Обжиговые печи. Барабанные печи. Печи для прокалки
Назначение барабанной печи
Назначение данной вращающейся обжиговой печи – нагревание подаваемого материала до максимальной температуры 950 °C. Конструкция оборудования основана на изложенных ниже условиях процесса, протекающего во вращающейся обжиговой печи.
Материал нагревается в следующих режимах теплопередачи, перечисленных в порядке возрастания их значимости:
1. Теплота излучения.
2. Теплота от прямого контакта с внутренней поверхностью барабана.
Необходимое количество тепла определяется с учетом следующих требований:
1. Тепло для увеличения температуры твердых компонентов.
2. Тепло для нагрева влажного подаваемого материала до температуры испарения.
3. Тепло для выпаривания влажного подаваемого материала.
4. Тепло для увеличения температуры струи воздуха.
Описание процесса работы барабанной печи
Влажный кек (UO
Полностью прореагировавший желтый урановый кек (U3O8) подается в охлаждающую секцию барабана. Тепло отводится от твердых компонентов, за счет высокой теплопроводности, через стенку барабана обжиговой печи и удаляется с охлаждающей водой, разбрызгиваемой на внешнюю часть барабана. Температура материала уменьшается приблизительно до 60 °C, затем материал подается в разгрузочный трубопровод, через который под действием силы тяжести попадает в транспортную систему. Через разгрузочный трубопровод во вращающуюся обжиговую печь подается мощный поток воздуха, проходящий через барабан навстречу потоку материала, чтобы удалить водяной пар, образовавшийся на нагревательной стадии процесса. Влажный воздух отводится из загрузочного трубопровода при помощи вентиляции.
Компоненты обжиговой барабанной печи
Барабан вращающейся обжиговой печи
Сварные секции барабана имеют швы, располагающиеся попеременно под углами 90° и 180° один к другому и полученные сваркой с полным проплавлением основного металла. Бандажи и зубчатые венцы смонтированы на механически обработанных поверхностях, отделенных от барабана распорными элементами, чтобы учесть различия в радиальном тепловом расширении. Конструкция барабана учитывает любые тепловые и механические нагрузки и поэтому обеспечивает надежную работу. На загрузочной стороне барабана расположены удерживающие материал накладки, преграждающие обратный поток материала в трубопровод и винтовые пластины для подачи материала в нагретые секции.
Бандаж
Барабан имеет два бандажа без сварных швов и стыков из кованой стали. Каждый бандаж имеет цельную прямоугольную секцию и упрочнен для увеличения срока службы.
Опорные колеса
Барабан печи вращается на четырех опорных колесах изготовленных из кованой стали. Опорные колеса упрочнены для увеличения срока службы. Колеса установлены с натягом на высокопрочный вал, установленный между двумя подшипниковыми опорами, имеющими срок службы не менее 60000 часов. Основание колес оснащено нажимными винтами для горизонтального выравнивания и регулировки колес.
Упорные ролики
Установка содержит два упорных ролика, состоящих из двух стальных колес с уплотненными сферическими роликоподшипниками, срок службы которых составляет не менее 60000 часов. Упорные ролики упрочнены для увеличения их срока службы.
Узел привода
Барабан рассчитан на вращение с частотой 1-5 об/мин при мощности 1,5 кВт от электродвигателя с частотой вращения 1425 об/мин, работающего от трехфазной сети переменного тока напряжением 380 В, частотой 50 Гц и выполненного в герметичном исполнении с воздушным охлаждением. Вал электродвигателя напрямую соединен с входным валом главного редуктора через гибкую муфту.
Циклоидный главный редуктор имеет точное понижающее передаточное отношение 71:1 с одной ступенью понижения. Низкоскоростной вал редуктора рассчитан на необходимый момент и предельные нагрузки.
Предотвращение деформации барабана обжиговой печи
Для предотвращения деформации барабана печи, во время сбоев в системе энергоснабжения электродвигателя, предусмотрен дополнительный дизельный двигатель для продолжения вращения барабана. Дизельный двигатель имеет регулируемую частоту вращения (1500-3000 об/мин) и номинальную мощность на выходе 1,5 – 3,8 кВт. Дизельный двигатель запускается вручную или электрическим стартером постоянного тока и напрямую соединен с валом электрического двигателя через муфту.
Барабанная обжиговая печь»>
Зубчатый венец
Зубчатый венец выполнен из углеродистой стали. Каждая звездочка имеет 96 закаленных зубьев, смонтирована на барабане и имеет разъемы для упрощения демонтажа.
Приводная шестерня
Изготовлена из углеродистой стали. Каждая шестерня имеет 14 закаленных зубьев и установлена на низкоскоростном валу редуктора.
Приводная цепь
Применяется цепь с наклоном для обеспечения вращения барабана обжиговой печи.
Система обжиговой печи
Кожух печи охватывает барабан и изготовлен из углеродистой стали. Стены и пол кожухов выполнены как одна полная секция. Крыша печи состоит из трех секций, по одной на каждую зону нагрева, и может быть снята с целью технического обслуживания печи или барабана.
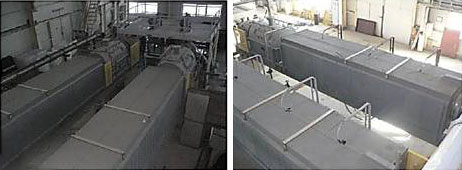
Характеристики камеры/нагревательных элементов:
Форсуночный водоохладитель
Форсуночный водоохладитель — уменьшает температуру продукта печи. Корпус охладителя изготовлен из углеродистой стали с внутренними поверхностями, покрытыми эпоксидной смолой (для уменьшения действия коррозии). Корпус оборудован двумя смонтированными в верхней части трубопроводами, имеющими распылительные сопла, впускные и выпускные вращающиеся лабиринтные уплотнения, верхнее сопло для выпуска пара, нижнее дренажное сопло, боковое перепускное сопло, дверцы для доступа и смотровые отверстия. Вода подается в распылительные сопла по трубопроводу, а выпуск осуществляется под действием силы тяжести через нижний дренажный фланец.
Трубопроводы обжиговой печи
Загрузочный трубопровод выполнен из стали нержавеющей стали. Комплектация: монтажная крышка, смотровое отверстие, качающееся сопло для выпуска газа, дверца для выпуска обратных утечек через барабан и узел вращающегося уплотнения.
Разгрузочный трубопровод выполнен из нержавеющей стали. Комплектация: желоб для разгрузки продукта, монтажную крышку, смотровое отверстие и узел вращающегося уплотнения. Разгрузочное уплотнение – температурный компенсатор сильфонного типа.
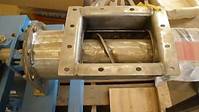
Винтовой питатель
Обжиговая печь оборудована загрузочным винтовым конвейером для подачи в барабан кека пероксида урана, представляет собой шнек, расположенный под нулевым углом к горизонтали, подвергшийся чистовой обработке.
Термопары обжиговой печи
Предусмотрены термопары для непрерывного контроля температуры в зонах печи и температур выгружаемого продукта.
