Изготовление муфельной печи своими руками
В нашей повседневной жизни часто возникают ситуации, когда ломаются какие-нибудь дорогостоящие запчасти, и первая мысль, которая приходит в голову в таких случаях: — кусок алюминия, а стоит как… В такие моменты мы жалеем о том, что не знаем как изготовить такую, казалось бы, простую деталь самостоятельно. Все есть, и алюминий, и форму при огромном желании сделать можно, но, как довести метал до жидкого состояния, чтобы отлить эту самую деталь? В этом нам поможет муфельная печь. Не стоит пугаться того, что это дорогостоящее оборудование, и вы не сможете позволить себе его приобрести, ведь в данной статье мы рассмотрим, как самостоятельно изготовить муфельную печь , ограничившись небольшими затратами.
Сборка газовой горелки
В своем примере мы рассмотрим, как можно сделать муфельную печь, работающую на газу своими руками. Она отлично подойдет для плавки металлов, температура плавления которых находится в пределах 1300°F. Печь состоит из корпуса и горелки.
Для изготовления газовой горелки нам понадобится кусок трубы диаметром примерно 1,5-2 см. и длинной 10-15 см., с одной стороны которой мы сделаем внешнюю резьбу, а с другой просверлим ряд отверстий.
Самое первое отверстие от края должно быть сквозным. В него будет вставлена трубка, через которую будет подводиться газ. Остальные три отверстия находятся немного дальше от края, они будут служить для поджига горелки, а также забора воздуха. Сквозное отверстие для газоподводящей трубки должно быть перпендикулярно остальным трем отверстиям. Если присмотреться на рисунке видно еще одно небольшое отверстие с краю, его ось пересекается с осью сквозного отверстия, оно предназначено для затяжного болта газоподводящей трубки.
Газоподводящая трубка представляет собой кусок медной трубы диаметром примерно 0,8 см., с обоих торцов которой нарезана резьба, а посередине сделано несквозное отверстие (для выхода газа). С одной стороны трубки на резьбу с использованием ФУМ-ленты навинчена заглушка, а с другой уголок с внутренней и наружной резьбой. В дальнейшем к уголку будет присоединяться шланг от газового баллона. Для того чтобы избежать проворота газоподводящей трубки в горелке, с боку на ней делается неглубокий спил – место для фиксации затяжным болтом горелки.
В сборе горелка с газоподводящим шлангом выгладит, как показано на рисунке ниже. Там же можно увидеть и газовый баллон с пропаном и две жестяные бадьи, которые будут использованы для изготовления корпуса печи.
Важным моментом, при соединении газового шланга с горелкой, является то, что для обеспечения безопасности между ними нужно поставить огнепреградительный клапан.
Отлив корпуса муфельной печи
Кожух печи мы будем изготавливать из двух жестяных тазов. Первый будет служить основанием, а второй обрежется, и будет служить в качестве крышки с вентиляционным окошком. Корпус необходимо делать из огнеупорного материала. В данном случае им будет выступать раствор, приготовленный из огнеупорной глины, песка и цемента, смешанных в равных количествах.
В боковой стенке кожуха и в муфеле вырезаем отверстие для насадки горелки, которая будет проводить пламя в рабочую камеру печи, затем на основание таза выкладываем толстым слоем часть раствора, он будет служить основным упором для муфеля. Устанавливаем муфель служащий рабочей камерой (в данном случае это труба из огнеупорного материала) и насадку горелки.
Затем, пространство между муфелем и кожухом засыпаем приготовленным раствором. Таз, который обрезан под крышку также заполняется до краев огнеупорным раствором. При заливке крышки для печи, в ней необходимо предусмотреть вентиляционное отверстие.
Готовый корпус печи.
После того, как все подготовительные работы завершены и в кожух залит огнеупорный раствор, готовому корпусу необходимо дать выстоятся (высохнуть) 1-2 недели.
Когда корпус затвердел, необходимо собрать печь и прокалить ее пару раз при небольшой температуре. Для этого необходимо собрать горелку, вкрутить ее в насадку, забетонированную в корпусе печи, подсоединить к горелке газовый шланг от баллона с газом, со всеми необходимыми элементами (огнепреградительный клапан и газовый редуктор), открыть вентиляционное окошко в крышке и зажечь горелку. После того, как прокаливание будет произведено несколько раз, можно приступать к испытаниям муфельной печи собственного производства.
