Туннельная печь для обжига керамических изделий
Изобретение относится к области техники, связанной с обжигом природных материалов и изделий из них, и может быть использовано при производстве строительных керамических изделий, в частности для производства кирпичей. Туннельная печь для обжига керамических изделий включает рабочий канал с зонами предварительного нагрева, обжига и охлаждения керамических изделий. Рабочий канал ограничен боковыми стенками, основным сводом и дополнительным сводом с межсводовым пространством. Система газораспределения (вентиляции) туннельной печи включает, по крайней мере, всасывающий трубопровод, вентилятор и подающий трубопровод, при этом всасывающий трубопровод соединяет межсводовое пространство печи с вентилятором, а подающий трубопровод соединяет вентилятор с зоной охлаждения рабочего канала и/или с пространством между зоной обжига и зоной охлаждения рабочего канала. Технический результат: стабилизация качественных показателей готовой продукции при обеспечении наиболее рационального температурного режима обработки, а также снижение расхода топлива за счет использования тепла из межсводового пространства. 4 з.п. ф-лы, 1 ил.
Изобретение относится к области техники, связанной с обжигом природных материалов и изделий из них, и может быть использовано при производстве строительных керамических изделий, в частности для производства кирпичей.
Известна туннельная печь, включающая рабочий канал, разделенный на зоны сушки, обжига и охлаждения изделий, и вентиляционную систему (патент RU 2187771, 2002 г.). В печи осуществляются отбор горячих газов из рабочего канала, разбавление их атмосферным воздухом, забираемым нагнетающим вентилятором, и подача в рабочий канал печи в зоне сушки. Эти операции обеспечивают рациональный режим работы печи и обработки изделий. Однако в зоне обжига происходит сильный нагрев свода. Тепло попадает в надсводовое пространство и не утилизируется, т.е. происходит нерациональный расход тепла, образующегося в зоне обжига, а, кроме того, значительный местный перегрев свода может вызвать его прогиб или обрушение.
Известна туннельная печь, над рабочим каналом которой находятся основной и дополнительный своды с межсводовым пространством (патент RU 2091688, 1997 г.). Газообразные продукты сгорания вместе с газами, выделяющимися из обжигаемых изделий из зоны обжига, направляются в межсводовое пространство, где обезвреживаются и удаляются через отверстия в стенах зоны подогрева.
В ряде случаев на границе зон обжига и охлаждения применяют устройства, обеспечивающие достаточно быстрое охлаждение изделий воздухом из атмосферы. Однако значительный перепад температуры и влажности между горячими изделиями и атмосферным воздухом может привести к растрескиванию обожженных изделий.
Согласно изобретению, туннельная печь для обжига керамических изделий включает рабочий канал с зонами предварительного нагрева, обжига и охлаждения керамических изделий. Рабочий канал ограничен боковыми стенками, основным сводом и дополнительным сводом с межсводовым пространством. Основной и дополнительный своды выполняются в виде перекрытий. Межсводовое пространство — это пространство между перекрытиями. Система газораспределения (вентиляции) туннельной печи включает, по крайней мере, всасывающий трубопровод, вентилятор и подающий трубопровод, при этом всасывающий трубопровод соединяет межсводовое пространство печи с вентилятором, а подающий трубопровод соединяет вентилятор с зоной охлаждения рабочего канала и/или с пространством между зоной обжига и зоной охлаждения рабочего канала.
Технический результат заявленного изобретения заключается в стабилизации качественных показателей готовой продукции при обеспечении наиболее рационального температурного режима обработки, а также в снижении расхода топлива за счет использования тепла из межсводового пространства. Кроме того, подача подогретого газа из межсводового пространства в рабочий канал компенсирует потери тепла, происходящие при открытии дверей печи на входе и выходе из рабочего канала. Еще одним техническим результатом является увеличение расхода газа, проходящего по межсводовому пространству, что предотвращает чрезмерный перегрев свода и способствует увеличению срока его эксплуатации.
Трубопроводы выполняют роль каналов для движения газа — газоводов (газоходов). По форме трубопроводы могут выполняться с прямоугольным, квадратным, овальным проходным сечением. На всасывающем трубопроводе может быть предусмотрено устройство забора воздуха из окружающей атмосферы, например, в виде патрубка с заслонкой. В предпочтительном конструктивном варианте всасывающий трубопровод соединен с межсводовым пространством печи над зоной обжига рабочего канала. Возможно также соединение всасывающего трубопровода с межсводовым пространством печи над зоной нагрева или зоной охлаждения рабочего канала.
Подающий трубопровод обычно содержит коллектор-распределитель с несколькими патрубками, непосредственно выходящими в зону охлаждения рабочего канала.
Межсводовое пространство выполнено в виде одной полости без сплошных перегородок или с перегородками, содержащими отверстия.
Туннельная печь входит в состав оборудования для изготовления керамических изделий. Оборудование для изготовления керамических изделий содержит сушильную печь и печь для обжига керамических изделий. Причем, с целью увеличения расхода газа (воздуха) через межсводовое пространство, межсводовое пространство посредством трубопровода (воздуховода или газовода) и вентилятора соединено с сушильной печью.
На чертеже изображена туннельная печь для обжига керамических изделий в продольном разрезе.
Позицией 1 на чертеже обозначена зона предварительного нагрева рабочего канала, позицией 2 — зона обжига, позицией 3 — зона охлаждения. Между основным сводом 4 и дополнительным сводом 5 находится межсводовое пространство 6. Система газораспределения (вентиляции) включает всасывающий трубопровод 7, вентилятор 8, подающий трубопровод 9 и коллектор-распределитель 10 с патрубками 11, при этом всасывающий трубопровод 7 соединяет межсводовое пространство 6 печи над зоной 2 обжига с вентилятором 8, а патрубки 11 коллектора-распределителя 10 выходят непосредственно в зону 3 охлаждения вблизи зоны 2 обжига рабочего канала. Позицией 13 на чертеже обозначены горелки, расположенные в зоне 2 обжига. Система вентиляции может включать несколько вентиляторов 8 с соответствующим количеством соединительных трубопроводов. Кроме того, печь может быть снабжена вытяжной вентиляцией для сброса части газов в атмосферу, а также трубопроводами для подачи горячих газов в зону 1 предварительного нагрева керамических изделий (такие конструктивные элементы на чертеже не изображены, поскольку не относятся к предмету изобретения).
