Доменное производство | Металлургический портал MetalSpace.ru
- Физическая роль. В то время когда железосодержащие материалы изменяют свои химические и физические свойства при опускании от уровня засыпи в горн печи вследствие восстановления, размягчения и расплавления, кокс остается единственным твёрдым материалом ниже зоны расплавления железосодержащих компонентов шихты (рис. ). Кокс должен гарантировать проницаемость печи во всём её объёме для газа и расплавленных продуктов. Кроме того, кокс, оставаясь единственным материалом в твёрдом состоянии во всём объёме доменной печи, несёт на себе нагрузку столба шихтовых материалов. В этом и заключается причина невозможности работы доменной печи без кокса.
- Химическая роль. Кокс предоставляет углерод для получения восстановительных газов, а также обеспечивает прямое восстановление оксидов железа, кремния и марганца и, кроме того, обеспечивает науглероживание жидкого чугуна, что необходимо для снижения температуры его плавления.
Стены доменной печи не отвесны, что связано с тепловым расширением материалов, которые увеличиваются в объёме при нагревании – такой профиль сформировался «сам собой» в ходе эволюции агрегата из примитивного сыродутного горна.
Важной зоной доменной печи является зона когезии (или зона размягчения-плавления): выше неё материалы находятся в твёрдом состоянии, а ниже твёрдым остаётся только кокс, железорудные же материалы плавятся и стекают по кускам кокса, постепенно восстанавливаясь и разделяясь на чугун и шлак (рис.). При этом кокс в нижней части печи делится на «активный» кокс, который движется, заполняя собой место сгоревшего кокса и «тотерман» – неподвижный слой кокса, по которому стекает чугун и шлак.
Чугун и шлак скапливаются в нижней части печи (из-за разности плотности они не смешиваются) и периодически выпускаются через специальные отверстия – лётки, в чугуновозные и шлаковозные ковши. Чугун при этом направляется в сталеплавильный цех, а шлак – либо на установку грануляции для переработки с строительные материалы, либо в шлаковый отвал.
Помимо собственно доменной печи в состав комплекса по производству чугуна (рис. ) входят бункера для хранения шихтовых материалов, оборудование для их подачи в доменную печь, загрузочное устройство доменной печи, а также воздухонагреватели, в которых подаваемое в печь воздушное дутьё (обогащённое кислородом) нагревается до температуры 700-1200 °С.
Нагретое дутьё поступает по трубопроводу к печи и подаётся в опоясывающий её кольцевой воздухопровод, к которому подключены расположенные равномерно по окружности водоохлаждаемые фурмы, через которые дутьё поступает непосредственно в печь. Их число на крупных печах может составлять несколько десятков.
Поскольку кокс достаточно дорог, для его экономии зачастую вместе с воздушным дутьём в печь вдувают природный газ, мазут или угольную пыль (пылеугольное топливо – ПУТ). Углерод, поступающий с этими материалами позволяет экономить углерод кокса, а следовательно – снижать расход самого кокса.
Выходящий из доменной печи колошниковый газ очищается от пыли и направляется в газовую сеть комбината для использования в качестве топлива, поскольку он содержит значительные количества горючих водорода и оксида углерода (СО).
Поскольку чугун содержит, получаемый в доменной печи в условиях избытка углерода, всегда содержит его столько, сколько может раствориться в жидком металле при имеющихся условиях, для получения стали необходимо удалить из чугуна часть углерода, для чего используются сталеплавильные агрегаты, упомянутые выше – кислородные конвертеры и электропечи. Вторым компонентом сталеплавильной шихты является стальной лом, закупаемый комбинатами у ломозаготавливающих компаний.
ПОДЕЛИСЬ ИНТЕРЕСНОЙ ИНФОРМАЦИЕЙ
Устройство доменной печи | Металлургический портал MetalSpace.ru
Процесс доменной плавки является непрерывным. Сверху в печь загружают исходные материалы (агломерат, окатыши, кокс), а в нижнюю часть подают нагретый воздух и газообразное, жидкое или пылевидное топливо. Газы, полученные от сжигания топлива, проходят через столб шихты и отдают ей свою тепловую энергию. Опускающаяся шихта нагревается, восстанавливается, а затем плавится. Большая часть кокса сгорает в нижней половине печи, являясь источником тепла, а часть кокса расходуется на восстановление и науглероживание железа.
Доменная печь является мощным и высокопроизводительным агрегатом, в котором расходуется огромное количество материалов. Современная доменная печь расходует около 20000 тонн шихты в сутки и выдает ежесуточно около 12000 тонн чугуна.
Для обеспечения непрерывной подачи и выпуска такого большого количества материалов необходимо, чтобы конструкция печи была проста и надежна в работе в течение длительного времени. Доменная печь снаружи заключена в металлический кожух, сваренный из стальных листов толщиной 25 – 40 мм. С внутренней стороны кожуха находится огнеупорная футеровка, охлаждаемая в нижней части печи с помощью закладываемых специальных холодильников – металлических коробок, внутри которых циркулирует вода. В связи с тем, что для охлаждения печи требуется большое количество воды, на некоторых печах применяют испарительное охлаждение, сущность которого состоит в том, что в холодильники подают воды в несколько раз меньше, чем при обычном способе. Вода нагревается до кипения и интенсивно испаряется, поглощая при этом большое количество тепла.
- колошник;
- шахту;
- распар;
- заплечики;
- горн.
Колошник
Это верхняя часть доменной печи, через которую осуществляется загрузка шихтовых материалов и отвод доменного или колошникового газа. Основной частью колошникового устройства является засыпной аппарат. На большинстве доменных печей установлены двухконусные загрузочные устройства. В обычном положении оба конуса закрыты и надежно изолируют внутреннее пространство печи от атмосферы. После загрузки шихты в приемную воронку малый конус опускается и шихта падает на большой конус. Малый конус закрывается. После того, как на большом конусе будет набрано заданное количество шихты, большой конус опускается при закрытом малом конусе и шихта высыпается в печь. После этого большой конус закрывается. Таким образом, рабочее пространство доменной печи постоянно герметизировано.
Шихтовые материалы обычно подаются на колошник печи с одной стороны. В результате, в воронке малого конуса образуется откос. Длительная Работа доменной печи с перекосом уровня шихты недопустима. Для устранения этого явления приемная воронка и малый конус сделаны вращающимися. После загрузки шихты воронка вместе с конусом поворачивается на угол кратный 60, благодаря чему после разгрузки нескольких подач неравномерность полностью устраняется. 0
На современных печах могут устанавливаться более сложные по конструкции засыпные аппараты. Вместо большого конуса устанавливается вращающийся желоб, угол наклона которого может регулироваться. Такая конструкция позволяет изменять место подачи материалов по диаметру колошника.
В процессе доменной плавки образуется большое количество газа, который отводится из колошниковой части печи. Такой газ называют колошниковым. Газ содержит горючие составляющие СO и Н2 и, поэтому, используется как газообразное топливо в металлургическом производстве. Кроме того, проходя через столб шихты, газ захватывает мелкие частицы железосодержащих материалов, образуя так называемую колошниковую пыль. Пыль улавливается в специальных газоочистителях и используется как добавка к шихте при агломерации или получении окатышей.
Шахта
На долю шахты приходится большая часть общей высоты и объема печи. Профиль шахты, представляющий собой усеченный конус, расширяющийся к низу, обеспечивает равномерное опускание и разрыхление шихтовых материалов. Значительная высота шахты позволяет осуществлять тепловую и химическую обработку материалов поднимающимися горячими газами.
Распар
Это средняя цилиндрическая часть рабочего пространства печи, имеющая самый большой диаметр. Распар создает некоторое дополнительное увеличение объема печи и устраняет возможные задержки шихтовых материалов.
Заплечики
Это часть профиля печи, расположенная ниже распара и представляющая собой усеченный конус, обращенный широким основанием к распару. Обратная конусность заплечиков соответствует уменьшению объема проплавляемых материалов при образовании чугуна и шлака.
Горн
Это нижняя цилиндрическая часть печи, где осуществляются высокотемпературные процессы доменной плавки. В горне происходит горение кокса и образование доменного газа, взаимодействие между жидкими фазами, накопление жидких продуктов плавки (чугуна и шлака) и периодический их выпуск из печи. Горн состоит из верхней или фурменной части и нижней или металлоприемника. Подину металлоприемника называют лещадью.
В нижней части горна расположены чугунные и шлаковые летки, представляющие собой отверстия для выпуска чугуна и шлака. После выпуска чугуна летку закрывают специальной огнеупорной массой при помощи так называемой пушки, которая представляет собой цилиндр с поршнем. Перед открытием чугунной летки пушку заполняют леточной огнеупорной массой. После окончания выпуска чугуна пушку подводят к летке, и с помощью поршневого механизма леточная масса выдавливается из пушки и заполняет леточный канал. Для вскрытия чугунной летки служит специальная бурильная машина, которая рассверливает в леточной массе отверстие, по которому выпускают чугун.
Шлаковые летки располагаются на высоте 1500 – 2000 мм от уровня чугунной летки и закрываются с помощью шлакового стопора, представляющего собой стальной шток с наконечником. Выходящие из доменной печи чугун и шлак направляются по желобам в чугуновозные и шлаковозные ковши. В настоящее время шлак в основном выпускается вместе с чугуном и отделяется от чугуна специальным устройством на желобе печи.
Шлак, вытекающий из доменной печи через чугунную летку, отделяется от чугуна на желобе печи с помощью разделительной плиты и перевала, выпол-няющих роль гидравлического затвора. Чугун, имеющий высокую плотность, проходит в зазор под разделительной плитой, а более легкий шлак отводится в боковой желоб.
При необходимости поставки чугуна другим предприятиям его разливают в слитки (чушки) массой 30 – 40 кг на специальной разливочной машине.
