Газогенератор — Энциклопедия журнала «За рулем»
Газогенератор
Газогенератор – это установка для получения горючего газа из твердого топлива. В качестве твердого топлива, как правило, применяются местные ресурсы: уголь, торф, древесина, солома, а так же отходы деревообрабатывающих производств. Превращение твердого топлива в газообразное называется «газификацией» и заключается в сжигании топлива с поступлением количества кислорода воздуха или водяного пара, недостаточном для полного сгорания.
Сегодня газогенераторные установки используют для получения пара, или горячего воздуха для различных технологических процессов, а так же в составе отопительных систем. Однако в 30-е – 40–е годы прошлого века газогенераторы с успехом применяли на транспорте: массовая эксплуатация автомобилей на древесных чурках обещала сберечь жидкое топливо для более важных нужд — тонны сэкономленного бензина можно было направить в вооруженные силы или авиацию.
В 1923 году профессором Наумовым была разработана газогенераторная установка для 3-тонного грузовика, способная работать на древесном угле или на антраците. Установка была испытана в стационарных условиях совместно с 4-цилиндровым бензиновым двигателем Berliet L 14 мощностью 35 л.с. В 1928 году FIAT-15Ter с газогенератором Наумова совершил пробег по маршруту Ленинград – Москва – Ленинград. Первая половина 30-х годов отмечена многочисленными исследованиями, направленными на выявление оптимальной конструкции газогенераторной установки. Статьи об испытательных автопробегах и новых разработках постоянно появлялись в прессе, в том числе и в журнале «За Рулем».
С + О2 = СО2 — это полное сгорание топлива, которое сопровождается выделением углекислого газа СО2;
и С + (1/2)О2 = СО — это неполное сгорание, в результате которого образуется горючий газ – оксид углерода СО.
Оксид углерода СО образуется также при прохождении углекислого газа СО2 сквозь слой раскаленного топлива:
С + СО2 = 2СО
В процессе участвует часть влаги топлива (или влага, подведенная извне) с образованием углекислого газа СО2, водорода Н2, и горючего оксида углерода СО.
С + Н2О = СО + Н2
СО + Н2О = СО2 + Н2
Зону, в которой протекают три описанных выше реакции называют «зоной восстановления» газогенератора. Обе зоны – горения и восстановления – несут общее название «активная зона газификации».
— водород Н2 16,1%;
— углекислый газ СО2 9,2%;
— оксид углерода СО 20,9%;
— метан СН4 2,3%;
— непредельные углеводороды СnHm (без смол) 0,2%;
— кислород О2 1,6%;
— азот N
Итак, генераторный газ состоит из горючих компонентов (СО, Н2, СН4, СnHm) и балласта (СО2, О2, N2, Н2О)
Топливо для газогенераторов
В качестве твердого топлива в газогенераторных установках могут быть использованы древесные чурки, древесный уголь, торф, бурый уголь, каменный уголь.
На территории СССР наиболее распространенным и доступным твердым топливом была древесина, по этому большую часть газогенераторного транспорта составляли автомобили с установками, работающими на древесных чурках.
Главные критериями качества топлива являлись порода древесины, абсолютная влажность и размеры чурок. Приоритет был отдан древесине твердых пород: березе, буку, грабу, ясеню, клену, вязу, лиственнице. Древесину мягких пород допускалось использовать лишь совместно с твердыми в соотношении 50/50. Сосновые чурки использовались без добавления древесины мягких пород.
Менее распространены были древесно-угольные газогенераторные установки. Для их эксплуатации рекомендовалось использовать угли древесины твердых пород. Угли древесины мягких пород, склонные к крошению, допускалось применять с добавлением не менее 50% углей древесины твердых пород. Размер кусков древесного угля для газогенераторов поперечного процесса — от 6 до 20 мм, для других типов генераторов – от 20 до 40 мм.
— газогенераторы прямого процесса газификации;
— газогенераторы обращенного (обратного, или «опрокинутого») процесса газификации;
— газогенераторы поперечного (горизонтального) процесса газификации.
Типы газогенераторов
Газогенераторы прямого процесса газификации
Основным преимуществом газогенераторов прямого процесса являлась возможность газифицировать небитуминозные многозольные сорта твердого топлива – полукокс и антрацит.
В газогенераторах прямого процесса подача воздуха обычно осуществлялась через колосниковую решетку снизу, а газ отбирался сверху. Непосредственно над решеткой располагалась зона горения. За счет выделяемого при горении тепла температура в зоне достигала 1300 – 1700 С.
Над зоной горения, занимавшей лишь 30 – 50 мм высоты слоя топлива, находилась зона восстановления. Так как восстановительные реакции протекают с поглощением тепла, то температура в зоне восстановления снижалась до 700 – 900 С.
В газогенераторах прямого процесса влага топлива не попадала в зону горения, поэтому воду в эту зону подводили специально, путем предварительного испарения и смешивания с поступающим в газогенератор воздухом. Водяные пары, реагируя с углеродом топлива, обогащали генераторный газ образующимся водородом, что повышало мощность двигателя.
— механический способ, когда вода подавалась в испаритель газогенератора с помощью насоса, приводимого в действие от двигателя и имевшего перепускной кран, который был связан с дроссельной заслонкой. Таким образом, количество воды, подаваемой в газогенератор, изменялось в зависимости от числа оборотов и нагрузки двигателя;
— гидравлический способ, когда расход воды регулировался иглой, перекрывавшей сечение жиклера, и связанной с мембраной, на которую действовала разность давлений до и после диафрагмы, установленной в газопроводе, соединявшим газогенераторную установку с двигателем;
— пневматический способ, при котором вода подавалась в испаритель газогенератора вместе с воздухом, засасываемым через обычный карбюратор.
В конструкции газогенератора ЦНИИАТ-АГ-2 был использован принцип центрального подвода воздуха и центрального отбора газа. Газогенератор состоял из корпуса, конической камеры газификации и зольника. Верхняя часть корпуса служила бункером для топлива и имела цилиндрический бак для воды. Трубка для подачи воды располагалась внутри газогенератора, бак подогревался теплом сгорающего топлива. Это обеспечивало надежную работу установки в зимнее время. Камера газификации представляла собой горловину конической формы, которая снизу была окружена рубашкой, заполненной водой для образования водяного пара. Необходимый уровень воды в рубашке поддерживался при помощи поплавкового устройства. Количество образовавшегося пара изменялось в зависимости от теплового режима газогенератора.
Воздух, засасываемый в газогенератор через подогреватель, смешивался с паром и поступал в камеру газификации через щель, образованную рубашкой и поворотной плитой. При вращении плиты рукояткой, расположенной снаружи под днищем газогенератора, ребра, имеющиеся на плите, срезали шлак и сбрасывали его в зольник.
Установки прямого процесса газификации не получили распространения, так как, во-первых, были непригодны для газификации самого распространенного твердого топлива — древесины, а во-вторых, потому что приспособления, необходимые для хранения, дозировки и испарения воды существенно усложняли конструкцию газогенератора.
Газогенераторы обращенного (опрокинутого) процесса газификации.
Газогенераторы обращенного процесса были предназначены для газификации битуминозных (смолистых) сортов твердого топлива – древесных чурок и древесного угля.
В генераторах этого типа воздух подавался в среднюю по их высоте часть, в которой и происходил процесс горения. Отбор образовавшихся газов осуществлялся ниже подвода воздуха. Активная зона занимала часть газогенератора от места подвода воздуха до колосниковой решетки, ниже которой был расположен зольник с газоотборным патрубком.
Зоны сухой перегонки и подсушки располагались выше активной зоны, поэтому влага топлива и смолы не могли выйти из газогенератора, минуя активную зону. Проходя через зону с высокой температурой, продукты сухой перегонки подвергались разложению, в результате чего количество смол в выходящем из генератора газе было незначительным. Как правило, в газогенераторах обращенного процесса газификации горячий генераторный газ использовался для подогрева топлива в бункере. Благодаря этому улучшалась осадка топлива, так как устранялось прилипание покрытых смолой чурок к стенкам бункера и тем самым повышалась устойчивость работы генератора.
Газогенератор ГАЗ-42 состоял из цилиндрического корпуса 1, изготовленного из 2-миллиметровой листовой стали, загрузочного люка 2 и внутреннего бункера 3, к нижней части которого была приварена стальная цельнолитая камера газификации 8 с периферийным подводом воздуха (через фурмы). Нижняя часть газогенератора служила зольником, который периодически очищался через зольниковый люк 7.
Воздух под действием разрежения, создаваемого двигателем, открывал обратный клапан 5 и через клапанную коробку 4, футорку 6, воздушный пояс и фурмы поступал в камеру газификации 8. Образующийся газ выходил из-под юбки камеры 8, поднимался вверх, проходил через кольцевое пространство между корпусом и внутренним бункером и отсасывался через газоотборный патрубок 10, расположенный в верхней части газогенератора. Равномерный отбор газа по всей окружной поверхности газогенератора обеспечивался отражателем 9, приваренным к внутренней стенке корпуса 1 со стороны газоотборного патрубка 10.
Для более полного разложения смол, особенно при малых нагрузках газогенератора, в камере газификации было предусмотрено сужение – горловина. Помимо уменьшения смолы в газе, применение горловины одновременно приводило к обеднению газа горючими компонентами сухой перегонки. На величину получаемой мощности влияла согласованность таких параметров конструкции газогенератора, как диаметр камеры газификации по фурменному поясу, проходное сечение фурм, диаметр горловины и высота активной зоны.