Предлагаемая туннельная печь работает следующим образом.
По рабочему каналу печи движутся обжиговые вагонетки, груженные высушенными керамическими изделиями. На чертеже вагонетки с обжигаемым материалом движутся справа налево, дымовые газы — в противоположном направлении. Подвергаемые термообработке керамические изделия проходят последовательно зоны предварительного нагрева, обжига и охлаждения, обозначенные позициями 1, 2 и 3 соответственно. Сначала изделия нагреваются в зоне 1 предварительного нагрева за счет тепла, поступающего из зоны 2 обжига, образующегося при сжигании топлива. Далее происходит собственно обжиг при максимальных температурах (зона 2). Затем изделия постепенно остывают в зоне 3 охлаждения.
При обжиге в туннельной печи изделия (в частности, кирпичи) подвергаются воздействию повышающейся температуры от 80°С до 750°С — в зоне предварительного нагрева; воздействию температуры от 750°С до 1100°С — в зоне обжига; воздействию понижающейся температуры от 1100°С до 50°С — в зоне охлаждения. Обжиг осуществляют в течение 40-55 часов.
Воздух, нагнетаемый в конце печи, проходит зону 3 охлаждения, нагревается и поступает в зону обжига, где участвует в процессе сгорания топлива, подаваемого в зону 2 обжига. Нагретый воздух также может отводиться для сушки сформованных изделий в сушильных установках. Дымовые газы от сгорания топлива направляют в зону 1 предварительного нагрева, где они используются в процессах окончательного удаления влаги, собственно нагрева и подготовки изделий к обжигу.
Тепло, образующееся от сгорания топлива, затрачивается не только на обжиг изделий, но и нагрев ограждающих конструкций печи (так называемые потери тепла), в том числе и подвесного свода. В конце зоны 1 предварительного нагрева, зоне 2 обжига и начале зоны 3 охлаждения создаются достаточно высокие температуры, влияющие на прочностные показатели поддерживающих металлических конструкций основного и дополнительного сводов. Тепло из рабочего канала за счет теплопередачи через основной свод попадает в межсводовое пространство.
Горячий воздух из межсводового пространства 6 через всасывающий трубопровод 7 отбирается вентилятором 8 и направляется по подающему трубопроводу 9 в зону 3 охлаждения рабочего канала или в пространство между зоной 2 обжига и зоной 3 охлаждения рабочего канала. Температура отбираемых из межсводового пространства 6 газов составляет 250-300°С, что явно ниже, чем температура изделий, покидающих зону обжига, но заметно превышает температуру атмосферного воздуха, также направляемого на охлаждение обожженных изделий. За счет начала охлаждения изделий воздухом с относительно высокой температурой (по сравнению с атмосферным воздухом) и постепенного понижения температуры охлаждающего воздуха по мере движения вагонеток с изделиями по зоне охлаждения к выходу рабочего канала достигается оптимальный режим остывания изделий. При этом по сравнению с процессом охлаждения только с помощью обдува атмосферным воздухом заметно уменьшается брак изделий, вызываемый резкими перепадами температур при охлаждении и неравномерным охлаждением разных участков изделий.
Когда температура газов, подаваемых в зону 3 охлаждения, оказывается слишком высокой, она может быть понижена до необходимого уровня путем смешивания горячих газов с атмосферным воздухом. Для этой цели на всасывающем трубопроводе 7 установлен патрубок 12 забора атмосферного воздуха. С целью регулирования количества отбираемого воздуха на всасывающем трубопроводе может быть установлен регулятор расхода (заслонка).
Система газораспределения обеспечивает подачу газа из межсводового пространства в рабочий канал с расходом от 0,01 м3/c до 10 м3/с. Система выполнена с возможностью регулирования расхода газа.
При этом обеспечивается стабилизация качественных показателей керамических изделий. Кроме того, обеспечивается наиболее рациональный температурный режим обработки керамических изделий, снижается расход топлива за счет использования тепла из межсводового пространства. Подача подогретого газа из межсводового пространства в рабочий канал компенсирует потери тепла, происходящие при открытии дверей печи.
1. Туннельная печь для обжига керамических изделий, включающая рабочий канал с зонами предварительного нагрева, обжига и охлаждения керамических изделий, ограниченный боковыми стенками, основным и дополнительным сводами с межсводовым пространством, и систему газораспределения (вентиляции), включающую, по крайней мере, всасывающий трубопровод, вентилятор и подающий трубопровод, при этом всасывающий трубопровод соединяет межсводовое пространство печи с вентилятором, а подающий трубопровод соединяет вентилятор с зоной охлаждения рабочего канала и/или с пространством между зоной обжига и зоной охлаждения рабочего канала.
2. Туннельная печь по п.1, отличающаяся тем, что на всасывающем трубопроводе установлено устройство забора воздуха из атмосферы.
3. Туннельная печь по п.2, отличающаяся тем, что устройство забора воздуха выполнено в виде патрубка с заслонкой.
4. Туннельная печь по п.1, отличающаяся тем, что всасывающий трубопровод соединен с межсводовым пространством печи над зоной обжига рабочего канала.
5. Туннельная печь по п.1, отличающаяся тем, что подающий трубопровод содержит коллектор-распределитель с патрубками.
