечивает сцепления с удельной плотностью гранул (-0,281), несмотря на заявлена корреляция между этими плотностями (0,392). Удельная и насыпная плотность гранул коррелировали со средними геометрическими значениями длин частиц (0.705 и 0,483 соответственно).
Таблица 6 Корреляционная матрица для среднего геометрического длины частицы x г , безразмерное стандартное отклонение с г , влажность биомассы MC b , влажность гранул p , коэффициент прочности DU , удельная плотность гранул ρ jp , насыпная плотность гранул ρ bp , теплотворная способность Q pКоэффициент долговечности отрицательно коррелировал со средним геометрическим значением длины частицы (- 0.450) и влажности измельченной биомассы (- 0,412). Чем меньше геометрический размер частиц и чем ниже была влажность материала, тем выше была долговечность гранул, но следует подчеркнуть, что изменение этих параметров, особенно влажности, было незначительным. {2} + {b_2} {x_g} {\ rho _ {jp }} / {\ rho _ {bp}} + {b_3} M {C_p} {x_g} {\ rho _ {jp}} / {\ rho _ {bp}} \) коэффициента прочности в зависимости от влажности гранул MC p , а соотношение x g ρ jp / ρ bp Фиг.2
Характеристика коэффициента долговечности в зависимости от влажности окатышей MC p и отношения x g ρ jp / ρ bp
На поверхности, представленной на рис.2, можно заметить, что долговечность гранул увеличивается с увеличением влажности гранул MC p , особенно для малых значений x g ρ jp / ρ т.н. .Эти отношения являются результатом небольших различий в содержании влаги, поскольку влажность измельченной биомассы была слишком мала для достижения хорошей пластичности частиц при термической декристаллизации биомассы. Это было следствием трения между частицами и стенками камеры фильеры, а также трения между соседними частицами, движущимися под давлением ролика на материал. На основе литературы можно утверждать, что на долговечность гранул могут влиять характеристики сырья, содержание влаги, форма и гранулометрический состав, истинная плотность биомассы, предварительная обработка и условия гранулирования, включая использование связующих, смеси сырья, температуры или давления уплотнения [6, 12, 14].Соответственно, необходимы дальнейшие исследования для разработки математических моделей, основанных на физических свойствах измельченного растительного материала и рабочих параметров гранулятора.
Подводя итоги анализа результатов исследований и их обсуждений, можно сделать вывод, что механическая прочность гранул была выше при меньшем размере частиц и более низком содержании влаги. В этих условиях удельная плотность гранул и насыпная плотность были выше, а теплотворная способность гранулированного материала была выше.Долговечность гранул из соломы была максимальной, что, вероятно, было связано с большим разбросом размера частиц. При значительной доле мелких частиц в соломе было довольно много более длинных частиц, которые способствовали более длительным сочетаниям между частицами. При испытании на долговечность гранулы трутся о внутренние поверхности устройства и между гранулами, но гранулы также подвергаются падению с внутреннего диагонального барьера под действием силы тяжести. В частности, удар окатышей о стальную поверхность устройства может привести к разрушению окатышей.Логический анализ позволяет предположить, что гранулы, изготовленные из материала с меньшими размерами частиц, могут делиться на границе между частицами, а с более крупными размерами частиц разделение гранул также может происходить по длине частиц, прочность которых чаще всего превышает прочность частиц. связи между частицами. Это предположение требует проведения целевых исследований.
Произошла ошибка при настройке пользовательского файла cookie
Этот сайт использует файлы cookie для повышения производительности.Если ваш браузер не принимает файлы cookie, вы не можете просматривать этот сайт.
Настройка вашего браузера для приема файлов cookie
Существует множество причин, по которым cookie не может быть установлен правильно. Ниже приведены наиболее частые причины:
- В вашем браузере отключены файлы cookie. Вам необходимо сбросить настройки своего браузера, чтобы он принимал файлы cookie, или чтобы спросить вас, хотите ли вы принимать файлы cookie.