Газогенераторы обращенного процесса применяли и для газификации древесного угля. Вследствие большого количества углерода в древесном угле процесс протекал при высокой температуре, которая разрушительно действовала на детали камеры газификации. Для повышения долговечности камер газогенераторов, работающих на древесном угле, применяли центральный подвод воздуха, снижавший воздействие высокой температуры на стенки камеры газификации.
Камера газогенератора НАТИ-Г-15), изготовленная из 12-миллиметровой листовой стали, имела вид усеченного конуса. В средней части газогенератора была смонтирована воздухоподводящая фурма. Она представляла собой чугунную отливку грушевидной формы. Внутри отливки – лабиринт для подвода воздуха в газогенератор. В нижней части камеры газификации располагалась колосниковая решетка, которую вынимали через зольниковый люк при чистке и разгрузке газогенератора. Образовавшийся в камере газификации газ проходил сквозь колосниковую решетку, поднимался вверх между корпусом газогенератора и камерой и отсасывался через газоотборный патрубок. Газогенератор был предназначен для работы на крупном древесном угле, с размером кусков 20 мм – 40 мм.
Газогенераторные установки обращенного процесса газификации, работавшие на древесных чурках, получили наибольшее распространение.
Газогенераторы поперечного (горизонтального) процесса газификации.
В газогенераторах поперечного процесса воздух с высокой скоростью дутья подводился через фурму, расположенную сбоку в нижней части. Отбор газа осуществлялся через газоотборную решетку, расположенную напротив фурмы, со стороны газоотборного патрубка. Активная зона была сосредоточена на небольшом пространстве между концом формы и газоотборной решеткой. Над ней располагалась зона сухой перегонки и выше – зона подсушки топлива.
Отличительной особенностью газогенератора этого типа являлась локализация очага горения в небольшом объеме и ведение процесса газификации при высокой температуре. Это обеспечивало газогенератору поперечного процесса хорошую приспособляемость к изменению режимов и снижает время пуска.
Газогенератор представлял собой цилиндрический бункер, нижняя часть которого, выполненная из листовой стали толщиной 6 – 8 мм, образовывала камеру газификации. В верхней части бункера был расположен люк для загрузки топлива.
Скорость дутья определялась проходным сечением воздухоподводящей фурмы. Фурма служила наиболее ответственной и сложной деталью газогенератора. Она была глубоко погружена в слой топлива и находилась в зоне высокой температуры – непосредственно около носка фурмы температура достигает 1200 – 1300 С. Высокие температурные нагрузки требовали применять водяное охлаждение фурмы. Конструктивно охлаждение фурмы являлось частью системы водяного охлаждения двигателя, или представляло собой самостоятельную систему, питаемую от отдельного бачка.
Воздухоподводящая фурма газогенератора НАТИ-Г-21 состояла из бронзового корпуса 1 и медных трубок 2 и 3 диаметром 20 и 40 мм, образующих водяную рубашку. Тыльная часть наружной трубки 3 была приварена к корпусу 1 фурмы, а носовая часть обварена медью и соединялась с внутренней трубкой 2, свободный конец которой при нагревании фурмы мог перемещаться в сальнике 4. Затяжкой накидной гайки 5 обеспечивалась герметичность водяной рубашки. Вода подавалась через нижний штуцер корпуса фурмы и после прохождения водяной рубашки отводилась через верхний штуцер. Для того чтобы поток воды достиг носка фурмы, к наружной поверхности внутренней трубки параллельно ее оси были приварены две перегородки, направлявшие поток воды к носу фурмы.
Другой важной деталью газогенераторов поперечного процесса газификации служила газоотборная решетка. Газоотборную решетку изготавливали из простой углеродистой или легированной стали толщиной 8 – 12 мм. Ее штамповали в виде изогнутого листа с отбортованными краями или изготавливали в виде плоской пластины. В последнем случае для монтажа решетки в газогенераторе предусматривали специальное гнездо. Отверстия в решетке для прохода газа делали круглыми, диаметром 10 – 12 мм, с раззенковкой со стороны выхода газа. Иногда отверстия делали овальными; в этом случае большая ось овала располагалась горизонтально, что позволяло увеличить проходное сечение без опасности проскакивания за решетку кусков угля (при наклонном расположении решетки).
Этот газогенератор, так же как и газогенератор прямого процесса, был непригоден для газификации топлив с большим содержанием смол. Эти установки применяли для древесного угля, древесноугольных брикетов, торфяного кокса.
Принцип работы автомобильной газогенераторной установки
Автомобильная газогенераторная установка состояла из газогенератора, грубых очистителей, тонкого очистителя, вентилятора розжига и смесителя. Воздух из окружающей среды засасывался в газогенератор тягой работающего двигателя. Этой же тягой выработанный горючий газ «выкачивался» из газогенератора и попадал сначала в грубые очистители охладители, затем – в фильтр тонкой очистки. Перемешавшись в смесителе с воздухом, газо-воздушная засасывалась в цилиндры двигателя.
Охлаждение и грубая очистка газа
На выходе из газогенератора газ имел высокую температуру и был загрязнен примесями. Чтобы улучшить наполнение цилиндров «зарядом» топлива, газ требовалось охладить. Для этого газ пропускался через длинный трубопровод, соединявший газогенератор с фильтром тонкой очистки, или через охладитель радиаторного типа, который устанавливался перед водяным радиатором автомобиля.
Охладитель радиаторного типа газогенераторной установки УралЗИС-2Г имел 16 трубок, расположенных вертикально в один ряд. Для слива воды при промывке охладителя служили пробки в нижнем резервуаре. Конденсат вытекал наружу через отверстия в пробках. Два кронштейна, приваренные к нижнему резервуару, служили для крепления охладителя на поперечине рамы автомобиля.
В качестве простейшего очистителя использовался циклон. Газ поступал в очиститель через патрубок 1, распологавшийся касательно к корпусу циклона. Вследствие этого газ получал вращательное движение и наиболее тяжелые частицы, содержащиеся в нем, отбрасывались центробежной силой к стенкам корпуса 3. Ударившись о стенки, частицы падали в пылесборник 6. Отражатель 4 препятствовал возвращению частиц в газовый поток. Очищенный газ выходил из циклона через газоотборный патрубок 2. Удаление осадка осуществлялось через люк 5.
Чаще всего в автомобильных газогенераторных установках применяли комбинированную систему инерционной очистки и охлаждения газа в грубых очистителях – охладителях. Осаждение крупных и средних частиц в таких очистителях осуществлялось путем изменения направления и скорости движения газа. При этом одновременно происходило охлаждение газа вследствие передачи тепла стенкам очистителя. Грубый очиститель-охладитель состоял из металлического кожуха 1, снабженного съемной крышкой 2. Внутри кожуха были установлены пластины 3 с большим количеством мелких отверстий, расположенных в шахматном порядке. Газ, проходя через отверстия пластин, менял скорость и направление, а частицы, ударяясь о стенки, оседали на них или падали вниз.
Грубые охладители-очистители последовательно соединяли в батареи из нескольких секций, причем каждая последующая секция имела большее количество пластин. Диаметр отверстий в пластинах от секции к секции уменьшался (РИСУНОК 5Г).
Фильтры тонкой очистки
Для тонкой очистки газа чаще всего применяли очистители с кольцами. Очистители этого типа представляли собой цилиндрический резервуар, корпус 3 которого был разделен на три части двумя горизонтальными металлическими сетками 5, на которых ровным слоем лежали кольца 4, изготовленные из листовой стали. Процесс охлаждения газа, начавшись в грубых очистителях – охладителях, продолжался и в фильтре тонкой очистки. Влага конденсировалась на поверхности колец и способствовала осаживанию на кольцах мелких частиц. Газ входил в очиститель через нижнюю трубу 6, и пройдя два слоя колец, отсасывался через газоотборную трубу 1, соединенную со смесителем двигателя. Для загрузки, выгрузки и промывки колец использовали люки на боковой поверхности корпуса. Применялись конструкции, в которых в качестве фильтрующего материала использовалась вода или масло. Принцип работы водяных (барботажных) очистителей заключался в том, что газ в виде маленьких пузырьков проходил через слой воды и таким образом избавлялся от мелких частиц.
Высота барботажного слоя воды в очистителе установки ЦНИИАТ-УГ-1 повышалась от нуля до максимума (100 мм – 120 мм) по мере увеличения отбора газов. Благодаря этому обеспечивалась устойчивая работа двигателя на холостых оборотах и хорошая очистка газа на больших нагрузках. Предварительно охлажденный газ поступал расположенную по центру очистителя газораздаточную коробку. Боковые стенки коробки имели два ряда отверстий диаметром 3 мм. Отверстия были расположены наклонно от уровня воды до нижнего края стенок, погруженных в воду на 70 мм. Четыре отверстия, расположенные выше уровня воды, служили для обеспечения подачи газа на холостом ходу. С ростом числа оборотов эти отверстия перекрывались водой. В пространстве над газораздаточной коробкой при увеличении нагрузки создавалось разряжение, и уровень воды снаружи коробки повышался, а внутри, соответственно – понижался. При этом газ, поступая внутрь коробки, попадал в отверстия, расположенные над уровнем воды, и уже в виде пузырьков поднимался вверх, сквозь наружный водяной столб. Очистившись в воде, газ проходил через кольца, насыпанные на сетки по обе стороны газораздаточной решетки, и направлялся во вторую секцию очистителя, где вторично пропускался через погруженную в воду гребенку окончательно очищался в слое колец.