Печи обжига керамических изделий — Справочник химика 21
Наиболее дорогой и ответственной операцией является обжиг. Для обжига керамических изделий применяются различные печи, но наибольшее распространение получают туннельные. [c.226]Туннельные печи непрерывного действия для обжига керамических изделий (см. рис. 36) имеют длинный канал (до 165 м), внутри которого по рельсам движутся плотно сомкнутые друг с другом вагонетки 3 с нагруженными на них изделиями. Вагонетки выложены огнеупорным кирпичом и по бокам снабжены железными щитами, которые при движении вагонеток ле- [c.158]
Печи для обжига керамических изделий бывают периодического и непрерывного действия. Камерные печ — периодического действия применяются для обжига изделий разнообразного ассортимента, вырабатываемых в небольших масштабах (специальная керамика, художественные изделия). [c.365]
Печи для обжига керамических изделий Печи для обжига стеклянных изделий Кольцевые [c.183] ПЕЧИ ОБЖИГА КЕРАМИЧЕСКИХ ИЗДЕЛИЙ Туннельные печи [c.169]Печи периодического действия применяют главным образом для термообработки металлических деталей (отжига, закалки, нормализации), а также сушки и обжига керамических изделий. В химической технике их используют в тех же целях, что и периодически действующие полочные и камерные сушилки, когда температура процесса сушки превышает температуру, которую могут выдержать без деформации металлические стенки (обычные полочные или камерные сушилки применяют редко, если температура циркулирующего газа >320—430°С). Кроме того, эти печи используют для обжига небольших количеств материала, термического разложения и других химических реакций, проведение которых в большом масштабе осуществляется во вращающихся обжиговых, подовых и шахтных печах. [c.235]
Важным прибором для регулирования обжига керамических изделий служат конусы Зегера — маленькие с узким основанием пирамиды, сделанные из тщательно приготовленной керамической смеси и имеющие резко выраженную температуру размягчения. Они устанавливаются в различных точках внутри печи так, чтобы их можно было наблюдать. Они разрушаются, если в этих местах печи достигается соответствующая температура. Конечно, это разрушение происходит с некоторым запаздыванием, но пирамиды достаточно дешевы, и потому их можно распределять повсюду в печи. [c.462] Примерами периодических процессов могут служить азотирование карбида кальция в цианамидных печах, обжиг керамических изделий в кольцевых печах в качестве примеров непрерывных процессов можно назвать обжиг колчедана или известняка, электролиз растворов хлоридов и др. [c.15] В том случае, когда садка нагревается и охлаждается в одной и той же нагревательной методической печи потери тепла будут невелики. Таков процесс обжига керамических изделий и процесс отжига металлов. В туннельной печи продукты сгорания нагревают подаваемую в печь садку, а выдаваемая из печи садка подогревает вдуваемый в печь воздух. В печи бесконечной длины с хорошей теплоизоляцией вряд ли вообще понадобилось бы добавлять топлива. Однако с удлинением печи и увеличением количества изоляции
3.3. Туннельные печи
Туннельные печи применяют для обжига строительных керамических изделий (кирпича, плитки, канализационных труб, сантехнических изделий и др.). Они являются наиболее совершенными по сравнению с другими видами печей, используемых для обжига данных видов изделий, т.к. значительно улучшают условия труда обслуживающего персонала и имеют более высокую производительность.
Рабочей камерой туннельной печи (рис. 16) служит сквозной канал (1), заполненный вагонетками (2), на которых установлены изделия (3). В средней части печи размещена зона обжига. В ней сжигается топливо и продукты горения, проходя через зону подогрева, омывают и подогревают изделия. Отработанные дымовые газы выбрасываются в атмосферу дымососом (4). Воздух в зону охлаждения подается вентилятором (5). Охлаждая изделия, он нагревается и поступает в зону обжига, где используется для процесса горения топлива.
В зоне подогрева изделия досушиваются и подогреваются в зоне обжига, а в конце ее происходит некоторое время выдержка изделий при максимальной температуре. В зоне охлаждения изделия сначала быстро остывают и переходят из пиропластического состояния в хрупкое, далее интенсивность охлаждения понижается. Процесс охлаждения заканчивается когда изделия достигнут температуры выгрузки (50-60 С).
При установившейся работе печи, туннель целиком загружен вагонетками, при этом наружные торцы крайних вагонеток почти совпадают с обрезами стен печи. Для загрузки очередной вагонетки, ее по рельсовым путям подают к загрузочному торцу печи и заталкивают в печь толкателем. Состав вагонеток, находящийся в туннеле, перемещается на длину одной вагонетки и с другого конца печи выталкивается вагонетка с обожженными изделиями. Подобное перемещение вагонеток может производиться либо непрерывно, либо ритмично. Таким образом, в туннельных печах, в отличие
Рис. 16. Принципиальная схема туннельной печи. |
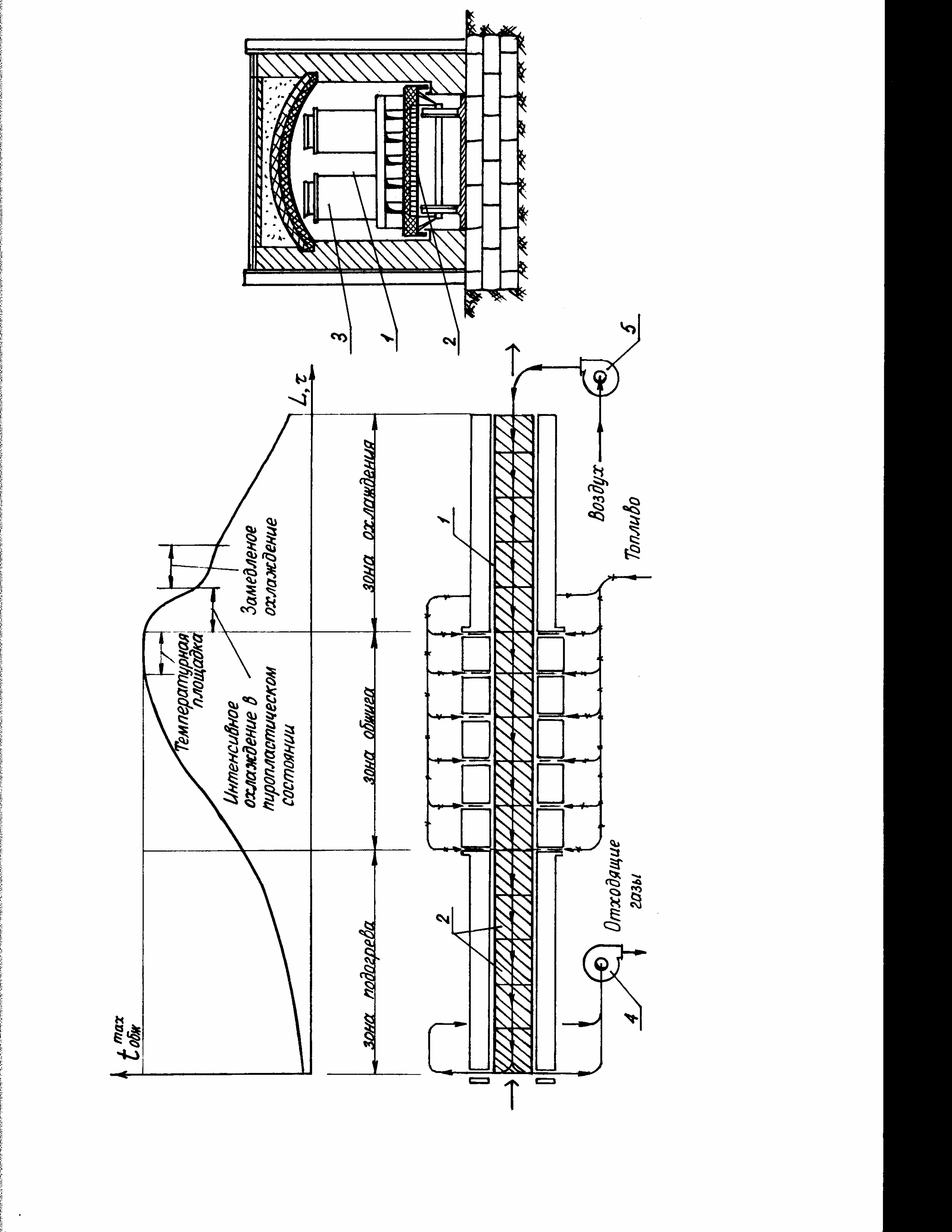
от кольцевых, тепловые зоны расположены стабильно, а обжигаемый материал перемещается относительно этих зон вдоль туннеля навстречу потоку газов, что дает возможность достигнуть высоких температур нагрева (примерно до 1700С).
