Конструкция доменной печи и вспомогательных устройств :: Технология металлов
Современные доменные печи имеют большие размеры — общая высота их достигает 70 м,объем — 2700 м2 и более, а производительность — более 5000 тчугуна в сутки.
Рис 1. Схема типовой доменной печи (вертикальный разрез):
1 — малый конус, 2 — большой конус, 3 — газоотводные трубы 4 — флюс, 5- кокс, 6 — руда, 7 — кожух, 8 — капли чугуна 9-капли шлака, 10 — броня, 11 — шлаковая летка, 12 -желоб для выпуска шлака, 13 — лещадь, 14-желоб для выпуска чугуна, 15 — чугунная летка, 16 — жидкий шлак, 17 — фурмы, 18-кольцевой воздухопровод, 19 — опорное кольцо, 20 — огнеупорная кладка
Доменная печь представляет собой печь шахтного типа, состоящую из колошника I (рис 1.), шахты II , распара III, заплечиков IV и горна V.
В колошник — верхнюю цилиндрическую часть печи — при помощи засыпного аппарата загружают шихтовые материалы(кокс, агломерат и частично руду с флюсом), называемые шихтой; там же находится загрузочно-распределительное устройство, обеспечивающее правильное распределение материалов шихты в печи и предотвращающее утечку газов.
К колошнику прикреплены газоотводные трубы, через которые отводят колошниковый газ. Температура в колошнике — от 150 до 300 ° С.
Шахта II имеет форму усеченного конуса, расширяющегося книзу. Это самая большая часть печи. В шахте происходят высушивание руды, выделение химически связанной воды, растрескивание руды и начинается восстановление ее окислов. Температура в шахте на разной высоте от 350 до 1200° С.
Распар III имеет цилиндрическую форму и является самой широкой частью доменной печи. В распаре начинаются шлакообразование и плавление металла. Температура в этой зоне около 1400° С и выше.
Заплечики IV имеют форму усеченного конуса, сужающегося книзу. В них происходит дальнейшее расплавление металла и шлака. Температура достигает 1600—1800—1900° С.
В верхней части горна V расположены фурмы 17 — устройство для вдувания в печь горячего воздуха, обеспечивающего горение топлива. Фурмы расположены по окружности горна. У доменных печей их бывает шестнадцать и больше.
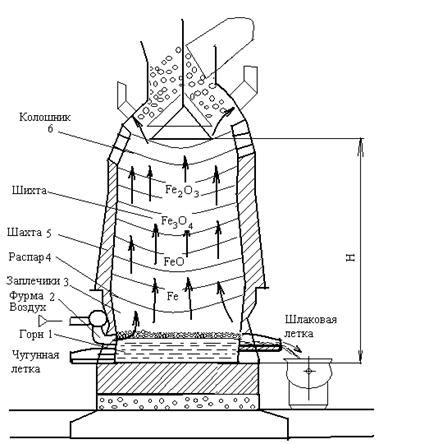
Вспомогательные устройства доменных печей должны быть надежны в работе для бесперебойного обслуживания печей в течение 5—7 лет. К их числу относятся: подъемные и загрузочные механизмы, литейные дворы и поддоменники, воздухонагреватели, воздуходувные машины и газоочистители.
Воздухонагреватели (рис. 2) предназначены для нагрева поступающего в доменную печь воздуха с целью ускорения процесса плавки путем получения в горне высокой температуры при меньшем расходе топлива.
Действие воздухонагревателя (см. рис. 2) следующее. Нагрев производится сжиганием доменного газа, поступающего в горелку 5, где газ смешивается с воздухом и сгорает.
Пламя поднимается по камере 1, проходит через каналы кирпичной насадки, раскаляет ее и выпускается через дымовую трубу 3.
После нагрева насадки ~до 1500° С через устройство 4 вводят наружный воздух. Проходя через насадку, он нагревается до 1000 — 1200° и поступает в доменную печь.
Рис. 2. Воздухонагреватель:1 — вертикальная камера, 2— насад, ка из огнеупорного кирпича, 3— дымовая труба, 4— устройство для нагнетания холодного воздуха, 5— газовая горелка, 6— выход нагретого воздуха
Источник:
Н.Н. Остапенко, Н.Н Крапивницкий «Технология металлов» М 1970
Устройство доменной печи: схема, принцип работы, видео
Доменная печь предназначена для выплавки чугуна.
Схема доменного процесса.
Суть этого процесса состоит в том, что в печи происходит восстановление оксидов железа, которые находятся в исходном материале – руде, продуктами сгорания топлива – водородом, оксидом углерода и твердым углеродом. Устройство доменной печи шахтного типа не отличается большой сложностью. Она состоит из нескольких деталей.
Конструкция печи
Верхняя часть доменной печи называется колошником. Он оборудован газоотводами, служащими для удаления колошникового газа. Сюда посредством специального засыпного аппарата загружается сырье.
Под колошником располагается шахта, имеющая вид усеченного конуса, расширяющегося книзу. Такая форма позволяет упростить процесс поступления в нее сырья из колошника. В шахте специальным образом подготавливается исходное сырье из окислов руды восстанавливается железо.
Самая широкая часть доменной печи носит название распар. Здесь плавится пустая порода флюса и руды, за счет чего из них получается шлак.
Следующая часть печи представляет собой усеченный конус, расширяющийся кверху. Называется она заплечики. В этом отделении конструкции заканчивается шлакообразование, оставляя в нем некоторое количество флюса и твердого топлива.
Горение поступившего сверху топлива происходит в горне. Он также служит для накопления чугуна и шлака, которые находятся в жидком состоянии.
Чтобы происходило сжигание топлива, необходим горячий воздух. Он поступает в печь от воздухонагревателей посредством кольцевого воздуховода, проходя через фурмы. Дно горна, носящее наименование лещадь, располагается на массивном фундаменте из железобетона. Здесь происходит накапливание шлака и чугуна. По окончании процесса плавки чугун и шлак выпускаются по специальным желобам через летки, предназначенные для этого, в ковши.
Вернуться к оглавлению
Принцип работы доменной печи
Схема доменной печи.
Конструкция доменной печи устроена таким образом, что шихта попадает в чашу через засыпное устройство, выполненного в виде небольшого конуса, расположенного вверху. Далее из чаши, попадая на большой конус при его опускании, шихта поступает в печь. Такая система не позволяет газу из доменной печи проникать в окружающую среду. После загрузки малый конус и воронка для приема сырья поворачиваются на угол, кратный 60 градусам. Это необходимо для того, чтобы шихта распределялась равномерно.
Металлургическая печь продолжает работать, шихта расплавляется и спускается дальше вниз, освобождая место для новых порций сырья. Полезный объем домны должен быть всегда полностью заполнен. Современная доменная печь может иметь полезный объем от 2000 до 50000 м³. Ее высота может достигать 35 м, что почти втрое больше ее диаметра. Такая конструкция придумана неслучайно: принцип работы доменной печи основан на движении материалов и газов навстречу друг другу, что позволяет увеличивать использование тепла до 85%.
Горн и лещадь выполняются из кирпича, имеющего в своем составе большое количество глинозема или из углеродистых блоков. Они расположены внутри стального кожуха и постоянно в процессе работы охлаждаются водой, поступающей по двум водопроводным системам из холодильников особой конструкции. Причем когда первая система работает, вторая в это время находится в резерве. Заплечики, шахта и распар изготавливаются из шамотного кирпича.
Колошник отделан плитами из стали, полости внутри которых полностью заполнены шамотом, а купол печи – плитами из чугуна.
Вернуться к оглавлению
Дополнительные элементы доменной печи
Устройство доменной печи схема.
В процессе работы требуются вспомогательные устройства и механизмы, обеспечивающие качественную плавку чугуна. Необходимыми являются устройства для подъема и загрузки исходного сырья в печь.
Доменная печь требует постоянного обслуживания, особенно при выпуске шлака и чугуна. Для этого приспособлены литейные дворы, которые оборудованы мостовыми кранами. Нагрев воздуха для работы печи, высокая температура плавки при меньшем количестве воздуха обеспечивают воздухонагреватели. К примеру, в печь, имеющую полезный объем 2000 м³, такое оборудование должно подавать в минуту 3800 м³ воздуха, температура которого составляет 1200 градусов. Пар, образующийся за счет поступления воздуха в воздухонагреватель, должен быть постоянно влажным. Значение этого показателя регулируется при помощи автоматической системы.
Сжатый воздух, который необходим для сжигания топлива, направляют в печь вихревые воздуходувки. Его давление на колошнике у современных печей достигает 25 МПа. Очистка колошникового газа происходит посредством газоочистителя.
Вернуться к оглавлению
В чем заключается доменный процесс
Устройство доменной печи:1. Горячее дутьё.2. Зона плавления (заплечики и горн).3. Зона восстановления FeO (распар).4. Зона восстановления Fe2O3 (шахта).5. Зона предварительного нагрева (колошник).6. Загрузка железорудных материалов, известняка и кокса.7. Доменный газ.8. Столб железорудных материалов, известняка и кокса.9. Выпуск шлака.10. Выпуск жидкого чугуна.11. Сбор отходящих газов.
Для успешной плавки чугуна в доменной печи должны всегда соблюдаться основные моменты. Во-первых, температура по всему объему печи и тепло должны обеспечивать протекание требуемых реакций в нужном месте и в определенное время. Это происходит за счет движения навстречу друг другу двух потоков. Газ от сгорания топлива поднимается снизу вверх, а шихта, нагревающаяся теплом газа, спускается сверху вниз. Во-вторых, шлак должен образовываться только тогда, как закончится восстановление железа и необходимых примесей из руды. Здесь важно правильно подобрать тугоплавкость шлака сорту чугуна. Это необходимо для того, чтобы шлак преждевременно не сплавил руду, что приведет впоследствии к изменению состава чугуна и может вызвать сбой в процессе плавки.
Началом данного процесса является горение топлива. При взаимодействии с кислородом, природный газ и углерод кокса сгорают, образуя значительное выделение тепла.
C + O2 = CO2 + Q; CH4 + 2O2 = CO2 + 2H2O + Q
Происходит взаимодействие продуктов сгорания с коксом в соответствии с реакциями:
CO2 + C = 2CO – Q; H2O + C = CO + H2 – Q
В этой смеси окись углерода – главный восстановитель железа из оксидов железа. Чтобы увеличить производительность печи, воздух, поступающий в печь, увлажняют, за счет чего увеличивается количество восстановителя. При поднятии газы, температура которых достаточно высока, нагревают шихту. Сами они при этом охлаждаются приблизительно до 300-400 градусов. Шихта двигается вниз навстречу газу. Когда температура достигнет приблизительно 570°С, происходит восстановление оксидов железа. Этот процесс состоит из нескольких последовательных этапов по схеме: Fe2O3 -> Fe3O4 -> FeO -> Fe.
Эти химические реакции определяет температура. Восстановление оксида железа происходит твердым углеродом (прямое восстановление), водородом и оксидом углерода (косвенное восстановление). В первом случае процесс осуществляется в зоне распара при наличии высоких температур в соответствии с реакцией: FeO + C = Fe + CO – Q.
Во втором случае, при косвенном восстановлении, реакция происходит при более низкой температуре в верхней части печи: 3Fe2O3 + CO = 2Fe3O4 + CO2 + Q; Fe3O4 + CO = 3Fe O + CO2 – Q; Fe O + CO = Fe + CO2 + Q.
Вернуться к оглавлению
Образование шлака
При требуемой температуре железо, восстановленное из руды, при определенных реакциях растворяет углерод. За счет этого происходит снижение температуры плавления, и железо расплавляется при температуре приблизительно 1300°С. Получившийся сплав, соприкасаясь с коксом, насыщается такими элементами, как кремний, фосфор, углерод, марганец, восстанавливаемые из руды. Насыщение серой происходит при температуре 1200 градусов из кокса. Внизу печи при сплавлении флюсов, пустой породы руды и золы образуется шлак, содержащий в составе окислы тех же элементов, что и сплав. Состав шлака, как и чугуна, определяется составом исходной шихты. Из-за того, что шлак имеет меньшую плотность, он располагается на поверхности чугуна.
Готовый чугун выпускается из печи через летку каждые 3-4 часа. Шлак также выпускается через другую летку через 1-2 часа. Летки открываются посредством специального устройства, а потом их закрывают огнеупорным составом. Чугун и шлак сливается в специальные ковши и чаши. Далее чугун отправляется в цех – мартеновский или кислородно-конвертерный, – где происходит его дальнейшая обработка.
Продукты, получаемые в результате доменного процесса
Самым главным продуктом, получающимся в результате плавки, являются чугуны, которые бывают разных видов – литейные и передельные. Они имеют различное содержание компонентов, в зависимости от чего происходит их дальнейшее использование.
Наряду с основным продуктом при плавке получаются дополнительные продукты – шлак, колошниковый газ и колошниковая пыль. Шлак используется для изготовления строительных материалов. К примеру, если его вылить в воду, получится материал, имеющий мелкозернистую структуру. Впоследствии его применяют для производства кирпичей, цемента и других материалов.