Вентилятор розжига
В автомобильных установках розжиг газогенератора осуществлялся центробежным вентилятором с электрическим приводом. При работе вентилятор розжига просасывал газ из газогенератора через всю систему очистки и охлаждения, поэтому вентилятор старались разместить ближе к смесителю двигателя, чтобы процессе розжига заполнить горючим газом весь газопровод.
Вентилятор розжига газогенераторной установки автомобиля УралЗИС-352 состоял из кожуха 6, в котором вращалась соединенная с валом электродвигателя крыльчатка 5. Кожух, отштампованный из листовой стали, одной из половин крепился к фланцу электродвигателя. К торцу другой половины был подведен газоотсасывающий патрубок газогенератора 4. Газоотводящий патрубок 1. Для направления газа при розжиге в атмосферу и при работе подогревателя – в подогреватель к газоотводящему патрубку был приварен тройник 3 с двумя заслонками 2.
Смеситель
Образование горючей смеси из генераторного газа и воздуха происходило в смесителе. Простейший двухструйный смеситель а представлял собой тройник с пересекающимися потоками газа и воздуха. Количество засасываемой в двигатель смеси регулировалось дроссельной заслонкой 1, а качество смеси – воздушной заслонкой 2, которая изменяла количество поступающего в смеситель воздуха.
Эжекционные смесители б и в различались по принципу подвода воздуха и газа. В первом случае газ в корпус смесителя 3 подводился через сопло 4, а воздух засасывался через кольцевой зазор вокруг сопла. Во втором случае в центр смесителя подавался воздух, а по периферии – газ.
Воздушная заслонка обычно была связана с рычагом, установленном на рулевой колонке автомобиля и регулировалась водителем вручную. Дроссельной заслонкой водитель управлял с помощью педали.
Методы уменьшения потерь мощности двигателей газогенераторных автомобилей
Бензиновые двигатели, переведенные на генераторный газ без каких-либо переделок, теряли 40-50% мощности. Причинами падения мощности являлись, во-первых, низкая теплотворность и медленная скорость горения газовоздушной смеси по сравнению с бензовоздушной, а во-вторых, ухудшение наполнения цилиндров как за счет повышенной температуры газа, так и за счет сопротивления в трубопроводах, охладителе и фильтре газогенераторной установки.
Для уменьшения влияния указанных причин в конструкцию двигателей были внесены изменения. В связи с тем что газовоздушная смесь обладает высокой детонационной стойкостью, была увеличена степень сжатия. Сечение впускного трубопровода было увеличено. Для устранения подогрева газовоздушной смеси и уменьшения потерь давления впускной трубопровод устанавливали отдельно от выпускного. Эти меры позволяли сократить потери мощности до 20-30%.
Эксплуатация автомобилей с газогенераторными установками
Эксплуатация автомобилей с газогенераторными установками имела свои особенности. В силу повышенной степени сжатия работа двигателя на бензине под нагрузкой допускалась лишь в крайних случаях и кратковременно: например, для маневрирования в гаражных условиях.
Инструкция категорически запрещала перевозить на газегенераторных автомобилях огнеопасные и легковоспламеняющиеся вещества, и тем более въезжать на территории, где не допускалось пользоваться открытым огнем – например, топливные склады. Разжигать газогенератор разрешалось только на открытой площадке.
Розжиг газогенератора осуществлялся факелом, тягу в при этом создавал электрический вентилятор. Газ, прокачиваемый вентилятором в процессе розжига, через патрубок выходил в атмосферу. Момент готовности газогенератора к работе определяли, поджигая газ у отверстия выходного патрубка – пламя должно было гореть устойчиво. По окончании розжига вентилятор выключали и пускали двигатель.
При неисправности вентилятора газогенератор можно было разжечь самотягой. Для этого зольниковый и загрузочный люки газогенератора открывали, а под колосниковую решетку подкладывали «растопку» — стружку, щепу, ветошь. Под действием естественной тяги пламя распространялось по всей камере. После розжига люки закрывали и пускали двигатель.
Розжиг газогенератора при помощи работающего на бензине двигателя допускался инструкцией лишь в аварийных случаях, так как при этом возникала опасность засмоления двигателя.
При движении автомобиля водитель вынужден был принимать во внимание инерцию газогенераторного процесса. Чтобы обеспечить запас мощности, необходимо было поддерживать отбор газа, близкий к максимальному. Для преодоления трудных участков рекомендовалось заранее переходить на понижающие передачи и поднимать обороты двигателя, а так же обогащать газо-воздушную смесь, прикрывая воздушную заслонку смесителя.
В отличие от бензиновых, газогенераторные автомобили требовали более частого пополнения топливом. Догрузку топлива в бункер производили в течение дня во время погрузочно-разгрузочных работ или стоянок.
Обслуживание газогенераторной установки было трудоемким. Чистка зольника газогенератора автомобиля УралЗИС-352 предусматривалась через каждые 250 – 300 км. Через 5000 – 6000 км газогенератор требовал полной чистки и разборки. Трубы охладителя рекомендовалось прочищать раз в 1000 км специальным скребком, входившим в комплект инструмента для обслуживания газогенераторной установки. Нижний слой колец фильтра тонкой очистки необходимо было промывать, выгрузив из фильтра на поддон, через 2500 – 3000 км пробега автомобиля. Верхний слой колец допускалось промывать каждые 10 000 км струей воды через люк в корпусе фильтра.
Оксид углерода СО опасен для человеческой жизни, по этому перед проведением работ по обслуживанию требовалось открыто все люки проветрить газогенераторную установку в течение 5 – 10 минут.
Дополнительные материалы:
За Рулем 1931 № 20 Автомобили на дровах
За Рулем 1933 № 16 Автомобили на дровах
За Рулем 1934 № 17 Газогенератор профессора Карпова
За Рулем 1935 № 1 Пробег газогенераторных автомашин
За Рулем 1935 № 2 Новый четырехосный газогенераторный автобус
За Рулем 1935 № 3 Первый автодоровский газогенератор
За Рулем 1935 № 14 Новый газогенератор для автомобиля ГАЗ-АА
wiki.zr.ru
Аппарат Киппа. Делаем СО2.
Можно долго спорить о необходимости углекислотной подкормки аквариумных растений. Это мой ответ.Существует несколько типов систем подачи СО2 в аквариум. Каждый из этих методов-систем имеет свои преимущества и недостатки. Я выбрал именно этот потому, что связываться с баллонной установкой на работе не позволили коллеги. Да и стоимость такой установки в десятки раз превышает данную, а установки бражечного типа были отметены из-за нестабильности выхода СО2 (нужна постоянная температура, а в межсезонные периоды для меня это просто не возможно).
Итак в отличии от браги, это генератор СО2 обеспечивает более стабильную подачу углекислого газа. Потому что гораздо удобнее реализовать равномерную добавку раствора лимонной кислоты к раствору соды, чем равномерный процесс брожения сахара.
Рецепт следующий 200 грамм соды + 200 мл воды. 200грамм лимонки + 600 мл воды. Каждый из растворов намешивается в 1,5 литровой «баклажке».
Фото комплекта поставки (с сайта, сам не догадался щелкнуть)все было так, кроме счетчика пузырьков, но за ту цену он и не предлагался.
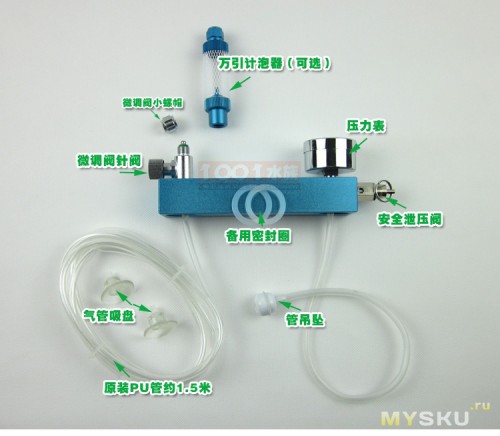
Собственно сам девайс представляет собой квадратный кусок легкого металла, выкрашенный в голубой цвет
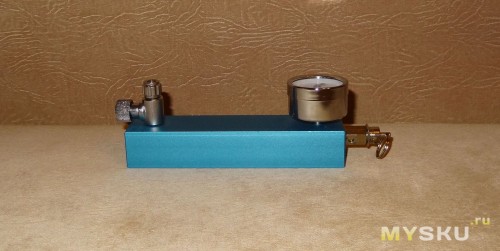
Имеется аварийный клапан, манометр и игольчатый кран
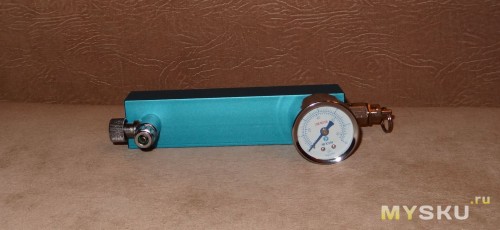
В отверстиях под горловину «баклажки» есть силиконовые прокладки (еще комплект идет в запасе)
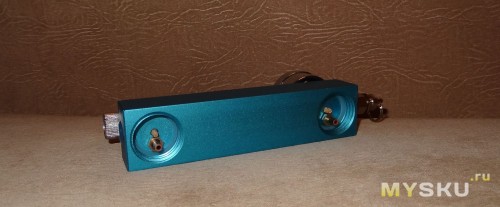
Обработка металла без заусенцев и прочих косяков.