Туннельные печи классифицируются по следующим признакам:
— по форме туннеля различают печи с прямолинейным и кольцевым каналом, щелевые и много канальные;
— по способу перемещения обжигаемых изделий печи бывают вагонеточные, ленточные, роликовые, со скользящими подкладками, с вращающимся и шагающим подом;
— по способу теплообмена различают печи прямого огня и муфельные печи;
— по источнику теплоснабжения печи могут быть пламенными и электрическими;
— по способу сжигания топлива.
Туннельные печи конструктивно отличаются друг от друга по аэродинамической схеме движения дымовых газов и воздуха. Наиболее распространенные схемы приведены в табл. 4.
Таблица 4
Характеристика аэродинамических схем туннельных печей
№ схемы рис. 37 | Особенности схем | Краткая оценка схемы |
1 | 2 | 3 |
а | Один отсасывающий вентилятор | Вся печь работает под разряжением при открытом канале с выгрузочной стороны печи. Большие подсосы излишнего воздуха и значительная неравномерность температур по высоте печи. Повышенный расход топлива |
б | Два концевых вентилятора, с нагнетанием холодного воздуха и отсосом дымовых газов | Простейшая и наиболее надежная схема для случая, когда не требуется отбор теплого воздуха для сушки |
Продолжение табл. 4 | ||
1 | 2 | 3 |
в | Отбор нагретого воздуха из зоны охлаждения в сушилку | Схема требует тщательного регулирования режима работы среднего вентилятора во избежание частичного отсоса дымовых газов из зоны обжига |
г | Передача нагретого воздуха из зоны охлаждения в зону подогрева | Существенно улучшается работа зоны подогрева, сокращается перепад температуры по высоте печи |
д | Рециркуляция газов в зоне подогрева | Схема сложная и трудно поддающаяся регулированию. Её применение оправдано лишь при обжиге сырца повышенной влажности |
е | Забор воздуха через открытые выгрузочные торцы печей и нагнетание его через сопловые турбулизаторы в зоне остывания | Обеспечивает выравнивание температур в зоне охлаждения, подогрева и обжига |
ж | Вентиляция подвагонеточного пространства посредством специальных вентиляторов | Достигается минимальный газообмен между печным каналом и окружающей средой |
з | Вентиляция подвагонеточного пространства при помощи основных вентиляторов | Вентиляция подвагонеточного пространства при такой схеме не эффективна и затрудняет работу основных вентиляторов |
Системы нагнетания и отбора воздуха и газов могут быть как сосредоточенные, так и распределенные. Сосредоточенный отбор газов обеспечивает работу с повышенными их скоростями по всей длине зоны подогрева, но не дает гибкого регулирования температурной кривой по отдельным зонам. Отбор газов в туннельных печах применяется в основном нижний, так как при верхнем отборе резко вырастает перепады температур по высоте зоны подогрева. Подача холодного воздуха в зону остывания возможна как верхняя, так и нижняя, причем, верхняя подача более эффективна при большом напоре воздуха.
Оборудование туннельных печей. Основным элементом туннельной печи является обжигательный канал, имеющий длину от 40 до 180 м и ширину от 1,7 до 3 м. Стабилизация заданной температурной кривой обжига возможна при определенных соотношениях между длиной и площадью поперечного сечения обжигательного канала. Канал перекрывается арочным сводом со стрелой подъема от 1/5 до 1/7 ширины печи.
Стены печей выкладывают составными: в зоне подогрева из 2,5 обыкновенного кирпича в зоне обжига из 1 обычного, 1 шамотного и 1 диатомитового кирпича; в зоне остывания из 2 обыкновенных кирпичей и 1 шамотного. В последнее время некоторые туннельные печи строят из жароупорного бетона. Толщина стен должна обеспечивать температуру наружной поверхности, не превышающей 50С. В наиболее высокотемпературной части печи стены выкладывают толщиной до 1,5 м. Для компенсации температурных расширений между составными частями стен (облицовкой, изоляцией и футеровкой) устраивают температурные швы, заполняемые асбестовым шнуром.
В конструкции печного канала в качестве обязательных элементов должны предусматриваться металлический каркас или наклонные наружные стены для восприятия горизонтальных распорных усилий свода; лабиринтовые стыки стен и вагонеток; песочные затворы для уменьшения газообмена между подвагонеточным пространством и печным каналом; песочницы для постоянного пополнения песком желобов песочных затворов; пескоуловители для приема песка, увлекаемого фартуками вагонеток; аварийные окна, размещаемые на стыке зон обжига и охлаждения, предназначенные для ликвидации завалов садки; двери, снижающие газообмен с окружающей средой через торцы канала. Для этих же целей на загрузочном конце канала в отдельных случаях устраивают форкамеры со шлюзовыми затворами. В высокотемпературных печах устраивают смотровые подвагонеточные подвалы, которые дают возможность предупреждать и быстро ликвидировать аварию.