Колошниковый газ, образующийся при сгорании топлива, очищается специальным методом от пыли и частиц руды. Его применяют в качестве топлива в доменных печах и котлах, работающих на воде или на пару. Если смешать колошниковый газ с природным, то его можно использовать в мартеновских печах.
Еще одним продуктом доменной плавки является колошниковая пыль. Она содержит в своем составе от 40 до 50% железа и широко применяется при агломерации.
Доменная печь. Выплавка чугуна. Печь для выплавки чугуна. Схема доменной печи. Устройство доменной печи. Работа доменной печи. Параметры и конструкция доменной печи.
Чугун выплавляют в печах шахтного типа – доменных печах. Сущность процесса получения чугуна в доменных печах заключается в восстановлении оксидов железа, входящих в состав руды оксидом углерода, водородом и твердым углеродом, выделяющимся при сгорании топлива.
При выплавке чугуна решаются задачи:
- Восстановление железа из окислов руды, науглероживание его и удаление в виде жидкого чугуна определенного химического состава.
- Оплавление пустой породы руды, образование шлака, растворение в нем золы кокса и удаление его из печи.
Устройство и работа доменной печи
Доменная печь имеет стальной кожух, выложенный огнеупорным шамотным кирпичом. Рабочее пространство печи включает колошник 6, шахту 5, распар 4, заплечики 3, горн 1, лещадь 15. В верхней части колошника находится засыпной аппарат 8, через который в печь загружают шихту. Шихту подают в вагонетки 9 подъемника, которые передвигаются по мосту 12 к засыпному аппарату и, опрокидываясь, высыпают шихту в приемную воронку 7 распределителя шихты. При опускании малого конуса 10 шихта попадает в чашу 11, а при опускании большого конуса 13 – в доменную печь, что предотвращает выход газов из доменной печи в атмосферу.
Схема доменной печи
При работе печи шихтовые материалы, проплавляясь, опускаются, а через загрузочное устройство подают новые порции шихты, чтобы весь полезный объем был заполнен.
Производство чугуна. Доменное производство чугуна. Технология производства чугуна. Процесс производства чугуна.
Полезный объем доменной печи – объем, занимаемый шихтой от лещади до нижней кромки большого конуса засыпного аппарата при его опускании. Полезная высота доменной печи (Н) достигает 35 м, а полезный объем – 2000…5000 м3.
В верхней части горна находятся фурменные устройства 14, через которые в печь поступает нагретый воздух, необходимый для горения топлива. Воздух поступает из воздухонагревателя, внутри которого имеются камера сгорания и насадка из огнеупорного кирпича, в которой имеются вертикальные каналы. В камеру сгорания к горелке подается очищенный доменный газ, который, сгорая, образует горячие газы. Проходя через насадку, газы нагревают ее и удаляются через дымовую трубу. Через насадку пропускается воздух, он нагревается до температуры 1000…1200 0С и поступает к фурменному устройству, а оттуда через фурмы 2 – в рабочее пространство печи. После охлаждения насадок нагреватели переключаются.
Горение топлива. Вблизи фурм природный газ и углерод кокса, взаимодействуя с кислородом воздуха, сгорают:
C + O2 = CO2 + Q
CH4 + 2O2 = CO2 + 2H2O(пар) + Q
В результате горения выделяется большое количество теплоты, в печи выше уровня фурм развивается температура выше 2000 0С. Продукты сгорания взаимодействуют с раскаленным коксом по реакциям:
CO2 + C = 2CO — Q
H2O + C = CO + H2 — Q
Образуется смесь восстановительных газов, в которой окись углерода CO является главным восстановителем железа из его оксидов. Для увеличения производительности подаваемый в доменную печь воздух увлажняется, что приводит к увеличению содержания восстановителя. Горячие газы, поднимаясь, отдают теплоту шихтовым материалам и нагревают их, охлаждаясь до 300…400 0С у колошника. Шихта (агломерат, кокс) опускается навстречу потоку газов, и при температуре около 570 0С начинается восстановление оксидов железа.
Восстановление железа в доменной печи. Восстановление железа происходит по мере продвижения шихты вниз по шахте и повышения температуры от высшего оксида к низшему, в несколько стадий:
Fe2O3 —> Fe3O4 —> FeO —> Fe
Температура определяет характер протекания химических реакций. Восстановителями окcидов железа являются твердый углерод, оксид углерода и водород. Восстановление твердым углеродом (коксом) называется прямым восстановлением, протекает в нижней части печи (зона распара), где более высокие температуры, по реакции:
FeO + C = Fe + CO — Q
Восстановление газами (CO и H2) называется косвенным восстановлением, протекает в верхней части печи при сравнительно низких температурах, по реакциям:
3Fe2O3 + CO = 2Fe3O4 + CO2 + Q
Fe3O4 + CO = 3FeO + CO2 — Q
FeO + CO = Fe + CO2 + Q
За счет CO и H2 восстанавливаются все высшие оксиды железа до низшего и 40…60 % металлического железа.
При температуре 1000…1100 0C восстановленное из руды твердое железо, взаимодействуя с оксидом углерода, коксом и сажистым углеродом, интенсивно растворяет углерод. При насыщении углеродом температура плавления понижается и на уровне распара и заплечиков железо расплавляется (при температуре около 1300 0С).
Капли железоуглеродистого сплава, протекая по кускам кокса, дополнительно насыщаются углеродом (до 4%), марганцем, кремнием, фосфором, которые при температуре 1200 0C восстанавливаются из руды, и серой, содержащейся в коксе.
В нижней части доменной печи образуется шлак в результате сплавления окислов пустой породы руды, флюсов и золы топлива. Шлаки содержат Al2O3, CaO, MgO, SiO2, MnO, FeO, CaS. Шлак образуется постепенно, его состав меняется по мере стекания в горн, где он скапливается на поверхности жидкого чугуна, благодаря меньшей плотности. Состав шлака зависит от состава применяемых шихтовых материалов и выплавляемого чугуна.
Чугун выпускают из печи каждые 3…4 часа через чугунную летку 16, а шлак – каждые 1…1,5 часа через шлаковую летку 17 (летка – отверстие в кладке, расположенное выше лещади). Летку открывают бурильной машиной, затем закрывают огнеупорной массой. Сливают чугун и шлак в чугуновозные ковши и шлаковозные чаши.
Чугун поступает в кислородно-конвертерные (см. Кислородный конвертер) или мартеновские цехи (см. Мартеновская печь), или разливается в изложницы разливочной машиной, где он затвердевает в виде чушек-слитков массой 45 кг.
Доменная печь: принцип работы и ее устройство
- История появления доменной печи
- Схема доменной печи
- Принцип работы домны
- Расчет годовой производительности доменной печи
- Заключение
Вот уже на протяжении нескольких столетий основными агрегатами для выплавки чугуна из железорудных материалов являются доменные печи. Конечно, с годами конструкция этих шахтных плавильных агрегатов модернизировалась, совершенствовалась и изготавливалась с применением разных материалов, тем не менее их принцип работы остается неизменным и основывается на противотоке шихты и раскаленных восстановительных газов. И несмотря на высокий уровень современных технологий, в ближайшие десятилетия доменный процесс все еще будет оставаться одним из основных способов производства в черной металлургии.
История появления доменной печи
Железо (Fe) является четвертым элементом по степени распространенности на Земле. Но на нашей планете оно не встречается в чистой элементарной форме, ну разве что в составе упавших метеоритов. Поэтому люди стали получать его методом восстановления из железосодержащих руд, представляющих собой окиси и углекислые соли закиси Fe. И так как элементарная связь между Fe и O2 довольно прочная, первым изобретателям пришлось методом проб и ошибок создавать первые и, возможно, не совсем эффективные плавильные агрегаты и использовать для получения высоких температур древесный уголь, который в древности был единственным источником энергии.
Учитывая уровень современных технологий, тяжело понять, как можно было пользоваться доменной печью при отсутствии мощных скиповых подъемников, многочисленных приборов и датчиков, без природного газа и пылеугольного топлива. Тем не менее, по всему миру сохранилось довольно большое количество доменных печей, построенных еще в XVII-XIX веках. Большинство из них представляют собой объекты исторического наследия и являются экспонатами музеев под открытым небом. Но самые первые домны были созданы в Китае, о чем свидетельствуют чугунные изделия, изготовление которых датируется еще V веком до нашей эры.
Китай
Многочисленные чугунные артефакты, найденные в разные годы в Китае, и ранние тибетские писания позволяют говорить о том, что именно на территории современной КНР впервые был изобретен и освоен доменный процесс. Причем зарождение домны и начало производства чугуна в Китае связывают с культурой царства Шанг Шунг.
Сегодня нельзя доподлинно установить, какое было устройство доменной печи в древнем Китае. Известно лишь, что ранние конструкции имели глиняные стены, а их домница имела форму двух усеченных конусов, соединенных большими основаниями. Малая мощность воздуходувных средств ограничивала возможное увеличение шахты печи по высоте, поэтому печи были высотой от 2 метров. Останки самых крупных и достигавших почти 10 метров в высоту агрегатов были найдены в провинциях Гуандун и Сыньчуан. Также из некоторых источников известно, что:
- в 500 г. до н. э. местные умельцы научились доводить температуру воздействия на шихту до 1130°С;
- к 300 г. до н. э. доменный чугун начинает широко использоваться в Поднебесной для изготовления оружия, инструментов и сельскохозяйственных орудий;
- в XI веке из-за возрастающих объемов выплавки чугуна в империи Сун началась массовая вырубка деревьев. И древесный уголь, единственное топливо для домны тех времен, начинают заменять на битуминозный каменный.
Средневековая Европа
В XII и XIII веке на территории Штирии (нынешняя Австрия) для получения черных металлов за счет химического восстановления железа из руды использовалась сыродутная печь (штукофен). Она функционировала почти так же, как работает доменная печь, что позволяет считать ее если не прототипом, то предшественником таковой.
Ближе к XV веку домны возводятся в Швейцарии, Швеции, Вестфалии и Англии. Высота их достигает 5 метров, а при обслуживании уже используются разнообразные механизированные средства. И хотя подача воздуха осуществлялась клинчатыми мехами, управляемыми гидроприводом, все же это не могло обеспечить высокую интенсивность плавки, и суточная производительность домны на то время в лучшем случае составляла 1,0…1,2 тонны.
Существует несколько гипотез о том, как доменное производство появилось в Европе. По одной из версий технология могла быть украдена у китайцев, по другой – перенята у народов, заселявших территории к югу от Каспийского моря. Зато все историки сходятся во мнении, что существенный вклад в развитие доменного производства в Европе внесли цистерцианцы. Монахи этого католического ордена активно занимались хозяйственной деятельностью и были лучшими металлургами в средневековье. Даже в примитивных доменных печах того времени цистерцианцы смогли добиться высокой эффективности в переплавке руды на чугун, о чем свидетельствуют найденные при раскопках остатки шлака с очень низким содержанием железа.
Современный этап
Дальнейшее становление и развитие доменного производства уже относится к XVIII-XX векам. И значительную роль в этом сыграли крупные научно-технические достижения. Среди них:
- получение в 1735 году младшим А. Дерби патента на коксование каменного угля;
- создание Д. Уайттом в 1784 универсального парового двигателя;
- разработка в 1828 году Д. Нельсоном технологии нагрева дутья перед подачей в домну;
- изобретение в 1850 году для загрузки шихты засыпного устройства типа «воронка-конус»;
- получение в период 1867…1871 Г. Бессемером патентов на плавку чугуна с высоким давлением внутри печи и на технологию работы домны на обогащенном кислородном дутье.
Паросиловые установки и агрегаты стали широко использоваться для нагрева и подачи дутья в домну, а также позволили значительно сократить использование угля и заменять его антрацитом. Но все же, несмотря на многочисленные инновации, основным топливом для доменной печи был и остается кокс. Именно его использование стало для металлургии ключевым фактором и основой для индустриальной революции XIX века, а коксовые домны работают по сей день.
Доменные печи также использовались для выплавки цинка. В отличие от печей, выплавляющих железо, они несколько ниже, не имеют огнеупорной футеровки в боковых стенах и абсолютно герметичны. Но из-за высокой себестоимости цинковые доменные печи почти не применяются.
В результате многочисленных разработок и внедренных идей доменное производство претерпело громадные качественные изменения, а увеличение объемов производства чугуна и стали привело к созданию высокопроизводительных доменных печей.
Схема доменной печи
А теперь пробуем более детально разобраться, что такое доменная печь. Ведь интересно, что же скрыто за мощной футеровкой и многочисленными техническими площадками, которые опоясывают домменую печь по всему периметру.