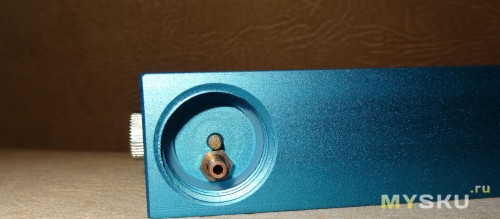
На кран одевается силиконовая трубочка подачи СО2 и герметизирующее зеленое колечко (в комплекте есть еще одно)
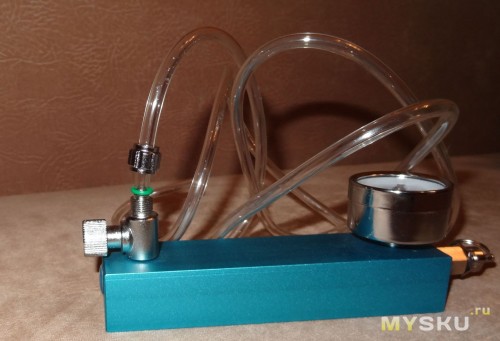
Все крутящееся и вкручивающееся имеет прокладочки
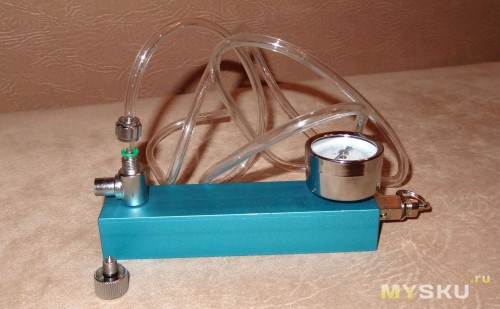
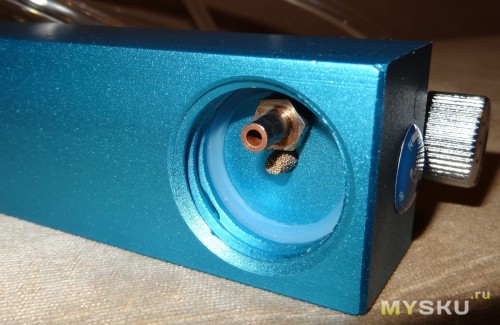
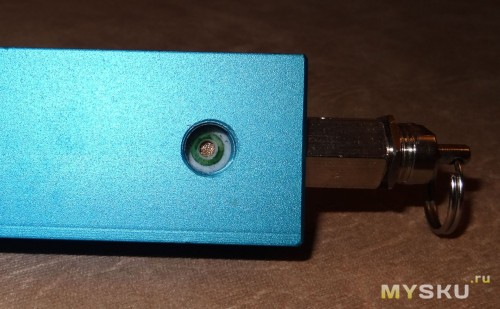
Манометр крупным планом. Давление в системе рекомендую поддерживать на уровне 1,5 кг/см2. Кстати, предохранительный клапан сработал при давлении 3 кг/cм2.
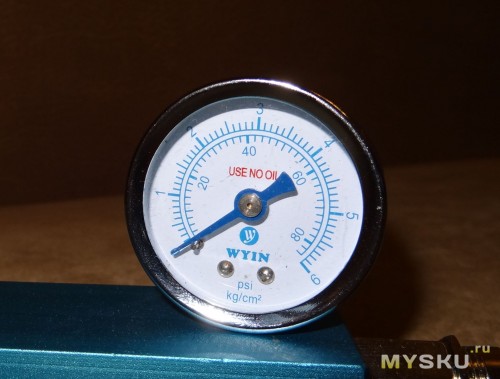
Кстати, настройку предохранительного клапана можно менять, но у меня в условиях производства ее можно проконтролировать при помощи поверенных приборов. Так что все на свой страх и риск.
Видео пробного «включения» (без соблюдения пропорции загружаемого материала).
В аквариуме успешно работает через ветку рябины уже третий день. Растения сразу начали пузырять. Полет нормальный.
Если начнете писать, что такое можно сделать самому — я это знаю! Делал несколько разных вариантов. Танцы с бубнами надоели. Купил простое и надежное решение от своей головной боли.
Вывод? Вывод один — при отсутствии должного терпения нужно брать!
mysku.ru
Промышленные газогенераторы: устройство и принцип работы
Промышленные газогенераторы для выработки электроэнергии используются на предприятиях для эффективной трансформации тепловой энергии в электрическую. Результат достигается за счет сжигания природного газа или другого газообразного топлива с высокой теплотворной способностью. Газогенераторные установки используются как для постоянного, так и для временного и резервного энергоснабжения.
Внутреннее устройство газогенератора
Схема устройства газогенератора крайне проста. Внутри установки располагается компрессор, камера сгорания, турбина и электрический двигатель. Внутри двигателя находится ротор и статор, а также обмотка, в которой возникает магнитное поле, когда ротор вращается вокруг оси. Также есть элементы управления. Различные виды газогенераторов имеют немного отличное друг от друга устройство, но в целом все так, как описано выше.
Помимо указанных выше элементов, устройство и работа генератора включает в себя пульт управления. Работа оборудования может управляться как вручную человеком, так и в автоматическом режиме. Например, можно настроить автоматическое подключение генератора в электрическую сеть сразу же после прекращения подачи электроэнергии из проводной электросети. Срабатывание происходит моментально.
Система охлаждения газогенератора
Независимо от назначения, газогенераторы в процессе работы достаточно сильно нагреваются. Чтобы нагрев не оказывал негативного влияния на оборудование, используется система охлаждения. Она бывает двух типов:
- Воздушное охлаждение. В промышленных установках практически не встречается, так как не может обеспечить должного охлаждения установки. Можно встретить в генераторах с мощностью до 15 кВт.
- Водяное охлаждение. Отличный вариант для охлаждения промышленных газогенераторов, мощность которых начинается от 20 кВт. Такое оборудование эффективно и не издает много шума при работе.
Можно купить газогенераторы для выработки электроэнергии с одной либо тремя фазами – это еще одна важная классификация газогенераторов для производства электрической энергии. Все промышленные газогенераторные установки способны выдавать трехфазное напряжение от 220 до 380 Вольт. Именно такой электрический ток потребляет промышленное оборудование, работающее преимущественно от трех фаз.
Принцип работы газогенераторного электрооборудования
Принцип работы газогенератора так же прост, как и его конструкция. Компрессор закачивает атмосферный воздух под давлением в камеру сгорания. Туда же поступает газообразное топливо, после чего смешивается с атмосферным воздухом. В результате образуется гремучая смесь, которая поджигается и детонирует внутри камеры сгорания. В ходе этой реакции образуется топочный газ, идущий на турбину и раскручивающий ее.
Процесс сгорания газообразного топлива осуществляется при постоянном высоком давлении. Камера сгорания используется для повышения температуры газа. Горячий газ обладает заметно большей энергией по сравнению с холодным или теплым, поэтому генератор работает более эффективно. Приблизительно 60% вырабатываемой турбиной электроэнергии направляется на вращение компрессора. Остальное уходит на включение генератора.
Мощность газогенератора в виде электрической энергии создается благодаря тому, что вал, соединяющий турбину и ротор, раскручивает ротор. В статоре образуется магнитное поле, а вместе с ним – электрический ток. Далее он через контакты и провода поступает к подключенным потребителям. Теперь вам известно внутреннее устройство и то, как работает газогенератор.
Топливо для работы промышленного газогенератора
Вы уже знаете принцип действия газогенератора – в его основе трансформация тепловой энергии сжигания газа в электрическую энергию. Главным образом для работы промышленных газогенераторов для электричества используется природный газ. Чаще всего в качестве топлива используется природный газ. Однако генераторы могут настраиваться на работу с другими видами газообразного топлива:
- Сжатый, сжиженный и магистральный природный газ – наиболее распространенный вариант.
- Пропан-бутановые смеси, характеризующиеся высокой теплотворной способностью.
- Коксовый, сточный, шахтный, пиролизный газ, а также газ, производимый в биореакторах.
В зависимости от того, какое именно газообразное топливо используется для работы газогенераторного оборудования, заметно изменяется мощность и производительность установки. Это надо учитывать при выборе типа топлива для работы промышленного газогенератора.
Конструкция газогенератора позволяет подключать его как к магистральному газопроводу, так и к автономным источникам газообразного топлива. Большинство моделей генераторов способны переключаться между разными видами топлива.
Как правильно выбрать оборудование?
Устройство газогенератора – не единственный фактор, на который важно обращать внимание при подборе той или иной модели для работы на предприятии. При выборе типа газогенератора надо учитывать:
- Класс защиты. Электрооборудование должно быть надежно защищено от попадания влаги, вибраций и механических повреждений, от проникновения пыли. Класс защиты обозначается как IP и две цифры. Чем выше значения обеих цифр, тем надежнее газогенератор защищен от внешних воздействий.
- Вариант исполнения. Газогенераторы электростанции могут размещаться как внутри помещений, так и снаружи в специальном боксе, либо на открытой площадке. Если планируется разместить оборудование под открытым небом, обязательно нужно позаботиться об установке бокса для защиты газогенератора.
- Мощность. Промышленные газовые генераторы характеризуются высокой мощностью, однако брать оборудование надо с запасом по мощности. Особенно если используется только один генератор. В среднем хватает запаса по мощности от 20% до 30% для стабильной работы.