В верхней части горна на расстоянии 2700 – 3500 мм от оси чугунной летки по окружности горна с равными промежутками устанавливаются воздушные фурмы, через которые подают в печь нагретое до 1100 – 1300 °С дутье, а также природный газ и другие топливные добавки (мазут, пылеугольное топливо). Каждая доменная печь обеспечивается дутьем от своей воздуходувки. Нагрев дутья осуществляется в воздухонагревателях регенеративного типа, когда под действием тепла сжигаемого газа вначале нагревается насадка воздухонагревателя из огнеупорного кирпича, а затем через нее пропускается воздух, забирающий тепло от насадки. В период нагрева насадки в камеру горения подается газ и воздух для его горения. Продукты сгорания, проходя через насадку, нагревают ее и уходят в дымоход. В период нагрева дутья холодный воздух поступает в нагретую насадку, нагревается, а затем подается в доменную печь. Как только насадка остыла настолько, что воздух не может быть нагрет до заданной температуры, его переводят на следующий воздухонагреватель, а остывший ставят на нагрев. Насадка воздухонагревателя охлаждается быстрее, чем нагревается. Поэтому блок воздухонагревателей доменной печи состоит из 3 – 4 аппаратов, из которых один нагревает воздух, а остальные разогреваются. Профиль доменной печи характеризуется диаметрами, высотами и углами наклона отдельных элементов. Размеры некоторых печей приведены в таблице 1.
Таблица 1 – Размеры печей
Размеры, мм | Полезный объем печи, м3 | ||
---|---|---|---|
2000 | 3000 | 5000 | |
Диаметр: | |||
горна | 9750 | 11700 | 14900 |
распара | 10900 | 12900 | 16300 |
колошника | 7300 | 8200 | 11200 |
Высота: | |||
полная | 32350 | 34650 | 36900 |
полезная | 29200 | 32200 | 32200 |
горна | 3600 | 3900 | 4500 |
шахты | 18200 | 20100 | 19500 |
Размеры каждой части печи должны быть увязаны между собой и находиться в определенных соотношениях с размерами других частей печи. Профиль печи должен быть рациональным, при котором обеспечиваются важнейшие условия доменного процесса:
- плавное и устойчивое опускание шихтовых материалов;
- выгодное распределение встречного газового потока;
- благоприятное развитие процессов восстановления и образование чугуна и шлака.
Основными величинами, характеризующими размеры рабочего пространства, являются полезный объем печи и полезная высота. Они включают высоту и объем, заполненные материалами и продуктами плавки. При определении этих параметров за верхний уровень берется отметка нижней кромки большого конуса засыпного устройства в опущенном положении, а нижнем уровнем является уровень оси чугунной летки.
ПОДЕЛИСЬ ИНТЕРЕСНОЙ ИНФОРМАЦИЕЙ
Как получается металл | Металлургический портал MetalSpace.ru
Руда – смесь соединений железа и кислорода – оксидов железа. Извлекают железо из руды при высокой температуре. Для этого ее нагревают с восстановителем – веществом, способным отобрать кислород у железа. Самым доступным, пожалуй, единственно возможным восстановителем в древности были дрова. Но дрова выделяют слишком мало тепла, так как в них много воды; даже в сухой древесине содержание горючего элемента (углерода) невелико. Есть в дровах и водород, но он связан с кислородом, входящим в состав древесины, а поэтому не может отнимать кислород у окислов железа.
Однако уже в древности люди заметили, что при небольшом доступе воздуха в процессе горения дрова обугливаются, превращаясь в древесный уголь, состоящий из углерода и водорода. При сгорании одного килограмма древесного угля выделяется в три-четыре раза больше теплоты, чем при сжигании одного килограмма дров. Сгорая, он дает высокую температуру, при которой идет восстановление оксидов железа. Углерод, соединяясь с кислородом, превращается в диоксид (углекислый газ) и оставляет почти чистый металл.
Установить, кто первый предложил плавить металл на древесном угле, вероятно, так же трудно, как установить автора первой заявки на изобретение колеса, лука, или лодки. Невозможно также установить, в какой стране впервые провели плавку металла на древесном угле. Однако известно, что древнейшие цивилизации Египта, Китая, Индии пользовались этими материалами. Более того, древесный уголь используется и сегодня.
Стволы деревьев, очищенные от веток, складывались или в яму (ямный способ) или в конусообразную кучу диаметром от 3 – 4 до 10 – 12 метров и высотой 3 – 7 метров (костровой способ). В куче оставлялись проходы для воздуха и выхода дымовых газов. Нижняя часть вертикальной кучи уплотнялась глиной, и вся поверхность кучи засыпалась землей. Дрова в середине кучи разжигались через специальное растопочное отверстие. Дым выходил в канал, оставленный в центре кучи, или, в более совершенных конструкциях куч, через трубу, специально сооружаемую в центре кучи. Костровой способ существовал в России и, например, в Швеции, которая являлась крупнейшим экспортером древесного угля вплоть до ХХ в.
При ямном способе яму обычно располагали на косогоре, для того чтобы стекала смола, образующаяся в процессе углежжения.
Искусство углежога состояла в том, чтобы, манипулируя открыванием и закрыванием отверстий для подачи воздуха, позволить сгореть в куче как можно меньшему количеству древесины с тем, чтобы оставшаяся часть под действием выделяющегося тепла подвергалась сухой перегонке – выделила воду, связанный кислород и превратилась в древесный уголь. Ямный способ давал уголь низкого качества, мелкий и малопрочный. Да и использовались для его производства ветки, мелкая древесина. При костровом способе использовалась отборная древесина, преимущественно хвойные. Со временем, древесный уголь стал все шире применяться для кузнечных работ и плавки железа. А его в свою очередь требовалось все больше и больше.
Чем выше температура в устройстве для производства железа или чугуна, тем быстрее идет процесс. Еще древние мастера освоили значение дутья для улучшения процессов горения топлива, поэтому стали использовать меха для подачи воздуха. Больше дутья, больше воздуха, выше температура, больше металла. Крупнее установка, выше ее производительность. Вот основное направление, по которому шло развитие агрегатов по производству железа, а потом и чугуна.
Первые мастера с большим трудом изготовляли 2 – 5 килограммов металла в день. Проходили столетия, металла требовалось все больше, печи росли и в ширину, и высоту, потребляли все больше руды, воздуха и древесины. Производительность агрегатов исчислялась уже сотнями килограммов и даже тоннами.
Несколько столетий назад были созданы аппараты для выплавки железа из руд, которые используют и в наши дни – это доменные печи. Само название происходит от старинного русского глагола «дмати» – дуть, и наглядно характеризует технологический процесс производства металла.
Доменная печь – пустотелое сооружение, составленное из двух усеченных конусов. Сверху в домну загружали уголь и руду, а снизу вдували воздух. Уголь сгорал в нижней части доменной печи, выделяя тепло и превращаясь в диоксид углерода (углекислый газ). Чуть выше углекислый газ встречался с новыми порциями древесного угля и обращался в монооксид или – «угарный газ», как его называют в просторечии. А уже на следующем ярусе монооксид углерода восстанавливал оксиды железа и вновь обращался в углекислый газ. Руда исчезала. Вместо нее образовывались жидкий металл и шлак. Они просачивались через слой материалов и собирались в нижней части агрегата.
В старину температура в домнах была недостаточно высокой, и потому металл не плавился, а в виде губчатой массы-крицы оседал на дно печи. Крицу извлекали и отковывали в горячем состоянии, выжимая из глубины на поверхность легкие неметаллические включения. Однако кричная металлургия была возможна лишь при небольших, в нашем современном представлении, масштабах производства. Сегодня в доменных печах получают только жидкий металл – чугун, который используется для изготовления разнообразных отливок. Однако большая часть чугуна перерабатывается в сталеплавильных агрегатах: конверторах, мартенах, в которых, удаляя из чугуна углерод, кремний, марганец, серу, получают прочную и упругую сталь.
В чугуне до 3% углерода, а в стали только 0,3%.
Самая распространенная сталь – 3, наш основной конструкционный материал- это тот же чугун, но в котором 0,3% углерода. Это сталь, из которой делают автомобили, арматуру, полосу и т.д.
Многие сотни лет черные металлы получали, используя древесный уголь. Для получения одной тонны металла расходовали от двух до четырех тонн такого угля.
А чтобы приготовить тонну древесного угля, требовалось 10 – 12 кубометров леса. Строились железоделательные заводы, и начинал гулять топор по соседним лесам. В конце XVI в. Королева Елизавета Английская вынуждена была запретить использовать лес для производства угля. Через 25 – 30 лет выплавка железа была прекращена почти по всей Англии. А в XVIII в. русская императрица Елизавета специальным указом запретила строить железоделательные заводы в радиусе 200 верст вокруг Москвы.
Но что Елизаветы? В древнем Египте при фараоне Рамзесе II работало более 1000 медеплавильных печей. Использовался древесный уголь, который выжигали из пальм. А потом (лет через 300) медеплавильное производство практически кончилось. Пальмы вырубили и перешли на привозную медь.
ПОДЕЛИСЬ ИНТЕРЕСНОЙ ИНФОРМАЦИЕЙ
Передел (металлургия) — Википедия
Материал из Википедии — свободной энциклопедии
Переде́л (от рус. переделывать — делать заново, по-другому[1][2]) — одна из стадий получения или переработки металла в чёрной и цветной металлургии. К переделам относятся: плавка и разливка металла, обжатие, прокат, трубное и метизное производство. Предприятия, реализующие часть полного металлургического цикла, называются передельными[3].
Технологическая схема металлургического передела руды — это последовательность и оптимальные условия операций (физических и химических процессов), при которых достигаются наиболее высокие технико-экономические показатели процесса по себестоимости и по качеству получаемого металла. В практике применяются сотни разнообразных технологических схем получения металлов. Однако принципиальная сущность всех этих схем одна и та же — отделение данного металла от пустой породы и сопутствующих элементов. Весь комплекс операций, входящих в технологические схемы, делится на четыре стадии (передела), на каждой из которых решается определённая задача[4]:
Стадия (передел) | Описание | |
---|---|---|
1 | Получение рудного концентрата | Механические способы (дробление, измельчение, обогащение) |
2 | Получение «химического» концентрата | Обжиг, спекание—разложение, хлорирование, ректификация, растворение—осаждение, плавка |
3 | Получение чернового металла или химического соединения металла | Хлорирование, фторирование, ректификация, экстракция, возгонка |
4 | Получение чистого металла | Химические и физические методы очистки |
В чёрной металлургии выделяется металлургический передел и вторичный передел чёрных сплавов. Металлургический передел включает в себя производство:
В процессе металлургического передела чугун преобразуется в сталь, а она, в свою очередь, в прокат. Чугун, не предназначенный для дальнейшего передела, называется литейным.