- Ваш браузер спрашивает вас, хотите ли вы принимать файлы cookie, и вы отказались.Чтобы принять файлы cookie с этого сайта, нажмите кнопку «Назад» и примите файлы cookie.
- Ваш браузер не поддерживает файлы cookie. Если вы подозреваете это, попробуйте другой браузер.
- Дата на вашем компьютере в прошлом. Если часы вашего компьютера показывают дату до 1 января 1970 г., браузер автоматически забудет файл cookie. Чтобы исправить это, установите правильное время и дату на своем компьютере.
- Вы установили приложение, которое отслеживает или блокирует установку файлов cookie.Вы должны отключить приложение при входе в систему или проконсультироваться с системным администратором.
Почему этому сайту требуются файлы cookie?
Этот сайт использует файлы cookie для повышения производительности, запоминая, что вы вошли в систему, когда переходите со страницы на страницу. Чтобы предоставить доступ без файлов cookie потребует, чтобы сайт создавал новый сеанс для каждой посещаемой страницы, что замедляет работу системы до неприемлемого уровня.
Что сохраняется в файле cookie?
Этот сайт не хранит ничего, кроме автоматически сгенерированного идентификатора сеанса в cookie; никакая другая информация не фиксируется.
Как правило, в файле cookie может храниться только информация, которую вы предоставляете, или выбор, который вы делаете при посещении веб-сайта. Например, сайт не может определить ваше имя электронной почты, пока вы не введете его. Разрешение веб-сайту создавать файлы cookie не дает этому или любому другому сайту доступа к остальной части вашего компьютера, и только сайт, который создал файл cookie, может его прочитать.
Произошла ошибка при настройке пользовательского файла cookie
Этот сайт использует файлы cookie для повышения производительности.Если ваш браузер не принимает файлы cookie, вы не можете просматривать этот сайт.
Настройка вашего браузера для приема файлов cookie
Существует множество причин, по которым cookie не может быть установлен правильно. Ниже приведены наиболее частые причины:
- В вашем браузере отключены файлы cookie. Вам необходимо сбросить настройки своего браузера, чтобы он принимал файлы cookie, или чтобы спросить вас, хотите ли вы принимать файлы cookie.
- Ваш браузер спрашивает вас, хотите ли вы принимать файлы cookie, и вы отказались.Чтобы принять файлы cookie с этого сайта, нажмите кнопку «Назад» и примите файлы cookie.
- Ваш браузер не поддерживает файлы cookie. Если вы подозреваете это, попробуйте другой браузер.
- Дата на вашем компьютере в прошлом. Если часы вашего компьютера показывают дату до 1 января 1970 г., браузер автоматически забудет файл cookie. Чтобы исправить это, установите правильное время и дату на своем компьютере.
- Вы установили приложение, которое отслеживает или блокирует установку файлов cookie.Вы должны отключить приложение при входе в систему или проконсультироваться с системным администратором.
Почему этому сайту требуются файлы cookie?
Этот сайт использует файлы cookie для повышения производительности, запоминая, что вы вошли в систему, когда переходите со страницы на страницу. Чтобы предоставить доступ без файлов cookie потребует, чтобы сайт создавал новый сеанс для каждой посещаемой страницы, что замедляет работу системы до неприемлемого уровня.
Что сохраняется в файле cookie?
Этот сайт не хранит ничего, кроме автоматически сгенерированного идентификатора сеанса в cookie; никакая другая информация не фиксируется.
Как правило, в файле cookie может храниться только информация, которую вы предоставляете, или выбор, который вы делаете при посещении веб-сайта. Например, сайт не может определить ваше имя электронной почты, пока вы не введете его. Разрешение веб-сайту создавать файлы cookie не дает этому или любому другому сайту доступа к остальной части вашего компьютера, и только сайт, который создал файл cookie, может его прочитать.