Домна – это плавильный агрегат шахтного типа и непрерывного действия, в котором все теплообменные, плавильные и восстановительные процессы осуществляются в потоке движущихся навстречу друг другу кусковых материалов шихты и восстановительных газов. Агрегаты могут отличаться объемами рабочего пространства, уровнем производительности и размерами, но в целом у них всех идентичная конструкция. А типовая схема доменной печи включает такие элементы как колошник, шахту, распар, заплечики, горн и лещадь.
Колошник
Это цилиндрическая часть расположена вверху печи. Через нее осуществляется загрузка и распределение шихты, поэтому колошник испытывает ударные и абразивные воздействия от ссыпающихся с большого конуса железорудных материалов, кокса и флюса. А как устройство он имеет сложную многоэтажную конструкцию, в которую входит загрузочное устройство, система газоотводов с клапанами, минициклоны и трубопроводная система выравнивания давления.
Шахта
Это самая большая по объему и наименее стойкая часть печи, имеющая форму усеченного конуса. Именно в шахте происходят основные физико-химические процессы взаимодействия между твердыми шихтовыми материалами и газами. И ее значительная высота обусловлена тем, что при движении материалов должно произойти наибольшее косвенное восстановление оксидов железа, а это достигается длительным пребыванием материалов в шахте. Если высота недостаточна, материалы переходят в нижнюю часть печи слабо восстановленными, а чтобы обеспечить высокую газопроницаемость столба шихты на протяжении всего плавильного процесса, шахта расширяется сверху вниз.
Распар
Цилиндрическая часть печи, имеющая наибольший диаметр и обеспечивающая плавный переход шахты в заплечики. В профиле домны распар расположен в соответствии с началом этапа шлакообразования. За счет его широких габаритов снижается скорость движения газов в зоне шлакообразования и предупреждается подвисание шихты, так как в момент перехода железорудных материалов в тестообразные массы снижается проницаемость слоя шихты и возрастает гидродинамическое сопротивление.
Заплечики
Эта часть печи имеет форму перевернутого усеченного конуса. Это позволяет направить газовые потоки из зоны горения в «рудный гребень» и замедляет темп движения шихтового столба вниз.
Горн
Он представляет собой нижнюю цилиндрическую часть домны и состоит из двух частей: фурменной зоны и металлоприемника. В фурменной зоне находятся фурменные отверстия и приборы, посредством которых в домну под давлением подается нагретое воздушное дутье. А в металлоприемнике, собирающем жидкий чугун и шлак, расположены отверстия для их выпуска.
Лещадь
Это подина металлоприемника. Учитывая массогабаритные параметры и принцип работы доменной печи, лещадь является одним из ее наиболее ответственных элементов. Она испытывает значительное гидростатическое давление и температурные напряжения и поэтому выполняется из углеродистого и высокоглиноземистого материала и имеет особый вид охлаждения.
Конструктивные размеры типовых доменных печей
Размеры профиля |
Полезный объем печи, м3 |
|||||
1033 |
1513 |
2000 |
2700 |
3000 |
5000 |
|
Высота, мм |
|
|||||
полная (Hп) |
28700 |
30750 |
32358 |
33650 |
34950 |
36100 |
полезная (H0) |
26000 |
28000 |
29400 |
31200 |
32200 |
33500 |
горна (hг) |
3200 |
3200 |
3600 |
3900 |
3900 |
4400 |
заплечиков (hз) |
3000 |
3200 |
3000 |
3400 |
3200 |
3700 |
распара (hp) |
2000 |
1800 |
1700 |
2200 |
2000 |
1700 |
шахты (hш) |
15000 |
17300 |
18200 |
18700 |
20100 |
20700 |
колошника (hк) |
2800 |
2500 |
2900 |
3000 |
3000 |
3000 |
«мертвого слоя» |
600 |
766 |
1101 |
1699 |
1740 |
1113 |
Диаметр, мм |
|
|||||
горна (dг) |
7200 |
8600 |
9750 |
11000 |
11600 |
14700 |
распара (D) |
8200 |
9600 |
10900 |
12300 |
12800 |
16100 |
колошника (dк) |
5800 |
6600 |
7300 |
8100 |
8400 |
10800 |
большого конуса |
4200 |
4800 |
5400 |
6200 |
6500 |
— |
Колошниковый зазор, мм |
800 |
900 |
950 |
950 |
950 |
— |
Отношение H0😀 |
3,18 |
2,92 |
2,70 |
2,64 |
2,51 |
2,24 |
Отношение dк😀 |
0,71 |
0,69 |
0,67 |
0,66 |
0,656 |
0,67 |
Отношение D:dг |
1,14 |
1,12 |
1,12 |
1,12 |
1,12 |
1,095 |
Количество воздушных фурм |
16 |
18 |
20 |
20 |
28 |
36 |
Количество чугунных/шлаковых леток |
1/2 |
1/2 |
1(2)/2 |
2/2 |
3/1 |
4/1 |
Принцип работы домны
Доменный процесс протекает довольно сложно и требует соблюдения технологии и строгого контроля за уровнем многочисленных физических параметров. Но попробуем упрощенно рассмотреть, как доменная печь работает.
Скиповым подъемником шихтовые материалы (железорудное сырье, кокс, флюсы) поднимаются на высоту колошникового устройства и засыпаются в печь. При этом засыпка шихтовых материалов осуществляется таким образом, чтобы слои кокса чередовались с железосодержащими материалами. Снизу, благодаря работе фурменных устройств, идет нагнетание внутрь домны мощного потока горячего воздуха, который содержит необходимый для реакции кислород. Поднимаясь вверх, он движется в противотоке с опускающимися вниз слоями шихтового столба и интенсивно пронизывает их за счет наличия межкусковых пространств, вызывая горение кокса и разложение компонентов шихты. Представим доменный процесс схематически.
Описание процессов в доменной печи
Процесс |
Химические реакции |
Вдуваемый посредством фурм кислород взаимодействует с углеродом кокса |
O2 + C = CO2 |
В зоне домны, расположенной несколько выше фурм, кислород уже израсходован и происходит взаимодействие двуокиси углерода с углеродом кокса. Такая реакция приводит к повышению температуры выше 1000°С |
CO2 + С = 2СО |
При нагреве железосодержащих материалов происходит череда восстановительных процессов. В результате на последней стадии восстановления образуется губчатое железо, а окись углерода переходит в двуокись углерода |
3Fe2О3 + СО = 2Fe3О4 + СО2 Fe3О4 + СО = 3FeО + СО2 FeО + СО = Fe + СО2 |
Губчатое железо науглероживается и превращается в чугун |
3Fe + 2СО = Fe3C + СО2 |
Пустая порода под воздействием температур выше 1000°С размягчается и плавится. При этом она образует шлак, взаимодействуя с кальцием флюса и невосстановленными окислами железа и марганца |
SiO2 + 2CaO = (CaO)2SiO2 SiO2 + 2FeO = (FeO)2SiO2 SiO2 + 2MnO = (MnO)2SiO2 |
В домне происходит восстановление фосфора, марганца и кремния. Растворяясь, они также реагируют с железом |
P2O5 + 5C = 2P + 5CO SiO2 + 2C = Si + 2CO MnO2 – Mn2O3 – Mn3O – MnO |
Жидкий чугун, проходя сквозь слой шлака, дополнительно освобождается от серы и собирается в горне, откуда выпускается через летку в равные временные интервалы. Шлак имеет более низкую плотность и поэтому находится сверху расплавленного чугуна и тем самым минимизирует его окисление. Шлак также отводится через летку с соблюдением определенной временной последовательности.
Сырьевые и топливные материалы
Железные руды – основное сырье для доменного производства. К ним относятся магнитный, красный и бурый железняк, а также сидериты и гетиты. Путем обогащения и подготовки из них получают железорудное сырье:
- окатыши;
- агломерат;
- концентрат.
В руде, кроме Fe, содержится пустая порода и различные примеси, которые в ходе плавки выделяются в шлак. Для этих целей в доменную шихту дополнительно вводят флюсы. Эти материалы снижают температуру плавления пустой породы и связывают ее в неметаллические включения. Применение флюсов позволяет снизить количество примесей в чугуне и придать шлаку необходимые свойства, ведь после выплавки он также используется в разных сферах современной промышленности.
Основным топливом для доменного производства вот уже на протяжении многих десятилетий является кокс. Это продукт коксохимических фабрик и результат бескислородной переработки специальных сортов каменного угля. При этом кокс, как содержащий углерод компонент шихты, одновременно выступает топливом и ключевым реагентом для восстановления Fe из руды. В современных условиях металлурги стали частично заменять его на альтернативные виды топлива – мазут, газ природный, коксовый и доменный, а также на пылеугольное топливо.
Почему нельзя остановить домну?
Доменная печь – это шахтные плавильные агрегаты непрерывного действия. Температура в них увеличивается сверху вниз. Атмосферный кислород, вдуваемый снизу, вступает в экзотермическую химическую реакцию с коксом, которая дает тепловую энергию, необходимую для доменного процесса и доходящую иногда до 2000-2300°С.
Поэтому, если по каким-либо причинам произойдет остановка печи, сразу возникает проблема – как нагреть доменную печь снова, ведь внутри нее находятся тонны твердых и тестообразных материалов шихты, жидкий чугун и шлак. При снижении температуры все это превратится в единую массу, которую нельзя будет повторно нагреть никакими внешними воздействиями. Поэтому доменные печи останавливают только в плановом режиме при выводе из эксплуатации или на капитальный ремонт.
Расчет годовой производительности доменной печи
Годовая производительность печи позволяет судить об эффективности ее эксплуатации. Рассчитывают ее по формуле Пгод = m × Vпол / КИПО, а исходными данными для ее расчета являются:
- полезный объем домны, Vпол, м3;
- коэффициент использования полезного объема, КИПО;
- годовое количество рабочих суток печи, m, дни.
Для примера выполним расчеты для печи с полезным объемом в 2000 м3. Учитывая характер эксплуатации печи, принимаем количество рабочих суток за календарное количество дней. В 2020 году их было 366. Значение КИПО возьмем из справочников, для отечественных домен постройки 70-80-х годов прошлого века данный коэффициент равен 0,6 и 0,7.
Пгод = m × Vпол / КИПО = 366 × 2000 / 0,6 = 1 220 000 тонн
Это означает, что при полной загрузке доменная печь с таким полезным объемом могла в 2020 году дать экономике 1,22 млн. тонн чугуна.
Украинская металлургия является одной из ведущих в мире. За последние несколько лет она неоднократно занимала 9-е место в ТОП-10 среди многочисленных стран-производителей стали.
На территории Украины расположена известная во всем мире доменная печь №9. Это самая мощная домна в Европе. Ее полезный объем составляет 5034 кубических метра, а годовая производительность может достигать 4 000 000 тонн.
Заключение
Итак, исходным сырьем для доменного производства являются железные руды, а продуктами, кроме основного – чугуна, являются шлак, колошниковый газ и колошниковая пыль. Собственные природные ресурсы и мощный производственный потенциал позволяют украинским металлургам лидировать на мировом рынке и обеспечивать потребности внутреннего рынка в чугуне и стали.
Принцип работы доменной печи | Железная лаборатория
Принцип работы доменной печи
Автор Сварщик | 2 августа 2010Чугун выплавляется из железных руд в специальных печах, называемых доменными. Отсюда процесс получения чугуна из железных руд называется доменным процессом.
Доменная печь имеет большое количество специальных устройств и механизмов, обеспечивающих беспрерывность процесса. Большинство механизмов работает автоматически.
1-скип; 2-засыпной аппарат; 3-доменная печь; 4-фурменные отверстия; 5- чугунная летка; шлаковая летка; 7-воздухонагреватели; 8-газоочистительные устройства; 9-дымовая труба
Смесь из руды, кокса и флюса подготовляется в определенной пропорции для загрузки в доменную печь. Такая смесь называется шихтой. Специальный подъемник — скип 1 перемещающийся по наклонным путям, доставляет шихту к верхней части доменной печи, откуда она через засыпной аппарат 2 поступает в печь 3.
Для поддержания интенсивного горения загружаемого кокса необходимо большое количество воздуха. Воздух подается в печь через специальные отверстия 4 в нижней части печи, которые называются фурменными отверстиями. Чтобы воздух пробил высокий столб шихты и проник во все части печи, а также чтобы имелось достаточное количество кислорода для сгорания всего топлива, воздух вдувают в печь под давлением в 1—2 ати. Воздух подогревается до температуры 600—800°, так как вдувание большого количества холодного воздуха снижает температуру внутри печи, в результате чего процесс плавки руды замедляется.
Подогрев воздуха осуществляется в воздухонагревателях 7, которые строятся рядом с доменной печью. Воздухонагреватели отапливаются доменным (колошниковым) газом, получающимся при выплавке чугуна. Доменный газ предварительно очищается от пыли в специальных газоочистительных устройствах 8. Продукты сгорания из воздухонагревателей удаляются через дымовую трубу 9.