В зависимости от особенностей проведения операций выделяют три группы процессов металлургического передела:
- пирометаллургические, протекающие при высоких температурах (700—2000°С): обжиг, восстановительные и окислительные плавки, возгонка, дистилляция;
- гидрометаллургические, когда проводят обработку рудного сырья водными растворами кислот, щелочей или солей, при которой извлекаемый металл переводится в раствор, а пустая порода остается в виде твердого остатка. Обработку ведут при относительно невысоких температурах: 20—300°С:
- электрометаллургические, при которых используют электрический ток для проведения окислительно-восстановительных процессов в водных растворах или расплавленных солях, в результате чего на одном из электродов выделяется целевой металл.
В большинстве технологических схем получения металлов используются комбинации указанных выше трех методов. Технологические схемы получения металлов оказываются тем сложнее, чем меньше концентрация данного металла в сырье и чем больше в нём примесей, чем ближе физико-химические свойства примесей к свойствам извлекаемого металла, чем чище по содержанию примесей требуется получить металл или его химическое соединение.
Конечной продукцией металлургического производства могут быть чистые металлы, их сплавы с другими элементами, а также химические соединения (например, оксиды). При этом металлы и их сплавы получают в большинстве случаев в виде расплава, который разливают в различной величины и формы слитки. Но тугоплавкие металлы получаются в виде порошков или пористой массы — губки, которые превращают в компактные образцы либо с помощью дуговой или электронно-лучевой плавки, либо методом порошковой металлургии[5].
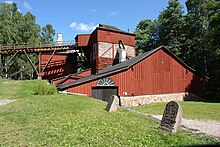
Исторически первым передельным процессом был кричный передел, когда чугун превращался в ковкое железо в кричном горне при помощи древесного угля и шлаков. В кричном горне примеси железа — углерод, кремний и марганец — окислялись, что придавало железу ковкость[6].
- ↑ Толковый словарь Даля онлайн (неопр.). slovardalja.net. Дата обращения 7 января 2017.
- ↑ Афразийская этимология : Результат запроса (неопр.). starling.rinet.ru. Дата обращения 7 января 2017.
- ↑ Кавкаева Н. В. Основы экономики и технологии важнейших отраслей хозяйства. — Москва: Directmedia, 2016. — 236 с. — ISBN 5447552230. — ISBN 9785447552237.
- ↑ Коротич, 2000, с. 54.
- ↑ Коротич, 2000, с. 56—57.
- ↑ Пугин К. Г., Вайсман Я. И., Юшков Б. С., Максимович Н. Г. Пакашненко А. А., Урунанидзе В. З., Зинединзиданов А. П. Снижение экологической нагрузки при обращении со шлаками черной металлургии. — Пермский национальный исследовательский политехнический университет, 2008. — 316 с. — ISBN 5398003003. — ISBN 9785398003000.
Производство чугуна | Металлургический портал MetalSpace.ru
В Германии чугун и нерафинированную сталь получают посредством конкурирующих процессов на нескольких металлургических заводах с полным циклом, использующих доменные печи и основные кислородные конвертеры.
Растущее в полном соответствии со спросом производство чугуна служит основой увеличения мирового потребления стали. В этом контексте доменный процесс останется ведущим технологическим процессом восстановления железа из руды. В Германии чугун и нерафинированную сталь получают посредством конкурирующих процессов на нескольких металлургических заводах с полным циклом, использующих доменные печи и основные кислородные конвертеры. По уровню технологии и оборудования эти заводы являются ведущими в мире. В рамках иследовательских программ осваивается доменный процесс с кислородным дутьем, который – в сочетании с системами улавливания и хранения СО2 (CCS) – позволит существенно уменьшить выбросы СО2. С помощью процессов прямого восстановления железа из железной руды получают твердое железо прямого восстановления (DRI) без использования кокса. DRI используют главным образом в качестве сырья для электросталеплавильных печей. Большую часть DRI получают посредством газофазных процессов, особенно в тех регионах, где имеется недорогой природный газ. Цель твердофазных процессов прямого восстановления (основанных на применении угля) – получение жидкого чугуна без использования кокса или с очень малым его расходом. Из числа различных вариантов подобных технологических процессов наиболее широкое распространение в промышленных масштабах получили процессы Corex и Finex. В то время как в процессе Corex используют в качестве шихты кусковую руду, процесс Finеx может работать на руде мелких фракций. Оба эти процесса требуют применения технологии CCS для существенного уменьшения выбросов СО2 в атмосферу.
Благодаря возможностям регулирования в широком диапазоне специфических свойств, благоприятному соотношению затрат и достигаемых с их помощью преимуществ, а также учитывая способность к рециклингу, сталь является базовым материалом и основой устойчивого развития современного индустриального общества. Сталь широко применяется во всех ключевых отраслях промышленности, в первую очередь – в общем машиностроении и приборостроении, мостостроении, строительстве, энергетике, транспорте и упаковке.
Важная роль доменного процесса
Доменный процесс и его предшественники обычно считаются родоначальниками черной металлургии. Это мнение утвердилось потому, что до начала использования металлолома в качестве шихтового материала в сталеплавильном производстве в основе всего металлургического процесса лежало восстановление железа из железной руды. Соотношение объемов производства жидкого чугуна и нерафинированной стали в мире и Германии наглядно свидетельствует о том, что до начала ХХ века сталь практически полностью получали из восстановленной железной руды (рис. 1). Снижение этого соотношения в первые 40 лет XX столетия было вызвано возрастающей долей повторного использования (рециклинга) стального лома. Однако начиная с 1940 г. соотношение выплавленного чугуна к нерафинированной стали остается практически постоянным. С тех пор растущая мировая потребность в стали удовлетворялась путем соответственного увеличения объема выплавляемого чугуна. Беспокойство, вызванное зависимостью доменного процесса от кокса, привело к появлению в 1960-х годах разработок альтернативных процессов восстановления железа из руды. В зависимости от получаемого продукта – жидкого чугуна или железа прямого восстановления (DRI) – эти процессы объединились под названиями «жидкофазное восстановление» (восстановительная плавка) или «прямое восстановление».
Рис. 1. Производство жидкого чугуна и нерафинированной стали в мире и Германии
В Германии в 2008 г. 31,2 млн.т нерафинированной стали (68 % общего объема производства) были выплавлены по технологической схеме «доменная печь – кислородный конвертер», а 14,6 млн.т – в электродуговых печах.
Производство чугуна в Германии
Реструктуризация черной металлургии. Увеличение размеров доменных печей, начавшееся в 1960-х годах, привело к фундаментальной реструктуризации черной металургии Германии (рис. 2) [1].
Рис. 2. Число действующих доменных печей и средняя годовая производительность одной печи в Германии
Для сравнения рассмотрим следующие показатели. В 1960 г. в Западной Германии в 129 доменных печах, входивших в состав 38 цехов, расположенных в 30 городах, было выплавлено 25,7 млн.т чугуна (рис. 3). Такому объему производства соответствовала средняя годовая производительность одной печи, равная 0,2 млн.т чугуна. В Германской Демократической Республике (ГДР) в восьми печах было выплавлено 2 млн.т чугуна. В 1974 г., когда наблюдался экономический подъем, в 78 доменных печах, действовавших в Западной Германии, выплавили 40 млн.т чугуна; средняя годовая производительность одной печи составила 0,5 млн.т. Для сравнения можно упомянуть, что в 2004 г. производительность каждой из 16 действующих доменных печей составила в среднем 2,1 млн.т, что означает рост на 950 % по сравнению с 1960 г. и на 320 % по сравнению с 1974 г. Такой прогресс является результатом не только увеличения размеров доменных печей, но и повышением их удельной производительности.
Рис. 3. Расположение доменных цехов в Германии в 1960 г.
В 1985 г. (в год 125-летия Института стали Общества немецких металлургов) в Западной Германии эксплуатировалось 26 доменных печей на 13 заводах (рис. 4).
Рис. 4. Расположение доменных печей в Германии в 1985 г.
В ГДР чугун выплавляли в шести доменных печах в Айзенхюттенштадте и двух доменных печах в Унтервелленборне.
Современное состояние. На рис. 5 показаны 15 доменных печей, находящихся в эксплуатации на семи заводах Германии в 2008 г. Центром производства чугуна в Германии является Дуйсбург с шестью доменными печами, выплавляющими 15,4 млн. т чугуна. Три доменные печи работают в Зальцгиттере и по две печи – в Диллингене, Бремене и Айзенхюттенштадте. Таким образом, в настоящее время Германия располагает несколькими высокоэффективными заводами с полным металлургическим циклом, на которых выплавляют нерафинированную сталь по конкурентоспособной технологии с использованием доменных печей и другого современного оборудования. Такая концентрация производства сопровождается постоянным совершенствованием технологии и оборудования с целью изыскания возможностей гибкого реагирования на колебания экономической ситуации.
Рис. 5. Расположение доменных печей в Германии в 2008 г.
Поставки руды, кокса и угля
Импорт железной руды
Импорт железной руды для немецкой черной металлургии резко изменился за последние десятилетия (рис. 6). Так, в 1970 г. основным поставщиком железной руды с объемом поставок 1,6 млн.т была шведская фирма LKAB. Кроме того, 8,2 млн.т импортировали из Либерии и 6,3 млн.т поступало из Бразилии. Вследствие гражданской войны в Либерии добыча руды была остановлена, и в 1990 г. рудники со всем оборудованием были закрыты [2]. К 2008 г. распределение импорта железной руды между странами-импортерами резко сместилось в сторону Бразилии, на долю которой приходится 53,7 %, или 22,5 млн. т, далее следуют Канада и Швеция.