Необходимо чтобы в рабочей камере печи поднялась температура. Этого добиваются увеличением или уменьшением подачи газа. Когда температура становится достаточно высокой, через вентиляционное окошко можно заложить в печь первый «опытный» брусок алюминия, ну или кусок алюминиевого профиля.
Вам будет приятно наблюдать, как после стольких стараний он начнет плавиться.
Наконец, можно с уверенностью сказать, что вы добились поставленной цели – расплавить металл. Теперь у вас есть не только желание, но и возможность чинить поломанные вещи, механизмы и вообще любое оборудование у себя в гараже, ведь из расплавленного металла можно отливать не только слитки.
Вы вполне можете отливать черновые заготовки деталей, которые после соответствующей обработки будут практически неотличимы от настоящих.
Уважаемые читатели, если у вас остались вопросы, задавайте их, используя форму ниже. Мы будем рады общению с вами 😉
Рекомендуем другие статьи по теме
Инжекционная горелка для плавильной печи своими руками
Здравствуйте, уважаемые читатели и самоделкины!В данной статье Михаил, автор YouTube канала «Добрый Мастер», расскажет Вам как он изготовил инжекционную горелку для плавильной печи.
У автора возникла необходимость плавки цветных металлов, и он решил изготовить плавильную печь. Но одним из основных ее элементов является правильная горелка.
Материалы.
— Стальная труба
— Жестяной хомут
— Наконечник от сварочного полуавтомата с диаметром 0,8 мм
— Пропановый редуктор
— Болт М10 под шестигранный ключ, гайка, шайба
— Газовый шланг.
Инструменты, использованные автором.
— Болгарка, отрезной и коралловый диски
— Токарный станок
— Тиски, молоток
— Ленточная шлифовальная машинка
— Метчики
— Штангенциркуль
— Линейка, карандаш.
Процесс изготовления.
В качестве ориентира мастер нашел чертеж данной горелки в интернете.
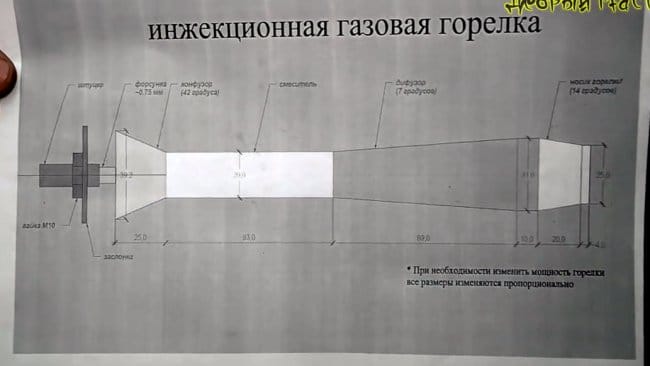
Затем подобрал стальные трубки.
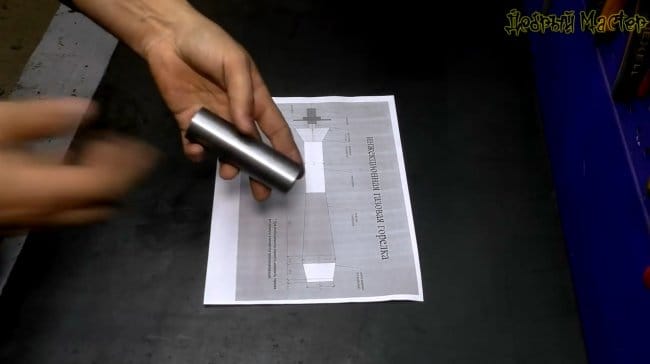
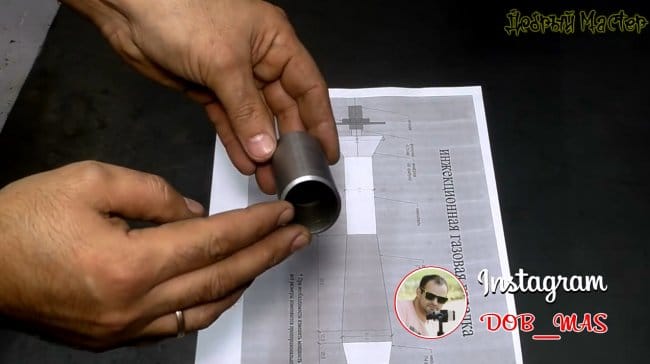
В качестве форсунки автор будет использовать болт под шестигранный ключ.