Печные вагонетки. Характеристика основных типов вагонеток туннельных печей приведена в табл. 5. Для предохранения от высоких температур металлические поды вагонеток футеруют шамотными камнями или жароупорным бетоном с теплоизолирующей прокладкой из легковесного кирпича. Стыки между стенами печи и вагонетками выполняются в виде лабиринта с песочным затвором. Передвижение вагонеток в туннельных печах осуществляется гидравлическим и механическим толкателем вагонеток.
Таблица 5
Волгатерм
Наращивание темпов строительства и конкуренция между производителями строительных материалов в России вызывают необходимость увеличения количества и улучшения качества строительного керамического кирпича. Эта задача может быть решена путем усовершенствования систем управления технологическими процессами, в частности обжига, который находится в конце производственного цикла. Именно во время этой операции формируются свойства продукции, которые определяют понятие «качество». Процесс обжига проводят преимущественно в туннельных печах, оснащенных, в большинстве, газогорелочными устройствами, не отвечающими современным требованиям по интенсификации теплообмена в печном канале. Это приводит к значительному снижению качества обжига или к потере производительности и, как следствие, к повышению удельного расхода топлива на обжиг.
Наиболее типичными недостатками отечественных туннельных печей являются:
- большой перепад температур по вертикали обжигательного канала в зоне подготовки (300°C и более), что обусловлено неудовлетворительной системой рециркуляции;
- неудовлетворительная конструкция горелочных устройств, их плохая регулируемость и отсутствие возможности определения их тепловой мощности;
- низкий уровень автоматизации систем безопасности и печи в целом.
Все эти недостатки приводят к снижению качества продукции и производительности (особенно перепад температур по вертикали обжигательного канала) печи. Поэтому замена старых газогорелочных устройств на современные с реконструкцией системы управления нагрева, учитывающей все стадии физико-химических превращений в процессах нагрева керамики, является актуальной задачей.
В настоящее время наиболее эффективными средствами по устранению вышеупомянутых проблем является оснащение туннельных печей скоростными горелками в зоне подготовки и сводовыми горелками в зоне обжига, а также внедрение современных систем управления и контроля, позволяющих использовать импульсный режим работы горелок.
-
Рис. 1 Туннельная печь
-
Рис. Туннельная печь
Одна из главных функций любой системы управления процессом нагрева – это регулирование подвода тепла в соответствии с технологическими потребностями. При использовании импульсного режима управления горелки работают в режиме большого пламени в течение контролируемого промежутка времени и затем циклически переключаются в режим малого пламени или полностью выключаются. Промежуток времени, когда горелка работает в режиме большого пламени, затем в режиме малого или отключена, управляется процессорным контроллером. Каждая горелка регулируется независимо от других горелок, что увеличивает гибкость и точность управления.
В традиционных системах управления сжиганием, горелки работают в диапазоне между большим и малым пламенем. Как правило в таких системах некоторое количество горелок, жестко привязанных друг к другу, разжигаются и контролируются совместно.
Хотя импульсный режим работы является относительно новым в России, он широко используется в Европе уже более двадцати лет. Фирма Kromschroeder была пионером в области импульсного сжигания и продвигала идею горелок для индивидуального импульсного режима работы в промышленности. Концепция и необходимые технические средства тщательно разработаны, проверены и испытаны в различных отраслях промышленности. Идея разработана в одном из университетов, а фирма Kromschroeder занималась проектированием средств управления и специальных клапанов, которые являются основой успешного импульсного режима работы.
На рис. 2 приведена схема пропорциональной системы управления. В данной схеме имеется одна регулирующая воздушная заслонка с приводом и по одному регулятору соотношения воздух/газ на каждой горелке. В момент, когда процесс требует большего количества тепла, температурный контроллер дает сигнал на открытие воздушной заслонки. Увеличивающееся в результате этого давление воздуха через импульсную линию, расположенную за воздушной заслонкой, воздействует на мембрану регулятора соотношения воздух/газ. Давление воздуха поднимает диафрагму, открывая седло клапана, чтобы увеличить расход газа на горелки. Поскольку давление газа растет, оно действует на диафрагму регулятора, создавая равновесие давления между воздухом и газом. Давление газа на выходе приблизительно равно импульсному давлению воздуха. В такой системе контроллер управляет одновременно всеми горелками, объединенными одной воздушной заслонкой, то есть расход газа и время работы всех горелок одинаковы, независимо от их расположения в печи.
-
Рис. 2 Пример системы плавного регулирования
-
Рис. 3 Пример системы импульсного регулирования
-
Рис. 4 Сводовая горелка
Главным отличием системы импульсного регулирования (рис. 3) от представленной выше системы является наличие электромагнитного клапана (заслонки) на линии подачи воздуха каждой отдельной горелки. Таким образом появляется возможность независимого управления временем включения и мощностью любой горелки в системе.
Сводовые горелки
Основным видом брака при обжиге кирпича является недожог нижних рядов садки, что обусловлено конструктивными особенностями эксплуатируемых туннельных печей. Группы высокоскоростных сводовых горелок обеспечивают постепенный нагрев изделий и стабильную температуру обжига по ширине и высоте туннеля печи, что крайне важно для получения стабильного размера готовых изделий (рис. 4).
Применение специальных горелок с отверстиями для продувки воздухом фирмы Kromschroeder служит равномерному распределению температуры в окислительной или восстановительной печной атмосфере (рис. 5).
Скоростные сводовые горелки играют немаловажную роль в процессе создания однородного температурного поля за счет кинетической энергии струи продуктов сгорания обеспечивая выравнивание температуры по высоте садки.
Концепции импульсного управления работой горелок керамических обжиговых печейВ туннельных обжиговых печах одновременно протекает ряд сложных процессов: горение топлива, движение продуктов горения в рабочем пространстве печи, теплообменные и массообменные процессы, связанные с экзотермическими и эндотермическими эффектами в обжигаемых изделиях. Формирование черепка изделий при обжиге достигается оптимальным выбором температуры и времени нагрева полуфабриката, а также химическим составом печной атмосферы (газовым режимом) и временем обжига.