Рис. 6. Распределение импорта железной руды в черную металлургию Германии по странам-импортерам в 1970-2008 гг.
Импорт кокса и угля
На протяжении 30 лет немецкая черная металлургия была вынуждена, в соответствии с конвенцией CenturyTreaty, заключенной в 1969 г. с германской угледобывающей фирмой Ruhrkohle, использовать исключительно уголь и кокс собственного производства. Только в начале 1990-х годов, по мере приближения срока окончания действия этого соглашения, ситуация начала меняться, а после 1999 г. немецкая черная металлургия начала постепенно повышать долю импортируемого кокса, коксующегося угля и угля для вдувания, доведя ее до 80 % и выше [3]. В дополнение к коксу, произведенному на собственных коксохимических предприятиях, металлургические заводы Германии в 2008 г. импортировали 3,3 млн.т из-за рубежа, присоединив этот импорт к 2 млн.т кокса, произведенного немецкой угледобывающей компанией RAGDeutscheSteinkohleAG (рис. 7) [1, 4]. Основными экспортерами кокса в Германию являются Польша (33,7 %), Франция (22,7 %), Испания (21,7 %) и Китай (16,7 %). Общий объем импорта коксующегося угля и угля для вдувания в 2008 г. составил 9,2 млн.т, причем основными странами-экспортерами угля были Австралия, США и Канада.
Рис. 7. Импорт угля и кокса для германской черной металлургии в 2008 г. из различных стран
Производство кокса в Германии
Производство кокса в Германии непрерывно сокращалось примерно с 40 млн.т в 1970 г., которые были произведены на 46 коксохимических предприятиях, до 8,26 млн.т в 2008 г., полученных только на пяти коксохимических заводах (рис. 8) [4]. Эту тенденцию можно объяснить, с одной стороны, сокращением потребления кокса в доменных печах в результате мероприятий по оптимизации и совершенствованию процесса, а с другой – потерей прочих рынков сбыта кокса. Особенно пострадали в этой ситуации коксохимические предприятия, принадлежавшие угледобывающим компаниям. Начиная с 1993 г. потребление кокса в доменных цехах и на агломерационных фабриках Германии превышало объем его производства в стране. С этого времени дефицит кокса покрывался поставками с мирового рынка.
Рис. 8. Производство и потребление кокса в Германии
Коксохимические цехи
Из пяти коксохимических цехов, действующих в Германии (рис. 9), цехи заводов, принадлежащих фирмам Pruna Schwelgern, Hьttenwerke Krupp Mannesmann (HKM), Zentralkokerei Saar (ZKS) и Salzgitter подключены к газораспределительным системам металлургических заводов с полным циклом [5]. Коксохимический цех Prosper компании RAG Deutsche Steinkohle имеет островную планировку и не связан с газопроводами металлургических заводов. Избыточный коксовый газ поставляется внешним потребителям. Коксохимический цех в Швельгерне, введенный в эксплуатацию в 2003 г., является наиболее современным цехом и производит 2,7 млн.т кокса/год в 140 коксовых печах [6]. Объем каждой камеры коксования достигает 93 м3, что является наивысшим в мире параметром. В 2008 г. эти пять коксохимических цехов обеспечивали около 75 % потребности немецкой черной металлургии в коксе.
Рис. 9. Расположение коксохимических заводов в Германии
Эволюция технологии доменного процесса
Диаметр горна и рабочий объем
В 1960 г. крупнейшие доменные печи производили около 2 тыс.т/сут. чугуна и имели горны диаметром 9 м, а рабочие объемы около 1400 м3 (рис. 10). Доменная печь Швельгерн-1, введенная в эксплуатацию в 1973 г., имела диаметр горна 14 м, а ее суточная производительность составляла 11 тыс. т чугуна [7]. В 1993 г. фирма ThyssenKruppSteel ввела в эксплуатацию доменную печь Швельгерн-2 (крупнейшую в то время в Западной Европе) с диамет ром горна 14,9 м, рабочим объемом 4769 м3 и производительностью 13 тыс.т/сут, или 4,3 млн.т/год чугуна [8]. Лишь немногие доменные печи в мире имеют годовую производительность, превышающую 4 млн.т чугуна. В их число входят доменные печи Кимицу-3, Оита-1 и Оита-2 фирмы NipponSteel, печи Чиба-6 и Кейхин-1 фирмы JFESteel, а также печь Кашима-3 фирмы SumitomoMetals в Японии; печь Швельгерн-2 фирмы ThyssenKruppSteelEurope в Германии; кроме того, печи № 1 и 4 фирмы BaoshanIronandSteel и печи № 1 и 2 фирмы ShougangJingtangIronandSteel в Китае. Крупнейшими в мире доменными печами являются печи Оита-1 и Оита-2 фирмы NipponSteel, имеющие диаметр горна 15,6 м и совместно выплавляющие 9,4 млн.т/год чугуна. Четыре новые доменные печи сопоставимых размеров сооружаются в настоящее время в Китае (фирмой WuhanIronandSteel в Фангченгганге и фирмой Baosteel в Чжанянг-Сити) [9].
Рис. 10. Эволюция размеров доменных печей в Германии с 1960 по 1993 г.
Технологические измерения и моделирование процесса
Прогресс в области технологических измерений (рис. 11) способствовал разработке моделей для оптимизации процесса плавки и контроля теплового баланса, а также внедрению их в доменный процесс. В этом плане решающую роль играет характер распределения материалов, температуры и газов на уровне засыпи и в массе шихты. Измерением давления и температуры по высоте печи можно определить расположение зоны когезии. Ключевым параметром для регулирования доменного процесса служит измерение теплопередачи в системе охлаждения и тепловых потерь над плоскостью фурм.
Рис. 11. Технологические измерения в доменной печи
Системы загрузки
Поток газов через столб шихтовых материалов регулируется целенаправленным распределением железосодержащей шихты (агломерата, окатышей, кусковой руды) и кокса на колошнике по периметру печи (рис. 12) [10]. Однако при использовании засыпного аппарата конусного типа, даже с регулируемым защитным сегментом на колошнике, такое регулирование возможно лишь в ограниченных пределах, так как невозможно контролировать распределение шихтовых материалов в тангенциальном направлении, вплоть до осевых зон колошника. Все известные засыпные аппараты конусного типа с регулируемыми защитными сегментами не могут решить проблемы распределения шихты. Операторы доменных печей искали пути решения проблемы целенаправленного распределения шихтовых материалов по периметру печи и их спирального или кольцевого перемещения к середине печи при плавной подаче материалов, которые обеспечили бы лишь небольшие зоны уплотнений, быстрое перемещение компонентов, низкий уровень капитальных затрат и небольшие расходы на ремонт и содержание оборудования. Полное удовлетворение этих требований возможно только в случае применения бесконусного загрузочного устройства с вращающимся желобом (рис. 13). Внедрение подобного загрузочного устройства в 1972 г. позволило значительно уменьшить массу оборудования (были исключены тяжелые конусы), а также сократить высоту конструкций над печью. С тех пор бесконусные загрузочные устройства подвергались непрерывному совершенствованию. В настоящее время почти все современные доменные печи имеют системы такого типа для загрузки и распределения шихты. В последние годы разработаны альтернативные бесконусные загрузочные устройства, которые внедрены лишь на нескольких печах [11, 12].
Рис. 12. Сравнение высоты конструкций загрузочных устройств доменных печей с диаметром горна 14 м
Рис. 13. Бесконусное загрузочное устройство доменной печи фирмы PaulWurth (1972г.)
Охлаждение и футеровка доменной печи
Конструкции систем охлаждения кожуха и футеровки доменных печей значительно отличаются для отдельных печей. Для охлаждения доменных печей, работающих на заводах Германии, применяются плитовые или коробчатые холодильники, а также сочетание этих двух типов холодильников. Новой разработкой в области охлаждения доменных печей являются медные плитовые холодильники, устанавливаемые в зонах, подверженных наиболее интенсивным тепловым нагрузкам (рис. 14) [13]. После первых успешных испытаний в некоторых зонах доменной печи Хамборн-4 медные плитовые холодильники впервые применили в промышленном масштабе в 1993 г. Так, на доменной печи Швельгерн-2 установили один ряд этих охлаждающих элементов, а затем на доменной печи в Зальцгиттере – три ряда охлаждающих элементов [8, 14]. Кроме охлаждения нижнего участка шахты, распара и заплечиков, такие элементы применяют также для охлаждения кожуха горна [15, 16].
Рис. 14. Установка медных холодильников на доменной печи в фирмы SalzgitterFlachstahlGmbH
По сравнению с холодильниками, изготовленными из чугуна с шаровидным графитом, медные холодильники могут обеспечивать более низкий уровень рабочих температур благодаря их большей теплопроводности. Из-за этого они менее подвержены растрескиванию и преждевременному износу (рис. 15). Еще одним их преимуществом является значительно меньшая толщина, что допускает увеличение рабочего объема доменной печи без изменения размеров кожуха.
Рис. 15. Изменение температуры холодильников горна из чугуна с шаровидным графитом и меди
Конструкция горна
На рис. 16 представлены типовые конструкции горнов доменных печей, работающих в Германии [17]. Слева показан вариант горна, изготовленного в нижней части из микропористых, а в верхней – из аморфных углеродистых блоков. С кожухом контактирует кладка из графитовых кирпичей, отличающихся высокой теплопроводностью. Днище горна выложено горизонтальными аморфными углеродистыми блоками, под которыми расположен слой графитовой кладки. На рис. 16 справа показан горн со стенками, изготовленными из микропористых углеродистых блоков. В этом варианте также имеется слой графитовых или полуграфитовых кирпичей между микропористыми блоками и кожухом. Днище горна выложено тремя верхними изолирующими слоями шамота, под которыми помещены углеродистые блоки. Горячая поверхность горна защищена керамической оболочкой.