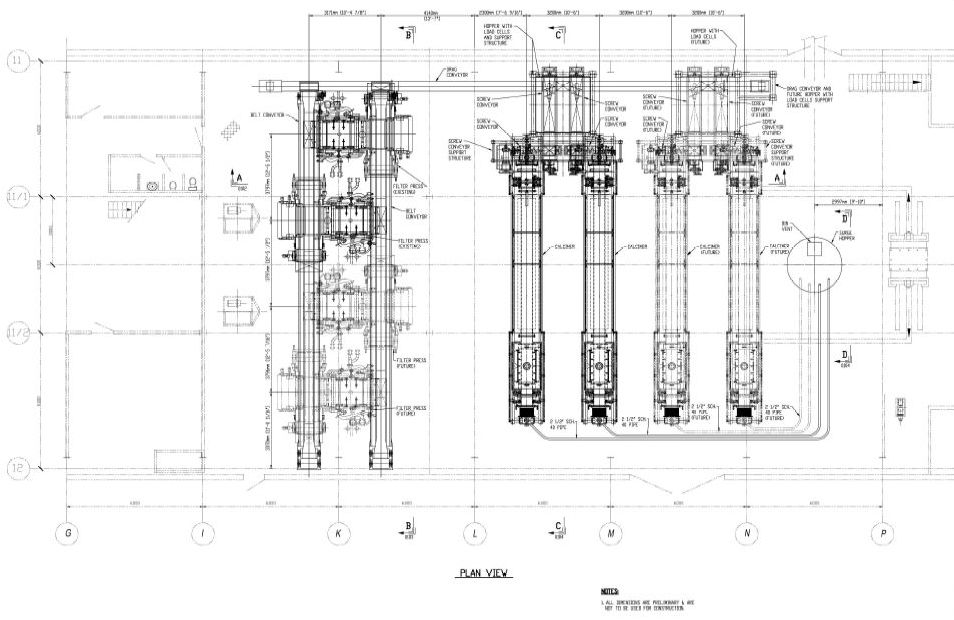
Выключатели по нулевой частоте вращения
Обжиговая печь поставляется с двумя выключателями по нулевой частоте вращения, один из которых непрерывно контролирует вращение барабана, другой – вращение загрузочной винтовой линии. Узлы выключателей по частоте вращения смонтированы на концах валов и имеют тип дисковых генераторов импульсов, создающих переменное магнитное поле, регистрируемое измерительным устройством.
Обжиг — Википедия
Материал из Википедии — свободной энциклопедии
О́бжиг — тепловая обработка материалов или изделий с целью изменения (стабилизации) их фазового и химического состава и / или повышения прочности и кажущейся плотности, снижения пористости.
Обжиг руды или рудных концентратов — операция подготовки рудных материалов к последующему переделу (обогащению, окускованию, плавке), осуществляемая в целях изменения их физических свойств и химического состава, перевода полезных компонентов в извлекаемую форму, удаления примесей. Заключается в нагреве до определённой температуры, зависящей от обжигаемого материала и целей обжига.
Чёрная металлургия[править | править код]
В чёрной металлургии используется магнетизирующий (обычно восстановительный) обжиг железной руды, назначение которого — перевод окислов железа в магнитную форму для дальнейшего обогащения. Производится в трубчатых (вращающихся) или шахтных печах, в печах кипящего слоя. Окислительный обжиг служит для удаления из руд углекислоты, карбонатов, гидратной влаги, серы. Обжиг железных руд имеет ограниченное промышленное применение
Также в чёрной металлургии обжиг используется для термической обработки сырых окатышей для их упрочнения[2].
Цветная металлургия[править | править код]
В цветной металлургии различают дистилляционный, окислительный, окислительно-восстановительный, кальцинирующий, сульфатизирующий, хлорирующий обжиги, иногда с применением активных добавок; цели этих видов обжигов — отгонка полезных компонентов в виде парообразных продуктов, перевод их в окисную форму, удаление углекислоты карбонатов, окисление сульфидов до сульфатов, образование легко растворимых или летучих хлоридов и т. п. Для обжига руд цветных металлов используются печи разнообразных конструкций — подовые, трубчатые, печи кипящего слоя и др.
Обжиг строительных и вяжущих материалов[править | править код]
Обжигу подвергают также сырьё, идущее на производство строительных или вяжущих материалов (например, огнеупорной глины, известняка, цементной шихты), огнеупорный кирпич (шамотный, магнезитовый и др.), фарфоровые и фаянсовые изделия, эмали и краски на посуде и т. д.
Степень обжига определяют, например, с помощью конусов Зегера.
- Вегман Е. Ф., Жеребин Б. Н., Похвиснев и др. Металлургия чугуна: Учебник для вузов / под ред. Ю. С. Юсфина. — З-е издание, переработанное и дополненное. — М.: ИКЦ «Академкнига», 2004. — 774 с. — 2000 экз. — ISBN 5-94628-120-8.
- Шумаков Н. С., Дмитриев А. Н., Гараева О. Г. Сырые материалы и топливо доменной плавки. — Екатеринбург: Институт металлургии УрО РАН, 2007. — 392 с. — ISBN 5-7691-1833-4.
ОБЖИГОВАЯ ПЕЧЬ — это… Что такое ОБЖИГОВАЯ ПЕЧЬ?
- ОБЖИГОВАЯ ПЕЧЬ
печь для обжига разл. материалов. О. п. с рабочей темп-рой 700 — 1300 °С для обжига огнеупорной глины, известняка, магнезита, доломита, цем. шихты, металлич. руд по конструкции бывают шахтными, многоподовыми, трубчатыми, вращающимися. В отд. случаях обжиг осуществляют в О. п. с кипящим слоем. Высокотемпературные (1000 °С и выше) О. п. для обжига огнеупорного кирпича, фарфоровых и фаянсовых изделий, эмали и красок на посуде, деталях машин и аппаратов по конструкции бывают камерными, кольцевыми, туннельными, конвейерными и т. д.
Большой энциклопедический политехнический словарь. 2004.
Смотреть что такое «ОБЖИГОВАЯ ПЕЧЬ» в других словарях:
ОБЖИГОВАЯ ПЕЧЬ — ОБЖИГОВАЯ ПЕЧЬ, в гончарном производстве печь для сушки и обжига изделий. Ранее роль таких печей выполняли ямы, куда ставили изделия и затем разводили огонь. Позже гончарные изделия стали обжигать в специальных печах духовках, которые топили… … Научно-технический энциклопедический словарь
обжиговая печь — — [А.С.Гольдберг. Англо русский энергетический словарь. 2006 г.] Тематики энергетика в целом EN calcinatorcalciner … Справочник технического переводчика
обжиговая печь — [kiln; roasting furnace] печь для обжига руд и рудных концентратов, огнеупоров, сырья для вяжущих материалов и др. Обжиговые печь отличаются большим многообразием конструкции, принципами теплогенерации и технологии, параметрами в зависимости от… … Энциклопедический словарь по металлургии
обжиговая печь для связывания радиоактивных отходов — — [А.С.Гольдберг. Англо русский энергетический словарь. 2006 г.] Тематики энергетика в целом EN radwaste calciner … Справочник технического переводчика
печь взвешенного слоя — [flash furnace] обжиговая или плавильная печь теплогенератор с массообменным автогенным режимом тепловой работы, в которой обрабатываемый измельченный («зернистый») материал находится во взвешенном (псевдогазовом) состоянии в потоке движущегося… … Энциклопедический словарь по металлургии
печь «кипящего слоя» — [fluidized bed furnace]: 1. Обжиговая печь теплогенератор с массообменным автогенным режимом тепловой работы, в которой обрабатываемый измельченный (зернистый) материал находится в псевдосжиженном состоянии («кипящем слое») в потоке движущегося… … Энциклопедический словарь по металлургии
печь электрошлакового переплава — [electroslag remelting furnace, ESR furnace] печь сопротивления косвенного действия с жидким теплоносителем в виде расплавленного синтетического шлака, рафинирующего переплавланный металл; применяется в спецэлектрометаллургии, в машиностроении… … Энциклопедический словарь по металлургии
печь-теплообменник — [heat exchange furnace] печь, в которой теплота получается из других видов энергии в зоне генерации теплоты и передается теплообменом в зону технологического процесса. Смотри также: Печь электронно лучевая печь электродоменная печь … Энциклопедический словарь по металлургии
печь-теплогенератор — [heat generation furnace] печь, в которой теплота генерируется непосредственно в зоне технологического процесса за счет введения в нее топлива или электрической энергии либо за счет химической энергии обрабатываемых материалов. Смотри также: Печь … Энциклопедический словарь по металлургии
печь с шагающим подом — [walking hearth furnace] проходная печь теплообменник непрерывного действия, в которой нагреваемые заготовки транспортируются вдоль рабочего пространства, периодически перекладывая их подвижными продольными элементами пода шагающими балками (ШБ) … Энциклопедический словарь по металлургии
обжиговая печь — это… Что такое обжиговая печь?