Полученный в печи жидкий чугун опускается в нижнюю ее часть, откуда периодически выпускается через отверстие 5, называемое чугунной леткой. В специальных ковшах большой емкости чугун от доменной печи отвозится в сталеплавильные цехи для переработки в сталь или к разливочной машине для получения чугунных чушек.
Пустая порода, флюсы и зола топлива образуют в печи жидкий шлак, который имеет меньший удельный вес, чем чугун, и поэтому располагается над жидким чугуном. Шлак выпускается из печи через шлаковую летку 6 и направляется для переработки и дальнейшего использования в качестве строительного материала или в шлаковый отвал.
Доменная печь работает беспрерывно по принципу противотока: исходные материалы загружаются сверху, постепенно опускаются вниз, превращаясь в чугун и шлак, а газы, нагревшиеся в нижней зоне печи, поднимаются кверху навстречу исходным материалам.
Печь имеет наружную стальную оболочку, которая называется кожухом, и внутреннюю кладку, или футеровку. Футеровка должна устойчиво сопротивляться износу от трения беспрерывно опускающихся столбом исходных материалов, выдерживать действие высоких температур, не расплавляясь и не давая деформаций. Поэтому для футеровки применяется высококачественный огнеупорный (шамотный) кирпич.
загрузка…
Похожие сообщения
- Нет связанных записей.
Устройство доменной печи — Энциклопедия по машиностроению XXL
Рис. 2.1 Устройство доменной печи |
ЭКСПЕРИМЕНТАЛЬНОЕ И ТЕОРЕТИЧЕСКОЕ ИССЛЕДОВАНИЕ ДИНАМИКИ ГИДРАВЛИЧЕСКИХ МЕХАНИЗМОВ ЗАГРУЗОЧНОГО УСТРОЙСТВА ДОМЕННОЙ ПЕЧИ [c.136] Вторым сложным узлом собственно доменной печи можно считать фурменные устройства. К фурменным устройствам доменной печи предъявляют следующие требования [c.330]
Фиг. 185. Фурменное устройство доменной печи. |
Глава III. УСТРОЙСТВО ДОМЕННОЙ ПЕЧИ [c.42]
УСТРОЙСТВО ДОМЕННОЙ ПЕЧИ [c.14]
УСТРОЙСТВО доменной печи и схема РАБОТЫ ДОМЕННОГО цеха [c.17]
Устройство доменной печи [c.16]
Устройство доменной печи и ее вспомогательные устройства [c.31]
Устройство доменной печИ 19 [c.19]
ВСПОМОГАТЕЛЬНЫЕ УСТРОЙСТВА ДОМЕННЫХ ПЕЧЕЙ [c.21]
Вспомогательные устройства доменных печей [c.23]
Фиг. 15. Большой конус засыпного устройства доменной печи, наплавляемый сормайтом на кольцевой канавке, расположенной в месте соприкосновения |
Фиг. 16. Чаша засыпного устройства доменной печи, наплавляемая сормайтом. |
Устройство доменной печи и ее работа. Доменная печь (рис. 2.1) имеет стальной кожух, выложенный внутри огнеупорным шамотным кирпичом. Рабочее пространство печи включает колошник 6, шахту 5, распар , заллечики 3, горн /, лещадь 15. В верхней части колошника находится засыпной аппарат 8, через который в печь загружают шихту (о(рлюсованный агломерат и окатыши). Шихту взвешивают, подают в вагонетки 5 подъемника, которые передвигаются по мосту 12 к засыпному аппарату 8 и, опрокидываясь, высыпают шихту в приемную воронку 7 распределителя шихты. При опускании малого конуса J0 засыпного аппарата шихта попадает в чашу /1, а при опускании большого конуса 7доменную печь, что предотвращает выход газов из доменной печи в атмосферу. Для равномерного распределения шихты в доменной печи малый конус и приемная воронка после очередной загрузки поворачиваются на угол, кратный 60 . [c.24]
Размеры и производительность доменных печей того времени больше всего за-висели от количества и давления воздуха, нагнетаемого в печи. Русские изобретатели XVIII в. успешно работали над совершенствованием воздуходувных устройств доменных печей. В 1743 г. крепостной мастер уральских заводчиков Демидовых Григорий Махотин предложил вдувать воздух в доменную печь не через одну, а через две фурмы. Это мероприятие улучшило работу печи и ускорило процесс плавки. [c.30]
В настояп] ей работе излагаются методика и результаты исследования объемного гидропривода, заслонок приемных воронок, верхних и нижних газоотсекаюш их клапанов и шихтовых затворов загрузочного устройства доменной печи объемом 5000 м . [c.137]
Как правило, укрупнение узлов проводят с целью уменьшения числа такелажных операций. Наглядным примером может служить монтаж засыпного устройства доменной печи. Как было указано ранее, подъем деталей засыпного устройства чаши, большого и малого корпуса, распределителя шихты и других произ водглся с помощью монтажной тележки, расположенной на копре гечи. Значительная высота подъема и неудобные условия для проверки взаимного прилегания деталей наверху вынуждают выносить все эти операции вниз. Так, например, укрупненный сборочных элемент засыпного устройства — большой конус и чаша — собираются и проверяются на плотность прилегания внизу. Затем этот узел весом около 50 т поднимается наверх и устанавливается на место. Перед самым подъемом внутрь чаши на большой конус укладывают малый конус и детали защиты. [c.503]
Устройство доменной печи и ее работа. Доменная печь (рис. 2.1) имеет стальной кожух, выложенный внутри огнеупорным шамотным кирпичом. Рабочее пространство печи включает колошник 6, шахту 5, распар 4, заплечики 3, горн I, лещадь 15. В верхней части колошника находится засыпной аппарат 8, через который в печь зафужают шихту (офлюсованный агломерат и окатыши). Шихту взвешивают, подают в вагонетки 9 подъемника, которые передвигаются по мосту 12 к засыпному аппарату 8 и, опрокидываясь, высыпают шихту в приемную воронку [c.28]
Назначение. Детали, работающие на износ в условиях ударных нагрузок и высоких давлений корпусы и бронефутерованные плиты дробилок и шаровых мельниц, зубья и передние стенки ковшей экскаваторов, черпаки и козырьки драг, звенья гусениц тракторов и экскаваторов, малые конусы загрузочных устройств доменных печей, трамвайные и железнодорожные стрелки н крестовины, корпусы вихревых мельниц. [c.531]
Назначение. Детали, к которым предъявляются высокие требования износоустойчивости щеки, конуса и била дробилок, бронефутеровочные плиты различных дробилок и мельниц, зубья и передние стенки ковша экскаватора, черпаки и козырьки драг, звенья гусениц тракторов и экскаваторов, железнодорожные крестовины, малые конуса загрузочных устройств доменных печей и т. д. [c.229]
Вспомогательные устройства доменных печей должны быть надежны в работе для бесперебойного обслуживания печей в течение 5—7 лет. К их числу относятся подъемные и загрузочные механизмы, литейные дворы и поддоменники, воздухонагреватели, воздуходувные машины и газоочистители. [c.69]
Схема устройства доменной печи представлена на фиг. 33. Основные элементы доменной печи колошник, шахта, распор, заклепки и горн. Рассмотрим их устройство. Колошником (I) называется верхняя часть доменной печи. Колошей, или подачей, называют определенную порцию руды, топлива и флюсов, загружаемых за один раз. В колошнике находится загрузочнораспределительное устройство, осуществляющее загрузку материалов в печь, их правильное распределение. Одновременно это устройство препятствует выходу доменных газов из печи. В настоящее время наиболее распространена конструкция засыпного аппарата, представленная на схеме фиг. 33. Аппарат состоит из двух конусов — малого 2 и большого 4 и двух воронок—малой 1 и большой 3, закрывающихся соответственно малым и большим конусами. Сначала материалы попадают в малую воронку и располагаются на малом конусе. При опускании малого конуса они просыпаются в образовавшуюся щель и располагаются на большом конусе, плотно прижатом к большой воронке. Затем поднимают малый конус, а большой опускают, и материалы попадают в печь. [c.61]
К вспомогательным устройствам доменных печей относятся подъемные и загрузочные устройства, а также литейные дворы и поддо-менники, представленные на рис. И-1. [c.21]
Устройство доменной печи и ее вспомогательные устройства
Устройство доменной печи и ее вспомогательные устройства [c.31]Чугун выплавляют в доменных печах. Современная доменная печь, в которой выплавляют 1700 т чугуна в сутки, потребляет до 3000 т руды, до 1700 т топлива, до 700 т флюсов и вместе с вспомогательными устройствами представляет сложнейшее инженерное сооружение. [c.16]
КОНСТРУКЦИИ ДОМЕННОЙ ПЕЧИ л и ВСПОМОГАТЕЛЬНЫХ УСТРОЙСТВ [c.66]
Автоматическое ведение доменной плавки осуществляется универсальной машиной, которая производит непрерывные записи режимов работы печи и вспомогательных устройств. [c.72]
КОНСТРУКЦИЯ ДОМЕННОЙ ПЕЧИ И ВСПОМОГАТЕЛЬНЫХ УСТРОЙСТВ [c.54]
Доменная печь. Основные и вспомогательные устройства доменного цеха [c.17]
Воздухонагреватели. К вспомогательным устройствам относятся и воздухонагреватели. В доменную печь вдувается раскаленный воздух, подогретый в воздухонагревателях за счет сжигания в них доменного (колошникового) газа. Современный воздухонагреватель устроен следующим образом (фиг. 34). Кладка его сделана из шамота. Снаружи воздухонагреватель покрыт стальным кожухом, верхняя часть закрыта куполом, внизу находится днище. Внутри кожуха расположена [c.63]
ВСПОМОГАТЕЛЬНЫЕ УСТРОЙСТВА ДОМЕННЫХ ПЕЧЕЙ [c.21]Вспомогательные устройства доменных печей [c.23]
КОНСТРУКЦИЯ ДОМЕННОЙ ПЕЧИ И ВСПОМОГАТЕЛЬНЫЕ УСТРОЙСТВА [c.110]
К вспомогательным устройствам доменной печи относятся оборудование складов для шихтовых материалов, воздухонагреватели (кауперы), воздуходувные машины, засыпной аппарат, газоочистители, подвижной состав (ковши) для транспортировки чугуна и шлака, разливочные машины и др. [c.15]
K. горячего дутья—вспомогательные устройства при доменных печах, которые служат 1) для отделения воздухонагревателей от трубы горячего дутья, 2) для отделения кольцевой трубы печи от воздухопровода горячего дутья и 3) для разобщения при общей трубе горячего дутья труб, работающих на разные печи. По конструкции своей эти К. бывают двух видов типа задвижки и тарельчатые. Для первой цели могут служить и те и другие, для двух остальных— только задвижки. К. горячего дутья являются слабым местом в арматуре доменных печей до сих пор еще не выработаны конструкции, могущие работать без порчи п смены в течение ряда лет. Клапаны горячего дутья работают в весьма тяжелых условиях, подвергаясь попеременно нагреву до 700— 000° и охлаждению почти до нормальной t°. Под влиянием этих темп-рных колебаний [c.152]
Развитие Д. п, происходило по трем важнейшим направлениям 1) по линии подготовки проплавляемых материалов и изучения физико-химических процессов, совершающихся в доменных печах, т. е. разработки теории доменного процесса 2) в направлении увеличения размеров и усовершенствования конструкции доменных печей и обслуживающих их вспомогательных устройств [c.488]
Конструкция печей. В настоящее время в доменном строительстве капиталистических стран имеется два течения — американское и немецкое, причем разнятся они как по конструкции самих печей, так и вспомогательных устройств и оборудования. Много отдельных конструкций, крайне разнообразных в прошлом, за последние 20 лет в значительной мере установились. [c.496]
Чугун выплавляют в доменных печах. Доменная печь вместе с вспомогательными устройствами представляет собой сложнейшее сооружение, в котором происходят химические процессы между загруженной шихтой и потоком газов, образующихся в результате горения топлива. [c.53]
М и л л е р В. Я., Металлические конструкции доменной печи объемом 2286 л з и ее вспомогательных устройств, вып. 4, ГПИ Проектстальконструкция, 1958. [c.459]
Инструкция по футеровке доменных печей и их вспомогательных устройств, Металлургиздат, 1956. [c.460]
Рис. 61. Схема строповки н монтажа засыпного устройства доменной печи полезным объемом 3000 м а — заводка верхнего укрупненного блока массой 142 т б — установленный нижвий блок массой 132 т 1 — приямок для опускания конца штангн при сборке 2 — штанга большого конуса 3—малый конус 4 — вращающаяся воронка 5 — штанга 6 — тележка вспомогательного подъема 7 — тележка главного подъема в — нижний фланец газового затвора 5 — чаша большого конуса /О — временная площадка под большой конус |
Предварительная подготовка железных руд, использование высококачественного топлива — кокса, применение более совершенных воздуходувных машин и горячего дутья позволили сооружать доменные печи значительно льшего объема и более высокой производительности. Это, в свою очередь, вызвало необходимость разработки более рациональной конструкции самой печи, а также вспомогательных устройств и механизмов доменного цеха. [c.109]
Вспомогательные устройства доменных печей должны быть надежны в работе для бесперебойного обслуживания печей в течение 5—7 лет. К их числу относятся подъемные и загрузочные механизмы, литейные дворы и поддоменники, воздухонагреватели, воздуходувные машины и газоочистители. [c.69]
Перерабатывая большое количество шихтовых материалов, доменная печь может работать лишь при условии полной механизации процессов их подготовки и загрузки. К вспомогательным устройствам, обеспечивающим работу печи, относятся шихтовые дворы, оборудованные погрузочно-разгрузочными устройствами бункерные эстакады с вагон-весами для автоматического взвешивания шихтовых материалов подъемные механизмы, доставляющие самоопрокиды-вающиеся тележки-скипы с шихтой к загрузочному аппарату доменной печи. Для нормальной работы печи необходимы также воздухонагреватели и другие устройства для подачи горячего дутья, литейный двор, ковши-чугуновозы и шлаковозы, разливочные машины и т, д. [c.28]
К вспомогательным устройствам доменных печей относятся подъемные и загрузочные устройства, а также литейные дворы и поддо-менники, представленные на рис. И-1. [c.21]
Конвейерный подъемник (табл. 1.2.1). С увеличением обьема доменных печей производительность существующих скиповых подъемников оказывается недостаточной. Поэтому на доменной печи объемом 5000 м (комбинат «Криворожсталь») установлен ленточный конвейер с ушом наклона ленты а = 10 30 для подачи шихты в приемную воронку (рис. 1.2.6). Конвейер содержит приводную станцию 5, хвостовой барабан 12, натяжную станцию 14, загрузочную воронку 9, головной барабан 1, направляющий лоток 34, отклоняющие барабаны 2, 3, 8 н 10к ленту 4 с системой поддерживающих роликов и вспомогательных устройств, которая размещена в наклонной галерее круглого сечения. Максимальный угол подъема ленты конвейера ограничивается углом трения транспортируемого груза по гладкой ленте. Конвейер оснащен теплостойкой резинотросовой лентой, состоящей из троса 35, резиновой основы 36, тканевых прокладок 37 и резиновых обкладок 38. Ширина ленты 2000 мм, ее разрывная сила [c.40]
Доменная печь | металлургия | Britannica
Доменная печь , вертикальная шахтная печь, производящая жидкие металлы за счет реакции потока воздуха, подаваемого под давлением в нижнюю часть печи, со смесью металлической руды, кокса и флюса, подаваемой в верхнюю часть. Доменные печи используются для производства чугуна из железной руды для последующей переработки в сталь, а также для обработки свинца, меди и других металлов. Быстрое горение поддерживается потоком воздуха под давлением.