Рис. 16. Типовые конструкции горна
Стойкостью горна определяется срок службы доменной печи. Учитывая, что при определенной глубине металлосборника становится невозможным равномерное дренирование ванны расплавленного металла и стабильный выпуск плавки без локализации износа, в настоящее время проявляется тенденция работы доменной печи с достаточно глубоким металлосборником. Кладка горна доменной печи часто подвергается преждевременному износу (эрозии), особенно на переходных участках от днища к стенке. Износ часто имеет форму «слоновьей ноги» или грибовидную форму. Выбор подходящей конструкции огнеупорной футеровки и геометрии горна гарантирует более рав
Топливо для доменных печей | Металлургический портал MetalSpace.ru
Топливо, используемое для доменной плавки, выполняет три основные функции:
- тепловую, являясь источником тепла при разогреве шихтовых материалов до высоких температур и обеспечивая интенсивное протекание химических реакций при плавлении чугуна и шлака;
- химическую, являясь основным химическим реагентом-восстановителем оксидов железа и других элементов;
- физическую, обеспечивая высокую газопроницаемость столба шихты.
Необходимо отметить, что физическая функция топлива предотвращает тяжелые расстройства хода доменной плавки. Поэтому топливо должно быть твердым, кусковым материалом, создающим высокую газопроницаемость в области высоких температур и обеспечивающим условия для противотока газа и расплавленных масс металла и шлака.
Для доменного процесса требуется прочное, неспекающееся твердое топливо. Оно занимает значительный объем доменной печи и большая его часть должна сохраниться твердой, кусковой и прочной до нижней части печи.
К топливу предъявляют следующие основные требования:
- высокая теплота сгорания и восстановительная способность в химических реакциях;
- достаточная прочность и термостойкость, чтобы не образовывалось много мелочи при нагреве топлива и прохождении его через печь;
- неспекаемость в условиях доменного процесса;
- достаточная чистота по содержанию вредных примесей – серы и фосфора.
Кроме того, твердое топливо должно содержать мало золы, особенно кремнезема и глинозема, требующих применения флюсов.
Топлива естественных видов не удовлетворяют этим требованиям. Поэтому для доменной плавки приходится специально изготовлять твердое топливо – древесный уголь, кокс.
Древесный уголь
Древесный уголь практически утратил свое значение из-за низкой прочности.
Кокс
Кокс является единственным видом твердого топлива для доменной плавки во всей мировой практике черной металлургии.
Исходным сырьем для получения кокса являются особые сорта каменных углей, называемых коксующимися. Подготовка углей к коксованию заключается в дроблении, обогащении для снижения зольности и усреднении.
Кокс получают сухой перегонкой каменных углей в коксовых печах, представляющих собой узкую камеру шириной около 0,5 м, высотой 4 – 5 м и длиной около 15 м, объединенных в батареи. Число печей в батарее может достигать 60 – 70 штук.
Подготовленная шихта загружается в камеру через специальные отверстия. Обогрев печи осуществляется с боков через стенки огнеупорного кирпича путем сжигания газа в обогревательных простенках.
Для повышения температуры коксования воздух, используемый для сжигания газа и газ, предварительно нагревают до 900 – 1000 °С в регенераторах, расположенных под печами. Горение газа происходит в простенке, за счет этого осуществляется нагрев стенок двух соседних камер до температуры 1350 – 1400 °С. Продукты сгорания через обводной канал попадают в другой простенок, опускаются по нему, обогревая две другие стенки камер, и, проходя через регенераторы, нагревают их и уходят в дымовую трубу. Периодически происходит смена направления движения газов. Через нагретые регенераторы попадают воздух и газ, а через остывшие – продукты сгорания.
Загруженная шихта нагревается в камерах примерно до 1000 °С. Продолжительность коксования составляет около 15 часов. Затем полученный коксовый пирог специальным выталкивателем выталкивают из печи и тушат водой или инертными газами.
В процессе коксования из 1 тонны угольной шихты получают около 700 кг кокса, 300 – 350 м3 коксового газа и около 20 кг смолы. Смола и газ являются ценным химическим сырьем, из которого производят лаки, краски, удобрения и другие продукты. Очищенный коксовый газ применяют в металлургических печах в качестве топлива.
В последнее время для экономии кокса при доменной плавке в печь вдувают природный газ, мазут, угольную пыль. Достоинством применения указанных видов топлива является то, что они способствуют улучшению процесса восстановления оксидов железа путем обогащения доменного газа реагентами-восстановителями (СО и Н2).
Флюсы
Флюсы вводят в доменную печь для перевода пустой породы рудной части шихты и золы кокса в шлак, обладающего определенными физическими свойствами.
Температура плавления оксидов, входящих в состав пустой породы руд составляет от 1700 до 2800 °С. Это значительно выше температуры шлака в доменной печи (1450 – 1600 °С). Кроме того, для обеспечения хорошей текучести некоторые оксиды необходимо нагревать значительно выше температуры плавления. Однако, при определенном соотношении оксидов, входящих в состав пустой породы (SiO2, Al2O3, CaO, MgO), образуются легкоплавкие соединения, которые имеют температуру плавления около 1300 °С и характеризуются хорошей текучестью при 1450 – 1600 °С.
Для удаления серы из металла необходимо, чтобы шлаки, получаемые в доменной печи, содержали определенное количество основных оксидов (CaO и MgO). Например, необходимо, чтобы в шлаках отношение (СaO + MgO) / (SiO2 + Al2O3) составляло около 1, а отношение SiO2 / Al2O3 было равно от 2 до 4.
В зависимости от состава пустой породы руды применяются основные, кислые или глиноземистые флюсы. В большинстве случаев добываемые руды содержат пустую кислую породу и имеют приемлемое соотношение SiO2 и Al2O3. Поэтому, обычно применяют основной флюс в виде известняка, состоящего из карбоната кальция СaCO3 или доломитизированного известняка, содержащего кроме СaCO3 еще MgCO3.
В настоящее время известняк вводят при окусковании железных руд или железорудных концентратов. Это приводит к улучшению показателей доменной плавки, так как уменьшается расход тепла на процесс разложения карбонатов, который осуществляется на стадии окускования (агломерации или получении окатышей).
ПОДЕЛИСЬ ИНТЕРЕСНОЙ ИНФОРМАЦИЕЙ
История производства и использования железа — Википедия
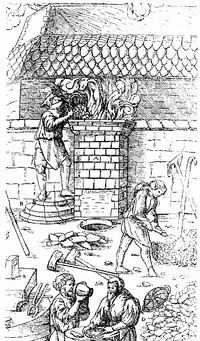
История производства и использования железа берёт своё начало в доисторической эпохе, скорее всего, с использования метеоритного железа. Выплавка в сыродутной печи применялась в XII веке до н. э. в Индии, Анатолии и на Кавказе. Также отмечается использование железа при выплавке и изготовлении орудий и инструментов в 1200 году до н. э. в Африке южнее Сахары[2][3]. Уже в первом тысячелетии до н. э. использовалось кованое железо (англ. Wrought iron). Об обработке железа упоминается в первой книге Библии (Быт. 4:22).
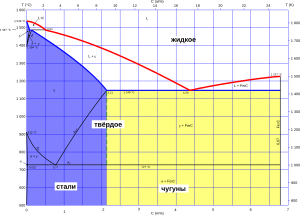
Материал, в обиходе называемый «железом», как правило, является сталью или чугуном и представляет собой сплав железа (Fe), как химического элемента, с углеродом (C). Кроме железа и углерода сплав содержит незначительные количества других химических элементов.
При концентрации углерода в сплаве менее 0,3 % получается мягкий пластичный тугоплавкий (температура плавления железа 1539 °C) сплав, за которым и закрепляется название его основного ингредиента — железа. Представление о том железе, с которым имели дело наши предки, сейчас можно получить, исследовав механические свойства гвоздя.
При концентрации углерода в сплаве от 0,3 до 2,14 % сплав называется «сталью». В первозданном виде сталь походит по своим свойствам на железо, но, в отличие от него, поддается закалке: при резком охлаждении после нагрева до определённых температур сталь приобретает большую твёрдость — замечательное достоинство, однако, почти совершенно сводимое на нет приобретённой в процессе той же закалки хрупкостью.
При концентрации углерода в сплаве свыше 2,14 % сплав называется «чугуном». Чугун — хрупкий легкоплавкий сплав, пригодный для литья, но не поддающийся обработке ковкой. Чугун насыщен графитовыми включениями, делающими его неоднородным и механически непрочным. Температура плавления чугуна варьируется от 1150 до 1300 °C.
Технологии производства и обработки железа и сплавов[править | править код]
Для производства железа исторически применялось несколько технологий, которые сложно расположить в хронологическом порядке.
Метеоритное железо[править | править код]
Использование железа началось намного раньше, чем его производство. Иногда люди находили куски серовато-чёрного металла, попавшие на Землю с метеоритами — метеоритное железо, использовали их для изготовления оружия: перековывали в кинжалы или наконечники копий. Метеоритное железо было более прочным и пластичным, чем бронза, и дольше «держало» остроту лезвия. Поскольку железные метеориты содержали железоникелевый сплав, можно предположить, что качество некоторых уникальных кинжалов могло соперничать с современным ширпотребом[4]. Однако, та же уникальность приводила к тому, что такое оружие оказывалось не на поле боя, а в сокровищнице очередного правителя.
Сыродутная печь[править | править код]
Первым устройством для получения железа из руды стала одноразовая сыродутная печь (сыродутный горн, домница). Несмотря на наличие недостатков способ получения железа с использованием такой печи долгое время оставался единственным способом получения железа из руды. На Руси появление первых домниц относят к IX веку[5].
Впервые железо научились обрабатывать народы Анатолии. Древние греки считали, что открывателями железа был народ халибов. В литературе этот народ назывался устойчивым выражением «отец железа». Слово «сталь» на греческом языке («Χάλυβς») происходит от этого этнонима.