- roasting furnace
- reheating furnace
Смотреть что такое «обжиговая печь» в других словарях:
ОБЖИГОВАЯ ПЕЧЬ — ОБЖИГОВАЯ ПЕЧЬ, в гончарном производстве печь для сушки и обжига изделий. Ранее роль таких печей выполняли ямы, куда ставили изделия и затем разводили огонь. Позже гончарные изделия стали обжигать в специальных печах духовках, которые топили… … Научно-технический энциклопедический словарь
обжиговая печь — — [А.С.Гольдберг. Англо русский энергетический словарь. 2006 г.] Тематики энергетика в целом EN calcinatorcalciner … Справочник технического переводчика
ОБЖИГОВАЯ ПЕЧЬ — печь для обжига разл. материалов. О. п. с рабочей темп рой 700 1300 °С для обжига огнеупорной глины, известняка, магнезита, доломита, цем. шихты, металлич. руд по конструкции бывают шахтными, многоподовыми, трубчатыми, вращающимися. В отд.… … Большой энциклопедический политехнический словарь
обжиговая печь для связывания радиоактивных отходов — — [А.С.Гольдберг. Англо русский энергетический словарь. 2006 г.] Тематики энергетика в целом EN radwaste calciner … Справочник технического переводчика
печь взвешенного слоя — [flash furnace] обжиговая или плавильная печь теплогенератор с массообменным автогенным режимом тепловой работы, в которой обрабатываемый измельченный («зернистый») материал находится во взвешенном (псевдогазовом) состоянии в потоке движущегося… … Энциклопедический словарь по металлургии
печь «кипящего слоя» — [fluidized bed furnace]: 1. Обжиговая печь теплогенератор с массообменным автогенным режимом тепловой работы, в которой обрабатываемый измельченный (зернистый) материал находится в псевдосжиженном состоянии («кипящем слое») в потоке движущегося… … Энциклопедический словарь по металлургии
печь электрошлакового переплава — [electroslag remelting furnace, ESR furnace] печь сопротивления косвенного действия с жидким теплоносителем в виде расплавленного синтетического шлака, рафинирующего переплавланный металл; применяется в спецэлектрометаллургии, в машиностроении… … Энциклопедический словарь по металлургии
печь-теплообменник — [heat exchange furnace] печь, в которой теплота получается из других видов энергии в зоне генерации теплоты и передается теплообменом в зону технологического процесса. Смотри также: Печь электронно лучевая печь электродоменная печь … Энциклопедический словарь по металлургии
печь-теплогенератор — [heat generation furnace] печь, в которой теплота генерируется непосредственно в зоне технологического процесса за счет введения в нее топлива или электрической энергии либо за счет химической энергии обрабатываемых материалов. Смотри также: Печь … Энциклопедический словарь по металлургии
печь с шагающим подом — [walking hearth furnace] проходная печь теплообменник непрерывного действия, в которой нагреваемые заготовки транспортируются вдоль рабочего пространства, периодически перекладывая их подвижными продольными элементами пода шагающими балками (ШБ) … Энциклопедический словарь по металлургии
Обжиг извести. Известковые печи. Регенеративные печи для обжига извести
Баланс материалов
Параметры для расчета баланса известняка / извести:
Последовательность технологическоого процесса
1. Процесс поставки и хранения сырья
Известняк и доломит с надлежащими размерами частиц доставляются автомобилем на склад сырья, где укладываются на различных участках, или выгружаются из вагона в бункер разгрузки вагонов для последующей обработки в печи. Известняк и доломит выгружаются в приемный бункер вилочным погрузчиком через вибрационный питатель с пылеуловителем и ленточный транспортер в башню грохота для просеивания, после чего материал с сита выгружается в силос для хранения, расположенный перед печью. Материал, находящийся под ситом, переносится в силос для хранения щебня, после чего погружается грузовой автомобиль через электрогидравлический затвор челюстного типа; известняк, находящийся в силосе материала, расположенном перед печью, взвешивается электронным весовым бункером-дозатором, загружается в корпус печи одноковшовым подъемником; реверсивный ленточный транспортер будет подавать известняк во вращающиеся бункера, расположенные в верхней части двух камер печи для загрузки; после падения известняка в корпус печи будут сжигаться кокс/уголь до достижения температуры в 1150 °C для обжига извести; выдача готового продукта осуществляются из отверстия для выгрузки обожженной извести, находящегося в нижней части печи, в бункер для хранения извести.
1 – весовой бункер-дозатор перед печью для обжига; 2 – подвозящее транспортное средство; 3 –верхний весовой бункер-дозатор печи; 4 – верхний вибрационный питатель печи; 5 – реверсивный ленточный транспортер; 6 – вращательный бункер; 7 – затвор, перекрывающий камеру печи; 8 –измеритель уровня материала; 9 – пики розжига горелок; 10 – устройство выгрузки извести; 11 –затвор устройства выдачи; 12 – нижний вибрационный питатель печи; 13 – вентилятор воздуха для поддержания горения; 14 – резервный вентилятор для воздуха поддержания горения/охлаждения извести; 15 – вентилятор для охлаждения извести; 16 – вентилятор для охлаждения пики розжига горелки; 17 – газовый компрессор; 18 – система удаления пыли из корпуса печи;
Описание блок-схемы процесса:
Двухшахтная прямоточная регенеративная печь для обжига извести с является современным оборудованием для обжига извести с двумя вертикальными шахтами, соединенными между собой через канал в нижней части корпуса печи. Процесс обжига в двухшахтной печи имеет две
составляющие: параллельный поток и регенерация тепла. Так называемый параллельный поток означает, что известняк и продукты сгорания параллельно перемещаются вниз при обжиге известняка, что благоприятствует получению высококачественной активной извести. Так
называемая регенерация тепла означает, что высокотемпературный топочный газ, производимый в Камере обжига A, проходит через поперечный канал в камеру B. Высокотемпературный топочный газ в Камере B течет вверх для подогрева известняка до высокой температуры в зоне подогрева. Данный процесс эквивалентен регенерации тепла топочного газа в зоне подогрева Камеры B. После охлаждения топочного газа до очень низкой температуры в Камере B, он выпускается наружу. Данный принцип работы позволяет полностью использовать отходящее тепло топочного газа и обеспечивает высокую полезную теплоотдачу печи. Обжиг и регенерации тепла двух шахтной печи являются чередующимися процессами. Одна камера осуществляет обжиг, вторая – регенерацию тепла; через 12 минут они меняются своими функциями.
1. Процесс выгрузки и хранения готового продукта
Известь и легкий обожженный доломит, выгружаемые из печи, перемещаются по термостойкому ленточному транспортеру и гусеничному подъемнику на вибрационное сито, расположенное в верхней части склада готовой продукции, для просеивания. Материал, находящийся на сите,выгружается ленточным транспортером по отдельности в силосы хранения извести и легкого доломита, после чего перемещается ленточным транспортером на поверхность из стальной ленты;материал, находящийся под ситом, перемещается к дробилке, и далее на склад. В случае если количество отходов, недообожженного материала или спеченной извести невелико, известь может выгружаться непосредственно в промежуточный бункер хранения, не проходя через сито. При необходимости, она подается в яму для подземного хранения материала, расположенную перед складом готовой продукции, при этом известь просеивается, проходя через вибрационный питатель, ковшовый подъемник и подъемник гусеничного типа на склад готовой продукции.