Свинцово-цинковая доменная печь и свинцовый конденсатор.
Британская энциклопедия, Inc.Подробнее по этой теме
Обработка чугуна: Доменная печь
По сути, доменная печь представляет собой противоточный теплообменник и кислородный теплообменник, в котором поднимающийся дымовой газ теряет большую часть своего тепла на …
Доменные печи производят чугун из железной руды за счет восстановительного действия углерода (поставляемого в виде кокса) при высокой температуре в присутствии флюса, такого как известняк.Доменные печи для производства чугуна состоят из нескольких зон: пода в форме тигля в нижней части печи; промежуточная зона, называемая чушкой, между подом и штабелем; вертикальная шахта (штабель), идущая от чушки до верха печи; и верх печи, который содержит механизм загрузки печи. Шихта или шихта из железосодержащих материалов (, например, железорудных окатышей и агломерата), кокса и флюса (, например, известняк ) опускается через шахту, где она предварительно нагревается и вступает в реакцию с восходящим восстановлением. газы для производства жидкого чугуна и шлака, которые накапливаются в очаге.Воздух, предварительно нагретый до температур от 900 ° до 1250 ° C (1650 ° и 2300 ° F), вместе с впрыскиваемым топливом, таким как нефть или природный газ, вдувается в печь через несколько фурм (форсунок), расположенных по окружности топка у верха очага; количество таких форсунок может быть от 12 до 40 на больших печах. Предварительно нагретый воздух, в свою очередь, подается из нагнетательной трубы — трубы большого диаметра, окружающей топку. Предварительно нагретый воздух бурно реагирует с предварительно нагретым коксом, что приводит как к образованию восстановительного газа (монооксида углерода), который поднимается через печь, так и к очень высокой температуре около 1650 ° C (3000 ° F), при которой образуется жидкое железо и шлак.
Принципиальная схема современной доменной печи (справа) и доменной печи (слева).
Encyclopædia Britannica, Inc.Чушь — самая горячая часть печи из-за ее непосредственной близости к реакции между воздухом и коксом. Расплавленное железо накапливается в поде, который имеет летку для отвода расплавленного железа и, выше, отверстие для шлака для удаления смеси примесей и флюса. Под и боша представляют собой толстостенные конструкции, облицованные огнеупорными блоками углеродного типа, а дымовая труба облицована высококачественным шамотным кирпичом для защиты кожуха печи.Чтобы эти огнеупорные материалы не выгорели, в них встроены пластины, козырьки или распылители для циркуляции холодной воды.
Кумба заполнена чередующимися слоями кокса, руды и известняка, которые попадают наверху во время непрерывной работы. Кокс воспламеняется внизу и быстро сгорает за счет нагнетаемого воздуха из фурм. Оксиды железа в руде химически восстанавливаются до расплавленного железа углеродом и оксидом углерода из кокса. Образовавшийся шлак состоит из известнякового флюса, золы кокса и веществ, образующихся в результате реакции примесей в руде с флюсом; он плавает в расплавленном состоянии поверх расплавленного чугуна.Горячие газы поднимаются из зоны горения, нагревая свежий материал в дымовой трубе, а затем выходят через каналы в верхней части печи.
Получите подписку Britannica Premium и получите доступ к эксклюзивному контенту. Подпишитесь сейчасДоменные печи могут иметь следующие вспомогательные помещения: складское помещение, где шихта готовится до ее подъема на верх печи скиповыми тележками или системой ленточных конвейеров; система верхней загрузки, состоящая из вертикального набора двойных колпаков (конусов) или вращающихся желобов для предотвращения выхода топочного газа во время загрузки; печи, использующие отходящие газы печи для подогрева воздуха, подаваемого к фурмам; и литейный цех, состоящий из желобов, по которым жидкий чугун и шлак распределяются по соответствующим ковшам для передачи в сталеплавильные печи и участки утилизации шлака.
В Европе доменная печь постепенно развивалась на протяжении веков из небольших печей, эксплуатируемых римлянами, в которых древесный уголь использовался для восстановления руды до полутвердой массы железа, содержащей относительно небольшое количество углерода и шлака. Затем железную массу обрабатывали молотком для удаления шлака, получая кованое железо. Увеличение высоты печи в сочетании с механическими сильфонами для подачи в нее большего количества воздуха позволило повысить температуру, необходимую для производства высокоуглеродистого чугуна, известного как чугун.Этот способ производства использовался в Центральной Европе к середине 14 века и был введен в Англию около 1500 года. Древесный уголь был единственным топочным топливом до 17 века, когда истощение лесов, которые давали древесный уголь в Англии, привело к экспериментам с коксом. , который производится из угля. К середине 18 века кокс получил широкое распространение в доменных печах, а принцип нагрева воздуха перед его поступлением в печь был введен в начале 19 века.
Размер современных доменных печей составляет от 20 до 35 м (от 70 до 120 футов), диаметр пода составляет от 6 до 14 м (от 20 до 45 футов), и они могут производить от 1000 до почти 10 000 тонн чугуна в день.
Работа доменной печи — обзор
14.1.1 Процесс спекания мелочи железной руды
Как и другие процессы агломерации, агломерация железной руды преобразует железорудную мелочь размером — 8 мм в более крупные агломераты, а именно агломерат от 5 до Размер частиц 50 мм, которые обладают физико-металлургическими характеристиками и газопроницаемостью, необходимыми для эффективной работы доменной печи. Как показано на рисунке 14.1, спекание железной руды осуществляется в три этапа: подготовка сырья, зажигание и обжиг, а также охлаждение.
Рисунок 14.1. Принципиальная схема, показывающая поток материала в аглофабрике (Anon 1, 2014).
Процесс спекания начинается с приготовления агломерационной смеси, состоящей из мелочи железной руды, флюсов, твердого топлива (называемого в Японии связующим веществом), такого как коксовая мелочь, и мелочи, возвращаемой из агломерационной фабрики и доменной печи, а также переработанного железа. материалы из последующих процессов производства чугуна и стали. После перемешивания во вращающемся барабане к смеси добавляют воду.Гранулирование осуществляется в том же или другом вращающемся барабане путем контроля содержания влаги и движения частиц агломерационной смеси, иногда с помощью связующих, с образованием агломератов агломерационной смеси или гранул (также называемых микропеллетами, квазичастицами или псевдочастицами). ). Эти гранулы намного крупнее по сравнению с исходной агломерационной смесью и способствуют достижению оптимальной проницаемости агломерационной смеси в процессе спекания.
Затем увлажненные гранулы агломерационной смеси загружаются на глубину обычно 0 °.5–1 м на агломерационной нити, которая представляет собой непрерывную решетку, движущуюся непрерывно со скоростью обычно 2–3 м / мин. Агломерационная нить обычно имеет ширину около 4–6 м с эффективной площадью спекания до 600 м. 2 и обычно покрыта слоем просеянного агломерата, отсеиваемого от агломерата в качестве материала подстилки для защиты решеток. . После загрузки и выравнивания гранул на агломашине агломерационный слой проходит через ряд газовых или масляных горелок, которые нагревают гранулы и воспламеняют частицы кокса на поверхности агломерационного слоя.Тепло, образующееся при сгорании частиц кокса, продолжает повышать температуру последовательных слоев агломерационного слоя, чтобы образовать фазу расплава сначала из прилипшей мелочи, а затем за счет ассимиляции крупных зародышевых частиц, которые при охлаждении затвердевают в матрицу агломерата, которая связывает первоначально рыхлые частицы железной руды в куски клинкероподобного материала. Максимальная температура горящего слоя кокса (также называемого фронтом пламени) достигает примерно 1300–1375 ° C. Нисходящее всасывание, применяемое к слою агломерата, помогает предварительно нагреть воздух, всасываемый сверху, охладить спеченный слой, а также нагреть и воспламенить частицы кокса в слое ниже фронта пламени.Это позволяет спеканию гранул железной руды на решетке двигаться вниз вместе с фронтом пламени, в то время как решетка движется горизонтально к точке разгрузки жгута. Скорость агломерата и поток газа регулируются таким образом, что «прожиг» (то есть точка, в которой фронт пламени достигает основания агломерата) происходит непосредственно перед выпуском горячего агломерата.
В конце стренги спеченный продукт в виде лепешки падает с решетки в дробилку горячего агломерата (первичную дробилку), где горячий спек измельчается до заданного верхнего размера частиц, как правило, 150–200 мм.Горячий измельченный агломерат иногда просеивают для удаления мелких частиц горячего возврата, а затем выгружают в прямой или кольцевой охладитель, который охлаждает агломерат примерно до 150 ° C. После охладителя крупные частицы агломерата размером более 50–75 мм обычно измельчаются вторичной дробилкой и транспортируются на станцию просеивания, где разделяются агломерат продукта, материал пода и возвратная мелочь. Возвратная мелочь, которая слишком мелкая и не подходит для использования в доменных печах (обычно имеет размер частиц 5 мм или меньше), направляется обратно в бункер для повторного использования в процессе спекания.
Отходящий газ из выбранных зон агломашины иногда смешивается с более холодными отходящими газами и / или окружающим воздухом и рециркулируется в агломашину с помощью системы рециркуляции дымовых газов спекания или системы спекания с оптимизацией выбросов (EOS®). Этот процесс не только позволяет сэкономить на связующих веществах за счет дожигания CO и рециркулируемого тепла, но также снижает объем отходящего газа и выбросы аглофабрики. Для получения подробной информации о EOS® и системах рециркуляции дымовых газов спекания, пожалуйста, обратитесь к Главе 18, посвященной выбросам при спекании и технологиям их снижения.Отходящий газ из других зон агломерационной машины обрабатывается серией этапов обработки после этапа первичного обеспыливания (например, с помощью электрофильтра или мультициклонов) для уменьшения содержания пыли, кислых газов, а также вредных металлических и органических компонентов. . Селективное каталитическое восстановление, где V 2 O 5 используется в качестве катализатора для восстановления NO x в N 2 , часто применяется для удаления NO x из отходящего газа. Удаление SO x достигается за счет установки оборудования для десульфуризации дымовых газов агломерации.В дополнение к обычным системам мокрого типа, использующим известняк / известь, Mg (OH) 2 или аммиак в качестве абсорбента, в настоящее время используются системы обессеривания сухого типа, использующие адсорбцию активированного кокса. Эти системы не только эффективны для обессеривания, но также эффективны для удаления NO x и диоксинов.