Качество и стандарты пеллет — Европейский совет по пеллетам
Превосходное качество гранул необходимо для достижения постоянного и оптимального процесса нагрева.Поскольку существуют виды топлива разного качества, владельцам печей и котлов очень важно выбрать топливо правильного качества, которое лучше всего подходит для их установок. Если не адаптироваться, опрометчивый выбор может не только привести к потере эффективности, но также может нарушить процесс горения и / или усложнить обслуживание прибора. Это особенно важно для небольших котлов и печей, используемых в жилых домах, поскольку допускаемые отклонения намного ниже, чем для котлов с большей мощностью.
Более крупные промышленные котлы на пеллетах не страдают от этой проблемы и поэтому могут использовать пеллеты более низкого качества, не испытывая тех же проблем.
Поэтому ключевым моментом является умение определять гранулы хорошего качества. Лучшая гарантия — это положиться на сертификат EN plus ® . EN plus ® — это всемирная система сертификации, которая гарантирует качество гранул путем контроля над ним по всей цепочке поставок. Действительно, контролируется производитель, но также все заинтересованные стороны, входящие в цепочку поставок (например, торговцы, дистрибьюторы), что делает схему очень уникальной.
Приведенные ниже параметры являются частью технических требований, контролируемых в процессе сертификации и надзора EN plus ® :
- Содержание золы: Зола — это остаток, оставшийся после полного сгорания.Чем ниже зольность, тем чище будут гореть пеллеты и тем эффективнее будет работать ваш котел. Низкое содержание золы снижает необходимость регулярной очистки и обслуживания.
- Зола Температура плавления: Зола, имеющая низкую температуру плавления, будет иметь тенденцию плавиться в самых горячих частях камеры сгорания и затвердевать, когда покидает эти области. Эта твердая зола, называемая «шлаком», может создать несколько проблем, включая влияние на процесс горения, блокировку оборудования и увеличение затрат на техническое обслуживание.
- Длина, диаметр и насыпная плотность: Длина и диаметр являются простыми параметрами, в то время как насыпная плотность должна быть объяснена как измерение веса гранул на объем гранул (кг / м³). Важно иметь пеллеты одинаковой длины, диаметра и насыпной плотности, поскольку котлы на древесных пеллетах предназначены для использования пеллет со стандартной энергетической плотностью (т. Е. С содержанием энергии на единицу объема). Использование гранул неправильного размера повлияет на энергетическую плотность. В случае чрезмерной плотности энергии потребляемая мощность котла будет слишком высокой, что приведет к перегреву камеры сгорания, в то время как недостаточная плотность энергии повлияет на эффективность и может не произвести достаточно тепла для работы системы.
- Пыль: Мелкие частицы древесины, которые можно найти в хранилищах гранул или мешках, низкое содержание пыли является важным фактором, поскольку это может повлиять на хранение, обращение, обслуживание, эффективность сгорания и выбросы загрязняющих веществ.
- Теплотворная способность и влажность: Нижняя теплотворная способность (LHV), выраженная в кВт / кг, отражает энергосодержание гранул. Это особенно верно для измерения LHV в полученном виде (a.r.) (с учетом влажности топлива).Содержание воды отражает количество воды, содержащейся в определенном количестве гранул, и выражается в процентах. Чем ниже уровень влаги в древесных гранулах, тем выше тепловая мощность на кг. Обычный LHV a.r. обычно колеблется от 4,6 до 5,1 кВтч / кг.
- Механическая износостойкость: Этот параметр отражает устойчивость гранул к ударам. Высокая механическая прочность означает, что гранулы менее склонны к разрушению и крошению во время транспортировки и в шнеках для подачи топлива, что позволяет сохранить консистенцию гранул и уменьшить количество пыли.
- Содержание азота, серы и хлора : Эти параметры, выраженные в процентах от общего веса пеллет, влияют на выбросы загрязняющих веществ и коррозию нагревательных приборов.