Известь, подаваемая на дробилку, измельчается дробилкой и перемещается цепным транспортером, ковшовым подъемником с пластинчатой цепью на верхнее вибрационное сито склада спеченной извести для просеивания; при этом материал, находящийся на сите,возвращается в силос, питающий дробилку, по ленточному транспортеру; материал, находящийся под ситом, переносится в хранилище спеченной извести, а затем – на установку спекания пневматической транспортной системой.
2. Технологическая схема процесса и установка параметров оборудования
2.1. Система загрузки и хранения сырья
1) яма для подземного хранения сырья и установка для просеивания сырья Известняк переносится из склада сырья в приемный силос; может рассматриваться выгрузка сырья из самосвала непосредственно в приемный силос или транспортировка с использованием вилочного автопогрузчика. Для обеспечения равномерного обжига активной извести, технология требует, чтобы размеры частиц составляли 20 ~ 40 мм, а также требует просеивания перед подачей в печь.
Используются следующие основные модели оборудования:
Подающий ленточный транспортер 1: DTII (A) -650, производительность по транспортировке
100 т/ч, мощность электродвигателя: 22 кВт;
Вибрационное сито, производительность: 100 т/ч, мощность: 2×7,5 кВт
Далее материал подается в бункер хранения, расположенный перед печью, по транспортерной ленте, а материал, находящийся под ситом, подается в силос дробленого известняка через лоток,после чего регулярно увозится грузовым автомобилем.
2) Силос для материала перед печью
Перед печью находится силос для материала, предназначенный для хранения определенного количества просеянного высококачественного известняка, чтобы процесс подготовки не оказывал влияния на подачу сырья при возникновении каких-либо проблем с просеивающей установкой.
Количество сырья в силосе, расположенном перед печью, обеспечивает производство в течение 8 часов. Под силосом имеется система вибрационных питателей. Когда система управления на основе программируемого-логического контроллера (ПЛК) посылает команду на подачу материала, вибрационный питатель начинает подавать материал в ковш для взвешивания сырья, расположенный перед печью.
Используются следующие основные модели оборудования:
Вибрационный питатель: GZG633, производительность: 110 т/ч, мощность электродвигателя 0,55 кВт * 2
3) весовой бункер-дозатор перед печью.
Весовой бункер-дозатор перед печью для обжига извести предназначен для подачи требуемого количества известняка в печь. Весовой бункер-дозатор устанавливает датчик взвешивания, объем составляет 3,5 м3.
Подача требуемого количества материала контролируется посредством человеко-машинного интерфейса системы управления. Под весовым бункером-дозатором располагаются затвор с гидравлическим приводом, при этом гидравлический клапан, управляющий данным затвором, открывается после получения сигнала, программируемого логического контроллера для подачи в поддающую тележку.
Система выгрузки и хранения готового продукта
Конфигурация этой системы будет выполнена отдельно в соответствии с фактическим
производством.
Система подачи и обжига материала в печи
Система подачи
Система управления подачей материала: материал надлежащего качества попадает в весовой бункер-дозатор из силоса для хранения материала, расположенного перед печью, а затем в подающую тележку и подается на верхнюю часть печи через по скиповому мосту, после чего поступает в приемный бункер и в два вращающихся бункера с помощью
реверсивного ленточного конвейера, и, далее, поступает в две камеры печи обжига.
2. Оборудование системы подачи материала Состоит из тележки для материала, скипового подъемника, бункера материала в верхней
части печи обжига, реверсивного ленточного конвейера и устройства определения уровня материала.
A. Тележка материала емкостью 5 т Суточная потребность в известняке: 400 * 1,75=712 т и
количество операций подачи в сутки: ~300 раз
Цикл подачи: 4,5 мин
Положение: кодовый датчик положения + бесконтактный переключатель
B. Скиповый подъемник
Номинальная нагрузка: 100Т
Средняя скорость троса: 0 ~ 0,75 м/с
Диаметр барабана * ширина: 650 x 950 мм
Высота подъема: Около 55 м
Характеристика троса: Ø 28 мм
Мощность электродвигателя 90 кВт/380 В (система регулирования с переменным
напряжением и переменной частотой переменного тока),
Диапазон частоты вращения: 0 ~ 1450 об/мин,
Коэффициент использования: 85 %,
Количество тормозов: 2.
C. Определение уровня материала
Молотковый уровнемер материала, расположенный в верхней части обжиговой печи, сравнивает уровень материала известняка, измеренный уровнемером, с теоретическим уровнем материала. Когда измеренный уровень материала оказывается выше теоретического уровня, он будет подавать команду на разгрузку на ПЛК, после чего ПЛК дает команду для управления возвратно-поступательным движением каретки машины выгрузки материала.
Система теплотехнического обжига
Эта часть состоит, главным образом, из корпуса печи для обжига извести и вспомогательного периферийного оборудования. Детали данного оборудования и параметры процесса необходимо рассмотреть подробно.
Система теплотехнического обжига
3.1. Конструкция корпуса печи
Для кожуха печи используются сварные стальные плиты толщиной 12-20 мм для обеспечения прочности стальной конструкции печи и надежного уплотнения. На месте поперечной сварки она усилена кругом арматурного хомута толщиной 16 мм. В то же время устанавливаются вертикальные полосы толщиной 10-12 мм на наружной поверхности стальных плит, при этом средняя часть окружена стальной плитой толщиной 1 мм.
В соответствии с оборудованием и функцией каждой части системы, по высоте печи имеется девять платформ:
Первая платформа, оборудованная, главным образом, разгрузочным клапаном.
Вторая платформа (бетонная), оборудованная, главным образом, разгрузочным ,гидравлическим цилиндром;
Третья платформа, оборудованная, главным образом, пневмопушкой для продувки и удаления пыли из канала;
Четвертая платформа, имеющая, главным образом, 36 шуровочных отверстий и запальную ,горелку;
Пятая платформа, оборудованная, главным образом, реверсивным газовым клапаном.
Шестая платформа, оборудованная, главным образом, пиками розжига горелок и трубами перед газовым соплом;
Седьмая платформа, оборудованная, главным образом, вращательным бункером,гидроцилиндром для закрытия камеры печи, уровнемером материала и клапаном ,отработавшего газа / реверсивным газовым клапаном;
Восьмая платформа, оборудованная, главным образом, реверсивным ленточным транспортером и вибрационным питателем, расположенным в верхней части печи;
Девятая платформа, оборудованная, главным образом, силосом материала в верхней части печи и реверсивными клапаном печной трубы / удаления пыли;
Футеровка печи
Используемые огнеупорные материалы должны иметь устойчивость к высоким температурам, механическому трению, химической эрозии и продувке восходящими потоками воздуха, а также выполнять функцию изоляции.
Во внутренней кирпичной кладке корпуса печи используется различный огнеупорный ,материал в соответствии с различными характеристиками и рабочей температурой каждой рабочей зоны. Это, главным образом, кирпичи из шпинели на основе оксидов магния и ,алюминия, кирпичи из оксида магния, кирпичи с высоким содержанием алюминия, кирпичи из высокопрочной глины, керамическое волокно, теплоизоляционные плиты, литые огнеупоры и огнеупорная масса. Нормальный срок службы корпуса печи превышает 5 лет. Внутренний слой футеровки является рабочим слоем, его материалом являются высокопрочные огнеупорные кирпичи; наружный слой представляет собой теплоизолирующий слой, состоящий, главным образом, из легкого изоляционного материала.