Наиболее оптимальна конструкция печи для обжига, соединяющая в себе равномерное распределение теплоносителя по высоте туннеля и интенсивное его движение в поперечном сечении сушилки. Зона обжига туннельной печи, как правило, делится на несколько зон с различными характеристиками по температуре и скорости нагрева.
Импульсный режим работы позволяет установить необходимое температурное поле по длине печи, независимо от количества зон, так как горелочные устройства автономны. Преимущества импульсной системы управленияБолее последовательный и точный контроль соотношения воздух/газ и подводимой мощности к системе, так как горелка настраивается всего на несколько стационарных режимов горения.

Пример установки сводовых горелок фирмы «Кромшрёдер» на Норском керамическом заводе (Ярославль)Увеличение производительности возможно за счет установки на печь горелок большей мощности, без ухудшения качества регулирования. Более интенсивная циркуляция дымовых газов, по сравнению с системой плавного регулирования, обеспечивает равномерное распределение температуры, что при увеличении мощности позволяет существенно сократить цикл обжига без снижения качества.
За счет полностью автоматизированной системы регулирования температуры в печи может быть достигнута большая гибкость управления технологическим процессом. В печах туннельного типа наличие большого числа управляемых зон горения позволяет создавать требуемое по условиям технологического процесса температурное поле по всей длине печи. Импульсный режим работы не ограничивает количество зон. Так как каждая горелка может регулироваться отдельно, появляется возможность тонкой регулировки мощности в печи.
Импульсный режим работы горелок позволяет добиться серьезного снижения брака за счет оптимизации процесса горения и точного регулирования температурного поля в продольном и поперечном сечениях печи. Интенсивная циркуляция продуктов сгорания и автоматизированная система поддержания температуры способствуют равномерному прогреву материала по всей высоте садки. При использовании импульсного режима можно снизить до минимума разницу скоростей сушки сырца по вертикали печи, который является одной из основных причин брака продукции при обжиге.
Существенная экономия топлива обуславливается сохранением точных соотношений газ/воздух в течение всего процесса сжигания, а также хорошим смесеобразованием присущим всем горелкам «Кромшрёдер». Соотношение воздух/газ может быть установлено очень близко к отношению 10:1 для всех режимов работы горелки. В зонах предварительного подогрева в туннельных печах или печах непрерывного действия может использоваться избыточный воздух. Благодаря этому экономия топлива составляет 20–25%.
Повышение безопасности и уменьшение времени вынужденного простоя обеспечивается за счет наличия у горелок фирмы «Кромшрёдер» индивидуального контроля пламени в каждой горелке. Пропадание одного контрольного сигнала по какой либо причине не влияет на работу других горелок в системе. При необходимости увеличения количества подаваемой теплоты система импульсного управления просто игнорирует любую горелку в цикле без контрольного сигнала пламени, и другие горелки компенсируют недостачу до тех пор, пока не будет устранена причина дефектного сигнала. Автоматизированное управление также обеспечивает автоматизированный, надежный и простой розжиг горелок.
Другой результат более точного контроля, предлагаемого импульсными системами, это уменьшение загрязнения воздуха. Могут быть значительно снижены уровни выбросов NOx.
Стоимость капитальных вложений может быть уменьшена в многозонных печах с импульсной системой, так как требуется только одна магистраль воздуха и газа. Это так же очень важный фактор. Если в системах с пропорциональным регулированием каждая зона имеет как минимум собственный воздухопровод, что обычно налагает ограничение на количество зон печи, то при импульсном управлении удвоение количества регулируемых тепловых зон не вызывает проблем. Устраняются такие факты как неравномерность загрузки, улучшается равномерность нагрева.
Туннельные печи для обжига фарфоровых и фаянсовых изделий 3
Особенностью туннельных печей для обжига фарфора является высокая температура второго обжига (1350-1410 °С) и наличие восстановительного периода, когда печные газы содержат 2-4% оксида углерода.
На скорость нагрева и охлаждения фарфора в разные периоды обжига оказывают большое влияние размеры и толщина стенок изделий, что отражается на выборе печей для обжига, конструкции которых многочисленны. Ниже приводится техническая характеристика туннельной печи для обжига фарфора Дмитровского фарфорового завода:
Длина печи (верхнего строения), м…………………. 93,5
Ширина печного канала, м………………………. 1,5
Высота печного канала от футеровки вагонетки до замка свода, м……… 1,7
Высота подставок под капсели (канализированного пода), м…. 0,34
Длина вагонетки, м…………………………… 1,85
Ширина рамы вагонетки, м………………………. 1,59
Ширина футеровки вагонетки, м…………………… 1,59
Ширина колеи, м…………………………….. 0,90
Количество вагонеток в печи, шт…………………… 50
Максимальная температура обжига, °С………………. 1450
Время обжига, ч……………………………… 35—40
Зона обжига этой печи оборудована 30 щелевыми и 8 межсадочными топками, подающими пламя в пролеты между садкой смежных вагонеток. Для надежного и более четкого разграничения окислительной и восстановительной зон устроены три газовые завесы. Воздух в газовые завесы подают из зоны охлаждения с предельно высокой для выбранных вентиляторов температурой. Количество воздуха, поступающего в каждую завесу через щели в своде, регулируется шиберами.
Наиболее выгодно используется печной объем при обжиге полых изделий без капселей на карборундовых этажерках, а блюдец, тарелок и блюд — в капселях. Для этого в печах с широким печным каналом среднюю часть вагонетки загружают полыми изделиями, а по краям ставят капсели с тарелками и блюдцами. Поэтому для обжига хозяйственного фарфора нецелесообразно строить туннельные печи с шириной канала меньше 1,5 м.
Преимущества туннельных печей — непрерывность процесса обжига; благоприятные условия загрузки и выгрузки изделий, выполняемых на вагонетках в нормальных температурных условиях вне печной камеры; удобство и надежность регулирования режима обжига путем перемещения изделий по заданному графику через зоны печи со стабилизированными температурными и газовыми условиями термообработки.