«Железная революция» началась на рубеже I тысячелетия до нашей эры в Ассирии. Железные мечи научились изготавливать представители Гальштатской культуры. С VIII века до нашей эры сварочное железо быстро стало распространяться в Европе, в III веке до нашей эры оно вытеснило бронзу в Галлии, во II веке новой эры появилось в Германии, а в VI веке уже широко употреблялось в Скандинавии; племенами же, проживающими на территории будущей Руси — киммерийцами, а позже скифами и сарматами — железо использовалось ещё до н. э.. В Японии железный век наступил только в VII веке нашей эры.
Известный популяризатор науки Айзек Азимов так описывает историю перехода человечества из бронзового века в железный[6]:
![]() | Где-то около XV—XIV вв. до н. э. техника выплавки и науглероживания железа была разработана в кавказских предгорьях в Урарту. Эта страна находилась тогда под властью Хеттского царства, которое находилось на высшей точке своей мощи. Хеттские цари тщательно охраняли монополию на новую технику, ибо понимали её важность. Вначале получали только маленькие партии железа, и в течение нескольких столетий оно стоило порой в сорок раз дороже серебра. Но ещё до того, как выплавку можно было увеличить, а хеттам — этим воспользоваться, им пришёл конец. Хеттское царство было разрушено во время беспорядков, последовавших за движением «народов моря», и хеттская монополия на железо была нарушена. Технология выплавки железа быстро распространялась в том числе, конечно, в Ассирию, которая граничила с «железным царством» Урарту. Торговля железом восстановила процветание Ассирии. Открылся путь для новых завоеваний. Вторгшиеся в Грецию дорийские племена обладали железным оружием, именно поэтому они так легко покорили вооруженных бронзой ахейцев. Было железо и у «народов моря», и, когда филистимляне захватывали ханаанское побережье, в сражениях они использовали железное оружие, Но они были не настолько глупы, чтобы раскрывать секрет выплавки железа. Пока им удавалось хранить эту техническую тайну, израильтянам приходилось обороняться более примитивным оружием. Благодаря железу филистимляне не только легко закрепились на побережье, но и обложили данью ближайшие к ним племена. Около двух веков (до прихода к власти Давида в 1013 году до н. э.) им удавалось господствовать над более многочисленными израильскими племенами. | ![]() |
Первым шагом в зарождающейся чёрной металлургии было получение железа путём восстановления его из окиси. Болотная руда перемешивалась с древесным углём и закладывалась в печь. При высокой температуре, создаваемой горением угля, углерод начинал соединяться не только с атмосферным кислородом, но и с тем кислородом, который был связан с атомами железа.
После выгорания угля в печи оставалась так называемая «крица» — комок пористого восстановленного железа с примесью большого количества шлаков. Крицу потом снова разогревали и подвергали обработке ковкой, выколачивая шлак из железа. Полученный брусок железа (в котором всё же оставалось 2—4 % шлака) назывался «кричной болванкой». Долгое время ковка была основным процессом в технологии производства железа, причём, с приданием изделию формы она была связана в последнюю очередь. Ковкой получался сам материал.
Сварное оружие[править | править код]
Сталь производилась уже из готового железа путём насыщения углеродом последнего. При высокой температуре и недостатке кислорода углерод, не успевая окисляться, пропитывал железо. Чем больше было углерода, тем твёрже оказывалась сталь после закалки.
Как можно было заметить, ни один из перечисленных выше сплавов не обладает таким свойством, как упругость. Железный сплав может приобрести это качество, только если в нём возникает чёткая кристаллическая структура, что происходит, например, в процессе застывания из расплава. Проблема же древних металлургов заключалась в том, что расплавить железо они не могли. Для этого требуется разогреть его до 1540 °C, в то время как технологии древности позволяли достичь температур в 1000‑1300 °C. Вплоть до середины XIX века было невозможно расплавить железо и сталь с содержанием углерода менее 0,4 %, так как плавкость железных сплавов снижается по мере уменьшения концентрации углерода.
Таким образом ни железо, ни сталь сами по себе для изготовления оружия не годились. Орудия и инструменты из чистого железа выходили слишком мягкими, а из чистой стали — слишком хрупкими. Потому, чтобы изготовить, например, меч, приходилось делать «бутерброд» из двух пластин железа, между которыми закладывалась стальная пластина. При заточке мягкое железо стачивалось и появлялась стальная режущая кромка.
Такое оружие, сваренное из нескольких слоёв с разными механическими свойствами, называлось сварным. Общими недостатками этой технологии являлись излишняя массивность и недостаточная прочность изделий. Сварной меч не мог пружинить, вследствие чего неизбежно ломался или гнулся при ударе о непреодолимую преграду.
Отсутствием упругости недостатки сварного оружия не исчерпывались. В дополнение к упомянутым недостаткам, его, например, невозможно было «толком» заточить. Железу можно было придать какую угодно остроту (хотя и стачивалось оно быстро), но и тупилась мягкая режущая кромка из железа почти мгновенно. Сталь же точиться не желала — режущая кромка крошилась. Здесь налицо полная аналогия с карандашами — мягкий грифель легко сделать острым, но он сразу затупится, а твёрдый до особой остроты не доведёшь — десять раз сломается. Так что, бритвы приходилось делать из железа и затачивать заново ежедневно.
В целом же сварное оружие не превосходило остротой столовый нож. Уже одно это обстоятельство требовало делать его достаточно массивным для придания удовлетворительных рубящих свойств.
Единственной мерой, позволяющей достичь сочетания остроты и твёрдости в рамках технологии сварки, была закалка изделия уже после его заточки. Применим же этот метод становился в случае, если стальная режущая кромка приваривалась просто к железному обуху, а не заключалась в «бутерброд» из железа. Либо после заточки могли быть закалены клинки, у которых железный сердечник покрывался снаружи сталью. Недостатком такого метода было то, что заточка оказывалась возможна лишь однажды. Когда стальное лезвие повреждалось и тупилось, весь клинок приходилось перековывать.
Тем не менее именно освоение техники сварки — несмотря на все её недостатки — произвело настоящий переворот во всех сферах человеческой деятельности и привело к огромному возрастанию производительных сил. Сварные орудия были вполне функциональны и, при том, общедоступны. Только с их распространением каменные орудия оказались окончательно вытеснены, и наступил век металла.
Железные орудия решительно расширили практические возможности человека. Стало возможным, например, строить рубленные из брёвен дома — ведь железный топор валил дерево уже не в три, как медный, а в 10 раз быстрее, чем каменный. Широкое распространение получило и строительство из тёсаного камня. Он, естественно, употреблялся и в эпоху бронзы, но большой расход сравнительно мягкого и дорогого металла решительно ограничивал такие эксперименты. Значительно расширились также и возможности земледельцев.
Булатная сталь и дамаск[править | править код]
Увидеть железо жидким металлурги смогли только в XIX веке, однако ещё на заре железной металлургии — в начале I тысячелетия до нашей эры — индийские мастера сумели решить проблему получения высокоуглеродистой стали с композитной структурой. Такую сталь называли булатом, но из-за сложности изготовления и отсутствия необходимых материалов в большей части мира эта сталь так и осталась индийским секретом на долгое время.
Более технологичный путь получения упругой стали, при котором не требовались ни особо чистая руда, ни графит, ни специальные печи, был найден в Китае во II веке нашей эры. Сталь перековывали до двенадцати раз, при каждой ковке складывая заготовку вдвое, в результате чего получался отличный оружейный материал, называемый «дамаском», из которого, в частности, делались японские катаны (мечи). Количество слоёв стали рассчитывается по формуле A=2Nx{\displaystyle A=2^{N}x}, где N{\displaystyle N} — количество проковок, а x{\displaystyle x} — изначальное количество видов (слоёв) стали, сковываемой в «бутерброд». При каждой ковке количество слоёв удваивалось, а после 12 проковок количество слоёв достигало 4096, и слои становились неразличимы.
Штукофен[править | править код]
Более высокую, по сравнению с сыродутной печью, ступень в развитии чёрной металлургии представляли собой постоянные высокие печи, называемые в Европе штукофенами. Это действительно была высокая печь — с четырёхметровой трубой для усиления тяги. Мехи штукофена «качались» уже несколькими людьми, а иногда и водяным двигателем. Штукофен имел дверцы, через которые раз в сутки извлекалась крица.
Изобретены штукофены были в Индии в начале первого тысячелетия до новой эры. В начале нашей эры они попали в Китай, а в VII веке вместе с «арабскими» цифрами арабы заимствовали из Индии и эту технологию. В конце XIII века штукофены стали появляться в Германии и Чехии (а ещё до того были на юге Испании) и в течение следующего века распространились по всей Европе.
Производительность штукофена была несравненно выше, чем сыродутной печи — в день он давал до 250 кг железа, а температура в нём оказывалась достаточна для науглероживания части железа до состояния чугуна. Однако штукофенный чугун при остановке печи застывал на её дне, смешиваясь со шлаками, а очищать металл от шлаков умели тогда только ковкой, но как раз ей-то чугун и не поддавался. Его приходилось выбрасывать.
Иногда, впрочем, штукофенному чугуну пытались найти какое-то применение. Например, древние индусы отливали из грязного чугуна гробы, а турки в начале XIX века — пушечные ядра. Трудно судить, сколь хорошими были гробы, но ядра из него получались невысокого качества.
Ядра для пушек из железистых шлаков в Европе отливали ещё в конце XVI века. Из литой брусчатки делались дороги. В Нижнем Тагиле до сих пор сохранились здания с фундаментами из литых шлаковых блоков[7].
Блауофен[править | править код]
Металлурги давно заметили связь между температурой плавления и выходом продукта — чем выше была температура, тем большую часть содержащегося в руде железа удавалось восстановить. Потому рано или поздно им приходила мысль улучшить штукофен — добавить предварительный подогрев воздуха и увеличить высоту трубы. В середине XV века в Европе появились печи нового типа — блауофены, которые сразу преподнесли сталеварам неприятный сюрприз.