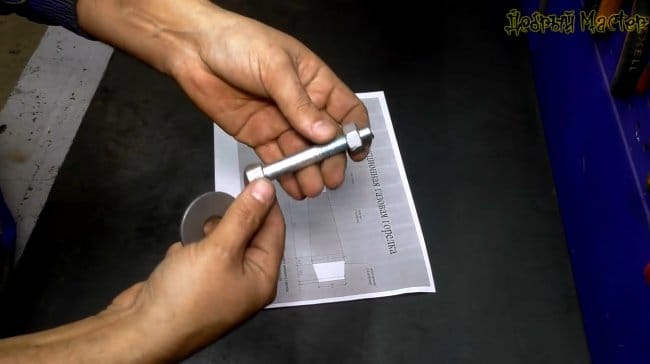
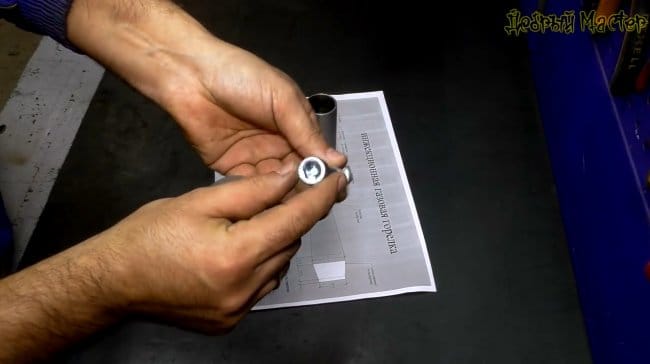
А в сам болт будет вкручиваться наконечник для сварочного полуавтомата. Диаметр отверстия 0,8 мм.
Также автор приобрел пропановый редуктор и газовый шланг.
Теперь нужно отрезать кусок трубы длинной 180 мм.
Торцы трубы автор зачистил лепестковым шлифовальным диском. А затем снял краску коралловым диском.
Затем размечает диффузор (120 мм) и носик (35 мм) горелки. Для точного реза можно просто обернуть трубу листом бумаги, и нанести разметку.
Также он разметил восемь продольных секций.
После предварительных надрезов, мастер стягивает хвостовик хомутом, и прорезает чуть шире. Корпус будущего диффузора нужно подогнать под размер смесителя.
Затем сдвигает хомут на середину, расширяет задние части.
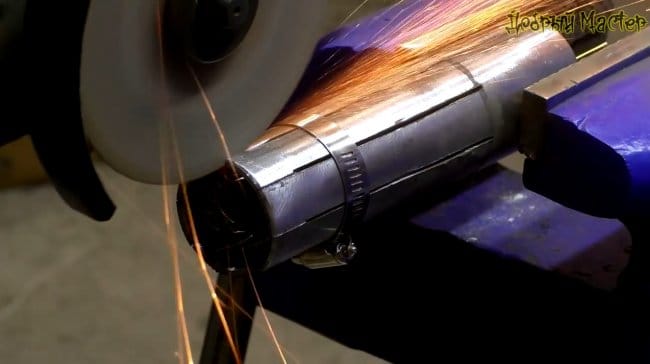
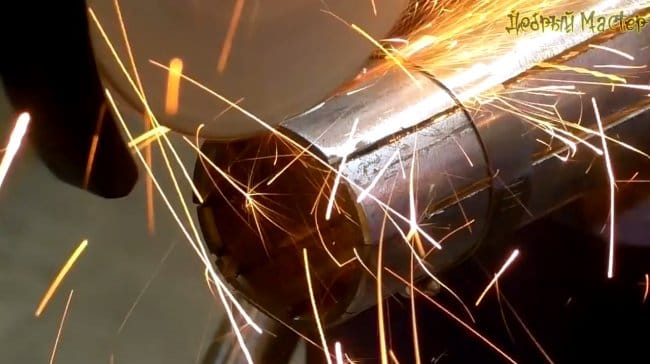
Прихватывает точечной сваркой, стянув полученные лепестки.