К недостаткам этих печей относится расслоение потоков печных газов в зонах подогрева и охлаждения и, как следствие, большая разница температур между верхней и нижней частями загрузки на вагонетках. В зоне обжига и у выхода из печи температуры в садке изделий выравниваются, что ведет к резкому удлинению цикла обжига и снижению производительности печей.
Туннельная печь обжига кирпича ОАО Ивановский завод керамических изделий (стр. 1 из 15)
МИНИСТЕРСТВО ОБРАЗОВАНИЯ РОССИЙСКОЙ ФЕДЕРАЦИИ
ИВАНОВСКИЙ ГОСУДАРСТВЕННЫЙ ЭНЕРГЕТИЧЕСКИЙ УНИВЕРСИТЕТ
к дипломному проекту на тему:
Туннельная печь обжига кирпича ОАО «Ивановский завод керамических изделий»
РЕФЕРАТ
Дипломный проект выполнен применительно к условиям ООИ «Взаимопомощь», ранее именуемый «Ивановский завод керамических изделий».
В дипломном проекте проведен расчет туннельной печи, включающий в себя: тепловой баланс печи, расчет горения топлива, расчет продолжительности обжига кирпича, выбор горелочных устройств, подбор вентиляторов. Также был проведен расчет камерного сушила для сушки кирпича-сырца.
Была разработана методика расчета внешнего теплообмена в щелевой электрической печи на основе метода ЗУП (зональный с условными поверхностями).
Разработана схема автоматизации туннельной печи. Выявлены вредные и опасные факторы, возникающие при эксплуатации туннельной печи, разработаны мероприятия по предупреждению и снижению воздействия их на обслуживающий персонал.
1. ОПИСАНИЕ ТЕПЛОТЕХНОЛОГИИ СУШКИ И ОБЖИГА КЕРАМИЧЕСКИХ ИЗДЕЛИЙ
1.1 Сушка керамических изделий
1.1.1 Значение сушки изделий и материалов
Для каждого материала и изделия устанавливается определенный режим сушки, то есть допустимая интенсивность сушки, температура материала, температура и относительная влажность сушильного агента и теплоносителя, скорость его движения у материала и изменение указанных параметров в различные периоды процесса сушки. Сушить песок можно при любых температурах и скоростях удаления влаги. Сушить комовую глину и топливо можно при любых скоростях удаления влаги, но температура нагрева этих материалов ограничивается. Так, глина при температуре выше 400°С теряет пластичность, а в топливе выше 150–200°С начинается возгонка горючих продуктов. Растрескивание глины при сушке, вследствие усадки и возникающих усадочных напряжений, ускоряет выделение влаги. Сушка керамических изделий требует определенного режима, как в отношении допускаемых безопасных скоростей сушки, так и температуры нагрева изделий.
Таким образом, теория сушки должна рассматривать не только вопросы статики сушки – материальный и тепловой балансы сушки, миграцию влаги в материале, законы тепло- и массообмена в зависимости от связи влаги с материалом, но и поведение изделий при сушки, связанное с усадочными напряжениями и максимально допускаемыми скоростями сушки. Только лишь это комплексное рассмотрение вопросов теории сушки позволит устанавливать оптимальные режимы сушки, при которых изделия будут высыхать в кратчайшие сроки и иметь высокое качество.
Сушкой называется процесс удаления из твердых материалов содержащейся в ней влаги за счет ее испарения и удаления образовавшихся паров с поверхности тела в окружающую среду. Для этого к влажному телу, то есть кирпичу сырцу, необходим подвод тепла при условии, что давление водяных паров у поверхности тела больше давления водяных паров в окружающей среде. Процесс сушки сопровождается изменением веса материала во времени вследствие удаления из него влаги. Зная начальную влажность и вес материала, можно выразить графически изменение влажности по времени ω = f(t), то есть построить кривую сушки, изображенную на рис. 1.1 (кривая 1). По кривой сушки можно построить кривую изменения влажности материала в единицу времени, то есть кривую скорости сушки wm (кривая 2).
При сушке керамических материалов влага испаряется в основном с поверхности, а поэтому концентрация влаги в середине материала остается большей, чем у его поверхности. Вследствие возникновения перепада (градиента) влажности или концентрации влаги она перемещается из места с большей концентрацией к месту с меньшей концентрацией, то есть из середины тела к поверхности его.
Механизм и скорость перемещения влаги зависят от ряда факторов: формы связи влаги с материалом, его строения, температуры и влажности, а также пористости материала и других его свойств. Экспериментально установлено, что чем выше температура, влажность тела и давление пара внутри него, тем скорость сушки больше.
Процесс сушки керамических изделий можно разделить на следующие периоды.
1) Период прогрева. Материал, будучи помещен в пространство с повышенной температурой, прогревается. В конце этого периода (точка А на рис. 1.1) устанавливается постоянная температура поверхности и тепловое равновесие между количеством тепла, воспринимаемым изделием, и расходом тепла на испарение влаги. После этого наступает период постоянной скорости сушки.
Рис. 1.1. Схема изменения во времени влажности 1, скорости сушки 2 и температуры 3 материала
I — период прогрева; II- период постоянной скорости сушки; III- период падающей скорости сушки;
IV – период равновесного состояния; V – период влажного состояния; VI – период гигроскопического состояния материала
2) Период постоянной скорости сушки. В этот период скорость сушки постоянна и численно равна скорости испарения влаги с открытой поверхности. Следовательно, происходит испарение свободной влаги с поверхности материала, и поверхность в течение этого времени остается влажной за счет поступления влаги из внутренних слоев изделий. Температура поверхности материала
, равная приблизительно температуре мокрого термометра, остается неизменной в течение всего периода (кривая 3 на рис. 1.1). Давление паров над поверхностью материала равно парциальному давлению насыщенных водяных паров при температуре поверхности и не зависит от влажности материала.Указанный период является наиболее ответственным и опасным, так как в течение его происходит усадка материала, порождающая усадочные напряжения. Скорость остается постоянной до тех пор, пока среднее содержание влаги в изделии не понизится до критического (точка К1 на рис. 1.1), а на поверхности изделия не станет равным гигроскопической влажности
. С этого момента начинается период падающей скорости сушки. Однако в действительных условиях он может начаться и тогда, когда вследствие неодинаковых условий испарения влаги со всей поверхности влажность отдельных участков достигает влажности ниже гигроскопической, в то время как другие участки имеют влажность ниже гигроскопической. Следовательно, более правильно переход от периода постоянной к периоду падающей скорости сушки характеризовать точкой на кривой сушки отвечающей , то есть критической влажности.Гигроскопическую влажность тело приобретает, если его поместить на длительный срок в среду с относительной влажностью φ = 100 % при данной температуре. Гигроскопическая влажность
зависит только от свойств материала и уменьшается при повышении температуры его нагрева. Такую влажность имеет тонкий поверхностный слой изделия в конце периода постоянной скорости сушки.Критическая влажность представляет собой среднюю по всему изделию влажность, которая зависит от режима сушки, толщины изделия и коэффициента влагопроводности. При достижении изделием влажности
усадка поверхностных слоев прекращается, и дальнейшая сушка вызывает лишь увеличение пористости изделия.3) Период падающей скорости сушки характеризуется тем, что с уменьшением влажности изделия сушка постепенно замедляется. Уменьшение интенсивности испарения вызывает уменьшение расхода тепла на испарение влаги, что при прочих постоянных условиях приводит к увеличению средней температуры изделия и уменьшению температурной разности между сушильным агентом и поверхностью материала.