Таблица 3.1 Типы и толщина огнеупорного материала каждого слоя
Оборудование корпуса печи
Загрузочное оборудование
Метод загрузки для печи для обжига извести: обычная чередующаяся загрузка сырья в две камеры печи. Поэтому для двухшахтной печи устанавливается один комплект загрузочного оборудования, располагаемого в его верхней части, включая один приемный бункер, один реверсивный ленточный транспортер для подачи в верхнюю часть печи, два вращательных бункера и два гидроцилиндра для открытия камер печи.
Объем бункера в верхней части печи составляет около 4 м3 , при этом известняк подается в корпус печи обычным образом согласно командам от ПЛК. Сначала камера печи открывается посредством соответствующего гидравлического цилиндра, затем опускается вращающийся бункер; далее открывается загрузочный конус и известняк падает в камеру печи. Процесс закрытия происходит в обратном порядке. Вышеописанные действия оборудования управляются ПЛК.
Загрузочное оборудование имеет гидропривод. Использование гидропривода рассматривается, главным образом, в двух аспектах: способность выдерживать высокие нагрузки и стабильность действия.
3.3.2. Оборудование для разгрузки материала
У днища печи установлена разгрузочная машина с возвратно-поступательным движением каретки, которая может обеспечить полную и равномерную выдачу готовой извести, а также плавно регулировать количество выгружаемого материала. Под разгрузочной машиной находятся два силоса для хранения извести, при этом разгрузка производится в промежуточный силос материала через разгрузочный клапан. Под промежуточным силосом материала располагается механизированное устройство вибрационной подачи, которое выгружает известь на ленточный конвейер, располагающийся под печью для обжига извести.
Система вдувания пылеугольного топлива ПУТ (Опция)
3.4.1. Обзор системы
От мельницы до угольного бункера
a. Угольная пыль надлежащего качества переносится по трубе в угольный бункер емкостью в 50 м3.
b. Крышка бункера оборудована термопарой, и установленным в трубопроводе устройством для контроля концентрации CO, предоставляющими информацию о ситуации внутри угольного бункера; как только концентрация CO или температура крыши бункера превышают установленные значения, это означает начало горения угля, что требует принятия соответствующих мер для обеспечения безопасности системы.
c. Угольный бункер является герметичным, при подаче угля срабатывает вентиляционное устройство в верхней части бункера для уравновешивания давления в бункере. d. Вентиляционное устройство состоит из малых устройств разгрузки пылесборников и малых воздуходувок, уменьшающих содержание угольной пыли в выпускаемом газе. В нижней части угольного бункера находится устройство для пылеугольного вдувания и поплавковым устройством, которое соединено с трубой для подачи сжатого воздуха с целью приведения угольной пыли в псевдоожиженное состояние.
От резервуара для подачи угля до шахт ПТР
a. Нижняя часть бункера угольной пыли емкостью в 50 м3 соединяется с нижним весовым бункером-дозатором угольной пыли через гидравлический затвор и ручной затвор.
b. В верхней части весового бункера-дозатора расположен прибор для измерения давления, который присоединен одной трубой к верхней части хранилища угольной пыли емкостью в 50 м3 для уравновешивания давления в двух бункерах.
c. В нижней части весового бункера-дозатора также имеются продувочное и поплавковое устройство. Днище весового бункера-дозатора разделено на две дорожки, обозначенные буквами A и B, соответственно, ведущие через дозирующий шнек в соответствующий трубопровод угля.
d. Воздуходувка Рутса, обеспечивает воздух для переноса угля. A1 и B1 разделяются на 16 дорожек по отдельности, A2 и B2 разделяются на 17 дорожек (всего 33 дорожки на каждую шахту) через распределитель угольной пыли.
e. От распределителя угольной пыли до труб форсунок устанавливаются прокладки из устойчивой к износу резины, удобные для установки и технического обслуживания. Усилие продувки после подачи угольной пыли к форсункам обеспечивается тремя воздуходувками Рутса (две работают, одна – в резерве).
Основное оборудование
1) Бункер угольной пыли: Готовая угольная пыль подается в силос угольной пыли через продувочный резервуар.
Емкость хранения угольной пыли составляет 50 м3 , что соответствует массе в 15 тонн.
Корпус бункера угольной пыли оборудован индикаторами высокого и низкого уровня материала, и уголь автоматически добавляется, когда уровень угольной пыли становится ниже установленного значения, и добавление угля прекращается по достижении высокого уровня материала. Кроме того, в бункере угольной пыли предусмотрены точки для контроля температуры и давления. В случае превышения установленных значений
система автоматически приводит в действие азотную защиту. Кроме того, при использовании бункера угольной пыли для сброса давления, сжатый газ должен выпускаться, и должен быть предусмотрен рукавный пылесборник. В нижней части установлены устройство для псевдоожижения, прямоточный шарнирный клапан и мягкое соединение с конусным насосом. Для поддержания баланса давления в бункере угольной пыли, в верхней части каждого бункера угольной пыли устанавливается пылесборник.
Когда угольная пыль переносится в бункер, сначала запускается пылеуловитель, и переносимый газ выпускается из бункера с течением времени для исключения утечки угольной пыли.
Для обеспечения безопасности на верху каждого бункера угольной пыли устанавливается взрывозащитный клапан. Бункер измельченного угля оборудован датчиками температуры и давления, которые используются, главным образом, для определения его рабочего состояния. Когда температура оказывается крайне высокой, и может произойти возгорание, немедленно приводится в действие устройство азотной продувки для обеспечения безопасного функционирования бункера угольной пыли.
(2) Камера-питатель для дозировки и вдувания угольной пыли (бункерный насос):
Камера-питатель представляет собой сосуд, работающий под давлением, который состоит из головки, корпуса барабана и вертикального корпуса. Она включает в себя взрывозащитное устройство, устройство псевдожижения и диффузор. Конусный насос должен развивать достаточное давление для обеспечения равномерной подачи угольной пыли без остановки. Взвешивающее устройство настраивается и управляется программой
автоматического управления ПЛК.
(3) Дозирующий клапан и форсунка ускорительной камеры Два дозирующих клапана типа AGR50. Скорость работы дозирующего клапана
контролироваться через центр управления с обратной связью, таким образом, чтобы обнаруживать поток угольной пыли и управлять им. Дозирующий клапан оборудован эжектором ускорительной камеры, в котором угольная пыль смешивается с воздухом, подаваемым под высоким давлением от внешней воздуходувки Рутса, а затем переносится к статическому распределителю.
Носителем является сжатый воздух, в качестве носителя используется воздуходувка Рутса, требуемое давление носителя составляет 75~150 кПа
(4) Статический распределитель:
Поскольку в данной системе вдувания угольной пыли используется система подачи содной трубой для дозирующих резервуаров, на платформе сопел горелок расположены
четыре статических дистрибьютора, одна камера печи с двумя распределителями и 16 (или 17) патрубков для каждого распределителя. Соединительная труба изготовлена из износостойкой резины, что позволяет сохранять одну и ту же эквивалентную длину.
Статический распределитель представляет собой распределитель дискового типа, обеспечивающий высокую точность распределения. Поскольку угольная пыль и среда заходят и выходят в фиксированном направлении, потери на сопротивление малы, и пыль не накапливается. Однородность каждого распределения может достигать 95 %. Кроме того, на входе трубы горелки установлен ручной регулировочный клапан, и расход одной трубы горелки может регулироваться в соответствии с состоянием печи.