Стоимость электрооборудования не должна становиться определяющим фактором при выборе газогенератора. Более того, многие газогенераторы заметно дешевле своих аналогов, работающих на бензине или дизельном топливе. Нельзя не отметить и низкую стоимость газообразного топлива. Благодаря этому можно выгодно купить газовый промышленный генератор и не иметь больших затрат при дальнейшей эксплуатации.
—
На нашем сайте Вы сможете найти промышленные газогенераторы, которые уже прошли проверку на качество и мощность в европейских странах. Все газогенераторы, представленные на сайте, находятся в исправном состоянии и обеспечиваются стабильную работу для промышленности.
leomaschinen.ru
Принцип работы газового генератора | Строительный портал
В поисках альтернативного источника энергии пришло понимание, что не обязательно добывать газ в шахтах, чтобы затем сжигать его в котлах и двигателях внутреннего сгорания, горючий газ можно добывать из отходов производства и древесины. Газогенератор или как его еще называют генератор газов путем сжигания местного топлива – дров, торфа, древесного угля, опилок и других отходов древесины, а также иногда других органических остатков способны выделять/генерировать горючие газы, такие как СО, СН4, Н2 и другие. Вариантов использования полученного газа несколько, но в любом случае в основу каждого устройства положен принцип газогенератора. О том, как работает газогенератор, из каких элементов он состоит, а также какие процессы проходят внутри него, мы расскажем в данной статье. Также рассмотрим варианты дальнейшего использования полученного газа и места, где можно устанавливать подобные агрегаты.
- Преимущества и недостатки генераторов газа
- Принцип работы газового генератора – газогенератора
- Типы газогенераторов
- Место установки газового генератора
- Дровяной газовый генератор своими руками
Итак, какие же существуют варианты использования газа, полученного в газогенераторе?
Первый – горючий газ направляется к газовой плите на кухне и используется для приготовления пищи. Второй – горючий газ сжигается сразу же в пиролизном котле отопления с газогенератором, соответственно, используется для отопления дома или теплиц. Кстати, подобные котлы могут называться газовым котлом на дровах, твердотопливным пиролизным котлом, газогенераторным котлом на дровах. Все они могут использоваться как для бытовых нужд, так и для отопления огромных производств и цехов или предприятий. Третий – горючий газ может направляться в двигатель внутреннего сгорания, который служит приводом насосной станции или генератора электроэнергии. Газовый генератор на дровах позволяет получать электроэнергию в тех регионах, где нет возможности провести линии электропередач, выполнить прокладку газопровода и затруднен подвоз газа в баллонах. Помимо автономности у газогенераторов есть и другие преимущества, которые мы раскроем ниже.
Преимущества и недостатки генераторов газа
В качестве примера рассмотрим преимущества и недостатки газогенераторных котлов отопления. Пиролизные котлы относятся к категории твердотопливных, но существенно отличаются от обычных печей на дровах или угле, где происходит обычный процесс сгорания топлива.
Преимущества газогенераторных котлов:
- КПД газогенераторных котлов находится в диапазоне 80 – 95 %, в то время как КПД обычного твердотопливного котла редко превышает 60 %.
- Регулируемый процесс горения в газогенераторном котле – одна закладка дров может гореть от 8 до 12 часов, для сравнения в обычном котле горение длится 3 – 5 часов. В газогенераторных котлах с верхним горением сгорание дров длится до 25 часов, а уголь может гореть 5 – 8 дней.
- Топливо сгорает полностью, поэтому чистить зольник и газоход приходится не часто.
- Благодаря тому, что процесс горения можно регулировать (мощность регулируется в диапазоне 30 – 100 %), работу котла можно автоматизировать, как например, газового или жидкотопливного.
- Выброс вредных веществ в атмосферу из газогенератора минимален.
- Газогенераторные котлы экономнее обычных.
- Топливо для газогенераторов не обязательно должно быть подсушено до 20 % влажности, существуют модели котлов, в которых можно использовать древесину до 50 % влажности и даже свежесрубленную.
- Возможность загрузки в котел неколотых поленьев до 1 м длиной и даже больше.
- Помимо дров и отходов древесной промышленности в пиролизных котлах можно утилизировать резину, пластмассу и другие полимеры.
- Высокая безопасность котла по сравнению с обычным твердотопливным котлом обеспечивается автоматикой и материалами, из которых изготовлен агрегат, а в особенности камеры сгорания.
Если говорить о газогенераторах, которые используются для производства электроэнергии, то они обладают точно такими же достоинствами, такими как экологичность, экономичность, высокий КПД, высокое октановое число 110 – 140, универсальность в плане используемого топлива и большая эффективность в зимнее время.
Недостатки газогенераторных котлов:
- На газовый генератор цена в 1,5 – 2 раза выше, чем на обычный твердотопливный котел.
- В большинстве своем газогенераторы энергозависимы, так как для подсоса воздуха используется вентилятор, но также существуют модели, которые могут работать и без электричества.
- Если использовать газогенераторный котел на мощности ниже 50 %, то наблюдается нестабильное горение – как результат выпадение в осадок дёгтя, который скапливается в газоходе.
- Температура обратки отопления не должна быть ниже 60 °С, иначе в газоходе будет выпадать конденсат.
- Обычно газогенераторы требовательны к влажности топлива, но как уже писалось выше, есть модели, в которых можно сжигать даже свежесрубленную древесину.
Других существенных недостатков газогенераторов не выявлено.
Кстати, газогенераторы – не такое уж и новое изобретение. Еще в середине прошлого века, когда большая часть нефтяных ресурсов Германии шла на вооружение, в качестве топлива для автомобилей использовались дрова. Даже на грузовые автомобили устанавливались газогенераторы. Современные агрегаты не слишком далеко ушли в своей конструкции, но, тем не менее, основательно усовершенствованы.
Принцип работы газового генератора – газогенератора
В генераторе газов или газогенераторе из твердого топлива добывается горючий газ. Основной секрет заключается в том, что в камеру сгорания подается воздух, объема которого недостаточно для полного сгорания топлива, при этом соблюдается высокая температура порядка 1100 – 1400 °С. Полученный газ охлаждается и направляется к потребителю или двигателю внутреннего сгорания, если, например, планируется добывать электричество. Более детально принцип работы газогенератора рассмотрим ниже, уточнив какой процесс в каком элементе агрегата происходит.
Устройство газового генератора на древесине
Рассмотрим устройство газогенератора бытового назначения. Сразу хотелось бы отметить, что пиролизные котлы с газогенератором отличаются от предложенной схемы, так как сгорание газа происходит внутри котла во второй камере сгорания. Мы же рассмотрим лишь сам газогенератор, на выходе из которого получается горючий газ.
Схема газогенератора:
Корпус газогенератора изготовлен из листовой стали и имеет сварные швы. Самая распространенная форма корпуса – цилиндрическая, но она вполне может быть и прямоугольной. К нижней части корпуса приварено днище и ножки, на которых будет стоять газогенератор.
Бункер или камера заполнения служит для загрузки внутрь газогенератора топлива. Он также имеет цилиндрическую форму и изготовлен из малоуглеродистой стали. Бункер установлен внутри корпуса газогенератора и закреплен болтами. На крышке люка, ведущего в бункер, на кромках использован асбестовый уплотнитель или прокладка. Так как асбест запрещен для использования в жилых помещениях, то существуют модели газогенераторов, уплотнители крышки которой изготовлены из другого материала.
Камера сгорания находится в нижней части бункера и изготовлена из жаропрочной стали, иногда внутренняя поверхность камеры сгорания отделывается керамикой. В камере сгорания происходит горение топлива. В нижней ее части происходит крекинг смол, для чего там установлена горловина, изготовленная из жаропрочной хромистой стали. Между корпусом и горловиной находится прокладка – уплотнительный асбестовый шнур. В средней части камеры сгорания находятся фурмы для подачи воздуха. Фурмы представляют собой калиброванные отверстия, которые соединяются с воздухораспределительной коробкой, связанной с атмосферой. Фурмы и распределительная коробка также изготавливаются из жаропрочной стали. На выходе из воздухораспределительной коробки установлен обратный клапан, который препятствует выходу горючего газа из газогенератора. Чтобы повысить мощность двигателя или иметь возможность использовать дрова повышенной влажности (более 50 %), перед воздухораспределительной коробкой можно установить вентилятор, который будет нагнетать внутрь воздух.
Колосниковая решетка служит для того, чтобы поддерживать раскаленные угли. Она располагается в нижней части газогенератора. Через отверстия решетки зола от сгоревших углей проваливается в зольник. Чтобы колосниковую решетку можно было очищать от шлака, ее средняя часть сделана подвижной. Для поворота чугунных колосников предусмотрен специальный рычаг.
Загрузочные люки оснащены герметично закрывающимися крышками. Например, верхний загрузочный люк откидывается горизонтально и уплотнен асбестовым шнуром. В креплении крышки есть специальный амортизатор – рессора, которая приподнимает крышку в случае избыточного давления внутри камеры. Сбоку корпуса есть также два загрузочных люка: один сверху – для добавления топлива в зону восстановления, второй снизу – для удаления золы. Отбор газа производится в зоне восстановления, поэтому чаще всего в верхней части газогенератора, но также возможно отведение газа и из нижней части агрегата. Отбор газа производится через патрубок, к которому приварены трубы газопровода. Не обязательно сразу же выводить газ за пределы корпуса газогенератора, пока он горячий, его можно использовать для подогрева и подсушивания дров или другого топлива в камере загрузки. Для этого отводящий газопровод проводится по кольцевой вокруг камеры, между корпусом газогенератора и бункером.