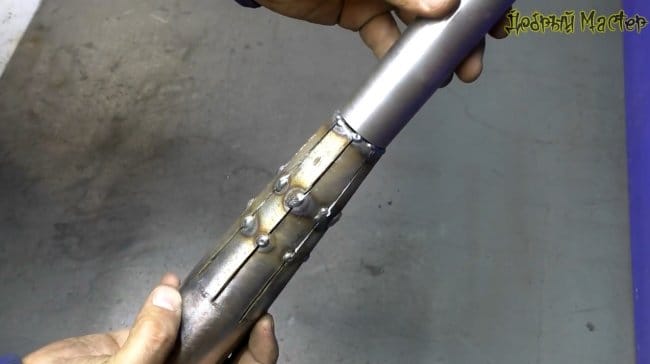
Теперь все швы диффузора можно проваривать.
Вот такой диффузор получился. Швы можно зачистить и при помощи болгарки, но у автора есть токарный станок.
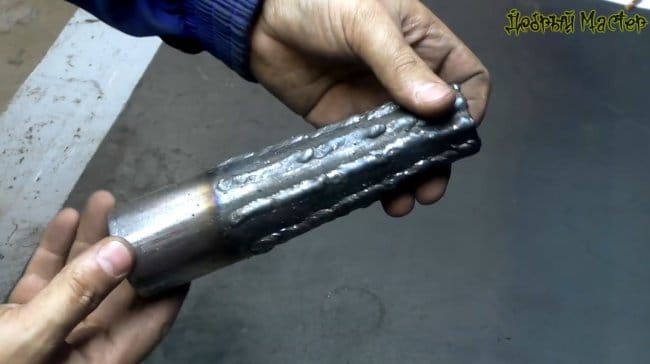
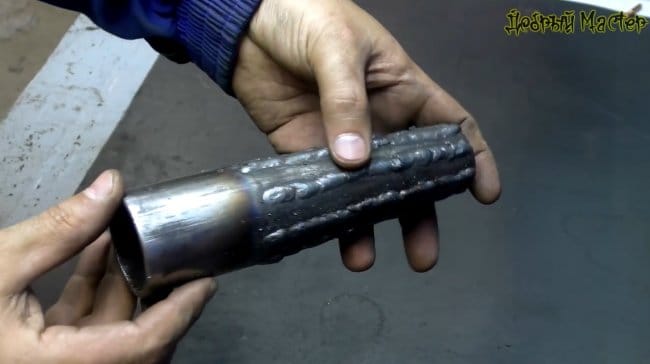
Зажимает заготовку в патроне токарного станка.
Для обработки конуса мастер использует малую продольную подачу, а чтобы не крутить вручную — он приспособил для этого шуруповерт.
Теперь можно приваривать трубку смесителя.
Носик горелки автор заужает таким же методом, как и диффузор.
Сгибает лепестки молотком, проваривает швы.
После зачистки получается вот так.
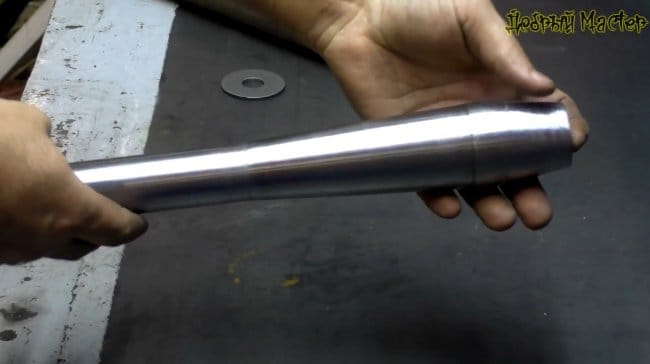
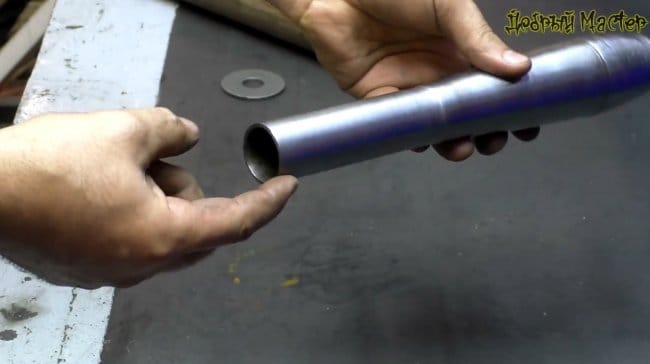
Осталось сделать последнюю деталь — конфузор, и приварить к основному корпусу. Способ изготовления такой же.