Уменьшение скорости сушки обуславливается тем, что парциальное давление водяных паров над поверхностью материала падает и становится меньше парциального давления насыщенных паров при температуре поверхности, являясь функцией температуры и влажности поверхности изделия, то есть
.По линии
на I-d- диаграмме и кривым равновесной влажности данного материала можно определить численные значения парциального давления пара над материалом в зависимости от температуры и влажности поверхности материала. При достижении поверхностью материала равновесной влажности скорость сушки становится равной нулю, то есть удаление влаги из материала прекращается. Величина равновесной влажности зависит от свойств материала и параметров окружающей среды, то есть от ее температуры и влажности.1.1.3 Требования, предъявляемые к сушилкам
Сушка изделий производится в специальных устройствах – сушилках. Сушилка должна обеспечивать максимальную скорость сушки материала при соблюдении его высокого качества, минимальный расход тепла и электроэнергии на 1 кг испаряемой влаги, равномерность сушки по всему объему сушилки; должна обладать возможно большей напряженностью объема по влаге (количеством испаряемой влаги на 1 м3 объема сушилки), легкостью регулирования параметров сушильного агента; должна быть оснащена механизмами для загрузки, выгрузки и перемещения материала; должна быть снабжена приборами теплового контроля (КИП) и автоматикой и удовлетворять санитарным нормам.
Печи для обжига фарфоровых и фаянсовых изделий периодического действия
Основным оборудованием, определяющим пропускную способность предприятия, являются печные агрегаты. Их стоимость в стоимости всего оборудования составляет 20- 32 %.
Печи, используемые для обжига фарфоровых и фаянсовых изделий, подразделяют по принципу работы (эксплуатационному режиму), способу теплообмена, способу отопления, конструктивным особенностям.
По эксплуатационному режиму различают печи периодического и непрерывного действия.
По способу нагрева различают печи с непосредственным нагревом изделий печными газами, муфельные (изделия отделяются от печных газов стенкой муфеля) и с электрообогревом.
По конструкции печи подразделяются на три группы:
туннельные (непрерывного действия) — с каналом, по которому изделия перемещаются на вагонетках;
конвейерные (непрерывного действия) — с одним или несколькими каналами малого сечения, по которым изделия перемещаются ленточными, роликовыми, шагающими или полочными конвейерами;
горны (периодического действия) — с круглыми или прямоугольными камерами.
Рассмотрим особенности работы некоторых типов печей.
Печи периодического действия (горны) работают по замкнутому, многократно повторяющемуся циклу: загрузка — обжиг — выгрузка. Конструктивно они подразделяются на одно- и двухкамерные, обычно круглой формы, и печи с выкатным подом (используются для обжига крупногабаритных изделий, небольших партий изделий, опытных образцов). По направлению движения топочных газов различают горны с восходящим (прямым) и нисходящим (обратным) пламенем. На ряде заводов еще используют двухэтажные круглые горны с обратным направлением движения топочных газов. Печи периодического действия имеют существенные недостатки — малую производительность, тяжелые условия труда по загрузке и выгрузке изделий, трудности по механизации и автоматизации этих работ. Преимущество горнов — возможность работы каждого цикла по индивидуальному режиму (температурному, аэродинамическому и газовому).
В настоящее время печи периодического действия повсеместно заменяют на печи непрерывного действия — туннельные и конвейерные.
Туннельные печи с непосредственным нагревом изделий широко используются, когда воздействие печных газов на изделия не может снизить их качество. В зависимости от объема производства и размеров обжигаемых изделий длина печей колеблется от 2-3 м (лабораторный тип) до 105 м, ширина канала 0,2-1,85 м, высота — 1-2 м.
Муфельные туннельные печи применяются для закрепления керамических красок при надглазурном декорировании изделий. В этих печах изделия отделены от действия печных газов перегородкой из огнеупорного материала и нагреваются в основном за счет излучения тепла от перегородок. В туннельных печах непосредственного нагрева этот эффект получают обжигом изделий в капселях, которые защищают изделия от воздействия газовой среды обжига.
Рис. 56. Туннельная печь: а — схема, б — разрез; 1 — горелки, 2 — вагонетка
Туннельные печи с электронагревом используются в тех же условиях, что и муфельные печи, но возможность их применения ограничивается высокой стоимостью электроэнергии по сравнению со стоимостью газообразного и жидкого топлива.
Туннельные печи (рис. 56) работают по непрерывному циклу. В них все стадии обжига (загрузка — обжиг — выгрузка) осуществляются одновременно и непрерывно. Основными конструктивными элементами этих печей являются печной канал, ограждения (стены, своды), топки, металлический каркас, механизм для перемещения в печном канале вагонеток с загруженными на них изделиями. В конструкцию канала печи входят двери с его торцов, лабиринтовые стыки стен и вагонеток, песочный затвор, пескоуловители, смотровые и аварийные окна, топки, камеры со шлюзовыми затворами, смотровые подвагонеточные подвалы (подподовый канал) и др.