Фильтр «Циклон» и фильтр тонкой очистки располагаются за корпусом газогенератора. Они изготовлены из труб, наполненных фильтрующими элементами.
Прежде чем поступить в фильтр тонкой очистки, газ проходит через охладитель. А после фильтра тонкой очистки очищенный газ поступает в смеситель, где смешивается с воздухом. И только затем газо-воздушная смесь поступает в двигатель внутреннего сгорания.
Более наглядно последовательность движения горючего газа, после того как он вышел из газогенератора, показана на схеме ниже.
Дрова или другое топливо горит в камере сгорания, окисляясь воздухом, поступающим в камеру сгорания через фурмы из воздухораспределительной коробки. Полученный горючий газ поступает в фильтр Циклон, где очищается. Затем охлаждается в фильтре грубой очистки. Затем уже охлажденный газ поступает в фильтр тонкой очистки, а затем в смеситель. Из смесителя полученная смесь поступает в двигатель.
Процесс превращения топлива в газ
И все же: как из твердого топлива получается газ? Внутри газогенератора происходит некий процесс превращения, который разбит на несколько этапов, происходящих в разных зонах:
Зона подсушки находится в верхней части бункера. Здесь температура порядка 150 – 200 °С. Топливо подсушивается горячим газом, который движется по кольцевому трубопроводу, как было описано выше.
Зона сухой перегонки расположена в средней части бункера. Здесь без доступа воздуха и при температуре 300 – 500 °С топливо обугливается. Из древесины выделяются кислоты, смолы и другие элементы сухой перегонки.
Зона горения находится внизу камеры сгорания в зоне, где расположены фурмы, через которые поступает воздух. Здесь при подаче воздуха и температуре 1100 – 1300 °С обугленное топливо и элементы сухой перегонки сгорают, в результате чего образуются газы СО и СО2.
Зона восстановления находится выше зоны горения между колосниковой решеткой и зоной горения. Здесь газ СО2 поднимается вверх, проходит через раскаленный уголь, взаимодействует с углеродом (С) угля и на выходе образуется газ СО – окись углерода. В данном процессе также участвует влага из топлива, поэтому помимо СО образуется СО2 и Н2.
Зоны горения и восстановления называются зоной активной газификации. В результате генераторный газ состоит из нескольких компонентов:
- Горючие газы: СО (оксид углерода), Н2 (водород), СН4 (метан) и СnНm (непредельные углеводороды без смол).
- Балласт: СО2 (углекислый газ), О2 (кислород), N2 (азот), Н2О (вода).
Полученный газ охлаждается до температуры окружающей среды, затем очищается от муравьиной и уксусной кислоты, золы, взвешенных частиц и смешивается с воздухом.
Типы газогенераторов
Различают три типа газогенераторов: прямого процесса газогенерации, обратного и горизонтального.
Газогенераторы прямого процесса могут сжигать уголь полукокс и антрацит – топливо небитуминозное. Конструктивное отличие данного типа агрегатов в том, что воздух поступает через колосниковую решетку снизу, а забор газа производится сверху. В газогенераторах прямого процесса влага из топлива не попадает в зону горения, поэтому ее подводят специально. Обогащение генераторного газа водородом из воды повышает мощность генератора.
Газогенераторы опрокинутого или обращенного процесса предназначены для сжигания смолистого топлива – дров, древесного угля и отходов. Их конструктивное отличие в том, что воздух подается в среднюю часть – в зону горения, а забор газа производится ниже зоны горения – в зольнике. Обычно в агрегатах такого типа отобранный горячий газ используется для подогрева топлива в бункере.
Газогенераторы горизонтального или поперечного процесса газификации отличаются тем, что воздух в них подводится сбоку – в нижней части корпуса, причем подается он с высокой скоростью дутья через фурмы. Отбор газа производится напротив фурмы через газоотборную решетку. Активная зона газификации в газогенераторе горизонтального процесса очень мала и сосредоточена между концом фурмы и газоотборной решеткой. Время пуска такого генератора намного меньше, также он легко приспосабливается к смене режимов работы.
Место установки газового генератора
Газогенераторы и газогенераторные котлы отопления можно устанавливать как внутри жилых помещений, например, в подвалах и цокольных этажах, так и на улице.
Так называемые пеллетные котлы чаще всего устанавливают в доме, так как их загрузка не сопряжена с большим количеством мусора, а также мешки с пеллетами весят немного и могут храниться где-то рядом с котлом.
Газогенераторы на дровах, а в особенности на дровах большой длины, имеет смысл устанавливать на улице недалеко от места хранения дров. Так можно будет подвезти дрова на тачке непосредственно к котлу или газогенератору и не спускать их в подвал дома. Стоящий на улице котел избавляет от грязи и золы в подвале. Особенно это актуально для деревянных домов, где повышенные нормы пожаробезопасности. Внешний корпус котла изготавливается из нержавеющей стали, которая не подвержена коррозии. Также котлы теплоизолированы насыпной теплоизоляцией, чтобы температура окружающей среды минимально влияла на процесс газификации и скорость пуска котла. Система регулирования размещается в стальном кожухе под крышкой, чтобы на нее не попадали осадки. Дымовая труба имеет двойные стенки. Если вас интересует, как подключить газовый генератор, если он стоит на улице, то ответ прост – трубы прокладываются в земле, чтобы они минимально охлаждались, если это котел отопления. Трубы отопления подходят к котлу снизу, а сам котел устанавливается так, чтобы при длительных перерывах в использовании он не замерзал.
Кстати, как уже отмечалось, длительность процесса горения топлива в котле может быть от 12 часов и достигать 25 часов. В зависимости от мощности котла и площади отапливаемого помещения, его придется топить раз в два дня, а иногда и раз в неделю. Чтобы сохранить вырабатываемое котлом тепло на столь длительный период, используется теплоаккумулятор.
Дровяной газовый генератор своими руками
В том чтобы изготовить газогенератор своими руками, нет ничего сверхсложного. Многие используют такой агрегат для бытовых нужд или устанавливают на автомобиль. Перед тем как начать изготавливать газогенератор самостоятельно, необходимо ознакомиться с принципом его действия и выбрать подходящую для себя схему работы.
Понадобятся – бочка, трубы или старая батарея радиаторов, фильтры тонкой и грубой очистки газа, вентилятор. С другой стороны набор элементов может быть самым разным, все зависит от фантазии исполнителя.
Ниже посмотрите видео пример газогенератора самостоятельного изготовления.
Схема газогенратора:
В интернете можно найти как фото, так и чертежи по монтажу газовых генераторов и пиролизных котлов. Есть даже умельцы, которые берут за основу готовый проверенный котел и полностью повторяют его в домашних условиях. Получается дешевле намного.
Схема газогенераторного котла:
Отличие пиролизного котла от обычного газогенератора в том, что он состоит из двух камер сгорания: в одной сгорает топливо и образуется газ, а в другой – сгорает газ и находится теплообменник. Устройство и принцип работы газогенератора мы уже рассмотрели, добавьте в него только вторую камеру сгорания, которая должна располагаться вверху, и теплообменник сверху. Иногда теплообменник располагают сбоку. Также не забудьте о разных типах газогенераторов, так что вторая камера сгорания может находиться не только сверху.
При сборе дымохода постарайтесь собирать его в последовательности, обратной движению дыма, так на его стенках будет меньше оседать всякой гадости. Сам дымоход лучше сделать легкоразбираемым, чтобы его можно было легко и быстро чистить. Пространство вокруг котла отопления должно быть свободным, так как он нагревается в процессе работы. После монтажа котла придется изучить его «повадки» и подобрать оптимальный для себя режим работы, при котором сгорают все смолы.
Хотелось бы отметить, что газогенератор может рассматриваться не только как сжигатель полезной древесины, но и как утилизатор отходов. В нем можно сжигать остатки линолеума, пакетов, мешков, резины, пластиковых бутылок и другого бытового мусора.
strport.ru
Газогенератор для переработки твердого топлива в генераторный газ с целью получения газа, тепла и электроэнергии.
Газогенератор — оборудование, предназначенное для переработки твердого топлива с целью получения газа, пара, тепла и электроэнергии. Газогенератор «УГЛАС-800» — представитель нового поколения газогенераторов (2013 г.) в линейке оборудования для утилизации, представляемого компанией «Технокомплекс» от производителя «Железно».
В газогенераторе «УГЛАС-800» используются следующие виды сырья: уголь бурый, каменный, антрацит, торф, пиролизный углерод брикетированный, брикеты из угольной пыли (штыба) и шлама, брикеты из сельхозотходов (в том числе шелуха риса и гречи и других агрокультур, солома), птичий помет, навоз КРС, древесные отходы (в том числе кора, щепа, опилки). Во время газификации перечисленных выше видов топлива получают генераторный газ и тепло, а также электроэнергию при наличии электрогенератора.
Комплектация газогенератора «УГЛАС — 800» включает сам газогенератор, автоматическую линию подачи сырья и линию подготовки газа, приборы для регулировки температуры процесса и подачи газа в объемном соотношении, а также устройство автоматической выгрузки золы. Схема расположения газогенератора обычно привязывается к помещению, либо участку покупателя после заключения договора.