Приступает к изготовлению форсунки из болта и наконечника.
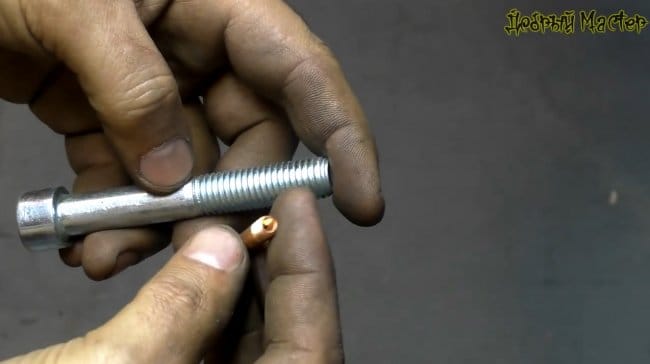
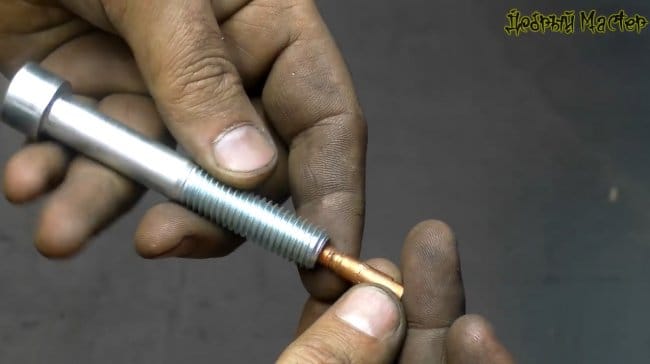
В болте сверлит сквозное отверстие 5 мм диаметром. Не забывая про смазку.
При отсутствии токарного станка эту работу можно выполнить, зажав сверло в тисках, а болт — в патроне дрели.
В отверстии нарезает резьбу, и вкручивает в него наконечник.
На второй стороне болта нарезает «елочку» для надежного закрепления шланга.
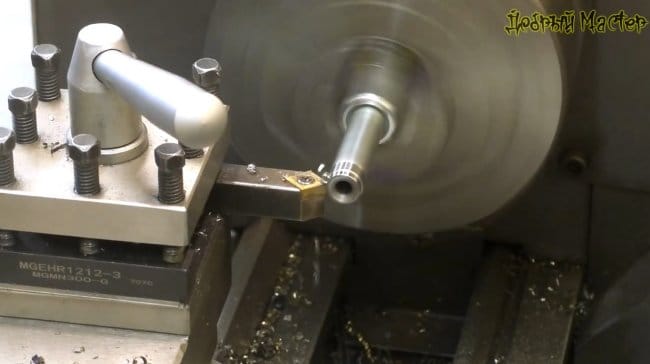

Вот форсунка и готова, ее нужно прикрепить к корпусу. Жиклер немного утопил в форсунке, увеличив расстояние для регулировки.