(5) Воздуходувка Рутса:
Бункер угольной пыли обслуживается тремя установками двухступенчатых воздуходувок Рутса высокого давления, две из которых работают, и одна находится в резерве, модель:
ZAS125S, давление нагнетания: 120 кПа, мощность: 60 кВт, объем воздуха: 1000 м/ч при нормальных условиях (н.у.). Воздух поступает в горелку с угольной пылью и участвует в сжигании угольной пыли.
3.4.3. Контроль и автоматическое управление
При работе топливной системы устанавливается оперативный контроль, запись,сигнализация и автоматическая остановка в соответствии с температурой,давлением и расходом. Основное контроллеры включены в систему ПЛК печи для обжига извести; это касается нагрева печи и перехода функции камеры в резервный режим; данная система устанавливает автоматическое управление микрокомпьютером в соответствии со специальными требованиями, регулирование скорости преобразования частоты и безопасный выпуск топлива.
3.4.5. Меры безопасности при использовании топлива
1) Система продувки и выпуска: использовать азот для выдувания остаточного топлива из трубы при запуске и остановке печи.
2) При использовании перехода функции в резервный режим: использовать азот для выдувания остаточного топлива из трубы с целью предотвращения обратной вспышки и дефлаграции.
3) Клапан быстрой отсечки трубы коллектора топлива: предотвращает отказ электрического питания или вентиляторов, а также низкое давление воздуха и газа.
4) Для настройки платформы для обслуживания в клапане: расходомер, местное устройство повышения давления.
5) Входные и выходные трубы во вспомогательной насосной станции оборудованы двустворчатым клапаном и отсечным клапаном, а также приспособлениями для выпуска и слива.
6) Входная и выходная труба каждой вспомогательной насосной станции оборудована двустворчатым клапаном, отсечным клапаном, глушителем и сильфонным компенсатором.
7) Здание вспомогательной насосной станции оборудовано подъемными mустройствами для облегчения технического обслуживания вспомогательной насосной станции подачи газа.
Воздушная система
В двухшахтной печи используется три типа воздуха: воздух для сжигания топлива, воздух для охлаждения извести и воздух для охлаждения сопел горелок, которые подаются в камеры печи каждой из воздуходувок Рутса.
Воздух для сжигания топлива
Воздух для сжигания топлива из помещения воздуходувок разделяется на два трубопровода, ведущих к двум реверсивным клапанам воздуха для сжигания топлива / топочного воздуха по трубопроводу коллектора воздуха для сжигания топлива. Благодаря последовательному срабатыванию двух реверсивных клапанов, реализуется функция обращения воздушной продувки и выпуска топочного газа из двух камер.
Воздух для сжигания топлива при переводе в резервный режим выпускается в атмосферу через клапан для выпуска воздуха, в то же самое время воздух для сжигания топлива в камеры не подается, и давление в печи не является повышенным. При изменении производительности печи для обжига извести, требуется изменение количества воздуха для сжигания топлива, подаваемого в печь, что будет достигаться путем изменения частоты электродвигателя воздуходувки и регулирования узлов открытия вентиляторов.
Расход воздуха для сжигания топлива в двухшахтной печи с суточной производительностью в 450 т составляет в среднем 15710 м3/ч при нормальных условиях, максимальное значение достигает 17143 м3/ч. Печь оборудована тремя установками воздуходувок Рутса для подачи воздуха для сжигания топлива. Кроме того, имеется одна установка частотного регулирования скорости. Значение расхода от одной воздуходувки
составляет 110 м3 /мин, давление на выходе составляет 49 кПа, электродвигатель: Y315M36N=110кВт.
Для обеспечения полного сгорания топлива и безопасной эксплуатации коэффициент избытка воздуха принимается равным 1.1. В производстве уровень значения расхода воздуха для сжигания топлива регулируется значением расхода газа, и расход на выходе вентилятора регулируется процессом частотного регулирования скорости,который управляется автоматически. Воздух для сжигания топлива направляется к двум реверсивным клапанам воздуха для сжигания топлива / топочного газа в сквозной трубе в верхней части печи, а затем поступает в камеры печи с прямоточным реверсивным клапаном топлива в камере сгорания печи.
Воздух для охлаждения извести
Воздух для охлаждения извести из помещения воздуходувок разделяется на два трубопровода, ведущие к двум входам охлаждающего воздуха у днища печи через трубопровод коллектора воздуха для охлаждения извести. На входе предусмотрены два двустворчатых клапана для регулирования расхода воздуха, подаваемого в каждую камеру.
Воздух для охлаждения извести при переводе в резервный режим выпускается в атмосферу через клапан для выпуска воздуха, в то же самое время воздух для охлаждения извести в камеры не подается, и давление в печи не является повышенным.
При изменении производительности печи, требуется изменение количества воздуха для охлаждения извести, подаваемого в печь, что будет достигаться путем изменения частоты электродвигателя воздуходувки и регулирования узлов открытия вентиляторов.
Воздух для охлаждения извести обеспечивает охлаждение готовой извести до 80~100 °C в нижней части корпуса печи, после чего выпускается из корпуса печи. Требуемый объем охлаждающего воздуха составляет 11900 м3/ч при нормальных условиях, давление на входе: ≥25 кПа. Установка оборудована двумя воздуходувками Рутса в состоянии открытия; ее резервные воздуходувки также являются резервными воздуходувками воздуха для сжигания топлива, расход от одной воздуходувки составляет 110 м/мин, давление на выходе: 39,2 кПа, электродвигатель Y315M3-6N = 110 кВт. В процессе работы, в соответствии с температурой окружающей среды и температурой воздуха, охлаждающего известь, количество охлаждающего воздуха регулируется, и температура на выходе извести контролируется на уровне ~100 °C. Двустворчатый клапан используется для регулирования расхода воздуха, охлаждающего известь, который должен равномерно подаваться в обе камеры.
Воздух для охлаждения сопел горелок
Когда печь не работает в режиме обжига, сопла горелок не пропускают через себя газ, в то же время им требуется воздух для охлаждения, предотвращения возгорания и возникновения простоя. Воздух для охлаждения сопел горелок поставляется двумявоздуходувками Рутса с регулируемой частотой вращения. Воздух для охлаждения сопелгорелок поставляется к трубам в верхней части печи через один отдельный трубопровод охлаждающего воздуха.
Роль воздуха для охлаждения труб горелок заключается в охлаждении сопел горелокугольной пыли в камере, где не происходит сгорание, что позволяет избежать их ,выгорания при высокой температуре. Печь оборудована тремя установками воздуходувок Рутса 3 (2 используются, 1 – в резерве), максимальная производительность одной воздуходувки составляет 125 м3/мин, при этом расход каждой из воздуходувок равен70 м3/мин, давление на выходе составляет 78,4 кПа. Воздух протекает через трубу в контур потока угольной пыли в верхней части двухкамерной печи, после чего равномерно подается в распылительную форсунку для охлаждения.
Продувка подающего трубопровода
Для обеспечения безопасности после перекрытия топливной системы и перед розжигом печи для обжига извести, топливопровод необходимо продуть азотом. Система продувки состоит из системы трубопроводов азотной продувки и системы трубопроводов подачи топлива.
Общая кольцевая труба двух камер печи соединена с трубой подачи топлива и выдаетсявверх, за пределы платформы печи, а затем в атмосферу.
Когда печь для обжига извести закрыта в течение длительного времени, перед еерозжигом следует выполнить продувку для очистки топливопровода. Для продувки трубопровода необходимо открыть вручную выпускной клапан, после чего открыть продувочный клапан для продувки трубопровода. Для выяснения того, соответствует продувка требованиям или нет, можно получить пробу, используя клапан для отбора проб, при этом печь для обжига извести может быть разожжена после достижения требуемого качества продувки. Из соображений безопасности, для продувки главного трубопровода и трубопровода источника топлива используются быстроразъемные муфты; в нерабочее время трубопроводы отсоединяются для предотвращения несчастных случаев.