посмотреть все фото газогенератораТехнико-экономические показатели газогенератора «УГЛАС-800»
Сырье и производительность | ||
Потребление твердого топлива | тонн/сутки | 3,5 — 7,5 |
Фракция твердого топлива | мм | 20 — 60 |
Производительность по электроэнергии | кВт*час | 400-800 |
Производительность по тепловой энергии | кВт*час | 250-480 |
Режим работы и персонал | ||
Количество рабочих в смену | чел. | 1 |
Количество смен | шт./часы | 3х8, 2х12 |
Расчетное время работы в сутки | часы | круглосуточно, либо посменно |
Расчетное время работы в году | сутки | 330 |
Габаритные размеры и инфраструктура | ||
Габаритные размеры | мм | 5 700 х 2 400 х 2 300 |
Размер участка/рабочего цеха, необходимого для эксплуатации газогенератора |
мм | 5 000 х 8 000 |
Склад сырья | м2 | от 100 |
Коммуникации | ||
Необходимый объем воды (проточной или оборотной) |
м3 | от 12 |
Необходимая мощность при пиковой нагрузке |
кВт*час | 6,7 |
Потребление электроэнергии | кВт/мес. | 4 422 |
Газогенератор «УГЛАС-800» может использоваться следующим способом:
- — как самостоятельная единица оборудования для получения газа и тепла из твердого топлива и брикетированных сельскохозяйственных отходов;
- — как дополнительное оборудование к пиролизной установке «Пиротекс» для получения газа и тепла из брекетированного обуглероженного остатка;
- — в связке с дизельным или газопоршневым генератором для получения электричества.
Видео работы газогенератора «УГЛАС-800»
www.tkomplex.ru
|
Газогенератор, аппарат для термической переработки твёрдых и жидких топлив в горючие газы, осуществляемой в присутствии воздуха, свободного или связанного кислорода (водяных паров). Получаемые в газогенераторе газы называются генераторными. Горение твёрдого топлива в газогенераторе в отличие от любой топки осуществляется в большом слое и характеризуется поступлением количества воздуха, недостаточного для полного сжигания топлива (например, при работе на паровоздушном дутье в газогенератор подаётся 33—35% воздуха от теоретически необходимого). Образующиеся в газогенераторе газы содержат продукты полного горения топлива (углекислый газ, вода) и продукты их восстановления, неполного горения и пирогенетического разложения топлива (угарный газ, водород, метан, углерод). В генераторные газы переходит также азот воздуха. Процесс, происходящий в газогенераторе, называется газификацией топлива. Газогенератор обычно представляет собой шахту, внутренние стенки которой выложены огнеупорным материалом. Сверху этой шахты загружается топливо, а снизу подаётся дутьё. Слой топлива поддерживается колосниковой решёткой. Процессы образования газов в слое топлива газогенератора показаны на рис. 1. Подаваемое в газогенератор дутьё вначале проходит через зону золы и шлака 0, где оно немного подогревается, а далее поступает в раскалённый слой топлива (окислительная зона, или зона горения 1), где кислород дутья вступает в реакцию с горючими элементами топлива. Образовавшиеся продукты горения, поднимаясь вверх по газогенератору и встречаясь с раскалённым топливом (зона газификации II), восстанавливаются до окиси углерода и водорода. При дальнейшем движении вверх сильно нагретых продуктов восстановления происходит термическое разложение топлива (зона разложения топлива III) и продукты восстановления обогащаются продуктами разложения (газами, смоляными и водяными парами). В результате разложения топлива образуются вначале полукокс, а затем и кокс, на поверхности которых при их опускании вниз происходит восстановление продуктов горения (зона II). При опускании ещё ниже происходит горение кокса (зона 1). В верхней части газогенератора происходит сушка топлива теплом поднимающихся газов и паров. В зависимости от того, в каком виде подаётся в газогенератор кислород дутья, состав генераторных газов изменяется. При подаче в газогенератор одного воздушного дутья получается воздушный газ, теплота горения которого в зависимости от перерабатываемого топлива колеблется от 3,8 до 4,5 Мдж/м3 (900—1080 ккал/м3). Применяя дутьё, обогащенное кислородом, получают т. н. парокислородный газ (содержащий меньшее количество азота, чем воздушный газ), теплота горения которого может быть доведена до 5—8,8 Мдж {м3(1200—2100 ккал/м3). При работе газогенератора на воздухе с умеренной добавкой к нему водяных паров получается смешанный газ, теплота сгорания которого (в зависимости от исходного топлива) колеблется от 5 до 6,7 Мдж/м3 (1200—1600 ккал/м3). И, наконец, при подаче в раскалённый слой топлива газогенератора водяного пара получают водяной газ с теплотой сгорания от 10 до 13,4 Мдж/м3 (2400—3200 ккал/м3. Несмотря на то, что идея газогенератора была выдвинута в конце 30-х гг. 19 в. в Германии (Бишофом в 1839 и Эбельманом в 1840), их промышленное применение началось после того, как Ф. Сименсом (1861) был предложен регенеративный принцип отопления заводских печей, позволивший эффективно применять генераторный газ. Изобретателями первого промышленного газогенератора были братья Ф. и В. Сименс. Их конструкция газогенератора получила повсеместное распространение и просуществовала в течение 40—50 лет. Только в начале 20 в. появились более совершенные конструкции. В зависимости от вида перерабатываемого твёрдого топлива различают типы газогенераторов: для тощего топлива — с незначительным выходом летучих веществ (кокс, антрацит, тощие угли), для битуминозного топлива — со значительным выходом летучих веществ (газовые и бурые угли), для древесного и торфяного топлива и для отбросов минерального топлива (коксовая и угольная мелочь, остатки обогатительных производств). Различают газогенераторы с жидким и твёрдым шлакоудалением. Битуминозные топлива обычно газифицируются в газогенераторе с вращающимся водяным поддоном, а древесина и торф — в газогенераторе большого внутреннего объёма, т. к. перерабатываемое топливо имеет незначительную плотность. Мелкое топливо перерабатывается в газогенераторе высокого давления и во взвешенном или кипящем слое. По назначению газогенераторы можно разделить на стационарные и транспортные, а по месту подвода воздуха и отбора газа на газогенераторы прямого, обращенного и горизонтального процесса. В газогенераторе прямого процесса (рис. 2) движение носителя кислорода и образующихся газов происходит снизу вверх. В газогенераторе с обращенным процессом (рис. 3) носитель кислорода и образующийся газ движутся сверху вниз. Для обеспечения обращенного потока средняя часть таких газогенераторов снабжается фурмами, через которые вводится дутьё. Так как отсасывание образовавшихся газов осуществляется снизу газогенератора, то зона горения 1 (окислительная) находится сразу же под фурмами, ниже этой зоны следует зона восстановления II, над зоной горения 1 располагается зона III — пирогенетического разложения топлива, происходящего за счёт тепла раскалённого горящего кокса зоны 1. Сушка самого верхнего слоя топлива в газогенераторе происходит за счёт передачи тепла от зоны III. В газогенераторе с горизонтальным процессом носитель кислорода и образующийся газ движутся в горизонтальном направлении. При эксплуатации газогенератора соблюдается режим давления и температуры, величина которых зависит от перерабатываемого топлива, назначения процесса газификации и конструкции газогенератора. Бурное развитие газовой промышленности в СССР привело к почти полной замене генераторных газов природными и попутными, т. к. себестоимость последних значительно ниже. В зарубежных странах, где мало природного газа, газогенераторы широко применяются в различных отраслях промышленности (ФРГ, Великобритания).
Лит.: Михеев В. П., Газовое топливо и его сжигание, Л., 1966. Н. И. Рябцев
Рис. 3. Схема газогенератора с обращённым процессом газификации топлива. Рис. 2. Газогенератор прямого процесса для получения смешанного газа: 1 — загрузочное устройство; 2 — шахта; 3 — водяная рубашка; 4 — колосниковая решётка; 5 — фартук; 6 — чаша с водой, образующая гидравлический затвор; 7 — выгребной нож; 8 — конвейер для удаления золы; 9 — дутьевая коробка. Рис. 1. Схема прямого процесса образования газа в газогенераторе. |
www.xumuk.ru
ООО «Экосинтез» — Газогенератор, генератор синтез газа. Получение генераторного газа, синтез газа.
Реактор генераторного газа или синтез газа, по сути это одно и тоже просто в процессе получения синтез газа мы имеем еще и водород, сам же реактор дополняется только лишь подводкой пара в зону реакции. Что мы видим в сравнении с теплотворностью метана (природного газа) Метан в районе 8000-8500 ккал/м3 Генераторный газ – 1000-1350 ккал/м3 Синтез газ- до 2700 ккал/м3 Если разбить на зоны, весь процесс происходящий в реакторе, то мы увидим зону окисления воздушным дутьем, это зона горения, зону раскаленного углерода где происходит реакция восстановления СО2 в СО и реакцию где пар превращается в СО и Н2 , выше же получаем зону нагрева сырья, то есть там как раз идет пиролиз и выделение летучих которые вместе с СО и Н2 создают газовую смесь, которую можно отправить на дизель генератор. Но при отправке в реактор Фишера Тропша для получения синтетических топлив нужно «промывать» газ где получим отходы, для реактора оптимальный вариант обуглероженная древесина, торф- из них мы получаем чистый синтез газ без отходов.
.
Данная схема показывает зоны реакции и принцип работы реактора.
1. Зона горения сырья.зона.
2. Зона раскаленного углерода, где происходит восстановление СО2 в СО и разложение Н2О на СО и Н2.
3. Зона пиролиза, то есть так как кислород сгорает в зоне 1 то в зоне 3 идет реакция нагрева без кислорода, то есть пиролиз и возгонка летучих —
в первую очередь метана, этана и этилена и т.д. в зависимости от сырья…
4. Сырье.
5. Паровоздушное дутьё.