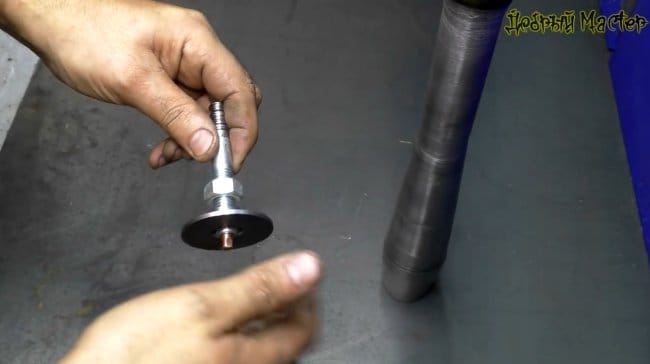
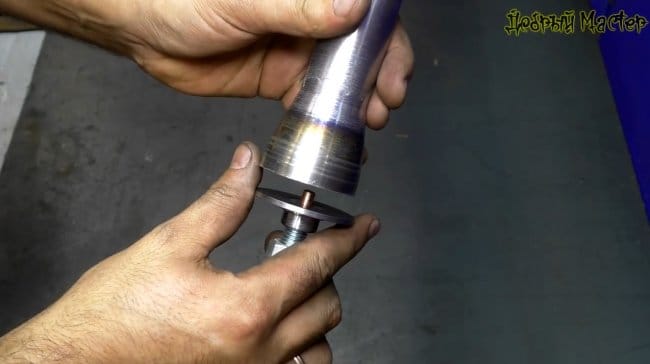
Вырезает полоску из стального листа. Зачищает ее от краски, сгибает в тисках. Затем сверлит отверстие под форсунку, нарезает в нем резьбу.
Теперь можно приварить к корпусу.


Окрасив корпус огнеупорной краской, горелка почти готова.
Сначала мастер закрепил горелку в тисках внутри мастерской.
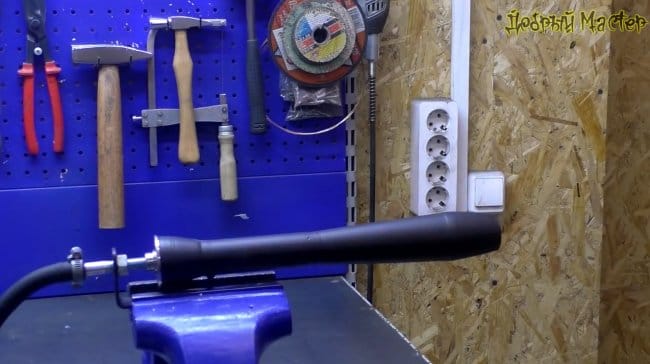
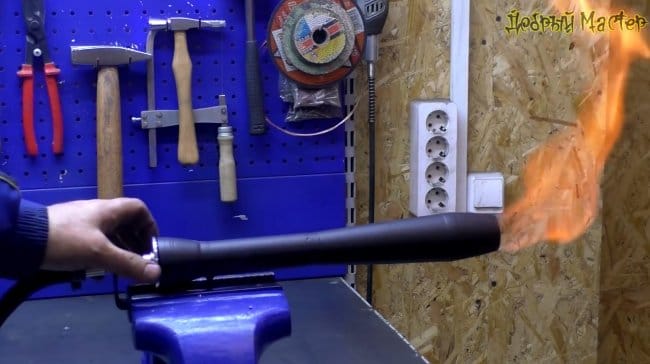
По причине быстрого сжигания кислорода пришлось выйти регулировать на улицу.
Горелка имеет три регулировки. Регулировка давления газа на редукторе, подачи воздуха, и глубина глубины форсунки в конфузоре. Подняв давление газа до 0,5 атмосферы, удалось очень быстро нагреть толстый стальной пруток 14 мм.
Спасибо автору за простое, но полезное приспособление для мастерской!
Всем хорошего настроения, удачи, и интересных идей!
Источник
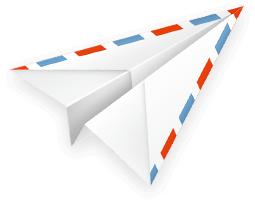
Получайте на почту подборку новых самоделок. Никакого спама, только полезные идеи!
*Заполняя форму вы соглашаетесь на обработку персональных данных
Становитесь автором сайта, публикуйте собственные статьи, описания самоделок с оплатой за текст. Подробнее здесь.Газовая печь для обжига керамики своими руками. / Газовые печи / Гончарная мастерская
Вид готовой печи со смотровыми окошками и термопарой. Низ и средняя часть на время обжига скрепляются покупными струбцинками. Для контроля температуры используется портативный мультиметр.Посмотрим из чего она состоит и что у нее внутри… Первое — это подставка. Сделана из профильной трубы 20×40, сварена и покрашена молотковой эмалью. (тут все просто)
Нижняя часть печи — устанавливается на подставку. Представляет собой каркас сваренный из профильной трубы 15×15, армированный сварной оцинкованной сеткой 25×25.