Чугун — маршрут доменной печи
В 2016 году во всем мире было произведено более 1,1 миллиарда тонн доменного чугуна. Экономика доменных печей такова, что более крупные агрегаты имеют более низкие производственные затраты, следовательно, наблюдается тенденция к все большему и большему размеру печей. .Современные доменные печи производят более 10 000 тонн в сутки.
Для получения общей информации о товарном чугуне посетите страницу чугуна.
Современные доменные печи производят более 10 000 тонн в сутки.Процесс в доменной печи
Доменная печь представляет собой противоточный реактор для газа / твердых частиц, в котором нисходящий столб шихты [кокс, железная руда и флюсы / добавки] вступает в реакцию с восходящими горячими газами. Процесс является непрерывным, сырье регулярно загружается в верхнюю часть печи, а расплавленный чугун и шлак выпускаются из нижней части печи через равные промежутки времени.
Ключевые этапы процесса следующие:
- верхняя часть печи — свободная влага отводится от шихтовых материалов, гидраты и карбонаты отделяются.
- нижняя часть шахты доменной печи — косвенное восстановление оксидов железа оксидом углерода и водородом происходит при температуре 700–1000 ° C.
- Bosh Участок печи, где шихта начинает размягчаться и плавиться — прямое восстановление оксидов железа [и других] и карбонизация коксом происходит при 1000–1600 ° C.Расплавленное железо и шлак начинают стекать на дно печи [под].
Между чушкой и подом расположены фурмы (медные сопла с водяным охлаждением), через которые в топку вдувается дутьевой воздух — воздух для горения, предварительно нагретый до 900–1300 ° C, часто обогащенный кислородом. Непосредственно перед фурмами находится зона горения, самая горячая часть печи, 1850–2200 ° C, где кокс реагирует с кислородом и паром в дутье с образованием окиси углерода и водорода [а также тепла] и железа. и шлак полностью плавится.
Расплавленный чугун и шлак собираются в поде печи. Менее плотный шлак плавает поверх чугуна. Шлак и железо выпускаются через определенные промежутки времени через отдельные летки. При производстве товарного чугуна чугун разливают в слитки; на металлургических комбинатах жидкий чугун или чугун в торпедных тележках-ковшах перемещается в сталеплавильные печи. Шлак поступает в шлаковые карьеры для дальнейшей переработки в полезные материалы, например, сырье для производства цемента, дорожного строительства и т. Д.
Машина для литья чугуна (любезно предоставлено Paul Wurth)Реакции в доменной печи
Основные реакции:
2C + O 2 → 2CO
C + H 2 O → CO + H 2
CO 2 + C → 2CO
3Fe 2 O 3 + CO → CO 2 + 2Fe 3 O 4
Fe 3 O 4 + CO → CO 2 + 3FeO
FeO + CO → Fe + CO 2
При загрузке доменной печи шихта добавляется слоями.Загрузка осуществляется либо с помощью элеватора, в котором ведро поднимается и опускается наверху печи для опорожнения непосредственно в печь [колокольная система], либо с помощью конвейерных лент к верхней части печи, где материалы загружаются в бункер, прикрепленный к верхней части печи [система без колпака], а оттуда в печь. С помощью вращающегося желоба можно добиться очень равномерного распределения шихты по печи. Система без колпака имеет дополнительное преимущество, заключающееся в том, что во время загрузки теряется меньше энергоемкого доменного газа.
Добавки и флюсы служат для преобразования отходов или пустых пород в шихте [в основном кремнезема и глинозема] в шлак с низкой температурой плавления, который также растворяет коксовую золу и удаляет серу. Например:
CaCO 3 → CaO + CO 2
CaO + SiO 2 → CaSiO 3
FeS + CaO + C → CaS + FeO + CO
Сама доменная печь представляет собой стальную шахту облицованы огнеупорными, огнеупорными материалами.Самая горячая часть печи, где температура стенок превышает 300 ° C, имеет водяное охлаждение. Вся конструкция поддерживается снаружи стальным каркасом.
Доменный газ, выходящий из верхней части печи, представляет собой смесь двуокиси углерода, окиси углерода, водорода и азота и имеет теплотворную способность от 3200 до 4000 кДж / м³. После очистки он используется для различных целей, в том числе для нагрева дутьевых печей [«кауперов»], на предприятиях по агломерации железной руды и для выработки электроэнергии.Кредит на этот газ — важный фактор в снижении эксплуатационных расходов доменной печи.
Посмотрите видео ниже, чтобы увидеть:- макет завода «Уральская Сталь» в России
- Производство передельного чугуна из вторсырья компанией DK Recycling в Германии
Для более подробного изучения процесса доменной печи, мы предлагаем ссылку на следующее:
Производство, формовка и обработка стали, 11-е издание, опубликовано Ассоциацией металлургических технологий.
Разработка модели доменной печи с описанием термодинамического процесса с помощью рабочей схемы Rist
Доменный процесс является наиболее важным процессом производства чугуна во всем мире.Он использовался веками и до сих пор разрабатывается с целью повышения эффективности, а также производительности. В дополнение к этому, в 1970-х годах началась разработка альтернативных процессов производства чугуна, так называемых восстановительных процессов плавки. Основная цель этих усилий заключалась в разработке технологических маршрутов, позволяющих производить чугун (ТМ) с низкой производительностью с использованием некоксующегося угля напрямую, тем самым снижая выбросы в окружающую среду [1]. На сегодняшний день в промышленных масштабах освоены только процессы восстановления плавки Corex® и Finex®.
По экономическим, а также экологическим причинам производство доменного чугуна за последние десятилетия значительно продвинулось вперед. Благодаря внедрению многочисленных технологических усовершенствований, таких как более высокие температуры дутья, повышенные уровни верхнего давления газа, улучшенное распределение нагрузки и качество агломерата, а также закачка углеводородов, таких как уголь, нефть и природный газ, общая потребность в восстановителях была успешно снижена. до уровней ниже 500 кг / т ТМ [2]. Эти разработки способствуют повышению конкурентоспособности современных доменных печей.Доли мирового рынка, превышающие 99% в последние годы, подтверждают, что доменная печь остается основным процессом для производства чугуна [3].
Схематический обзор доменного процесса показан на рис. 1. В целом доменный процесс можно охарактеризовать как противоточный многофазный тепло- и массообменный реактор. Кислород удаляется из компонентов оксидной шихты и передается в восходящую горячую фазу восстановительного газа, которая, в свою очередь, передает тепло нисходящей шихте и коксу [4].Как явное тепло, так и потенциал химического восстановления (за счет восстановительного газа), необходимые для доменного процесса, обеспечиваются за счет газификации кокса и углеводородов внутри канала перед фурмами доменной печи. Способ характеризовать условия в дорожке качения — с помощью адиабатической температуры пламени на дорожке качения (RAFT) [5]. Эта адиабатическая температура является теоретическим понятием, обычно рассматриваемым на практике как эмпирический параметр для стабильной работы доменной печи [4].
Рис. 1Обзор доменного процесса
В связи с важностью доменного процесса за последние десятилетия было разработано множество различных математических моделей. К ним относятся статистические модели, термодинамические модели, а также кинетико-динамические модели. В то время как статистические модели основаны на долгосрочном анализе рабочих данных, термодинамические и кинетические модели основаны на балансе массы и энергии, а также на кинетике химических реакций [6]. Все эти типы моделей до сих пор используются в черной металлургии.
Другой способ охарактеризовать работу доменной печи — это диаграмма работы Рист (см. Рис. 2). Он основан на графиках данных восстановления лабораторной доменной печи [7] и в последующие годы был разработан до полноценной аналоговой схемы. Отличительной особенностью этой рабочей диаграммы является графическое представление балансов углерода, кислорода и водорода через рабочую строку. Эти элементы участвуют в образовании и утилизации восстановительной газовой смеси в доменной печи [8].Кроме того, с помощью линии равновесия учитываются условия равновесия протекающих непрямых реакций восстановления оксида железа [9].
Рис. 2Пример рабочей диаграммы Rist
Минимизация расхода топлива в доменной печи за счет оптимизации распределения шлама и газа (Технический отчет)
Чжоу, Ченн. Минимизация расхода топлива в доменной печи за счет оптимизации распределения шлама и газа .США: Н. П., 2012.
Интернет. DOI: 10,2172 / 1053052.
Чжоу, Ченн. Минимизация расхода топлива в доменной печи за счет оптимизации распределения шлама и газа . Соединенные Штаты. https://doi.org/10.2172/1053052
Чжоу, Ченн. Мы б .
«Минимизация расхода топлива в доменной печи за счет оптимизации распределения нагрузки и газа».Соединенные Штаты. https://doi.org/10.2172/1053052. https://www.osti.gov/servlets/purl/1053052.
@article {osti_1053052,
title = {Минимизация расхода топлива в доменной печи за счет оптимизации распределения шлама и газа},
author = {Чжоу, Ченн},
abstractNote = {Целью исследования является повышение конкурентоспособности сталелитейных заводов за счет использования передовой технологии CFD для оптимизации распределения газа и шихты внутри доменной печи для достижения наилучшего использования газа.Современная трехмерная модель CFD была разработана для моделирования распределения газа внутри доменной печи при заданных условиях нагрузки, распределении нагрузки и параметрах дутья. Комплексная трехмерная CFD-модель была подтверждена данными заводских измерений на реальной доменной печи. Также выполняется проверка подмоделей. Удобный для пользователя программный пакет под названием «Симулятор вала доменной печи» (BFSS) был разработан для моделирования процесса в шахте доменной печи. Исследование принесло металлургической промышленности значительные преимущества благодаря высокой производительности, низкому потреблению энергии и улучшению окружающей среды.},
doi = {10.2172 / 1053052},
url = {https://www.osti.gov/biblio/1053052},
journal = {},
number =,
объем =,
place = {United States},
год = {2012},
месяц = {8}
}
изменений в производстве железа | История западной цивилизации II
25.4.2: Изменения в производстве чугуна
Технологический прогресс в металлургии, в первую очередь в плавке с использованием угля или кокса, увеличил предложение и снизил цену на железо, что помогло ряду отраслей промышленности и сделало железо обычным в быстрорастущих секторах машиностроения и двигателей.
Цель обучения
Узнайте, как изменилось производство чугуна во время промышленной революции
Ключевые моменты
- На ранних этапах выплавки чугуна древесный уголь использовался как в качестве источника тепла, так и в качестве восстановителя.К 18 веку доступность древесины для производства древесного угля ограничивала расширение производства железа, поэтому Англия становилась все более зависимой от импорта из Швеции и России. Плавка с использованием угля (или его производного кокса) была долгожданной целью, с некоторыми ранними достижениями, достигнутыми в течение 17 века. Спрос Великобритании на железо и сталь в сочетании с большим капиталом и энергичными предпринимателями быстро сделал ее мировым лидером в металлургии.
- Основным изменением в металлургической промышленности в эпоху промышленной революции стала замена древесины и других видов биотоплива углем.Использование угля в плавке началось несколько до промышленной революции, основанной на нововведениях сэра Клемента Клерка и других из 1678 года, с использованием угольных отражательных печей, известных как вагранки. При использовании куполов примеси из угля не переходили в металл.
- Авраам Дарби добился больших успехов в использовании кокса для топлива своих доменных печей в Коулбрукдейле в 1709 году. Однако коксовый чугун практически не использовался для производства кованого железа в кузнях до середины 1750-х годов, когда его сын Авраам Дарби II построил печи Horsehay и Ketley.Поскольку чугун становился все более дешевым и доступным, он стал конструкционным материалом после постройки новаторского Железного моста в 1778 году Авраамом Дарби III.
- Кованое железо, которое кузнецы использовали для изготовления потребительских товаров, все еще производилось в кузницах для украшений, как и раньше. Однако в последующие годы были приняты новые процессы. Первый сегодня называют заливкой и штамповкой, но его заменил процесс лужения Генри Корта. Корт разработал два важных процесса производства чугуна: прокатку в 1783 году и лужение в 1784 году.Прокатка заменила молоток для уплотнения кованого железа и удаления некоторого количества окалины. Прокатка была в 15 раз быстрее, чем удар молотком.
- Горячий дутье, запатентованный Джеймсом Бомонтом Нейлсоном в 1828 году, был самым важным достижением XIX века в области экономии энергии при производстве чугуна. За счет использования отработанного тепла выхлопных газов для предварительного нагрева воздуха для горения было уменьшено количество топлива для изготовления единицы чугуна.
- Поставки более дешевого железа помогли ряду отраслей промышленности.Развитие станков позволило улучшить обработку чугуна, расширив его использование в быстрорастущих машиностроительной и моторной промышленности. Цены на многие товары снизились, что сделало их более доступными и распространенными.