6. Загрузка сырья.
7. выход генераторного газа, либо синтез газа, либо смеси синтез газа с летучими, зависит от конструкции сырья.
Далее, сам реактор должен состоять из реактора системы золоудаления и системы очистки полученного газа. Система золоудаления, довольно сложный момент и зависит от сырья, сырье при сгорании которого получается рассыпчатая зола выводится сквозь колосники вниз в водяной затвор, а часть с потоком газа где проходя через циклон осаждается в золоуловителе. Данный момент прошел испытания практически, и показал что золоудаление по такой системе работает эффективно без сбоев. Далее, система очистки получаемого газа состоит из вертикальной трубы где в противоток газу идет водяной душ, и очищает газ от вкраплений мелкой золы, остатков пара и смол, а так же если смешивать воду с щелочью, известковать её то можно снизить кислотность газа. Реактор может запускаться автономно используя минимум энергии, то есть от какого то небольшого генератора тока, для этого подходит схема отработанная мной на реакторе где весь процесс обеспечивается маломощным вентилятором высокого давления, 2.5 квт, 220 вольт, который соединен с частотным преобразователем который дает возможность изменять производительность вентилятора, т.е. подачу воздуха, которая нужна для того что определить оптимальный вариант подачи воздуха в реактор. НО!!!! При использовании данной схемы сырье должно быть кусковым, то есть при работа вентилятора воздух должен проходить сквозь сырье, а это может дать кусковое сырье но не коем случае не пылевидное или очень мелкое смешанное с пылью, которое не даст прохода воздуха при такой мощности вентилятора. Если мы все же используем более мелкое и пылевидное сырье, тогда вентилятор должен быть мощнее, и конечно потребление электроэнергии будет выше, и принцип работы уже будет в «кипящем слое». При переработке сырья типа древесины, сланцев , торфа, и т.д мы получаем парогазовую смесь смешанную с синтез газом, так как в зоне 3 протекает в принципе низкотемпературный пиролиз, и чем больше парогазовой смеси дает сырье, тем с одной стороны больше теплотворность газа, но с другой стороны при охлаждении его мы получаем жидкие сконденсированные продукты. Поэтому конструкция должна предусматривать если очистку и охлаждение синтез газа то и отвод и удаления сконденсированных продуктов, разделение их от вкраплений золы, разделения от воды в варианте скруббера и так далее..то есть от применяемого сырья зависит не только золоудаление но и конечный продукт и возможно дополнительные узлы очистки, охлаждения, разделения, отстаивания, чистки, обслуживания. Поэтому и писал выше что оптимальный вариант для получения чистого синтетического газа это обуглероженный продукт, где все смолы уже отсутствуют.
Варианты конструкции. На данном этапе определяемся по конструкции самого реактора и системе очистки газа, тут несколько моментов, первое, ручная загрузка реактора, либо механическая, ручная выгрузка золы , либо механическая. Для того чтобы определится описываю момент загрузки сырья в реактор.
- Простейший способ: В процессе работы частотным преобразователем устанавливается минимальная скорость производительность вентилятора и открывается верхний люк реактора куда в ручную загружается сырье, метод простой но требует остановки реактора на момент загрузки что ведет к остановки и дизель генератора, и требует увеличения объема самого реактора чтобы как можно меньше было остановок, данный реактор дает безостановочную работу в районе 3.5-4.5 часа , так же продолжительность работы реактора зависит и от сырья, влажности сырья, максимальная влажность сырья не должна превышать 30- 40 процентов, пуск системы должен происходить на сырье влажностью не более 20 процентов.
- Следующий способ это шнековая подача, тут надо знать размер кусков сырья, шнек подачи для такого оборудования делается под заказ, но по сути его можно установить после того как испытали систему, если он нужен.
Данный реактор без системы тонкой очистки газа в действии, пламя это горит синтез газ, мощность данного реактора 0.7 МВт.
Загрузка реактора сырьем через люк, который расположен в верхней части реактора.
Пуск реактора, через люк укладываются дрова, зажигаются, включается дутье вентилятором, люк закрывается, рабочее же сырье засыпается через верхний люк.
Парогенератор который так же работает на твердом топливе и обеспечивает реактор паром для получения синтез газа.
Внутренняя часть реактора.
Данный реактор синтез газа потребляет: 1. обуглероженной древесины (древесного угля)- 110-120 кг в час. 2. Пара — замеров не былло. 3. Электричество- вентилятор высокого давления 2.5 квт потребления в час. Получаем 0.7 МВт приблизительно тепловой энергии. электрической возможно получить 150-200 квт. при присоединении ДВС с электрогенератором. Ну и получение синтетических жидких топлив при работе с реактором Фишера Тропша на катализаторах.
видео работы реактора синтез газа:
Ну немножко информации из «Технологии лесохимических производств , издательство»Лесная промышленность «, Москва 1970 год А.К. Славянский, Ф.А.Медников.
Как видите из приведенных выше сканов , данные газогенераторы сложнее, я пошел по пути использования обуглероженного сырья… то есть у меня меньше аппаратного обеспечения для очисти генераторного газа либо синтез газа, хотя возможно проектирование и изготовление и на щепе… конечно и на другом сырье.
Немного добавлю сканов, специально разместил титульный лист справочника , что бы было понятно, как давно человечество занимается этим направлением — получение энергетики таким вот способом!
Ну и вот предварительная предпроектная схемка недорогого реактора сравнительно, мощностью 1.5 мегаватта с потреблением сырья по углероду 200 кг в час.
ну а ниже схема небольшого газогенератора для так скажем бытовых нужд,данный газогенератор можно спроектировать от 1.5 до 3 метров высотой, и он может питать ДВС который будет крутить электрогенератор или водяной насос, либо расположен в кузове грузовика.
Ну а тут компактная схема газогенератора для питания ДВС .
1. Газогенератор (бункер)
2. Съемная часть бункера.
3. Реактор газогенератора.
4. Расширитель зольник газогенератора.
5. Парогенератор на твердом топливе типа РИ 5 м.
6. Контейнер 20 футовый размер 6058х2438х2915(высота)
7. Вентилятор высокого давления газогенератора.
8. Вентилятор охлаждения системы фильтрации газа.
9. Шнек подающий топливо в газогенератор.
10. Шнек удаляющий золу с газогенератора.
11. Шкаф управления .
12. Фланцы соединяющие сборный бункер.
13. Блок грубых фильтров системы фильтрации генераторного газа.
14. фильтрующий элемент с возможностью механической очистки и промывания.
15. Фильтр тонкой очистки генераторного газа, с удалением влаги.
16. Пространство контейнера куда укладываются шнеки и съемная часть бункера, инструмент, соединяющие шланги.
2. Принцип работы установки.
Контейнер(6) устанавливается на ровную площадку, открываются технологические люки, монтируется съемная часть бункера(2), шнеки(9,10).
В реактор газогенератора (3) закладывается легко поджигаемое топливо, типа сухой щепы, поджигается через открытое технологическое отверстие, вентилятор поддува(7) пускается на минимальный ход. После того как щепа разгорается идет подача топлива в бункер(1, 2) через шнек(9) до полной загрузки. А далее после устойчивого горения прибавить ход вентилятора(7) и засыпать полный бункер.
В подающий шнек(9) загружается топливо и подается в бункер до полной загрузки, мерная часть — сам бункер
шнека.
Шнек выгружающий(10) закрыт.(На рисунке шнеки изображены схематически.)
Так же запускается парогенератор ( описание эксплуатации парогенератора в инструкции по эксплуатации парогенератора.)
Поступление пара в реактор регулируется вентилем, излишки пара уходят в атмосферу.
Рабочий режим газогенератора считать при протекании стабильной незатухающей реакции с выходом нужного к-ва газа и нужной его калорийности в пределах норм. К-во газа регулируется частотным преобразователем, который определяет обороты вентилятора поддува (7) и находится в шкафу управления(11). Калорийность при добавлении пара увеличивается но при избытке возможна затухающая реакция.
Принцип работы газогенератора состоит в том что топливо загружается в приемный бункер(9) и попадает в реактор газогенератора(3), где происходит реакция восстановления СО2 в СО плюс при добавлении пара разложение воды на водород и кислород,, а так же уменьшение доли азота, что дает дополнительную калорийность газа. И чем больше газа нужно получить тем стабильнее реакция. Калорийность газа следующая: Генераторный газ до 990 ккал м3, синтез газ(смешанный газ) до 1630 ккал на м3.
После получения (восстановительная реакция) газа в ректоре газогенератора(3) газ поступает в зольник расширитель(4), куда так же поступает и зола с реактора газогенератора (3). Зола выгружается с помощью шнека (10), а газ поступает в блок грубой очистки ( 13), где фильтра связаны с собой последовательно, фильтры (14)выемные с возможностью очистки. После грубой очистки газ поступает в фильтр тонкой очистки газа (15), где дополнительно очищается и обезвоживается и далее поступает на ДВС либо другому потребителю.
Ну а это газогенераторный ЗиЛ 130, т.е. машина едет на дровах:
Ну вот дорогие друзья, коллеги и товарищи… добавлю немножко интересного материала, добавляю сканы чтобы было понятно что это не моя отсебятина: Обложка справочника:
Москва , «Лесная промышленность» 1990 год.
ну вот как бы, наслаждайтесь!
тел: 8-911-281-95-62 Суслов Михаил Борисович, ООО «Экосинтез», Санкт-Петербург. Электронная почта для связи: [email protected]
suslovm.ucoz.ru