Более высокая температура действительно значительно повысила выход железа из руды, но она же повысила и долю железа науглероживающегося до состояния чугуна. Теперь уже не 10 %, как в штукофене, а 30 % выхода составлял чугун — «свиное железо», ни к какому делу не годное. В итоге, выигрыш часто не окупал модернизации.
Блауофенный чугун, как и штукофенный, застывал на дне печи, смешиваясь со шлаками. Он выходил несколько лучшим, так как его самого было больше, следовательно, относительное содержание шлаков выходило меньше, но продолжал оставаться малопригодным для литья. Чугун, получаемый из блауофенов, оказывался уже достаточно прочен, но оставался ещё очень неоднородным. Из него выходили только предметы простые и грубые — кувалды, наковальни, пушечные ядра.
Кроме того, если в сыродутных печах могло быть получено только железо, которое потом науглероживалось, то в штукофенах и блауофенах внешние слои крицы оказывались состоящими из стали. В блауофенных крицах стали было даже больше, чем железа. С одной стороны, это было хорошо, но вот отделить сталь от железа оказалось весьма затруднительно. Содержание углерода становилось трудно контролировать. Только долгой ковкой можно было добиться однородности его распределения.
В своё время, столкнувшись с этими затруднениями, индусы не стали двигаться дальше, а занялись тонким усовершенствованием технологии и пришли к получению булата. Но индусов в ту пору интересовало не количество, а качество продукта. Европейцы, экспериментируя с чугуном, скоро открыли передельный процесс, поднявший металлургию железа на качественно новый уровень.
Доменная печь[править | править код]
Следующим этапом в развитии металлургии стало появление доменных печей. За счёт увеличения размера, предварительного подогрева воздуха и механического дутья, в такой печи всё железо из руды превращалось в чугун, который расплавлялся и периодически выпускался наружу. Производство стало непрерывным — печь работала круглосуточно и не остывала. За день она выдавала до полутора тонн чугуна. Перегнать же чугун в железо в горнах было значительно проще, чем выколачивать его из крицы, хотя ковка все равно требовалась — но теперь уже выколачивали шлаки из железа, а не железо из шлаков.
Хотя найденные в Китае чугунные изделия восходят к V веку до нашей эры[8], самые ранние доменные печи, производящие чугун в «чушках» (слитках), который мог переплавляться в очищенный чугун в вагранках, датируются III—II веками до нашей эры. Подавляющее большинство обнаруженных ранних мест доменного производства относятся к периоду после введения государственной монополии на соль и железорудную промышленность в 117 году до нашей эры (период правления императора У-ди, 141—87 до н. э.) в эпоху династии Хань (202 год до нашей эры — 220 год нашей эры). Большинство железоделательных мест, открытых до 117 года до нашей эры, занимались лишь литьём из заготовок, выплавленных в доменных печах в других районах, отдалённых от населённых пунктов[9][10].
В Европе доменные печи впервые были применены на рубеже XV—XVI веков. На Ближнем Востоке и в Индии эта технология появилась только в XIX веке (в значительной степени, вероятно, потому, что водяной двигатель из-за характерного дефицита воды на Ближнем Востоке не употреблялся). Наличие в Европе доменных печей позволило ей обогнать в XVI веке Турцию если не по качеству металла, то по валу. Это оказало несомненное влияние на исход борьбы, особенно когда оказалось, что из чугуна можно лить пушки.
Георгий Агрикола так описывает средневековую технологию плавки[11]:
![]() | Обычай выдающихся плавильщиков, умеющих управлять четырьмя элементами (имеются в виду земля, воздух, огонь и вода — вне цитаты), таков. Они смешивают в правильных пропорциях руды, содержащие земли, и загружают их в печи. Затем льют нужное количество воды и умело управляют движением воздуха, поступающего из мехов, забрасывая руду туда, где огонь горит с наибольшей силой. Мастер равномерно обрызгивает водой внутреннее пространство печи, слегка увлажняя древесный уголь с тем, чтобы к нему приставали мелкие частицы руды; иначе эти частицы приводятся в движение силой дутья и огня и уносятся вместе с дымом. | ![]() |
Также Агрикола верно объясняет необходимость изменения конструкции печи в зависимости от типа руд[11]:
![]() | Так как природа руд, подлежащих плавке, бывает различной, плавильщикам приходится устраивать горн то выше, то ниже и устанавливать трубу, куда вводятся насадки мехов под меньшим или большим углом для того, чтобы дутье при надобности было более или менее сильным. Если руды нагреваются и плавятся легко, то для работы плавильщиков необходим низкий горн, а труба должна быть установлена под небольшим углом, чтобы дутье было легкое. Наоборот, если руды нагреваются и плавятся медленно, то требуется высокий горн, а труба должна быть установлена с крутым уклоном, чтобы обеспечить сильное дутье. Для руд этого рода нужна весьма горячая печь, в которой сначала расплавляются шлаки, штейны или легкоплавкие камни для того, чтобы руда не могла пригореть к поду горна и закрыть выпускное отверстие. | ![]() |
Передельный процесс[править | править код]
С XVI века в Европе получил распространение так называемый передельный процесс в металлургии — технология, при которой железо ещё при получении за счёт высокой температуры плавления и интенсивного науглероживания перегонялось в чугун, а уже затем, жидкий чугун, освобождаясь от лишнего углерода при отжиге в горнах, превращался в сталь.
Из передельной стали уже можно было изготавливать кривые мечи (например, сабли), чего не позволяла сделать сварная технология.
Применение угля, коксование, пудлингование, горячее дутьё[править | править код]
С начала XVII века европейской кузницей стала Швеция, производившая половину железа в Европе. В середине XVIII века её роль в этом отношении стала стремительно падать в связи с очередным изобретением — применением в металлургии каменного угля.
Прежде всего надо сказать, что до XVIII века включительно каменный уголь в металлургии практически не использовался — из-за высокого содержания вредных для качества продукта примесей, в первую очередь — серы. С XVII века в Англии каменный уголь, правда, начали применять в пудлинговочных печах для отжига чугуна, но это позволяло достичь лишь небольшой экономии древесного угля — большая часть топлива расходовалась на плавку, где исключить контакт угля с рудой было невозможно.
Потребление же топлива в металлургии уже тогда было огромно — домна (доменная печь) пожирала воз угля в час. Древесный уголь превратился в стратегический ресурс. Именно изобилие дерева в самой Швеции и принадлежащей ей Финляндии позволило шведам развернуть производство таких масштабов. Англичане, имевшие меньше лесов (да и те были зарезервированы для нужд флота), вынуждены были покупать железо в Швеции до тех пор, пока не научились использовать каменный уголь. Его ввёл в употребление в XVII веке Клемент Клерк и его мастера кузнечных дел и литья.
С 1709 году в местечке Коулбрукдейл Абрахам Дарби, основатель целой династии металлургов и кузнецов, использовал кокс для получения чугуна из руды в доменной печи. Из него поначалу делали лишь кухонную утварь, которая отличалась от работы конкурентов лишь тем, что её стенки были тоньше, а вес меньше. В 1750-х годах сын Дарби (Абрахам Дарби II) построил ещё несколько домен, и к этому времени его изделия были ещё и дешевле, чем изготовленные на древесном угле. В 1778 году внук Дарби, Абрахам Дарби III, из своего литья построил в Шропшире знаменитый Железный мост, первый мост в Европе, полностью состоящий из металлических конструкций.
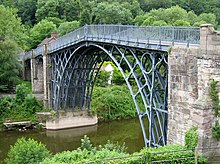
Для дальнейшего улучшения качества чугуна в 1784 году Генри Корт разработал процесс пудлингования. Среди многих металлургических профессий того времени, пожалуй, самой тяжелой была профессия пудлинговщика. Пудлингование было основным способом получения железа почти на протяжении всего XIX века. Это был очень тяжёлый и трудоёмкий процесс. Работа при нём шла так. На подину пламенной печи загружались чушки (слитки) чугуна; чушки расплавляли. По мере выгорания из металла углерода и других примесей температура плавления металла повышалась, и из жидкого расплава начинали «вымораживаться» кристаллы довольно чистого железа. На подине печи собирался комок слипшейся тестообразной массы. Рабочие-пудлинговщики приступали к операции накатывания крицы при помощи железного лома. Перемешивая ломом массу металла, они старались собрать вокруг лома комок, или крицу, железа. Такой комок весил до 50—80 кг и более. Крицу вытаскивали из печи и подавали сразу под молот — для проковки с целью удаления частиц шлака и уплотнения металла[7].
Рост производства и улучшение качества английского металла к концу XVIII века позволило Великобритании полностью отказаться от импорта шведского и российского железа. Развернулось сооружение каналов, позволявших перевозить уголь и металлы.
С 1830 по 1847 год производство металла в Англии возросло более чем в 3 раза. Применение горячего дутья при плавке руды, начавшееся в 1828 году, втрое сократило расход топлива и позволило использовать в производстве низшие сорта каменного угля, С 1826 по 1846 год экспорт железа и чугуна из Великобритании увеличился в 7,5 раза[12].
Конвертерное производство и мартеновские печи[править | править код]
В 1856 году Генри Бессемер получил патент на новую технологию производства стали (бессемеровский процесс). Он изобрёл конвертер — устройство, в котором сквозь жидкий чугун, получаемый в доменных печах, продувался воздух. В конвертере происходит выгорание углерода, растворённого в железе, что позволяет получать сталь в существенно больших количествах, чем это было ранее доступно.
Альтернативой применения конвертера на протяжении XX века являлась мартеновская печь, в которой также происходило дожигание углерода. К концу XX века мартеновские печи стали очевидно устаревшей технологией и были вытеснены кислородно-конвертерным производством стали.
В середине XX века был изобретён турбодетандер, позволяющий снизить затраты на производство кислорода. Кислород стал достаточно дешёвым, чтобы получить массовое применение в сталелитейной промышленности. Продувка расплавленного чугуна кислородом существенно разогревает металл, что упрощает производство (железо не «вымораживается», а остаётся жидким), позволяет также в конвертер сбрасывать металлолом для переплавки, а также в ряде случаев улучшает качество металла за счёт отсутствия растворённого в металле азота.