Система продувки сопел горелок
При переходе функции камер для обжига извести в резервный режим топливо в соплахгорелок для камеры регенерации тепла следующего цикла должно быть выпущено для беспечения безопасности. В системе используются газообразный азот, замещающий топливо в трубопроводах, трубопровод для подачи азота от заводской установки, один резервуар для хранения воздуха емкостью в 4 м3; для стабилизации давления подачи,максимальный расход воздуха от источника составляет 12 м3/мин.
Источник воздуха для КИПиА и система очистки продувкой сжатым воздухом
В источнике воздуха для КИПиА используется сжатый воздух; система, главным образом обеспечивает питание пневматического клапана. Трубопровод источника воздуха имеет ,один резервуар хранения воздуха емкостью в 3м3 для стабилизации давления подачи и приведения всех пневматических клапанов всей печи в безопасное состояние в случае внезапного прекращения подачи электрического питания. Максимальный расход воздуха от источника составляет 3м3/мин.
В источнике продувочного воздуха пневмопушки в поперечном канале и при разжигании,печи используется сжатый воздух, при этом в системе используется тот же самый резервуар для хранения азота с источником воздуха КИПиА .
Для обеспечения устойчивой работы системы используется азот для резервирования.
Система удаления пыли
Область проектирования систему удаления пыли из дымохода печи для обжига извести;cистему удаления пыли сырья, готового продукта и верхней части печи.
Параметры отходящего воздуха верхней части печи (нормальное производство).
Объем топочного газа: 124500 м3/ч при н.у.
Температура топочного газа: 150 °C~210 °C, в среднем 180°C.
Содержание пыли: 3~5 г/м3 при н.у.
В системе обеспыливания отходящего воздуха используется отрицательное давление. В пылесборнике используется рукавный фильтр с импульсной очисткой рукавов низкого давления, в качестве пылевого фильтра используется фильтр FMS, устойчивый к воздействию высоких температур. Максимальная температура топочного газа на входе пылесборника равна 180 °C; когда температура превышает 180 °C, смесительный клапан охлаждающего воздуха автоматически открывается для смешения части воздуха с целью снижения температуры топочного воздуха до допустимого уровня и для защитыфильтрующего рукава от выгорания. Пыль, собранная пылесборником, подается в бункер скребковым транспортером, после чего собирается для обработки и ежедневного вывоза автоцистерной.
Отходящий воздух очищается пылесборником, после чего выпускается через воздуходувку и дымовую трубу; при этом концентрация пыли в выпускаемом воздухе составляет <50 мг/м3 при н.у. Когда происходит разгрузка бункера пыли в автоцистерну, образуется вторичная пыль, которая захватывается через пылеотсасывающий колпак в главный трубопровод. Расход воздуха пылеотсасывающего колпака оперативно регулируется электрическим клапаном.
Сиcтема удаления пыли сырья, готовой продукции и верхней части печи
Система удаления пыли сырья и готовой продукции включает в себя: систему сырья,систему конечной продукции и систему удаления пыли из верхней части печи.
Пыль, собранная пылесборником, подается в бункер пыли скребковым транспортером,после чего собирается для обработки и ежедневного вывоза автоцистерной. Для удаления пыли при помощи пылесборника используется сухой сжатый воздух. Для очистки от пыли и подачи пыли используется централизованное управление посредством ПЛК.
Воздух, содержащий пыль, очищается пылесборником, после чего выпускается через воздуходувку и дымовую трубу; при этом концентрация пыли в выпускаемом воздухе составляет ≤30 мг/м3 при н.у. В нижней части дымовой трубы находится лоток и клапан выгрузки пыли для очистки трубы от пыли.
Гидравлическая система
Гидравлическое устройство встроено в гидравлическую станцию.
Комплект оборудования гидравлического устройства предварительно устанавливается,чистится, регулируется, далее следуют конечная установка и наладка на рабочем месте.
В гидравлической станции пульт управления гидравлическим устройством на машинной стороне выполняет следующие функции:
Выбор места работы (пульт управления на машинной стороне, центральный пункт управления).
ОБЖИГОВАЯ ПЕЧЬ — это… Что такое ОБЖИГОВАЯ ПЕЧЬ?
- ОБЖИГОВАЯ ПЕЧЬ
ОБЖИГОВАЯ ПЕЧЬ, в гончарном производстве — печь для сушки и обжига изделий. Ранее роль таких печей выполняли ямы, куда ставили изделия и затем разводили огонь. Позже гончарные изделия стали обжигать в специальных печах-духовках, которые топили дровами или углем. В настоящее время для обжига используют электричество или газ.
Научно-технический энциклопедический словарь.
Смотреть что такое «ОБЖИГОВАЯ ПЕЧЬ» в других словарях:
обжиговая печь — — [А.С.Гольдберг. Англо русский энергетический словарь. 2006 г.] Тематики энергетика в целом EN calcinatorcalciner … Справочник технического переводчика
ОБЖИГОВАЯ ПЕЧЬ — печь для обжига разл. материалов. О. п. с рабочей темп рой 700 1300 °С для обжига огнеупорной глины, известняка, магнезита, доломита, цем. шихты, металлич. руд по конструкции бывают шахтными, многоподовыми, трубчатыми, вращающимися. В отд.… … Большой энциклопедический политехнический словарь
обжиговая печь — [kiln; roasting furnace] печь для обжига руд и рудных концентратов, огнеупоров, сырья для вяжущих материалов и др. Обжиговые печь отличаются большим многообразием конструкции, принципами теплогенерации и технологии, параметрами в зависимости от… … Энциклопедический словарь по металлургии
обжиговая печь для связывания радиоактивных отходов — — [А.С.Гольдберг. Англо русский энергетический словарь. 2006 г.] Тематики энергетика в целом EN radwaste calciner … Справочник технического переводчика
печь взвешенного слоя — [flash furnace] обжиговая или плавильная печь теплогенератор с массообменным автогенным режимом тепловой работы, в которой обрабатываемый измельченный («зернистый») материал находится во взвешенном (псевдогазовом) состоянии в потоке движущегося… … Энциклопедический словарь по металлургии
печь «кипящего слоя» — [fluidized bed furnace]: 1. Обжиговая печь теплогенератор с массообменным автогенным режимом тепловой работы, в которой обрабатываемый измельченный (зернистый) материал находится в псевдосжиженном состоянии («кипящем слое») в потоке движущегося… … Энциклопедический словарь по металлургии
печь электрошлакового переплава — [electroslag remelting furnace, ESR furnace] печь сопротивления косвенного действия с жидким теплоносителем в виде расплавленного синтетического шлака, рафинирующего переплавланный металл; применяется в спецэлектрометаллургии, в машиностроении… … Энциклопедический словарь по металлургии
печь-теплообменник — [heat exchange furnace] печь, в которой теплота получается из других видов энергии в зоне генерации теплоты и передается теплообменом в зону технологического процесса. Смотри также: Печь электронно лучевая печь электродоменная печь … Энциклопедический словарь по металлургии
печь-теплогенератор — [heat generation furnace] печь, в которой теплота генерируется непосредственно в зоне технологического процесса за счет введения в нее топлива или электрической энергии либо за счет химической энергии обрабатываемых материалов. Смотри также: Печь … Энциклопедический словарь по металлургии
печь с шагающим подом — [walking hearth furnace] проходная печь теплообменник непрерывного действия, в которой нагреваемые заготовки транспортируются вдоль рабочего пространства, периодически перекладывая их подвижными продольными элементами пода шагающими балками (ШБ) … Энциклопедический словарь по металлургии
Печь для обжига кирпича | Полезное своими руками
Для сооружения печи необходимо выбрать ровную горизонтальную площадку на возвышенном месте, защищенном от грунтовых и осадочных вод.