На дне лежит cerablanket 25мм, на нем уложен один слой кирпича ШЛ-0.8. По бокам cerablanket в два слоя — внешний 25мм, внутренний 50мм. (укреплен керамическими пуговицами).
В чашке прорезано отверстие для горелки.
Средняя часть по аналогии выполнена из той же трубы 15×15, той же сетки.
Внутри аналогично — два слоя Cerablanket 25 и 50мм закрепленных пуговицами.
Крышка аналогично — из сетки, два слоя Cerablanket.
Вырезано отверстие для выхода газов
На крышке Cerablanket закреплен теми же пуговицами собственного изготовления
Термопара внутри печи.
Самодельные печки. Нагревательная газовая мини-печь — Общий
Решил создать новую ветку, т.как Арти уже кривится на мои сообщения в его ветке. 🙂
Эта печка была сделана с целью что — либо поделать, т.е. погреть и постучать и даже расплавить что-нибуди цветное, во время выездов на природу. Печка, 12л. газовый баллон, 30кг. наковаленка, кузнечные клещи и молоток, да пара кусочков металла,- все это свободно умещается в багажнике.
Как и обычно все начинается с эскиза.
Далее подыскивается подходящий корпус. Для него прекасно подошел пустой фреоновый баллон.
Правда его длина была немного маловата. Баллон был разрезан, в него вварено кольцо проставка удлинняющая корпус. Бали изготовлены и приварены хомутики для стяжных болтов, а также патрубок в который вставляется корундовая трубка доходящая по касательной до огневой зоны.
Далее, заранее купленные блоки «Термоизола 1400» (1400 — это рабочая температура данного огнеупора) были размечены.
Вырезано дно
И кольца создающие огневую зону
Термоизол легко режется ножевкой, строгается ножем или стамеской. Отходы, т.е. стружки и опилки термоизола не выбрасываются. Собираются, перемалываются, просеиваются. Полученный порошок далее будет необходим для изготовления огнеупорной обмазки.
Кольца вставляются в половинки корпуса. Внутренняя часть и боковые поверхности пропитываются АХФС (алюмохромфосфатным связующим) на основе порошка термоизола и АХФС делается мастика для обмазки огневой зоны и склейки колец термоизола. С АХФС термостойкость пропитанного термоизола повыщается до 1600*С
Половинки печки складываются и стягиваются болтами.
Изготавливается подставка для печки
Печка практически готова
Осталось поставить ручку для переноски, кронштейник, чтобы опирать горелку, и передний столик перед леткой с вставленной керамической пластиной. Так как это фактически газовый горн, то крышка не делается. Подставляется небольшой блок термоизола с дырочкой, для контроля за огневой зоной.
Печка в работе.
Окрашивается корпус печи термостойкой краской (до 650*С) снаружи черной, внутри аллюминизированной. Справедливости ради надо сказать, что однослойная изоляция имеет более высокий коэффициэнт теплопередачи и после получаса работы печи поверхность ее нагревается, что рука уже не терпит. Какую температуру можно получить в такой печке? Скажу, что однажды делал отжиг 4-х клинков из стали Х12МФ, зазевался и получил единый монолит. Сплавились в один кусок. Надо сказать, что в таких малых объемах газовую печь сложно контролировать с помощью термопар. В основном на глаз, по цвету раскаленного металла.
В настоящее время делаются две похожих минипечки, но центральная (огневая) зона из корундовой трубы, точнее из пенокорунда, рабочая температура до 1750*С, а далее муллитокремнеземный фетр пропитанный окисью циркония, с рабочей температурой 1400*С. По расчетам такая изоляция позволит дольше держать высокие температуры.
В такой печке можно греть металл под ковку. Даже свободно делать (сваривать) дамаск. Можно плавить цветмет в небольших тиглях. Проводить высокотемпературную пайку. Сплавлять пакеты пластин из цветных металлов, для изготовления Мокуме-гане. Проводить закалку, отжиг, термоциклирование, нормализацию, отпуск и т.д.