Электрометаллургия[править | править код]
Способность постоянного электрического тока восстанавливать металлы была обнаружена ещё в самом начале XIX века, однако отсутствие мощных источников электроэнергии ограничивало применение этих процессов лабораторными исследованиями. Появление в начале XX века мощных электростанций позволило создать промышленные технологии электрометаллургии. Изначально такие процессы применялись для производства цветных металлов, но к середине XX века пришли и в чёрную металлургию. Широкое применение нашли процессы электрической рудовосстанавливающей плавки, при которой железная руда, смешенная с незначительным количеством углерода, подвергается воздействию мощной электрической дуги, где происходит электрическое восстановление железа на катоде и выгорание примесей на аноде. Таким способом удаётся получить чугун высокого качества, сократить расход кислорода и снизить уровень выбросов углекислого газа. Передельные электрометаллургические процессы дают возможность плавить чугун в вакууме, в среде защитного газа, в присутствии химически активных легирующих элементов, что позволяет получать легированные стали высокого качества и специальные стали (жаропрочные, радиационно стойкие). Стали, получение которых возможно только электрометаллургическими процессами называют электросталями.
Восстановление водородом[править | править код]
Доменные печи и конвертерное производство является достаточно современным, но весьма грязным для экологии процессом. При том, что большая часть железа получается в кислородно-конвертерном производстве, велики и выбросы углекислого и угарного газов в атмосферу. Модной альтернативой становится прямое восстановление железа из руды водородом. При этом образующиеся частички железа расплавляются в электрических печах, после чего добавляется углерод и получается сталь.
Кузнецы-любители[править | править код]
Первыми производство железных изделий организовали кузнецы-любители — обычные крестьяне, промышлявшие таким ремеслом в свободное от обработки земли время. Кузнец сам находил «руду» (болотная руда вблизи ржавого болота или красный песок), сам выжигал уголь, сам строил сыродутную печь и выплавлял железо, сам ковал, сам обрабатывал.
Умение мастера на данном этапе закономерно было ограничено выковыванием изделий самой простой формы. Инструментарий же его состоял из мехов, каменных молота и наковальни и точильного камня. Железные орудия производились с помощью каменных инструментов.
Если удобные для разработки залежи руды имелись поблизости, то и целая деревня могла заниматься производством железа, но такое было возможным только при наличии устойчивой возможности выгодного сбыта продукции, чего практически не могло быть в условиях натурального хозяйства.
При такой организации производства железа, никогда не удавалось за его счёт полностью покрыть все потребности в самом простом оружии и самых необходимых орудиях труда. Из камня продолжали изготавливаться топоры, из дерева — гвозди и плуги. Металлические доспехи оставались недоступными даже для вождей. Концентрация железных изделий составляла всего порядка 200 граммов на душу населения[источник не указан 1105 дней].
На таком уровне доступности железа находились в начале нашей эры наиболее отсталые племена среди бриттов, германцев и славян. В XII‑XIII веке прибалты и финны сражаясь с крестоносцами пользовались ещё каменным и костяным оружием. Все эти народы умели уже делать железо, но ещё не могли получить его в необходимом количестве.[источник не указан 1105 дней]
Профессиональные кузнецы[править | править код]
Следующим этапом развития чёрной металлургии были профессиональные кузнецы, которые всё ещё сами выплавляли металл, но на добычу железоносного песка и выжигания угля чаще уже отправляли других мужиков — в порядке натурального обмена. На этом этапе кузнец, обычно, уже имел помощника-молотобойца и как-то оборудованную кузницу.
С появлением кузнецов концентрация железных изделий возрастала в 4‑5 раз. Теперь уже каждый крестьянский двор мог быть обеспечен персональным ножом и топором. Возрастало и качество изделий. Кузнецы профессионалы, как правило, владели техникой сварки и могли вытягивать проволоку. В принципе, такой умелец мог получить и дамаск, если знал как, но производство дамаскового оружия требовало такого количества железа, что не могло ещё быть сколько-то массовым.
В XVIII-XIX веках деревенские кузнецы умудрялись даже изготовлять стволы к нарезному оружию, но в этот период они уже пользовались оборудованием, которое сделали не сами. Некоторого масштаба перенос ремесленного производства из города в деревню становился возможным на таком этапе развития города, когда стоимость даже довольно сложного оборудования оказывалась незначительной.
Средневековые же деревенские кузнецы сами делали свои орудия труда. Как умели. Поэтому рядовой мастер обычно преуспевал в изготовлении предметов простой плоской формы, но положительно затруднялся, когда требовалось изготовить трёхмерное изделие, или состыковать несколько изделий между собой — что, например, требовалось для создания надёжного шлема. Изготовить же такое сложное изделие, как спусковой механизм для арбалета, деревенскому кузнецу было непосильно — для этого ведь потребовались бы даже измерительные устройства.
Не было у кустарных кузнецов и специализации — и мечи, и иголки, и подковы делал один и тот же мастер. Более того, во все времена сельские кузнецы были заняты в первую очередь именно изготовлением наиболее необходимых односельчанам простейших производственных и бытовых орудий, но не оружия.
Впрочем, последнее отнюдь не отменяет того обстоятельства, что в примитивных культурах даже самый заурядный кузнец считался несколько сродни колдуну, хотя, более адекватно его можно уподобить художнику. Выковывание даже обычного меча было настоящим искусством.
Теоретически всё выглядело просто: надо только наложить одна на другую три полоски металла, проковать их, и клинок готов. На практике, однако, возникали проблемы — с одной стороны надо было добиться прочной сварки и даже взаимопроникновения слоев, а с другой, нельзя было нарушать равномерность толщины слоя (а она-то и была — с лист бумаги) и, тем более, допустить, чтобы слой разорвался. А, ведь, обработка производилась тяжёлым молотом.
До разделения труда между городом и деревней годовое производство железа не превышало 100 граммов в год на человека, форма изделий была очень простой, а качество — низким, и, когда описывается вооружение какого-нибудь варяга, систематически упускается из вида, что речь идёт об оружии вождя, откопанном в его кургане. Варвары, которым курганы не полагались, вооружались существенно проще. На данном уровне развития производительных сил (характерном, например, для галлов, франков, норманнов, Руси X века) тяжёлое вооружение могло иметься только у аристократии — не более одного воина в броне на 1000 человек населения.
На новый уровень металлообрабатывающая промышленность вступила только тогда, когда стало возможным разделение труда и возникновение специальностей. Мастер железо покупал, причём уже нужного качества, покупал инструменты, необходимые по его профилю, и нанимал подмастерьев. Если уж он и делал ножи, то сдавал их на реализацию ящиками. Если делал мечи, то не по два в год, а по четыре в неделю. И, естественно, обладал большим опытом в их изготовлении.
Но для возникновения специализации непременно требовался город — хоть на несколько тысяч жителей — чтобы мастер мог всё купить и продать. Даже очень крупные призамковые посёлки (а их население тоже иногда достигало нескольких тысяч человек) не давали такой возможности — ведь в них не только ничего не производилось на продажу в другие поселения, но и отсутствовал даже внутренний товарообмен.
Чем более был развит обмен, тем больше могло быть мастеров и их специализаций, сформироваться разделение труда. Но для значительного развития обмена требовались деньги и сравнительная стабильность.
Ещё больший прогресс мог быть достигнут организацией мануфактуры, но вокруг неё требовалось выстроить уже 50-тысячный город, и наличие ещё нескольких таких же поблизости.
Тем не менее, даже после сосредоточения ремесленного производства в городах, колоритная фигура кузнеца оставалась непременным элементом пасторального ландшафта вплоть до начала, а кое-где и до середины XX века. Долгое время крестьяне просто не имели возможности покупать городские изделия. На ранних этапах развития обмена квалифицированные ремесленники обслуживали только господствующие классы — в первую очередь военные сословия.
После распространения штукофенов[править | править код]
Кустарное производство железа, однако, перестало практиковаться сразу после распространения штукофенов. Кузнецы начали покупать железо в слитках, а ещё чаще — железный лом, на предмет перековки мечей на орала.
Когда же развитие товарности хозяйства сделало ремесленные изделия доступными широким массам, кузнецы ещё долго занимались починкой сделанных в городах орудий.
Параллельно с решением организационных моментов улучшение методов обработки металлов требовало и совершенствования техники. Поскольку же основным методом была ковка, то усовершенствованию подлежали в первую очередь молоты.
Дело было в том, что, если ковка осуществлялась ручным молотом, то и размер изделия оказывался ограничен физическими возможностями кузнеца. Человек был способен отковать деталь весом не более нескольких килограммов. В большинстве случаев этого оказывалось достаточно, но при изготовлении, скажем, деталей осадных машин без механического молота, приводимого в движение водяным колесом, мулами или рабочими, было уже не обойтись.
Проблема выковывания массивных (до нескольких центнеров) деталей была решена ещё в античности, но в период средних веков она обрела новую остроту, так как крицы, получаемые из штукофенов, тоже нельзя было отковать кувалдой.
Конечно, можно было делить их на небольшие части, но, при этом, в каждой оказалось бы своё, причём неизвестное, содержание углерода, а потом, для изготовления мало-мальски крупного изделия полученные куски пришлось бы сковывать обратно.
Всё это было крайне невыгодно. Ковать крицу надо было целиком. Потому, штукофен по-хорошему требовалось комплектовать даже не одной, а тремя водяными машинами — одна качала мехи, другая — орудовала молотом, третья — откачивала воду из шахты. Без третьей тоже было никак — кустарными заготовками штукофен рудой было не обеспечить.
Впрочем, объёмы производства зависели не столько от технологий, сколько от организации труда. Если металлург не отвлекался на другие задачи, то и сыродутных печей он мог наделать куда больше. Так, в Риме производство достигло 1.5 килограмма на человека в год, и этого не хватало — железо в Рим возили даже из Китая. В Европе же и Азии даже с использованием штукофенов производство редко достигало килограмма. Но с появлением доменных печей в Европе этот показатель разом утроил