После выравнивания и очистки выбранной площадки от растительного слоя, производят ее горизонтальную планировку и трамбовку.
Общий вид обжиговой печи представлен на рис. 6.
Это одна из самых маленьких печей и ее вместимость составляет: 700-1500 шт.
Внутренние размеры печи: ширина — 160 см, длина (в зависимости от предполагаемой загрузки) — от 132 до 208 см, высота укладки сырца колеблется от 165 до 180 см.
Высота печи планируется в соответствии с выбранной высотой укладки.
Стены печи изготавливают из кирпича-сырца и делают толщиной в один кирпич (250 мм).
Перекрытие желательно сделать на металлическом каркасе, при условии, что каждый ряд кирпичей свода будет ложиться на две стальные полосы 8×40 мм, или стержни Ø 20-24 мм, которые собираются в металлическую рамку при помощи сварки. Свод в середине должен иметь высоту над укладкой сырца не менее 30-35 см.
Топку формируют при укладке сырца в печи. Ширина топки 48-50 см, высота 38-40 см. В топке по всей длине нужно выполнить на высоте 25-30 см уступы на обеих стенках, куда потом укладывают колосниковые решетки (при использовании в качестве топлива угля).
При обжиге дровами колосниковую решетку можно не устанавливать.
Топка закрывается дверкой размерами 40×40 см. В своде делают дымовые каналы сечением 25×28 см, а если обжиг ведется малокалорийным топливом (торфом или бурым углем), тогда предусматриваются еще и отверстия сечением 25×15 см, в которые по необходимости сверху подсыпается уголь или торф. Эти отверстия должны иметь крышки.
Дымовая труба делается высотой до 5 м (из кирпича) с внутренним сечением 40×40 см или из любой огнестойкой трубы Ø 30-40 см.
Труба устанавливается рядом с печью, с задней стороны печи (можно с одной стороны использовать заднюю стенку печи), и соединяется с печью дымовым каналом сечением 40х30 см, который делается в верхней части задней стенки печи.
На середине высоты укладки в стенках печи устраивают временные смотровые отверстия 25×15 см, которые после просмотра закладывают кирпичами и замазывают глиной.
Кладку печи производят, учитывая необходимость частичной ее разборки при укладке и разборке садки.
Боковые стенки, свод, задняя стенка, труба, а также угловые части передней стенки кладут на обычном глинопесчаном растворе. Та часть передней стенки, которая будет разбираться для разделки садка, укладывается без раствора.
После заделки проема кирпичом стенка обмазывается глиной.
Садка (укладка)
Укладывать в печь можно только хорошо высушенный сырец, иначе при обжиге потребуется много топлива. Кроме того, недостаточно высохший сырец дает до 80% брака.
Главная причина брака заключается в том, что излишняя влага, превращаясь в пар, ищет выход и приводит к растрескиванию кирпича.
Укладку сырца в печь (см. рис. 7) производят так, чтобы в первых 3-4 рядах уложенного кирпича просветы между ними были (для кирпичей, расположенных непосредственно вблизи топки) 10-15 мм, а по мере удаления (от топки дальше) увеличивались до 25 мм.
Ряды можно укладывать любым способом, например, «решеткой» или «елочкой». Способы можно чередовать.
Нужно помнить главное: каждый кирпич должен быть доступен обтеканию его дымовым газам.
Расстояние между кирпичами садка и стенками печи должно быть в пределах 20-25 мм.
Обжиг
Печь начинают топить соломой, хворостом и затем дровами.
Первая стадия — сушка. Это самая ответственная стадия.
Топить следует неинтенсивно, используя низкокалорийное топливо (отходы древесины), до тех пор, пока кирпич не избавится от внутренней влаги. Наличие влаги в кирпиче определяется наличием конденсата в верхних рядах.
Просушку можно считать законченной, если опущенный на пару минут в печь железный штырь не будет запотевать. При определенном опыте, наличие влаги можно определить рукой, поместив ладонь над выходящими газами.
Процесс сушки обычно занимает до 12 часов.
После того как будет установлено, что остаточная влага удалена, огонь постепенно усиливают, доведя кирпич до темно-красного цвета (наблюдая по своду). Подогрев длится до 9 часов, затем переходят на большой огонь до выхода огня наружу.
Увеличение тепла производится только увеличением подачи топлива. Если по какой-либо причине пламя начинает выбиваться из какого-либо места, это место сразу засыпают землей.
Когда в верхней части печи появится огонь (900-950°C) — верхние ряды светло-красного цвета, а нижние — желтого, печь «ставят на остывание». Для этого топочное отверстие закладывают кирпичом и обмазывают глиной, а на верх печи насыпают сухую землю, кирпичную пыль или сухой песок слоем 10-15 см.
Температурный режим обжига характеризуется четырьмя этапами:
- Сушка: температура 20-90°С, время 10-13 часов.
- Подогрев: температура 90-600°С; время 8-10 часов.
- Обжиг: температура 600-1000°С; время 10-12 часов.
- Остывание: температура 1000-50°С; время 7-10 часов.
Контроль температуры обжига в печи производится визуально по цвету свода:
- Темно-красный, видимый в темноте — 450-500°С.
- Темно-красный — 600-650°С.
- Вишнево-красный — 700°С.
- Светло-красный — 850°С.
- Желтый — 950-1000°С.
- Белый — 1200°С — ПЕРЕЖОГ!
Раньше для получения качественного кирпича, печь выдерживали в закрытом состоянии до недели и лишь потом приступали к охлаждению. Это давало отличные результаты, так как снятие термических напряжений происходило очень медленно.
Практически же достаточно выдержать 7-10 часов.
Охлаждение печи начинают пробивкой в топке малого отверстия — величиной с куриное яйцо, через час отверстие увеличивают вдвое, еще через час — уже вчетверо. Таким образом, через 6 часов можно открыть топочную дверку и ждать полного остуживания печи.
После остуживания разбирается передняя стенка печи и производится разделка садки, начиная с верхних рядов. После разборки, сортировки и выбраковки качественный кирпич складывают штабелем плотно друг к другу.
Недообожженный складывают отдельно и в будущем применяют в неответственных конструкциях для перегородок или в верхних рядах кладки.
Визуальное определение качества кирпича. Причины брака.
Правильно обожженный кирпич — однородного оранжево-красного цвета. Он имеет правильную форму с прямыми ребрами и ровными поверхностями. При ударе металлическим молотком издает чистый звук.
Недообожженный — имеет более светлый цвет, неоднороден на изломе. При ударе издает глухой звук (причина — недостаточная температура или время обжига).
Пережженный — имеет темно-серый или сине-черный цвет, часто со следами оплавления по поверхности. При ударе издает высокий звук. Образуется при чрезмерно высокой температуре обжига.
Повреждение углов и ребер изделия — результат небрежной переноски, транспортировки или неосторожной укладки изделий в печи.
Деформация изделия — недосушенность перед укладкой в печь.
Мелкие трещины образуются при слишком быстром нагревании или охлаждении печи.
О том, как определить качество глины для изготовления сырца, читайте здесь.Крупные трещины и сквозное растрескивание изделия — результат неправильного соотношения глины и песка, плохого качества глины, нарушения режима сушки и обжига.
Черный кирпич получается из-за недостатка воздуха или из-за плохой его циркуляции в печи.
Белые пятна на готовом изделии — следствие неправильной просушки (пересушка).