Ключевые термины
- отражательные печи
- Металлургическая или технологическая печь, которая изолирует обрабатываемый материал от контакта с топливом, но не от контакта с дымовыми газами. Термин «реверберация» используется здесь в общем смысле отражения или отражения, а не в акустическом смысле эха.
- Железный мост
- Мост через реку Северн в Шропшире, Англия. Открытый в 1781 году, это был первый арочный мост в мире, сделанный из чугуна и получивший широкую известность после постройки.
- чугун
- Промежуточный продукт черной металлургии. Он имеет очень высокое содержание углерода, обычно 3,5–4,5%, наряду с диоксидом кремния и другими составляющими шлака, что делает его очень хрупким и непригодным в качестве материала, за исключением ограниченного применения.Его получают путем плавления железной руды в транспортируемый слиток неочищенного железа с высоким содержанием углерода в качестве ингредиента для дальнейших этапов обработки. Это жидкий чугун из доменной печи, большой печи цилиндрической формы, в которую загружается железная руда, кокс и известняк.
- кокс
- Топливо с небольшим количеством примесей и высоким содержанием углерода, обычно производимое из угля. Это твердый углеродсодержащий материал, полученный в результате деструктивной перегонки малозольного битуминозного угля с низким содержанием серы.Хотя он может быть образован естественным образом, обычно используется искусственная форма.
В начале выплавки чугуна древесный уголь использовался как в качестве источника тепла, так и в качестве восстановителя. К 18 веку доступность древесины для производства древесного угля ограничила расширение производства железа, поэтому Англия становилась все более зависимой от Швеции (с середины 17 века), а затем примерно с 1725 года от России в производстве железа, необходимого для промышленности. Плавка с использованием угля (или его производного кокса) была долгожданной целью.Производство чугуна с коксом, вероятно, было достигнуто Дадом Дадли в 1620-х годах, а смешанное топливо из угля и древесины снова было получено в 1670-х годах. Однако это был скорее технологический, чем коммерческий успех. Шадрах Фокс, возможно, плавил железо с коксом в Коулбрукдейле в Шропшире в 1690-х годах, но только для изготовления пушечных ядер и других изделий из чугуна, таких как снаряды. В мирное время они не пользовались большим спросом.
Британский спрос на железо и сталь в сочетании с большим капиталом и энергичными предпринимателями быстро сделал ее мировым лидером в металлургии.В 1875 году на Великобританию приходилось 47% мирового производства чугуна и почти 40% стали. Сорок процентов британской продукции экспортировалось в США, которые быстро строили железнодорожную и промышленную инфраструктуру. Рост производства чугуна был резким. Великобритания увеличила объем производства с 1,3 миллиона тонн в 1840 году до 6,7 миллиона в 1870 году и 10,4 миллиона тонн в 1913 году.
Основным изменением в металлургической промышленности в эпоху промышленной революции стала замена древесины и других видов биотоплива углем.При заданном количестве тепла для добычи угля требовалось гораздо меньше труда, чем для рубки древесины и преобразования ее в древесный уголь, а угля было больше, чем древесины. Использование угля в плавке началось до промышленной революции на основе нововведений сэра Клемента Клерка и других из 1678 года с использованием угольных отражательных печей, известных как вагранки. Они работали с пламенем, воздействующим на смесь руды и древесного угля или кокса, восстанавливая оксид до металла. Это имеет то преимущество, что примеси, такие как серная зола в угле, не мигрируют в металл.Эта технология применялась к свинцу с 1678 года и к меди с 1687 года. Она также применялась в чугунолитейном производстве в 1690-х годах, но в этом случае отражательная печь была известна как воздушная печь. Литейный купол — отдельная (и более поздняя) новинка.
Отражательная печь. Отражательная печь могла производить чугун из добытого угля. Горящий уголь оставался отделенным от железной руды и поэтому не загрязнял железо такими примесями, как сера и зола. Это открыло путь к увеличению производства чугуна.
Авраам Дарби добился больших успехов в использовании кокса в качестве топлива для своих доменных печей в Коулбрукдейле в 1709 году. Однако полученный им чугун из кокса использовался в основном для производства чугунных изделий, таких как котлы и котлы. У него было преимущество перед конкурентами в том, что его кастрюли, отлитые по его запатентованной технологии, были тоньше и дешевле, чем у них. Коксовый чугун практически не использовался для производства кованого железа в кузнях до середины 1750-х годов, когда его сын Авраам Дарби II построил печи Horsehay и Ketley.К тому времени коксохимический чугун был дешевле, чем чугун на древесном угле. Поскольку чугун становился все более дешевым и доступным, он стал конструкционным материалом после постройки новаторского Железного моста в 1778 году Авраамом Дарби III.
Железный мост, открытый в 1781 году
Железный мост пересекает реку Северн в Шропшире, Англия, и является первым мостом в мире, сделанным из чугуна. Зимой 1773–1774 годов местные газеты рекламировали предложение подать прошение в парламент о разрешении построить железный мост с одним пролетом в 120 футов (37 м).В 1775 году казначеем проекта был назначен Авраам Дарби III, внук Авраама Дарби I и мастер по металлу, работавший в Coalbrookdale.
Кованое железо, которое кузнецы использовали для изготовления потребительских товаров, все еще производилось в кузницах для украшений, как и раньше. Однако в последующие годы были приняты новые процессы. Первый сегодня называют заливкой и штамповкой, но его заменил процесс лужения Генри Корта. Корт разработал два важных процесса производства чугуна: прокатку в 1783 году и лужение в 1784 году.Прокатка заменила молоток для уплотнения кованого железа и удаления некоторого количества окалины. Прокатка была в 15 раз быстрее, чем удар молотком. Вальцовые мельницы сначала использовались для изготовления листов, но также прокатывались конструкционные формы, такие как уголки и рельсы.
Puddling производит конструкционное железо по относительно низкой цене. Это был способ обезуглероживания чугуна путем медленного окисления с использованием железной руды в качестве источника кислорода, поскольку железо вручную перемешивалось с помощью длинного стержня. Обработка луж производилась в отражательной печи, что позволяло использовать уголь или кокс в качестве топлива.Обезуглероженное железо, имеющее более высокую температуру плавления, чем чугун, сгребало лужу на шарики. Когда шарик становился достаточно большим, лужица удаляла его. Лужа была изнурительной и очень жаркой работой. Мало кто из лужиц дожил до 40 лет. Этот процесс продолжался до конца 19 века, когда железо было вытеснено сталью. Поскольку лужа требовала от человека навыков распознавания железных шариков, механизация никогда не была успешной.
Горячий дутье, запатентованный Джеймсом Бомонтом Нейлсоном в 1828 году, был самым важным достижением XIX века в области энергосбережения при производстве чугуна.За счет использования отработанного тепла выхлопных газов для предварительного нагрева воздуха для горения количество топлива для производства чушкового чугуна было уменьшено на одну треть при использовании угля или на две трети при использовании кокса. Однако повышение эффективности продолжалось по мере совершенствования технологии. Горячий дутье также повысил рабочую температуру печей, увеличив их мощность. Использование меньшего количества угля или кокса означало внесение меньшего количества примесей в чугун. Это означало, что уголь более низкого качества или антрацит можно было использовать в районах, где коксующийся уголь был недоступен или слишком дорог.
Поставки более дешевого железа помогли ряду отраслей, например, производству гвоздей, петель, проволоки и других металлических изделий. Развитие станков позволило улучшить обработку чугуна, что привело к увеличению его использования в быстрорастущих отраслях машиностроения и двигателестроения. Железо использовалось в сельскохозяйственных машинах, что делало сельскохозяйственный труд более эффективным. Новые технологические достижения также имели решающее значение для развития железных дорог. Цены на многие товары, такие как железная кухонная утварь, снизились, что сделало их более доступными и широко используемыми.
Авторство
- Изменения в производстве чугуна
Извлечение железа и цинка из пыли доменной печи с использованием восстановления в железной ванне
Количество пыли, производимой в доменной печи, очень велико, и в этой статье был предложен новый метод комплексной утилизации доменной пыли. Во-первых, агломераты холодного склеивания, непосредственно помещаемые в паз железа, были образованы доменной пылью. Агломераты, связанные холодным соединением, восстанавливались и плавились за счет энергии расплавленного железа, и ценные элементы, такие как Fe, восстановленное в расплавленное железо, и цинк, присутствовавшие в пыли с высоким содержанием цинка в агломератах холодного связывания, могли быть извлечены.Чтобы смоделировать этот процесс, было изучено поведение при восстановлении холодного связанного агломерата в ванне железа, и механизм восстановления был проанализирован с помощью расчетов Factsage и SEM-EDS. Результаты показали, что: в фазе шлака есть мелкие частицы металлического железа, диспергированные и трудно собираемые. Основная причина этого явления связана с тормозящей ролью углеродного остатка в агломератах, и проблема может быть решена путем добавления магнетитового концентрата в агломераты с холодным соединением.
1 Введение
С развитием металлургической промышленности и повышением осведомленности об охране окружающей среды большое внимание было уделено рекуперации и обработке металлургической пыли. Большинство отечественных металлургических предприятий сбрасывают пыль непосредственно на предприятия по переработке черной металлургии в Китае. Однако из-за циркуляции и обогащения цинка в доменной печи это сократит срок службы футеровки доменной печи и повлияет на нормальную работу доменной печи [1, 2, 3, 4].В настоящее время существует ряд методов обработки доменной пыли, предложенных в стране и за рубежом. Б. Асади Зейдабади избирательно выщелачивал ценные элементы пыли серной кислотой при низкой концентрации кислоты и комнатной температуре и достиг высокого извлечения цинка. Он также может отделять цинк и щелочные металлы от пыли доменных печей, из которой получается цинк как ценный металл. Во-вторых, контролировались подмости и другие подобные неровности в доменных печах [5].Джунвэй Хан предложил новый метод восстановления цинка и железа путем восстановительного обжига с низким кислотным выщелачиванием и магнитной сепарацией [6]. Дас. B проанализировал характеристики, обогащение и аспекты использования дымовой пыли доменных печей, шлама доменных печей, шлама LD и шлака LD, образующихся на современных сталелитейных заводах, и были использованы методы клеточной или колонной флотации для извлечения углерода из дымовой пыли доменных печей [ 7]. А. Лопес-Дельгадо оценил использование шлама доменных печей в качестве адсорбента для удаления ионов тяжелых металлов из водных стоков [8].Маниш Кумар Синха занимался извлечением цинка и железа из отработанного хлоридного раствора сталелитейной промышленности с использованием экстракции растворителем и процесса осаждения-отпарки для синтеза продуктов с добавленной стоимостью высокой чистоты [9]. Однако все вышеперечисленные методы не получили широкого распространения в Китае. Поэтому разработка экологически безопасных технологий защиты окружающей среды и эффективных технологий переработки доменной пыли имела большое значение.
В этой статье доменная пыль была спрессована в агломераты с холодной связкой с использованием горизонтальной двухроликовой машины, а затем непосредственно помещена в устройство моделирования ванны железа, и оксиды металлов будут восстановлены углеродом в доменной пыли с использованием энергии расплавленного утюг.Таким образом, оксиды железа в доменной печи восстанавливались до металлического железа в расплавленное железо, а оксид цинка восстанавливался до металлического цинка, который улетучивался и собирался пылесборником. Остальные компоненты вошли в шлак. Он может достичь цели переработки железа и
цинк в доменной пыли. В этой статье также анализировалась причина того, что железо и шлак не собирались после высокотемпературной реакции холодных склеенных агломератов, чтобы, наконец, реализовать эффективное разделение железа и шлака.
2 Эксперимент
2.1 Материалы
Доменная пыль и чугун, использованные в экспериментах, были предоставлены сталелитейной компанией в Китае. Их химический состав представлен в Таблице 1 и Таблице 2 соответственно.
Таблица 1Химический состав доменной пыли,%
T Fe | ZnO | С | SiO 2 | Al 2 O 3 | CaO | MgO | К 2 О | Na 2 O | Пб | LOI |
---|---|---|---|---|---|---|---|---|---|---|
33.94 | 3,57 | 16,30 | 5,54 | 1,90 | 6,52 | 2,82 | 1,64 | 0,92 | 0,29 | 13,04 |
Химический состав чугуна,%
Fe | Si | Mn | -п. | S | Ti | В |
---|---|---|---|---|---|---|
94.78 | 0,34 | 0,21 | 0,080 | 0,049 | 0,124 | 0,061 |
Было обнаружено, что содержание углерода в доменной пыли велико, и он может быть основным восстановителем во время восстановления оксида железа и цинка, что означает, что внешний углерод не требуется во время процесса восстановления. Оксид железа восстанавливается до металлического железа, а другие составы образуют фазу шлака, а Zn превращается в пар и летучие вещества для удаления.
2.2 Экспериментальное оборудование
Использовалось устройство моделирования ванны железа, как показано на рисунке 1. В эксперименте чугун помещался в тигель. Когда печь была нагрета до температуры испытания, чугун расплавился, что могло имитировать ситуацию с канавкой для железа перед доменной печью. Основными конструкциями устройства были нагревательная печь и регулятор температуры. Подом печи служила корундовая труба, а в качестве нагревательного элемента использовался кремний-молибденовый стержень U-типа, распределенный по поду.Температура печи измерялась двойной платиново-родиевой термопарой, а программа управлялась ПИД-регулятором. Максимальная температура устройства составляла 1873 К, а номинальная мощность — 8000 Вт.
Рисунок 1
Устройство моделирования ванны железа (баллон с газом 1-Ar; 2-нагревательная печь; 3-тигель; 4-температурный регулятор)
2.3 Экспериментальные методы
Доменная пыль и связующее были интенсивно перемешаны в ступке, затем спрессованы в цилиндрические холодноклееные агломераты ϕ 20 мм × 30 мм с водой под давлением 20 МПа.Добавление связующего составляло 2%. Затем агломераты сушили в термостатической печи в течение 8 часов при 378 К. Тигель с железным блоком помещали в устройство моделирования ванны железа, затем повышали температуру устройства до 1773 К и выдерживали в течение 30 минут, чтобы обеспечить выдержку. железный блок полностью расплавится. После этого холодные агломераты добавляли в тигель с железной баней, и продукт реакции извлекали через 1 час. Доля холодно склеенных агломератов составляла 15% расплавленного железа.Продукты реакции исследовали с помощью химического анализа и анализа SEM-EDS. Чтобы прояснить влияние состава расплавленного чугуна на эффект плавления агломератов холодного скрепления, агломераты холодного скрепления добавляли непосредственно в тигель и реагировали при 1773 К для сравнения продуктов реакции в двух условиях.
3 Результаты и обсуждения
3.1 Процесс восстановления агломератов холодного склеивания
На рис. 2 показана степень металлизации и содержание оксида цинка в агломератах.Из рисунка 2 видно, что скорость металлизации холодных агломератов постепенно увеличивается с увеличением времени реакции. По истечении времени реакции, превышающего 15 мин, скорость металлизации снижается и стремится к равновесию. Содержание ZnO в агломератах, склеенных холодным способом, было очень низким, которое в основном поддерживалось на уровне около 0,001%. В процессе восстановления оксид железа в агломератах холодного склеивания может быть восстановлен до металлического железа, а степень металлизации может достигать более 83%, в то время как ZnO может быть восстановлен до металлического Zn, что может гарантировать, что степень извлечения и удаления железа цинка [10, 11, 12, 13, 14].
Рисунок 2
Влияние времени реакции на скорость металлизации и содержание ZnO в холодносвязанных агломератах
Рисунок 3 демонстрирует морфологию холодных агломератов, восстановленных в тигле (а) и в ванне железа (б). Температура реакции 1773 К, время реакции 30 мин.
Рисунок 3
Морфология брикетирования после реакции
Как показано на Рисунке 3, можно видеть, что агломерат холодного скрепления, помещенный непосредственно в тигель или в ванну железа, оксид железа в агломерате холодного скрепления мог быть восстановлен, но он все еще находился в диспергированном состоянии после реакции на 30 мин в состоянии 1773 К.Были частицы железа, прикрепленные или смешанные с поверхностью холодного связанного агломерата. Фаза железа и фаза шлака не собирались отдельно, что не способствовало извлечению железа и образованию шлака. Поэтому важно проанализировать причину этого явления для эффективного обращения с доменной пылью.
3.2 Термодинамический анализ жидкого шлака
В соответствии с химическим составом доменной пыли в таблице 1 было принято, что только CaO, MgO, SiO 2 и Al 2 O 3 находились в фазе шлака, когда реакция закончилась.Состав, содержащий четыре компонента, был нормализован для определения процентного содержания каждого компонента, и четвертичная фазовая диаграмма CaO-MgO-SiO 2 -Al 2 O 3 была построена с помощью FactSage [15, 16]. Фазовая диаграмма которого представлена на рисунке 4.
Рисунок 4
Четвертичная фазовая диаграмма CaO-MgO-SiO 2 -Al 2 O 3
На рисунке 4 показана температура плавления фазы шлака, образовавшейся после реакции холодного связанного агломерата, превышает 1873 К.Температура плавления шлака была выше, а температура процесса восстановления не могла
.достигает своей точки плавления, что приводит к тому, что агломерат, связанный холодным соединением, не может плавиться и все еще находится в диспергированном состоянии, препятствуя агрегации между частицами железа. В результате невозможно разделить фазу железа и фазу шлака. Из рисунка 4 видно, что если содержание SiO 2 в фазе шлака было увеличено на 4%, температура плавления шлака, образовавшегося после реакции брикетирования, могла снизиться примерно до 1523 К.Поэтому, чтобы снизить температуру плавления фазы шлака, было добавлено 4% реагента SiO 2 . Доменная пыль и 4% реагента SiO 2 были интенсивно перемешаны в ступке, затем спрессованы в агломераты холодного склеивания. Высушенный холодносвязанный агломерат помещали в тигель с чугунной баней и проводили реакцию при 1500 18 ° C в течение 30 мин. На рис. 5 показана морфология продукта реакции.
Рисунок 5
Морфология продукта реакции, содержащего SiO 2
Не было очевидной разницы между агломератом холодного склеивания, содержащим SiO 2 или нет, как показано на Рисунке 5.Продукт реакции в фазе шлака был диспергирован и не собирался вместе. Частицы железа были восстановлены в середине фазы шлака, что не могло обеспечить отделение шлакового железа, восстановить ценный элемент железа из доменной пыли. Это не соответствовало результатам анализа четырехфазной фазовой диаграммы CaO-MgO-SiO 2 -Al 2 O 3 на рисунке 4. Таким образом, доля компонентов шлакообразующей фазы в холодном состоянии связанный агломерат не был основным фактором, влияющим на плавление и накопление шлака в продукте реакции.
3.3 Анализ SEM-EDS
Для определения состояния присутствия металлического железа и шлака в продукте реакции после высокотемпературного восстановления холодного связанного агломерата продукт реакции подвергали анализу SEM-EDS. На рисунке 6 показаны морфология и анализ энергетического спектра фазы Fe (a) и фазы шлака (b) в продукте реакции.
Рисунок 6
Анализ морфологии и энергетического спектра фазы Fe (а) и фазы шлака (б) продукта реакции
Таблица 1 показывает, что содержание T Fe в агломерате холодного склеивания составляет 33.94% и C составляет 16,30%. Согласно восстановлению оксидов углерода и железа, содержание углерода избыточно для восстановления оксида железа и цинка. Остаточного углерода в продукте реакции по-прежнему не происходит, как показано на Рисунке 6.
Из рисунка 6 (а) можно видеть, что оксид железа в продукте реакции восстанавливается при высокой температуре, но частицы металлического железа окружены остаточным углеродом в пыли доменной печи. Частицы железа также были смешаны с непрореагировавшим углеродом внутри, в результате чего железо было трудно собрать.Поскольку частицы железа были легче, они будут смешиваться только в фазе шлака, плавая в верхней части расплавленного чугуна, что влияет на извлечение ценных элементов в холодносвязанном агломерате. Этим невозможно добиться полной утилизации доменной пыли.
Результаты анализа энергетического спектра метки на Рисунке 6 (b) показывают, что фаза шлака, которая также обернута или изолирована от остаточного углерода в холодносвязанном агломерате, образована другими компонентами и не может быть собрана вместе Фаза шлака в продукте реакции макроскопически диспергирован и смешан со многими частицами восстановленного железа.
3.4 Проверка результатов
Для проверки изложенной выше точки зрения в ходе эксперимента холодноклееные агломераты прессовали с использованием доменной пыли и добавляли некоторое количество магнетита для полного израсходования углерода. Агломераты, связанные холодным соединением, содержащие концентрат магнетита, помещали в ванну с железом на 30 минут при 1773 К. Фиг.7 показывает морфологию продукта реакции.
Рисунок 7
Морфология продукта реакции, содержащего магнетитовый концентрат
Из рисунка 7 можно видеть, что продукт реакции металлического железа и фазы шлака собирался вместе, когда холодно связанный агломерат содержал концентрат магнетита, а фаза шлака образовывала твердую фазу, которая больше не диспергировалась.Это способствовало реализации разделения железа и шлака, и железо можно было легко восстановить в расплавленном чугуне. Тогда будет достигнута цель по извлечению ценных элементов из доменной пыли.
4 Выводы
Помещая агломерат холодного скрепления в расплавленный чугун и полагаясь на тепло, обеспечиваемое расплавленным железом, оксид железа в агломерате холодного скрепления может быть восстановлен в металлическое железо в случае его собственного углерода в качестве восстановителя без дополнительный восстановитель.
Когда холодно-связанный агломерат помещается непосредственно в расплавленный чугун, восстановление оксида железа не может полностью потреблять собственный углерод, и продукт реакции также сохраняет часть углерода. Восстановленное железо все еще смешивается с фазой шлака, что влияет на извлечение железа.
Добавляя определенное количество высокоокислительных материалов в процессе брикетирования доменной пыли, углерод, содержащийся в доменной пыли, может быть полностью израсходован без каких-либо остатков после высокотемпературной реакции.Оксид железа восстанавливается до металлического железа в чугун, а другие компоненты образуют фазу шлака, которая плавает на расплавленном железе, что обеспечивает разделение железа и шлака.
Это исследование было поддержано Национальным фондом естественных наук Китая (51874025) и Национальной программой ключевых исследований и разработок Китая (2017YFB0304300 и 2017YFB0304302)
Ссылки
[1] X.F. Она, Q.G. Сюэ, Дж. Дж. Донг, Дж. Ван и Х. Цзэн, Чин.J. Process Eng., 9 (2009) 7-10. Искать в Google Scholar
[2] S.M.Hay и W.J.Rankin, Miner. Eng., 18 (1994) 987-1001. Искать в Google Scholar
[3] В. Глади, В. С. Филиппов, Steel in Translation, 31 (2001) 1-4. Искать в Google Scholar
[4] Ф. Кукуругя, Т. Виндт и Т. Хавлик, Hydrometallurgy, 154 (2015) 20-32.10.1016 / j.hydromet.2015.03.008 Искать в Google Scholar
[5] B Асади Зейдабади, Д. Моула и М.Х.Шриат, Гидрометаллургия, 47 (1997) 113-125.10.1016 / S0304-386X (97) 00039-X Искать в Google Scholar
[6] J.W. Хан, В. Лю, W.Q. Цинь, Б. Пэн, К. Ян и Ю. X. Zheng, J. Ind. Eng. Chem., 22 (2015) 272-279.10.1016 / j.jiec.2014.07.020 Поиск в Google Scholar
[7] B Das., S. Prakash., P. S. R. Reddy, V.N. Misra, Resources Conservation and Recycling, 50 (2007) 40-57.10.1016 / j.resconrec.2006.05.008 Поиск в Google Scholar
[8] A. Lopez-Delgado, C. Perez и FA Lopez, Water Res., 32 (1998) 989-996.10.1016 / S0043-1354 (97) 00304-7 Поиск в Google Scholar
[9] М.К. Синха, С. Праманик, С. К. Саху, Л. Б. Прасад, М. К. Джа и Б. Д. Панди, сен.Purif. Technol., 167 (2016) 37-44.10.1016 / j.seppur.2016.04.049 Поиск в Google Scholar
[10] J.L. Zhang, Y.F. Ян, М. Сюй, X.H. Чжао и X.D. Чжан, Железо и сталь, 41 (2006) 78-81. Искать в Google Scholar
[11] X.D. Xing, J.L. Zhang, M.M. Цао, К. Цзяо и С. Рен, Горное и металлургическое машиностроение, 32 (2012) 86-91. Искать в Google Scholar
[12] M Sethurajan, D Huguenot, R Jain, P N.L. Линза, H A. Horn L H.A. Фигейредо и Э. Д. Хуллебуш, Дж. Хазард. Матер., 324 Часть A (2017) 71-82. Искать в Google Scholar
[13] Райан Робинсон, Thermochim. Acta, 432 (2005) 112-123. Искать в Google Scholar
[14] В.П. Джин, CA Joong и S Hocheol, Resources Conservation and Recycling, 34 (2002) 129-140.10.1016 / S0921-3449 (01) 00098-2 Искать в Google Scholar
[15 ] JR Kim, YS Lee and DJ Min, ISIJ Int., 44 (2004) 1291-1297.10.2355 / isijinternational.44.1291 Поиск в Google Scholar
[16] BJ Monaghan, L Chen and J Sorbe, Ironmaking Steelmaking, 32 ( 2005) 258-264.10.1179 / 174328105X28793 Искать в Google Scholar
Поступила: -25.12.2018
Принято: 16.05.2019
Опубликовано в сети: 08.09.2019
Опубликовано в печати: 25.02.2019
© 2019 X.-L. Лю и др. ., Опубликовано De Gruyter
Это произведение находится под лицензией Creative Commons Attribution 4.0 Public License.
.